AGV Dematic - solution la plus cool pour Oxford Cold Storage
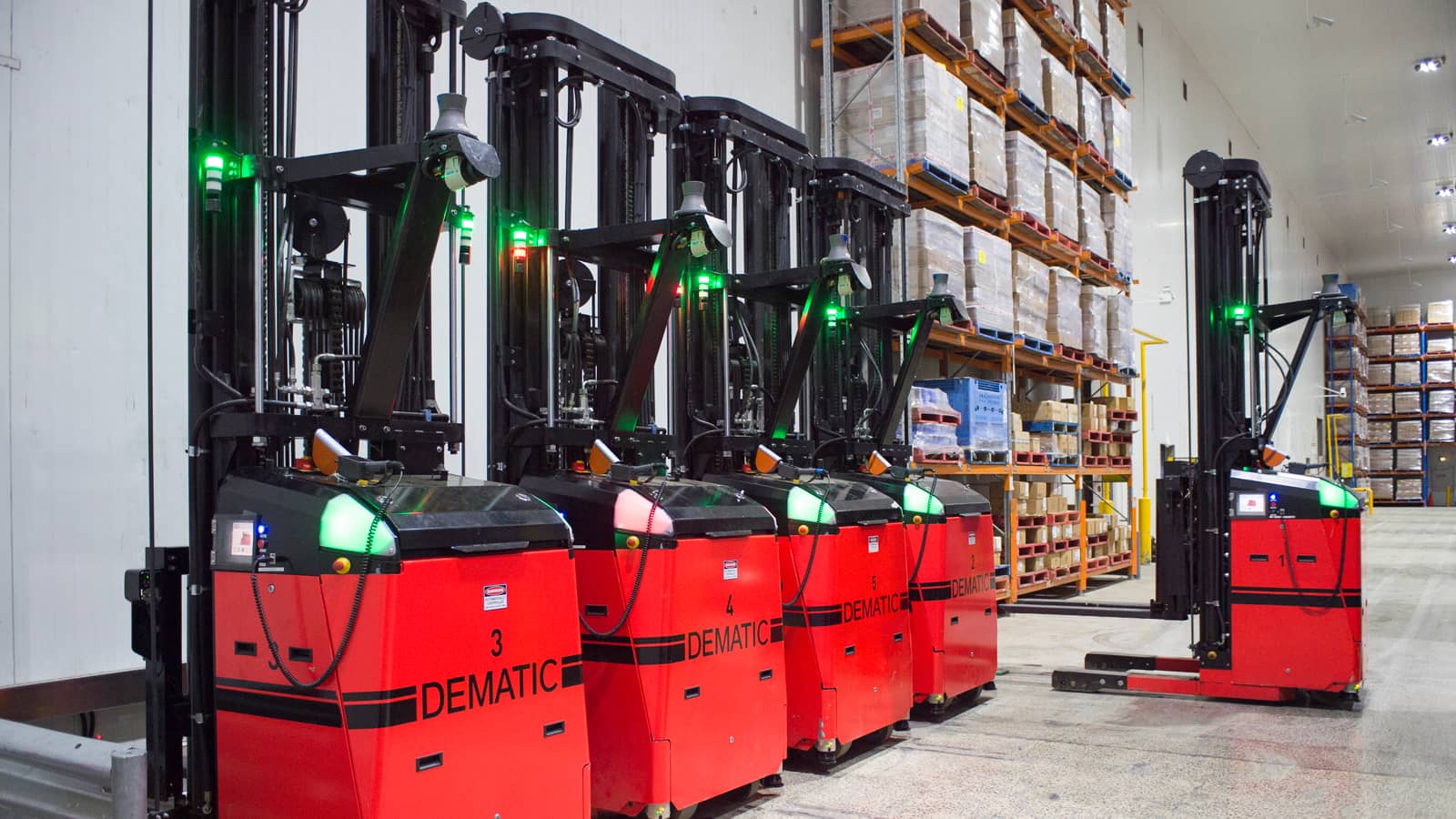
Oxford Cold Storage a été établie en 1975, au départ pour servir des producteurs de viande voisins, le premier réfrigérateur étant érigé à côté de l’usine de transformation de la volaille, Cambridge Poultry Distributors. Au fil des ans, l’entreprise a évolué, proposant aujourd’hui des services aux fabricants de denrées alimentaires transformées, aux importateurs et exportateurs de denrées alimentaires et aux laboratoires pharmaceutiques. La direction a développé des systèmes et investi lourdement dans la technologie pour fournir le meilleur service possible.
Investissement dans les AGV Dematic
La décision d’essayer les véhicules autoguidés (AGV) Dematic a logiquement découlé de la réalité d’un flux constant de pression des coûts. Les détaillants baissant les prix pour leurs consommateurs, l’austérité qui se répercute le long de la chaîne est synonyme de marges plus serrées pour des sociétés de LTP comme Oxford Cold Storage.
« Les AGV sont devenus une option attractive lorsque nous avons réalisé les économies à long terme que nous pouvions réaliser », déclare Mark Fleiszig, Chief Information Officer chez Oxford Cold Storage. « Les AGV peuvent fonctionner nonstop et la nuit, tous feux éteints, dans l’entrepôt réfrigéré, dont la température est de moins 25 degrés Celsius. L’addition d’AGV dans l’entrepôt s’est soldée par une réduction des problèmes de santé et sécurité au travail, de même que l’élimination de l’erreur humaine. »
Avec 175.000 palettes, un million de mètres cubes de stockage et une main-d’œuvre de 400-500 personnes, Oxford Cold Storage envisage de déployer les AGV par étapes, dans le but de les utiliser au final pour traiter 90 % de son fret.
« Nous avons cinq AGV en cours de test ; ils remplaceront quatre chariots élévateurs à fourche manuels et fonctionneront dans un réfrigérateur 7 000 palettes », déclare Mark. « Mais l’adoption d’AGV ne signifie pas sacrifier les aptitudes des opérateurs humains à résoudre les problèmes. Nous espérons reproduire la flexibilité dont nous bénéficions aujourd’hui avec l’entrepôt manuel, mais avec l’automatisation en plus. »
La configuration
Oxford Cold Storage a choisi de déployer des AGV dans un entrepôt existant plutôt de que construire un entrepôt entièrement automatisé, ce qui même en leur économisant potentiellement des millions, présentait quelques difficultés. Pour garantir l’adaptation de l’entrepôt aux AGV, chaque centimètre de l’espace de travail devait être relevé, cartographié et numérisé.
Les AGV utilisés dans l’entrepôt d’Oxford fonctionnent par guidage laser. Un scanner laser sur le dessus de l’AGV mesure les angles et les distances par rapport aux réflecteurs montés sur les murs et les rayonnages. Le véhicule triangule ensuite sa position dans l’entrepôt et se déplace jusqu’à sa position programmée en conséquence, avec une précision de +/- 5 mm.
Il y a des exigences strictes de propreté et d’état des sols et des rayonnages lorsque des AGV sont utilisés. Les AGV transporteront des palettes standard de 1 165 mm x 1 165 mm, avec un poids de palette maximum (palette incluse) de 1 300 kg. Les palettes doivent être intactes et dépourvues de clous qui dépassent, détritus et excédent, pour éviter de dérouter les capteurs des AGV.
Pour vérifier les tolérances et simplifier le fonctionnement, un système de chaîne de production sera mis en œuvre, où les palettes seront déchargées du véhicule par chariot élévateur manuel, puis acheminées jusqu’à un convoyeur pour être scannées et profilées. La variabilité du stock peut présenter d’autres complications.
« En tant que société de LTP, nous n’avons guère de contrôle sur ce que nous recevons », déclare Mark. « On nous demande juste de traiter la marchandise. Et la manière de le faire aujourd’hui dans une installation manuelle devra être adaptée à l’utilisation des AGV. » Une fois acceptées, les palettes sont étiquetées – elles vont dans la chambre principale, où les AGV les prélèvent et les amènent aux rayonnages. La programmation des AGV pour leur faire faire ce que vous voulez est une des tâches les plus délicates.
Contrairement à de nombreuses autres entreprises, Oxford Cold Storage utilise son propre logiciel de gestion d’entrepôt (WMS), plutôt qu’un système tiers. Par conséquent, l’établissement de lignes de communications claires entre le WMS Oxford Cold Storage et le logiciel des AGV constitue une part essentielle de la mise en route de l’ensemble du système.
« L’idée consiste à piloter les systèmes via le WMS maison seulement, ce pour maintenir l’homogénéité et éviter d’avoir à reformer les opérateurs à un nouveau logiciel », déclare Mark. « Le système convoyeur interface avec le système AGV, et puis il y a notre WMS qui interface avec les deux systèmes. »
Introduction de robots dans l’entrepôt
Le modèle des cinq AGV à l’essai est le HR-1300-94 SSRF, et il est spécialement conçu pour les exigences de l’entrepôt Oxford Cold Storage. Les AGV mesurent 3.825 mm de haut, 2.560 mm de long, des mastodontes qui pèsent 5.800 kg chacun et peuvent soulever une charge jusqu’à plus de neuf mètres de hauteur.
Il y a trois moteurs à courant alternatif : transmission, direction et levage. La transmission transforme l’alimentation en courant continu des accus en courant alternatif triphasé. Le contrôleur de l’AGV gère toutes les fonctionnalités principales.
Les accus gel plomb à usage spécial sont capables de recevoir un courant de charge élevé et ils sont étanches à vie. Le véhicule se dirige jusqu’à son chargeur de lui-même dès qu’il en a besoin. Le chargeur comprend une plaque de charge au sol, point auquel il se connecte au patin de charge monté sur le véhicule. Il y a un dispositif de commande manuelle sur chaque AGV, ce qui leur permet sa mise hors service pour maintenance, ou chaque fois qu’une opération manuelle peut être requise.
Un panneau de commande opérateur tactile apporte des informations telles que l’état de charge de la batterie, la navigation et la position, l’identification des erreurs et les paramètres de vitesse.
Une période excitante pour la logistique automatisée
Une fois mis en service, les cinq AGV dans cet entrepôt réfrigéré déplaceront environ 500 palettes par jour par quart, atteignant au final 4 000 palettes sur une période de 24 heures.
« En mettant le système à l’essai sous contrainte dans un environnement isolé qui ne causera pas de perturbations aux activités commerciales régulières, nous espérons apprendre exactement ce dont sont capables les AGV, surtout dans un environnement réfrigéré, et ce que l’avenir réserve aux solutions logistiques automatisées. »