FTS von Dematic – Die coolste Lösung für Oxford Cold Storage
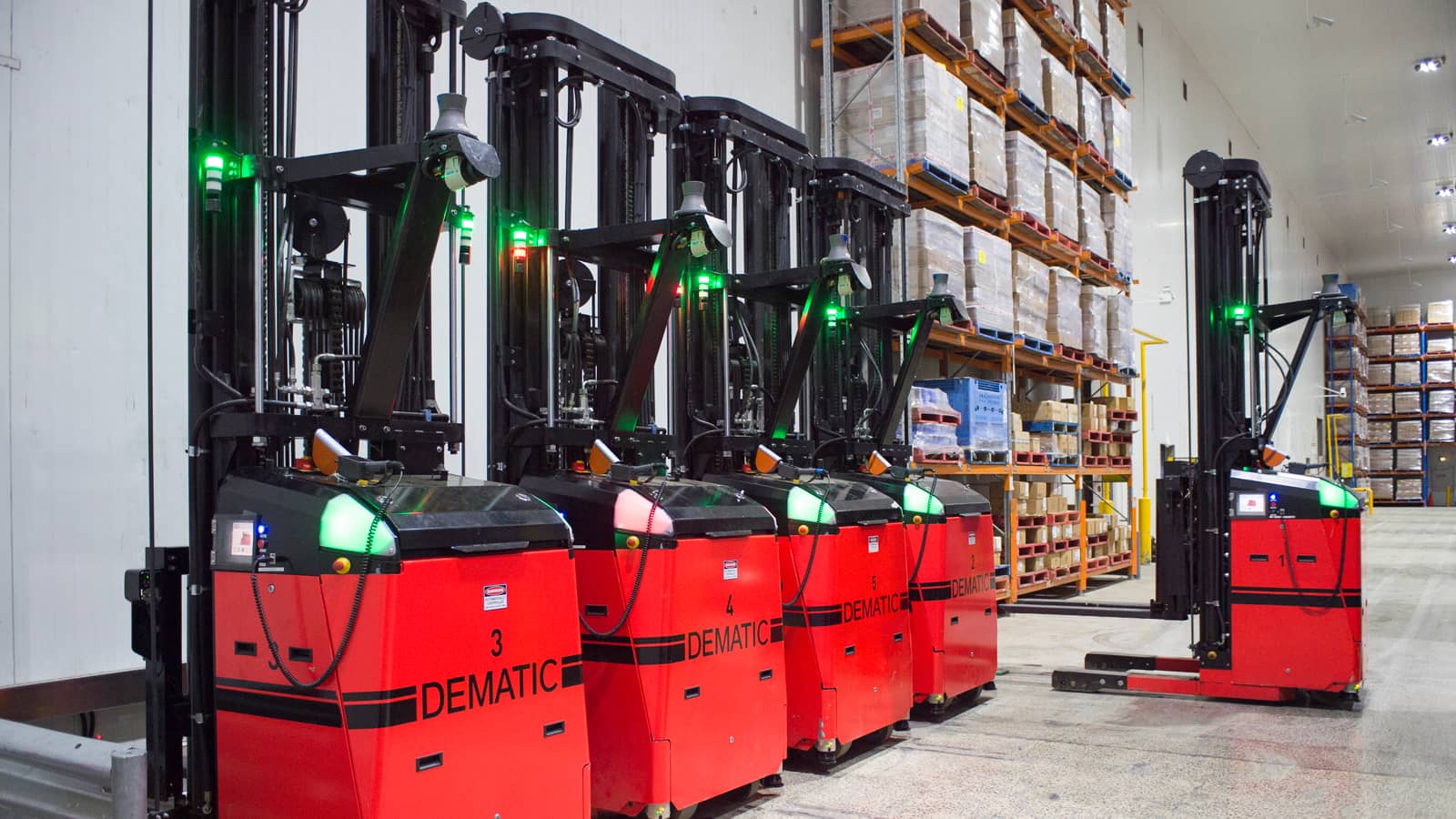
Oxford Cold Storage wurde 1975 gegründet und unterstützte zunächst benachbarte Fleischproduzenten. Der erste Gefrierschrank wurde im Geflügelverarbeitungsbetrieb von Cambridge Poultry Distributors aufgestellt. Im Verlauf der Jahre entwickelte sich das Geschäft stetig weiter und die angebotene Produktpalette bedient jetzt Hersteller von verarbeiteten Lebensmittelerzeugnissen, Lebensmittelimporteure und -exporteure sowie pharmazeutische Unternehmen. Zur Optimierung der Serviceleistungen hat die Firmenleitung Systeme entwickelt und umfangreiche technologische Investitionen getätigt.
Investition in FTS von Dematic
Die Entscheidung, versuchsweise die fahrerlosen Transportsysteme (FTS) von Dematic einzuführen, wurde wegen des ständigen Kostendrucks getroffen. Einzelhändler senken die Preise für die Verbraucherinnen und Verbraucher. Die dadurch notwendige Sparsamkeit in der gesamten Lieferkette bedeutet engere Margen für externe Logistikdienstleister wie Oxford Cold Storage.
„FTS wurden für uns eine attraktive Option, als wir erkannten, welche langfristigen Einsparungen wir damit erzielen konnten“, so Mark Fleiszig, Chief Information Officer bei Oxford Cold Storage. „FTS können rund um die Uhr und auch mitten in der Nacht bei ausgeschalteter Beleuchtung in unserem Tiefkühllager betrieben werden, in dem eine Temperatur von -25 Grad Celsius herrscht. Der Einsatz von FTS im Lager ermöglicht die Reduzierung von Gesundheits- und Sicherheitsrisiken für die Mitarbeiterinnen und Mitarbeiter und die Vermeidung von Fehlern durch menschliches Versagen.“
Angesichts von 175.000 Paletten, einer Million Kubikmeter Lagerraum und 400–500 Mitarbeiterinnen und Mitarbeitern wird Oxford Cold Storage die FTS stufenweise einführen. Letztendlich sollen damit 90 Prozent der Fracht abgefertigt werden.
„Wir testen derzeit fünf FTS gleichzeitig. Sie werden vier Gabelstapler mit menschlichem Bedienpersonal ersetzen. Wir setzen sie in einem Kühlraum mit 7.000 Paletten ein“, so Mark Fleiszig. „Der Umstieg auf FTS bedeutet aber nicht den Verzicht auf die Fähigkeiten, die Menschen bei der Bedienung von Maschinen haben. Wir hoffen, die gleiche Flexibilität zu erzielen, wie wir sie jetzt im manuellen Lager haben, nur eben mit Automatisierung.“
Einrichtung
Oxford Cold Storage entschied sich für die Implementierung von FTS in einem bereits vorhandenen Lager, anstatt ein voll automatisiertes Lager neu zu bauen. Dadurch konnte das Unternehmen zwar beträchtliche Summen sparen, doch die Entscheidung war auch mit einigen Herausforderungen verbunden. Um die Eignung für FTS sicherzustellen, musste jeder Zentimeter Arbeitsraum vermessen, kartografiert und digitalisiert werden.
Die im Lager von Oxford eingesetzten FTS sind lasergeführt. Ein Laserscanner oben am FTS misst die Winkel und die Abstände zu an Wänden und Regalen montierten Reflektoren. Das Transportsystem trianguliert dann seine Position innerhalb des Lagers und bewegt sich entsprechend an die programmierte Position. Die Genauigkeit dabei beträgt +/- 5,0 mm.
Es gelten strikte Anforderungen an die Sauberkeit und den Zustand der Böden und Regale, wenn FTS eingesetzt werden. Die FTS werden Standardpaletten mit einer Größe von 1.165 x 1.165 mm und einem maximalen Palettengewicht (einschließlich Palette) von 1.300 kg befördern. Die Paletten müssen unbeschädigt sein und es dürfen keine Nägel herausstehen. Sie dürfen keine Abfälle enthalten und es darf nichts überstehen, da es sonst zu Fehlinterpretationen der FTS-Sensoren kommen kann.
Um Toleranzen zu prüfen und die Betriebsabläufe zu rationalisieren, wird ein Fertigungsliniensystem implementiert, bei dem Paletten manuell per Gabelstapler vom Lkw entladen und dann auf ein Band befördert werden, wo sie gescannt und profiliert werden. Die unterschiedlichen Merkmale der Artikel im Lager können ebenfalls zu Komplikationen führen.
„Als externer Logistikdienstleister haben wir kaum Kontrolle darüber, welche Waren wir erhalten“, so Mark Fleiszig. „Wir müssen einfach unsere Aufträge abwickeln. Und die Abläufe beim Betrieb mit menschlichem Bedienpersonal müssen bei einer Nutzung von FTS entsprechend angepasst werden.“ Nach der Annahme werden die Paletten etikettiert und kommen in die Hauptkammer, wo die FTS sie aufnehmen und zu den Regalen befördern. Die Programmierung der FTS für die vorgesehenen Aufgaben ist einer der arbeitsintensivsten Punkte.
Im Gegensatz zu vielen anderen Unternehmen arbeitet Oxford Cold Storage mit einer eigenen Lagerverwaltungssoftware, anstatt ein System eines externen Anbieters einzusetzen. Die Einrichtung klarer Kommunikationsverbindungen zwischen dem Lagerverwaltungssystem (Warehouse Management System, WMS) von Oxford Cold Storage und der FTS-Software ist daher ein wichtiger Teil der Inbetriebnahme des Systems.
„Wir möchten die Systeme ausschließlich über das interne WMS laufen lassen, um die Einheitlichkeit zu wahren und Bediener nicht in der Anwendung neuer Software schulen zu müssen“, so Fleiszig. „Das Bandfördersystem hat Schnittstellen mit dem FTS-System, und unser WMS muss sowohl mit dem einen als auch mit dem anderen Schnittstellen haben.“
Einführung von Robotern im Lager
Bei den fünf in der Versuchsphase eingesetzten FTS handelte es sich um das Modell HR-1300-94 SSRF. Sie waren speziell für die Anforderungen des Lagers von Oxford Cold Storage entwickelt worden. Die FTS sind 3.825 mm hoch, 2.560 mm lang, wiegen jeweils ganze 5.800 kg und können Lasten auf eine Höhe von mehr als neun Metern anheben.
Sie haben drei Wechselstrommotoren, einen zum Fahren, einen zum Lenken und einen zum Anheben. Der Drehstromantrieb wandelt Gleichstrom aus dem Akku in dreiphasigen Wechselstrom um. Über den FTS-Controller lassen sich alle wichtigen Funktionen steuern.
Bei den Akkus handelt es sich um spezielle Blei-Gel-Akkus, die eine hohe Ladung aufnehmen können und auf Lebenszeit versiegelt sind. Das Transportsystem fährt bei Bedarf selbstständig zum Ladegerät. Das Ladegerät besteht aus einer Ladeplatte am Boden, die mit dem am Transportsystem montierten Ladeschuh verbunden wird. Jedes FTS hat ein manuelles Steuergerät, damit der automatische Betrieb zu Wartungszwecken oder bei manuellem Betrieb abgeschaltet werden kann.
Auf dem Touchscreen-Bedienfeld können Informationen wie Akkuladestand, Navigations- und Positionsstatus, Fehlererkennung und Geschwindigkeitseinstellungen abgelesen werden.
Eine spannende Zeit für die automatisierte Logistik
Nach der Inbetriebnahme werden die fünf FTS in diesem Gefrierlager ca. 500 Paletten täglich im Einzelschichtbetrieb transportieren, bevor dann die endgültige Steigerung auf 4.000 Paletten im 24-Stunden-Betrieb erfolgt.
„Wir hoffen, durch Belastungstests am System in einer isolierten Umgebung, die keine Unterbrechungen des Tagesgeschäfts verursachen kann, genau die Möglichkeiten von FTS auszuloten (insbesondere in einer Gefrierumgebung) und uns mit der Zukunft automatisierter Logistiklösungen vertraut zu machen.“