Dematic AGV's de coolste oplossing voor Oxford Cold Storage
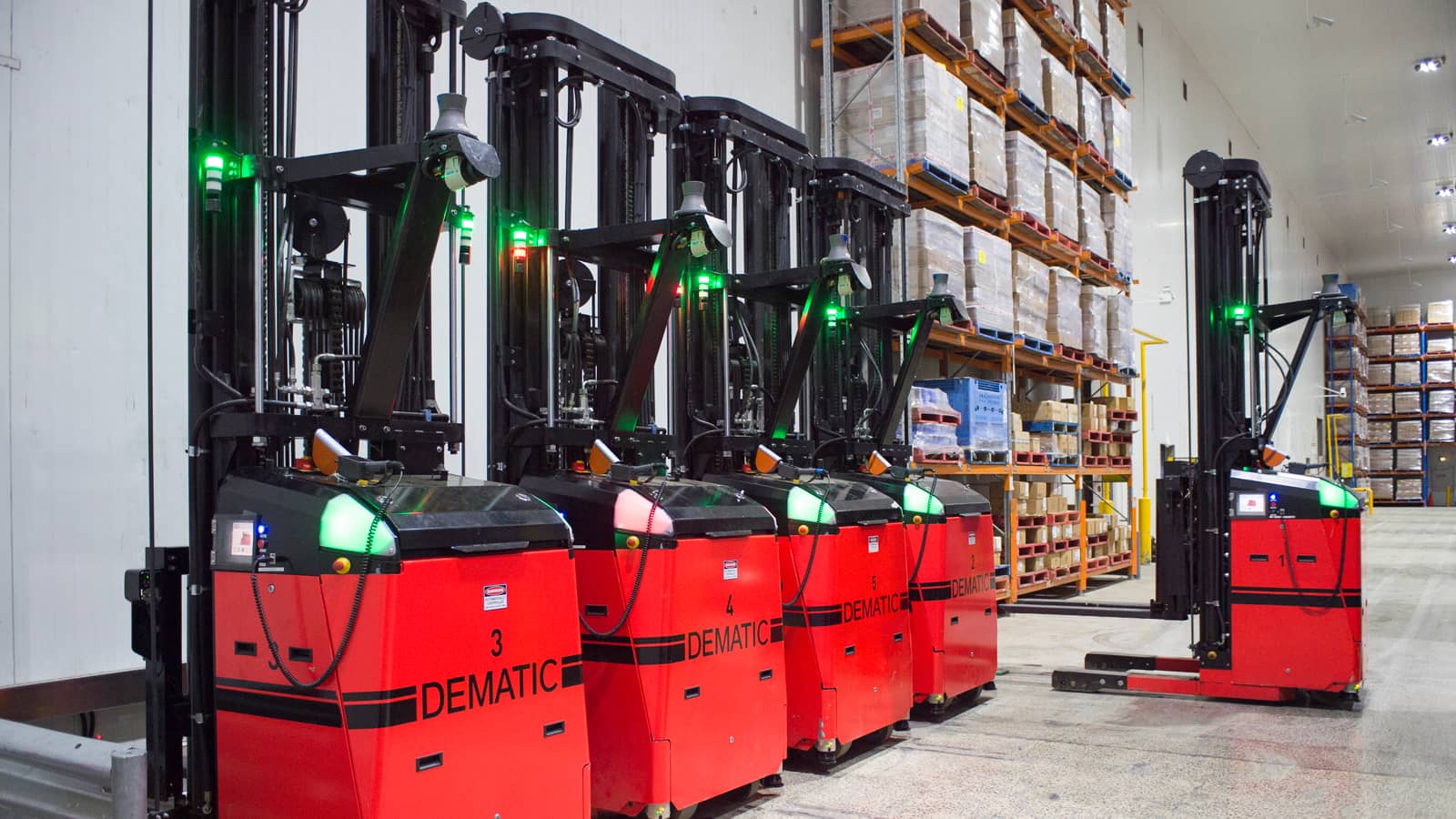
Oxford Cold Storage werd in 1975 opgericht, aanvankelijk om nabijgelegen vleesproducenten van dienst te zijn, en liet haar eerste vriezer neerzetten naast het pluimveeverwerkingsbedrijf, Cambridge Poultry Distributors. Door de jaren heen heeft het bedrijf zich verder ontwikkeld en het verleent inmiddels diensten aan fabrikanten van verwerkt voedsel, voedselimporteurs en exporteurs en farmaceutische bedrijven. Het management heeft systemen ontwikkeld en sterk geïnvesteerd in technologie om de best mogelijke diensten te verlenen.
Investeren in AGV's van Dematic
Het besluit om proeven te draaien met de Automatic Guided Vehicles (AGV's) van Dematic komt voort uit de realiteit van een constante kostendruk. Omdat winkeliers hun prijzen voor de consument laten zakken, hebben de daarmee gemoeide besparingsmaatregelen binnen de gehele keten geleid tot een krappere marge voor 3PL bedrijven zoals Oxford Cold Storage.
“AGV's werden een aantrekkelijke optie toen we ons realiseerden welke besparingen we op lange termijn konden behalen,” aldus Mark Fleiszig, Chief Information Officer bij Oxford Cold Storage. “AGV's kunnen dag en nacht werkzaam zijn en kunnen 's nachts zonder verlichting draaien in het vriezermagazijn, waar de temperatuur min 25 graden Celsius is. Door de toevoeging van AGV's aan het magazijn, hebben we minder zorgen op het gebied van beroepsgezondheid en -veiligheid, en hebben we het aantal menselijke fouten kunnen verminderen.”
Met 175.000 pallets, één miljoen kubieke meter opslag en een mankracht van 400-500 personen, heeft Oxford Cold Storage gepland om AGV's gefaseerd uit te rollen met het doel ze uiteindelijk te gebruiken om 90 procent van de vracht te verwerken.
“Momenteel worden vijf AGV's getest, welke vier handbediende vorkheftrucks zullen gaan vervangen in een vriezer met 7.000 pallets,” aldus Mark. “De verschuiving naar AGV's betekent echter niet dat we de probleemoplossende mogelijkheden van menselijke operateurs gaan vervangen. We hopen de flexibiliteit die we nu hebben in het handbediende magazijn na te bootsen met automatisering.”
De opzet
Oxford Cold Storage heeft AGV's opgenomen in een bestaand magazijn en heeft er niet voor gekozen een volledig geautomatiseerd magazijn te bouwen. Deze keuze leidt tot een besparing van miljoenen, maar kent zo haar uitdagingen. Om ervoor te zorgen dat het magazijn geschikt is voor AGV's, moest elke centimeter werkruimte worden onderzocht, in kaart gebracht en gedigitaliseerd.
De AGV's die in het magazijn van Oxford worden gebruikt, werken op laserbegeleiding. Een laserscanner bovenop de AGV meet de hoeken en afstanden tot reflectors die op de muren en rekken zijn gemonteerd. Het voertuig meet vervolgens waar het zich bevindt in het magazijn en verplaatst zich dienovereenkomstig naar de geprogrammeerde positie, dit alles met een nauwkeurigheid van +/- 5,0 mm.
Als er AGV's worden gebruikt, zijn er strikte eisen aan hoe schoon en in welke conditie de vloeren en de rekken zijn. De AGV's vervoeren standaard pallets van 1.165 mm x 1.165 mm, met een maximumgewicht (inclusief pallet) van 1.300 kg. De pallets moeten onbeschadigd zijn en vrij van uitstekende spijkers, vuil en overhangende materialen om te voorkomen dat de sensors van de AGV in verwarring worden gebracht.
Om de tolerantie te controleren en het gebruik te stroomlijnen, wordt een productielijnsysteem geïmplementeerd waarbij pallets handmatig met een vorkheftruck worden uitgeladen en naar een band worden gebracht om te worden gescand en geprofileerd. De variatie aan voorraad kan tot bepaalde complicaties leiden.
“Als 3PL hebben we weinig controle over wat we ontvangen,” aldus Mark. “We zullen het ermee moeten doen. En de manier waarop we het nu doen tijdens handmatig gebruik zal moeten worden aangepast als we de AGV's gebruiken.” Na acceptatie worden pallets voorzien van etiketten, waarna ze naar de hoofdruimte gaan en de AGV's ze ophalen om naar de rekken te brengen. Het programmeren van de AGV's zodat ze doen wat ze moeten doen, is één van de grootste taken.
In tegenstelling tot vele andere bedrijven, heeft Oxford Cold Storage haar eigen magazijnsoftware in plaats van een systeem van een derde partij. Het vestigen van duidelijke communicatie tussen de Oxford Cold Storage WMS en de software van de AGV's is daardoor van groot belang om het gehele systeem draaiend te krijgen.
“Het idee is om de systemen alleen aan te sturen vanuit de interne WMS voor een goede consistentie en om te voorkomen dat we operators opnieuw moeten opleidingen in het gebruik van nieuwe software,” aldus Mark. “Het bandsysteem is gekoppeld met het AGV-systeem en dan is er nog ons WMS, dat gekoppeld is met beide systemen.”
Introductie van robots in het magazijn
Het model van de proef met de vijf AGV's heet de HR-1300-94 SSRF en ze zijn specifiek ontworpen voor de eisen van het magazijn van Oxford Cold Storage. De AGV's zijn 3.825 mm hoog, 2.560 mm lang, wegen elk 5.800 kg en kunnen tot een hoogte van meer dan negen meter heffen.
Ze zijn voorzien van drie wisselstroommotoren: rijden, sturen en heffen. De wisselstroomaandrijving zet gelijkstroomelektriciteit van de accu om naar driefasige wisselstroom. De controller van de AGV beheert alle belangrijke functies.
De accu's zijn voorzien van loodgel, kunnen een hoge spanning ontvangen en zijn levenslang afgedicht. Het voertuig brengt zichzelf naar de lader als hij opgeladen moet worden. De lader bestaat uit een laderplaat op de vloer die verbinding maakt met de laadschoen op het voertuig. Er bevindt zich een handmatige bediening op elke AGV zodat deze uit dienst kan worden gehaald voor onderhoud of voor gevallen waarin handmatig bediend moet worden.
Een touchscreen bedieningspaneel voor de operateur geeft informatie zoals de status van de accu, navigatie en positie, fouten, snelheidsinstellingen, etc.
Een spannende tijd voor de geautomatiseerde logistiek
Zodra de vijf AGV's helemaal operationeel zijn, zullen zij in dit vriezermagazijn zo'n 500 pallets per dag verplaatsen tijdens één enkele dienst, wat uiteindelijk oploopt tot zo'n 4.000 pallets per periode van 24 uur.
“Door het systeem aan een test te onderwerpen onder hoge druk, in een geïsoleerde omgeving die geen onderbrekingen veroorzaken van de reguliere bedrijfsvoering, hopen wij precies te kunnen leren wat AGV's voor ons kunnen betekenen, en dan met name in een vriezeromgeving, en wat de toekomst ons zal brengen op het gebied van geautomatiseerde logistieke oplossingen.”