Pojazdy AVG Dematic rozwiązaniem dla Oxford Cold Storage, które jest najbardziej cool
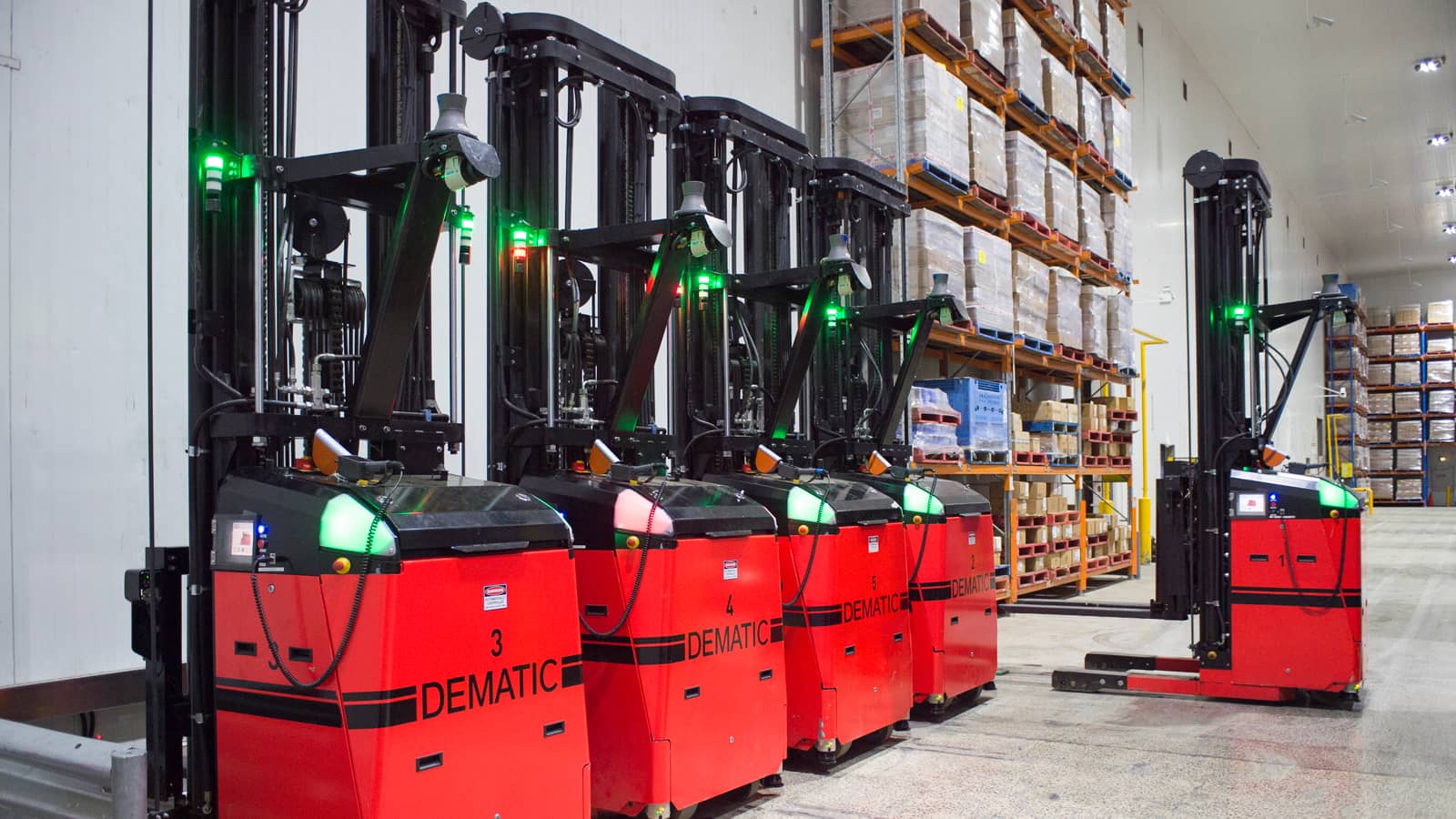
Firma Oxford Cold Storage została założona w 1975 r., początkowo w celu obsługi okolicznych producentów mięsa, przy czym pierwszą mroźnię postawiono w sąsiedztwie zakładu przetwórstwa drobiu Cambridge Poultry Distributors. Z biegiem lat firma rozwinęła się, oferując usługi skierowane do producentów żywności przetworzonej, importerów i eksporterów żywności oraz firm farmaceutycznych. Kierownictwo opracowało systemy i zainwestowało w technologię, aby zapewnić jak najwyższą jakość świadczonych usług.
Inwestycja w automatycznie sterowane pojazdy Dematic (AGV)
Decyzja o wypróbowaniu automatycznie sterowanych pojazdów Dematic (AGV) wynika z realiów ciągłej presji kosztowej. W miarę jak detaliści obniżali ceny dla swoich konsumentów, oszczędności w dalszych ogniwach łańcucha dostaw oznaczały niższe marże dla zewnętrznych dostawców usług logistycznych (3PL), takich jak Oxford Cold Storage.
„Pojazdy AGV stały się atrakcyjną opcją, gdy zdaliśmy sobie sprawę z długoterminowych oszczędności, jakie mogliśmy uzyskać”, powiedział Mark Fleiszig, dyrektor ds. technologii informacyjnych w Oxford Cold Storage. „Pojazdy AGV mogą działać przez całą dobę i pracować w nocy przy zgaszonym świetle w mroźni, w której panuje temperatura minus 25 stopni Celsjusza. Wyposażenie magazynu w pojazdy AGV oznaczało zmniejszenie obaw związanych z bezpieczeństwem i higieną pracy oraz wyeliminowanie błędów ludzkich”.
Oxford Cold Storage, posiadający 175 000 palet, milion metrów sześciennych powierzchni magazynowej i zatrudniający 400-500 pracowników, planuje wdrażać rozwiązanie AGV etapami, aby docelowo wykorzystywać je do obsługi 90 procent swoich towarów.
„Obecnie testujemy pięć pojazdów AGV, zastąpią one cztery ręczne wózki widłowe i będą pracować w chłodni o pojemności 7000 palet”, powiedział Mark. „Jednak przejście na AGV nie oznacza rezygnacji z umiejętności rozwiązywania problemów przez magazynierów. Mamy nadzieję, że uda nam się odwzorować warunki, gwarantujące elastyczność, jaką mamy teraz przy wykorzystaniu magazynu z obsługą ręczną, również po wprowadzeniu automatyzacji”.
Konfiguracja
Firma Oxford Cold Storage zdecydowała się na wdrożenie AGV w istniejącym magazynie, zamiast budować w pełni zautomatyzowany magazyn, co, choć potencjalnie pozwoliło zaoszczędzić miliony, wiązało się z kilkoma wyzwaniami. Aby upewnić się, że magazyn jest przystosowany do obsługi przez pojazdy AGV, należało zbadać, zmapować i zdigitalizować każdy centymetr przestrzeni roboczej.
Pojazdy AGV używane w magazynie Oxford pracują dzięki naprowadzaniu laserowemu. Skaner laserowy zamontowany na pojeździe AGV mierzy kąty i odległości do reflektorów zamocowanych na ścianach i na regałach. Następnie, pojazd oblicza metodą triangulacji, jaka jest jego lokalizacja wewnątrz magazynu, i przemieszcza się tak, by osiągnąć zaprogramowaną pozycję, z dokładnością +/- 5,0 mm.
Istnieją surowe wymagania dotyczące czystości i stanu podłóg i regałów, gdy stosuje się pojazdy AGV. Pojazdy AGV będą transportować standardowe palety o wymiarach 1165 mm x 1165 mm, o maksymalnej wadze (łącznie z paletą) 1300 kg. Palety muszą być nieuszkodzone, pozbawione wystających gwoździ, zanieczyszczeń i nawisów, aby nie dezorientować czujników AGV.
Aby sprawdzić tolerancje i usprawnić działanie, zostanie wdrożona linia produkcyjna obejmująca system, w którym palety będą rozładowywane z ciężarówki za pomocą ręcznie obsługiwanego wózka widłowego, a następnie przenoszone na taśmociąg, gdzie będą skanowane i profilowane. Różnorodność towarów może przysparzać dodatkowych trudności.
„Ponieważ działamy jako zewnętrzny dostawca usług logistycznych, mamy niewielka kontrolę nad tym, co otrzymujemy”, powiedział Mark. „Musimy sobie z tym po prostu radzić. A nasz tryb postępowania przy ręcznej obsłudze będzie wymagał zmiany po wprowadzeniu pojazdów AVG do użytkowania”. Po pomyślnej weryfikacji palety są opatrywane etykietami - kierowane są do głównego pomieszczenia, w którym są przejmowane przez pojazdy AGV i zabierane na regały. Jednym z największych wyzwań jest zaprogramowanie pojazdów AVG tak, by wykonały wszystkie pożądane czynności.
W odróżnieniu od wielu innych spółek, firma Oxford Cold Storage korzysta z własnego oprogramowania obsługującego gospodarkę magazynową, a nie system zewnętrznego dostawcy. Z tego względu ustanowienie skutecznej łączności pomiędzy systemem WMS Oxford Cold Storage i oprogramowaniem AVG okazało się istotną częścią wymaganą do uruchomienia systemu.
„Przyświecała nam idea, aby systemy były obsługiwane wyłącznie przez wewnętrzny system WMS w trosce o zachowanie spójności i uniknięcie konieczności ponownego szkolenia pracowników w zakresie obsługi nowego oprogramowania”, mówi Mark. „System taśmociągów łączy się z systemem AGV, a następnie wkracza do akcji nasz system WMS, który ma interfejs z obydwoma systemami”.
Wdrożenie robotów w magazynie
Model pięciu testowanych AGV nazywa się HR-1300-94 SSRF i został zaprojektowany specjalnie pod kątem wymagań magazynu Oxford Cold Storage. Pojazdy AGV mają wysokość 3825 mm, długość 2560 mm, ważą po 5800 kg każdy i mogą sięgać na wysokość ponad dziewięciu metrów.
Mają trzy silniki zmiennoprądowe: napędowy, sterujący i podnoszący. Napędy zmiennoprądowe przetwarzają prąd stały z akumulatora na trójfazowy prąd zmienny. Sterownik AGV zarządza wszystkimi głównymi funkcjami.
Wykorzystuje się w nich żelowe baterie LED o specjalnym przeznaczeniu, które mogą być ładowane prądem o wysokim natężeniu i są trwale zaplombowane. Pojazd sam podjedzie do ładowarki, gdy będzie taka potrzeba. Ładowarka składa się z płyty ładującej na podłodze, do której podłącza się zamontowaną w pojeździe stopę ładującą. Na każdym AGV znajduje się ręczne urządzenie sterujące, pozwalające na wyłączenie go z eksploatacji w celu konserwacji lub w dowolnych okolicznościach, gdy wymagana jest obsługa ręczna.
Panel sterowania użytkownika z ekranem dotykowym dostarcza informacje takie jak stan baterii, status nawigacji i pozycji, identyfikacja usterek oraz ustawienia prędkości.
Ciekawe czasy dla zautomatyzowanej logistyki
Po uruchomieniu pięć pojazdów AGV pracujących w mroźni będzie przemieszczać około 500 palet dziennie w ciągu jednej zmiany, a docelowo do 4000 palet w ciągu 24 godzin.
„Testując system w warunkach skrajnych w odizolowanym środowisku, które nie spowoduje zakłóceń w zwykłych operacjach biznesowych, mamy nadzieję dowiedzieć się dokładnie, do czego są zdolne pojazdy AGV, zwłaszcza w środowisku mroźni, i jaka jest przyszłość zautomatyzowanych rozwiązań logistycznych”.