Los vehículos de guiado automático (AGV) de Dematic: la solución más increíble para Oxford Cold Storage
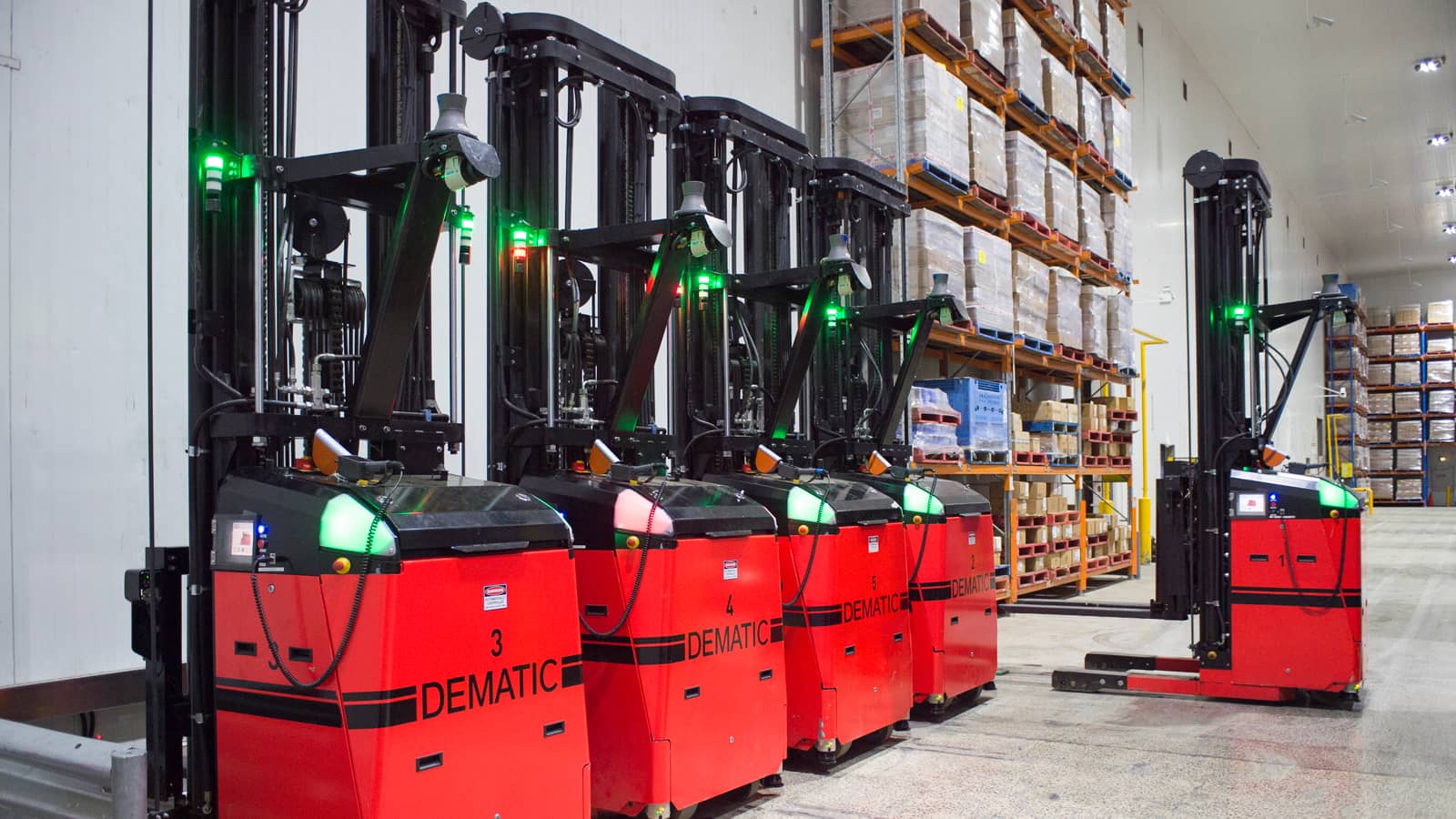
Oxford Cold Storage se fundó en 1975, con el objetivo inicial de dar servicio a los productores de carne vecinos, con el primer congelador junto a la planta de procesamiento de aves de corral, Cambridge Poultry Distributors. Con los años, la empresa ha evolucionado para ofrecer servicios a fabricantes de alimentos procesados, importadores y exportadores de alimentos y empresas farmacéuticas. Los directivos han desarrollado sistemas y realizado grandes inversiones en tecnología para ofrecer el mejor servicio posible.
La inversión en los AGV de Dematic
La decisión de probar los vehículos de guiado automático (AGV) de Dematic surgió de la realidad de hacer frente a un flujo constante de presiones por los costes. Con la reducción de precios de los minoristas para sus consumidores, la austeridad constante en la cadena significó márgenes más ajustados para las empresas 3PL como Oxford Cold Storage.
“Los vehículos AGV se convirtieron en una opción atractiva cuando nos dimos cuenta del ahorro que podíamos lograr a largo plazo”, dijo Mark Fleiszig, director de información de Oxford Cold Storage. “Los AGV pueden funcionar las veinticuatro horas del día y también a la noche, con las luces apagadas en el almacén de congelados, que tiene una temperatura de menos 25 grados centígrados. La incorporación de los AGV en el almacén supuso una reducción de los problemas de salud y seguridad laboral, además de eliminar los errores humanos”.
Gracias a sus 175 000 palés, un millón de metros cúbicos de almacenamiento y una plantilla de entre 400 y 500 trabajadores, Oxford Cold Storage tiene previsto implementar los AGV por etapas, con el objetivo de utilizarlos para manipular el 90 % de su carga.
“En la actualidad estamos probando cinco AGV, que sustituirán a cuatro carretillas elevadoras manuales y funcionarán en un frigorífico de 7 000 palés”, explicó Mark. “Pero el paso a los AGV no significa sacrificar la capacidad de resolución de problemas de las personas. Esperamos reproducir la flexibilidad que tenemos ahora con el almacén manual, pero con la automatización”.
La organización
Oxford Cold Storage optó por implementar los AGV en un almacén ya existente en lugar de construir un almacén totalmente automatizado, lo que, si bien les permitió ahorrar millones, planteó algunos desafíos. Para garantizar que el almacén fuera adecuado para los AGV, hubo que inspeccionar, cartografiar y digitalizar cada pulgada del espacio de trabajo.
Los AGV que se utilizan en el almacén de Oxford funcionan con guía láser. Un escáner láser que se encuentra en la parte superior del AGV mide los ángulos y las distancias con respecto a los reflectores montados en las paredes y en las estanterías. Entonces, el vehículo triangula su posición en el almacén y se desplaza a su posición programada en consecuencia, con una precisión de +/- 5,0 mm.
La limpieza y el estado de los suelos y de las estanterías son requisitos estrictos cuando se utilizan los vehículos AGV. Los AGV transportarán palés estándar de 1 165 mm x 1 165 mm, con un peso máximo de palés (incluido el palé) de 1 300 kg. Los palés deben estar intactos y libres de clavos que sobresalgan, basura y protuberancias para evitar que los sensores del AGV se confundan.
Para comprobar las tolerancias y agilizar la operación, se implementará un sistema de línea de producción, en el que los palés se descargarán del camión con una carretilla manual y luego se llevarán a una cinta transportadora para escanearlos y perfilados. La variabilidad de las existencias puede presentar algunas complicaciones extra.
“Al ser una 3PL, tenemos poco control sobre lo que recibimos”, afirmó Mark. “Solo tenemos que ocuparnos de eso. Y la forma en que nos ocupamos ahora en una operación manual tendrá que adaptarse cuando utilicemos los AGV”. Una vez que se aceptan los palés, se etiquetan y pasan a la cámara principal, donde los AGV los recogen y los llevan a las estanterías. Una de las tareas más importantes es programar los AGV para que hagan lo que queremos que hagan.
En contraste con muchas otras empresas, Oxford Cold Storage utiliza su propio software de gestión de almacenes, en lugar de un sistema de terceros. Por lo tanto, establecer líneas claras de comunicación entre el WMS de Oxford Cold Storage y el software de los AGV ha sido una parte esencial para poner en marcha todo el sistema.
“La idea es manejar los sistemas solo a través del WMS interno para mantener la coherencia y evitar tener que volver a formar a los operadores en cuanto al uso de un nuevo software”, expresó Mark. “El sistema de cintas transportadoras se conecta con el sistema AGV, y luego tenemos nuestro WMS que se conecta con ambos sistemas”.
La introducción de los robots en el almacén
El modelo de los cinco AGV que se prueban se llama HR-1300-94 SSRF, y están diseñados específicamente para los requisitos del almacén de Oxford Cold Storage. Los AGV tienen 3 825 mm de altura, 2 560 mm de longitud, pesan 5 800 kg cada uno y pueden elevarse a una altura de más de nueve metros.
Hay tres motores con CA: de accionamiento, de dirección y de elevación. Los motores de CA convierten la energía de CC de la batería en energía trifásica de CA. El controlador del AGV gestiona todas las funciones principales.
Las baterías son de gel led para fines especiales, y pueden recibir una alta carga de corriente y sellarse de por vida. El vehículo se conducirá solo a su cargador cuando lo necesite. El cargador consiste en una placa de carga en el suelo, donde se conectará con la zapata de carga con la que cuenta el vehículo. Hay un dispositivo de control manual en cada AGV para que quede fuera de servicio para su mantenimiento o siempre que se requiera una operación manual.
Un panel de control táctil del operador brinda información como el estado de la batería, el estado de la navegación y la posición, la identificación de fallos y los ajustes de velocidad.
El momento más emocionante para la logística automatizada
Una vez que estén en funcionamiento, los cinco AGV de este almacén frigorífico moverán alrededor de 500 palés al día en un solo turno de trabajo, y eventualmente aumentarán a 4000 palés en un período de 24 horas.
“Al someter el sistema a pruebas de estrés en un entorno aislado que no causará interrupciones en las operaciones habituales de la empresa, esperamos aprender exactamente qué pueden hacer los AGV, en especial en el entorno de un frigorífico, y qué nos depara el futuro para las soluciones logísticas automatizadas”.