Gli AGV Dematic, la soluzione più cool per l'immagazzinamento a freddo di Oxford Cold Sorage
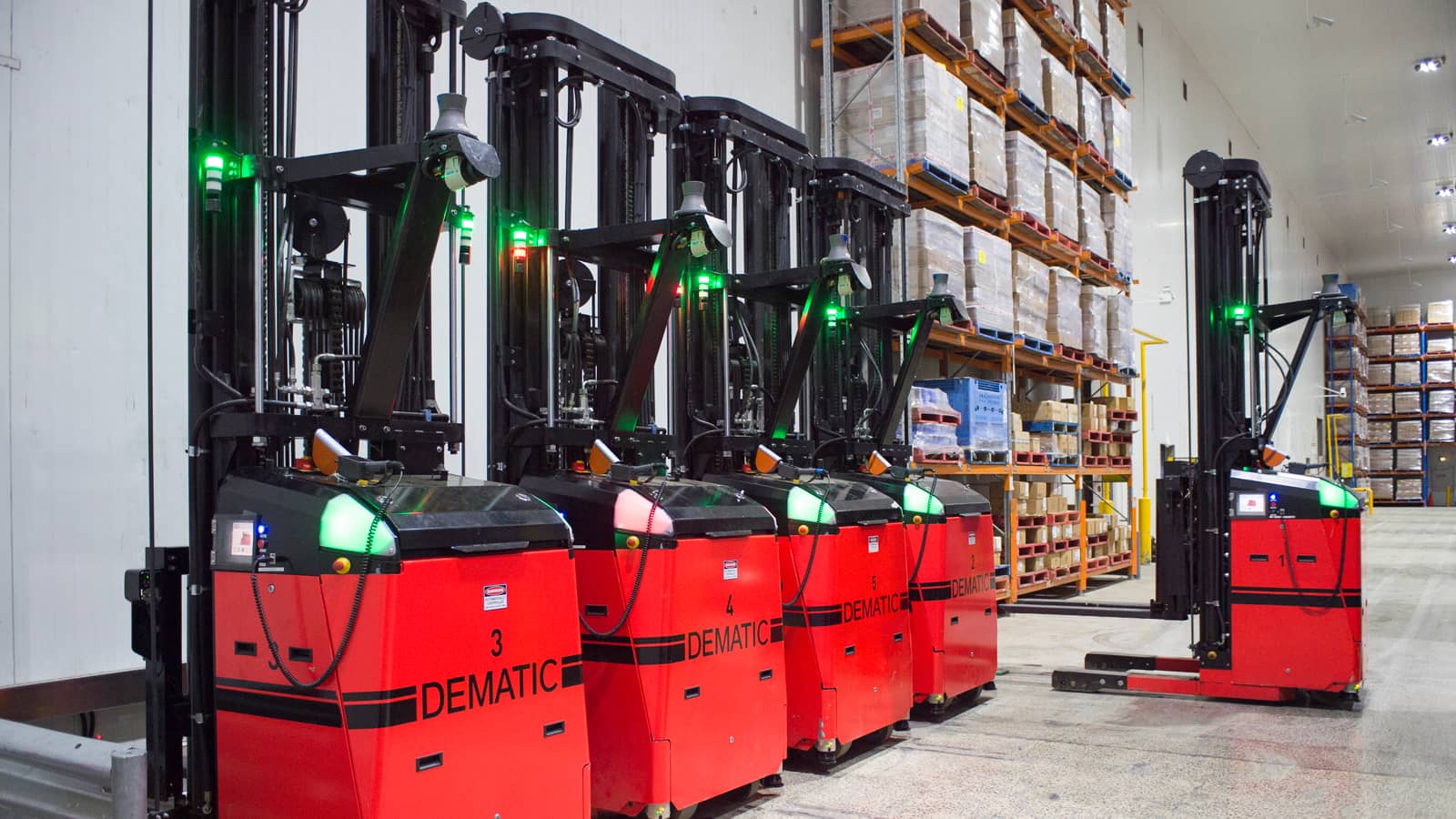
Oxford Cold Storage è stata fondata nel 1975, inizialmente per servire i produttori di carne della zona, con la prima cella frigorifera costruita accanto all'impianto di lavorazione del pollame della Cambridge Poultry Distributors. Negli anni l'azienda si è evoluta per offrire servizi a produttori di alimenti lavorati, importatori ed esportatori di prodotti alimentari e aziende farmaceutiche. La Direzione ha sviluppato dei sistemi e investito pesantemente in tecnologia per fornire il miglior servizio possibile.
L'investimento in AGV Dematic
La decisione di provare i veicoli a guida automatica (AGV) Dematic è nata dalla realtà di un flusso costante di pressioni sui costi. Con i rivenditori che riducevano i prezzi ai consumatori, l'austerity sempre più imperante lungo la catena significava per le aziende terze fornitrici di logistica, come la Oxford Cold Storage, avere margini sempre più stretti.
"Gli AGV sono diventati un'opzione interessante quando ci siamo resi conto dei risparmi a lungo termine che avremmo potuto ottenere", ha affermato Mark Fleiszig, Chief Information Officer della Oxford Cold Storage. "Gli AGV possono lavorare ventiquattro ore su ventiquattro e anche di notte, a luci spente nel magazzino freezer, che ha una temperatura di -25°C. L'aggiunta di AGV nel magazzino ha significato una riduzione delle preoccupazioni per la salute e la sicurezza dei lavoratori e l'eliminazione dell'errore umano."
Con 175.000 pallet, un milione di metri cubi di magazzino e una forza lavoro di 400-500 persone, Oxford Cold Storage prevede di applicare gli AGV gradualmente, per arrivare ad usarli alla fine per gestire il 90 percento delle sue merci.
"Abbiamo attualmente in fase di prova cinque AGV, che sostituiranno quattro carrelli a forche manuali, operando in un frigo da 7000 pallet, " ha commentato Mark. "Ma passare agli AGV non significa sacrificare la capacità degli operatori umani di risolvere i problemi. Speriamo di replicare la flessibilità che oggi abbiamo con il magazzino manuale, ma con l'automazione."
La configurazione
Oxford Cold Storage ha scelto di implementare gli AGV in un magazzino esistente piuttosto che costruire un magazzino totalmente automatizzato che, sia pur facendo loro risparmiare potenzialmente milioni, presentava alcuni problemi. Per assicurare che il magazzino fosse adatto agli AGV, ogni centimetro di spazio utile doveva essere misurato, mappato e digitalizzato.
Gli AGV usati nel magazzino di Oxford funzionano con una guida laser. Uno scanner laser in alto sull'AGV misura angoli e distanze rispetto a riflettori montati sulle pareti e sulle scaffalature. Il veicolo poi effettua una triangolazione, in cui si muove all'interno del magazzino secondo la sua posizione programmata, con una precisione pari a +/- 5.0 mm.
Quando si usano degli AGV, vi sono severi requisiti per la pulizia e le condizioni dei pavimenti e delle scaffalature. Gli AGV trasporteranno pallet standard 1165 mm x 1165 mm, con un peso massimo dei pallet di 1300 kg (pallet incluso). I pallet non devono subire danni e devono essere privi di qualunque chiudo sporgente, immondizia o prodotti sporgenti, per evitare di confondere i sensori degli AGV.
Per controllare le tolleranze e avere un funzionamento fluido e ineccepibile, sarà implementato un sistema nella linea di produzione, in cui i pallet verranno scaricati dal camion tramite un carrello a forche manuale, e poi portati ad un nastro trasportatore per essere scannerizzati e profilati. La variabilità dello stock può presentare ulteriori complicazioni.
"Essendo un'azienda terza fornitrice di logistica, abbiamo scarso controllo su quanto riceviamo" ha commentato Mark. "Dobbiamo semplicemente gestire la cosa. E il modo in cui lo facciamo ora in modalità manuale dovrà essere adattato alla nuova situazione quando utilizzeremo gli AGV." Una volta accettati, i pallet vengono etichettati - passano nella sala principale in cui gli AGV li prelevano per portarli alle scaffalature. Programmare gli AGV a fare quello che si desidera facciano è uno dei compiti più difficili.
A differenza di molte altre aziende, Oxford Cold Storage utilizza un suo software di gestione del magazzino e non un sistema realizzato da terzi. Pertanto stabilire chiare linee di comunicazione tra il software di gestione del magazzino di Oxford Cold Sorage e il software degli AGV è stata una parte essenziale dell'attivazione dell'intero sistema.
"L'idea è di guidare il tutto solo attraverso il sistema di gestione del magazzino che abbiamo, per mantenere l'uniformità ed evitare di dover addestrare nuovamente gli operatori all'uso di un nuovo software," ha dichiarato Mark. "Il sistema di trasporto interno si interfaccia con il sistema degli AGV, poi abbiamo il nostro sistema di gestione magazzino che si interfaccia con entrambi i sistemi.
Introduzione dei robot nel magazzino
Il modello dei cinque AGV in prova è stato definito HR-1300-94 SSRF. Essi sono studiati specificamente per i requisiti del magazzino Oxford Cold Sorage. Gli AGV sono alti 3.825 mm, lunghi 2.560 mm, pesano addirittura 5.800 kg cadauno e possono sollevare i pesi fino ad un'altezza di oltre nove metri.
Ci sono tre motori a.c.: trazione, direzione e sollevamento. I motori a.c. convertono la potenza della c.c. dalla batteria alla potenza c.a. trifase. Il controller dell'AGV gestisce tutte le principali funzionalità.
Le batterie sono in speciale gel al piombo, in grado di ricevere una elevata carica di corrente e sono a tenuta stagna. Il veicolo si porterà al suo caricatore quando ne avrà bisogno. Il caricatore consiste in una piastra di carica a pavimento, dove si collegherà con il pattino di carica montato sul veicolo. Su ogni AGV c'è un dispositivo di controllo manuale che permette di rimuoverlo dal servizio per scopi di manutenzione o ogni qualvolta possa essere necessario il funzionamento manuale.
Un pannello di controllo operatore con sistema touch fornisce informazioni come lo stato della batteria, della posizione e della navigazione, identificazione dei difetti e regolazioni di velocità.
Un momento interessante per la logistica automatizzata
Una volta in funzione, i cinque AGV in questo magazzino freezer si sposteranno tra 500 pallet al giorno in un solo turno, salendo poi a 4000 pallet in un periodo di 24 ore.
"Effettuando un test degli sforzi a cui l'impianto è soggetto, in un ambiente isolato che non causi disturbo al funzionamento ordinario dell'azienda, speriamo di comprendere con esattezza quello che gli AGV sono in grado di fare, in particolare in ambiente di surgelazione, e che cosa ha in serbo il futuro per le soluzioni di logistica automatizzata."