Polaris mit neuem Distributionszentrum auf der Überholspur
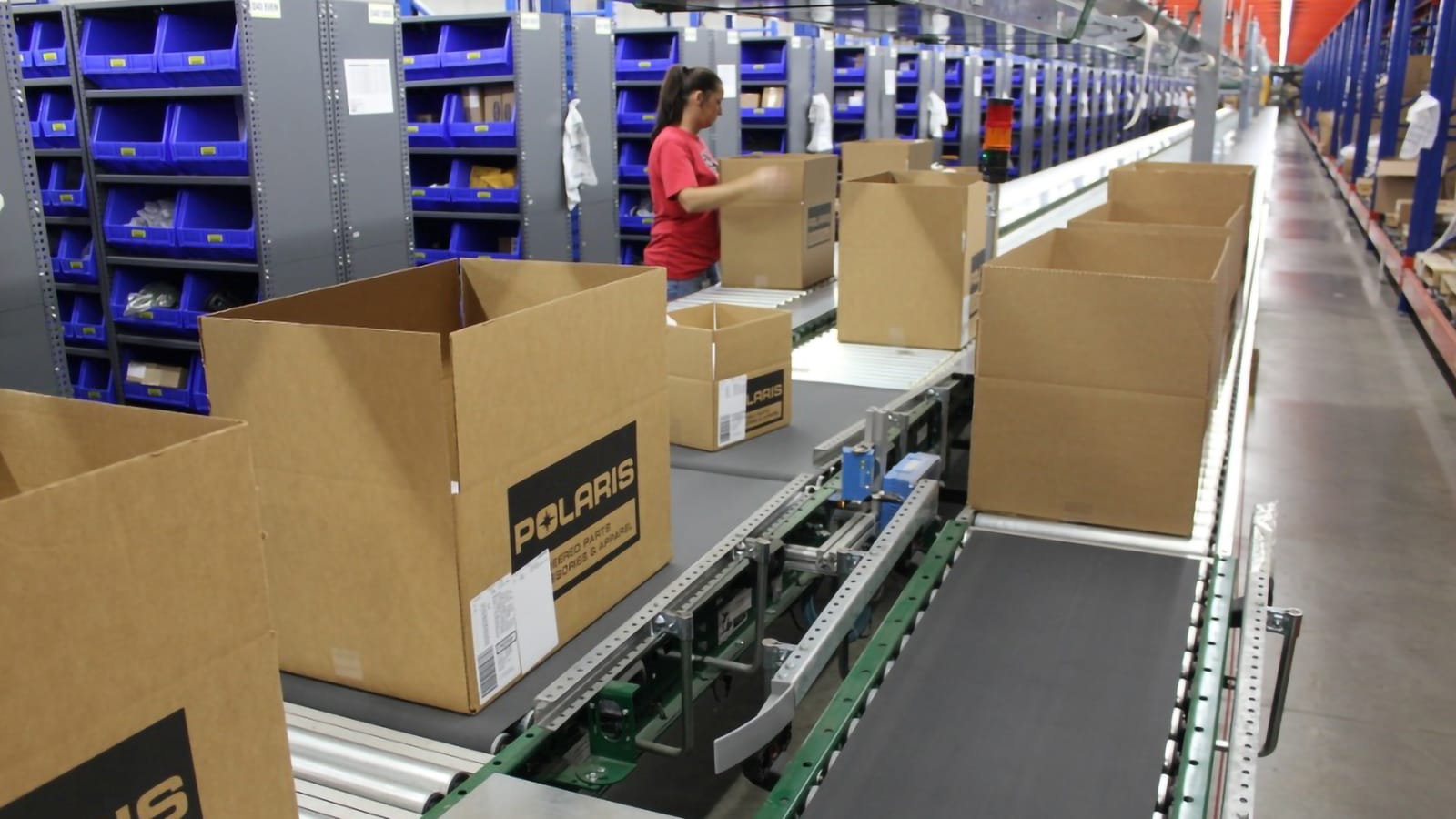
5. Februar 2025
Polaris Industries, Hersteller von motorisierten On- und Off-Road-Fahrzeugen, Schneemobilen und Motorrädern, unterstützt Outdoor-Fans, Fahrerinnen und Fahrer und Arbeiterinnen und Arbeiter mit innovativen, hochwertigen Fahrzeugen und Dienstleistungen. Zur Belieferung seiner Händler mit Teilen, Kleidungsstücken und Zubehör hat Polaris ein neues Distributionszentrum entworfen, errichtet und implementiert, über das die Händler im östlichen Teil Nordamerikas versorgt werden sollen.
Überblick
Um den hohen Erwartungen seiner Händler gerecht zu werden und sicherzustellen, dass Aufträge schnell, präzise und effizient bearbeitet werden, benötigte Polaris eine Lösung zur Optimierung des Kommissionier-, Verpackungs- und Versandprozesses. „Unser entscheidender Vorteil sind unsere innovative Kultur, die Schnelligkeit und Flexibilität unserer Betriebsabläufe sowie unsere Leidenschaft für die ständige Verbesserung der Lieferkette im Teilevertrieb“, so Paul Eickhoff, Director of Operations bei Polaris.
Herausforderungen
Bisher hat Polaris seine Händler im Osten der USA über sein Distributionszentrum in Vermillion, South Dakota, mit Teilen, Kleidungsstücken und Zubehör beliefert. Um die Service- und Reaktionszeit für diese Händler zu optimieren und das zukünftige Wachstum des Unternehmens zu fördern, wurde eine neue Distributionseinrichtung benötigt. Im Hinblick auf die Netzwerkeffizienz wurde Ohio zum idealen geografischen Standort bestimmt. Ein bestehendes Gebäude wurde erworben und ein neues Polaris-Distributionszentrum war geboren.
Lösung
Dieses Distributionszentrum nutzt einen strategischen Lagerortplan, um die Betriebsleistung zu optimieren. In Kisten kommissionierte Polaris-Teile werden im Full-Case-Kommissionierungsmodul zentralisiert. Als „Einzelstücke“ kommissionierte Teile werden im Split-Case-Kommissionierungsmodul zentralisiert. Artikel mit niedriger Geschwindigkeit, große und nicht förderfähige Artikel werden zusammen auf Paletten in Regalen platziert. Darüber hinaus erfolgt die Lagerplatzzuordnung der SKUs in diesen Bereichen nach Geschwindigkeit.
Das Split-Case-Kommissionierungsmodul basiert auf einer Methodik, bei der der Auftragsbehälter zum Kommissionierer bewegt wird. Diese Methode wird als Zone-Routing-System bezeichnet. Die Kommissionierer bleiben in einer bestimmten Zone. Da die Kommissionierer nicht auf der Suche nach Waren kreuz und quer durch das Lager laufen müssen, sondern sich stattdessen auf das Kommissionieren eines Segments in einem begrenzten Bereich des Lagers konzentrieren, wird die Effizienz gesteigert.
Das Split-Case-Kommissionierungsmodul ist mit 4 Zonen konfiguriert. In jeder Zone werden SKUs in Durchlaufregalen bereitgestellt. Die Lagerplatzzuordnung in den Zonen erfolgt nach Attributen wie der Teilefamilie, der Geschwindigkeit oder des Raumnutzungsgrads. Die Arbeitsweise besteht darin, dass der Auftragsbehälter nur in Zonen mit Kommissionierungen geleitet wird.
Zur Unterstützung der Kommissioniermethode gemäß dem Zone-Routing-System steht ein Fördernetzwerk zur Verfügung, um den Fluss der Auftragskartons in die Zonen und aus den Zonen zu steuern. In jeder Zone arbeitet ein Kommissionierer – in Stoßzeiten können hier jedoch auch weitere Mitarbeiterinnen und Mitarbeiter positioniert werden. In Zeiten mit geringerem Auftragsvolumen könnten wiederum mehrere Zonen von einem einzigen Kommissionierer bedient werden.
Das Förderlayout umfasst eine zentrale Stauförderstrecke, die das gesamte Split-Case-Kommissionierungsmodul durchläuft und über einen Ausgang und eine Nebenförderstrecke für jede Zone verfügt. Jeder Ausgang besteht aus einem Barcode-Scanner und einem rechtwinkligen Transfer, um den Auftragsbehälter in die Kommissionierzone auszuschleusen. Wenn die Kommissionierungen abgeschlossen sind, schiebt der Bediener den Auftragsbehälter zurück auf die zentrale Hauptförderstrecke. Wenn weitere Kommissionierungen durchzuführen sind, wird er in eine andere Zone befördert. Wenn alle Kommissionierungen erledigt sind, wird er auf der Hauptförderstrecke direkt zum Verpacken transportiert.
Vor der Hauptförderstrecke im Split-Case-Kommissionierungsmodul befindet sich eine Auftragsbeginn-Arbeitsstation. Eine Mitarbeiterin bzw. ein Mitarbeiter bringt an jedem Karton ein Etikett mit einem eindeutigen Barcode an, richtet den Karton auf und führt ihn in die Inline-Verschließmaschine ein. Der Karton wird auf der Hauptförderstrecke zu der Zone weiterbefördert, in der sich die Waren für den Auftrag befinden.
Die in den Zonen positionierten Mitarbeiterinnen und Mitarbeiter erhalten Kommissionierungsanweisungen über tragbare RF-Handgeräte. Wenn ein Auftragsbehälter in der Kommissionierzone eintrifft, scannt die Mitarbeiterin bzw. der Mitarbeiter den Barcode auf dem Auftragsbehälter mit dem RF-Gerät. Daraufhin werden Kommissionieranweisungen auf dem Display angezeigt. Am Kommissionierort scannt die Mitarbeiterin bzw. der Mitarbeiter den SKU-Barcode auf dem Produkt, um die korrekte SKU zu bestätigen. Die Artikel werden kommissioniert und in den Auftragsbehälter gelegt. Der Auftragsbehälter wird von Hand zurück auf die zentrale Hauptförderstrecke geschoben.
Jeder Split-Case-Auftragsbehälter wird zum Subsystem Verpackung und Versand befördert. An der Verpackungsstation wird der Auftrag auf Genauigkeit geprüft und der Karton zur Berechnung der Versandkosten gewogen, mit einem Versandetikett versehen und verschlossen. Diese fertigen Split-Case-Auftragskartons werden in den Versandbereich befördert, wo eine Sortieranlage die Kartons für ein flüssiges Verladen in Lkw-Anhänger automatisch zum entsprechenden Versandtor ausschleust. Die Kartons für LTL-Transporte werden automatisch in eine manuelle Palettierstation einsortiert.
Das Full-Case-Kommissionierungsmodul besteht aus Paletten mit Kisten, die in einer Regalstruktur platziert sind. Gemäß den Anweisungen auf einem tragbaren RF-Gerät geht eine Mitarbeiterin bzw. ein Mitarbeiter zu einem Palettenplatz und platziert die Kiste(n) auf den Förderer in der Mitte des Full-Case-Kommissionierungsmoduls. An jeder Kiste wird ein vorgedrucktes Etikett angebracht. Kisten aus dem Full-Case-Kommissionierungsmodul werden zum Versand befördert und für ein flüssiges Verladen automatisch zum entsprechenden Lkw-Anhänger oder zum LTL-Palettieren und Versand ausgeschleust.
Die Warehouse Control Systems-Software verwaltet den automatisierten Betrieb des gesamten Förder- und Sortiernetzwerks. Diese modulare Software leitet den Fluss der Split-Case-Auftragsbehälter in die entsprechenden Kommissionierzonen. Anhand der Daten von den Barcode-Scannern aktiviert die Software die rechtwinkligen Transfervorrichtungen, sodass Kartons automatisch in die Kommissionierzonen ausgeschleust werden können.
Außerdem lenkt die WCS-Software den Betrieb und die Steuerung des Förderer-Subsystems des Full-Case-Kommissionierungsmoduls, der Verpackungs-Arbeitsstationen und des Versandsortierer-Subsystems. Es sind Echtzeitinformationen zum Kartonstandort im System, zu Ausschleuse-/Sortierstatistiken, zu den Barcode-Leseraten und zur Rezirkulation von Kartons verfügbar. Eine Grafik des Systemlayouts zeigt Echtzeitinformationen zum Status und zu den Leistungsattributen der einzelnen Subsysteme an: Kommissionierung, Verpackung, Verpackungszusammenführung, Abfallentsorgung und Versand.
Ergebnis
Der modulare Systemaufbau fördert die betriebliche Effizienz, die Auftragsverarbeitungsgeschwindigkeit und die Auftragsgenauigkeit und bietet zugleich die nötige Flexibilität für Änderungen der täglichen Anforderungen. Die Kapazität für die Auftragsverarbeitung kann gesteigert werden, indem die Anzahl der Mitarbeiterinnen und Mitarbeiter im Split-Case- und Full-Case-Modul zu Stoßzeiten erhöht wird. In Zeiten mit geringer Aktivität können weniger Mitarbeiterinnen und Mitarbeiter zur Verarbeitung des Auftragsvolumens zugeteilt werden. Darüber hinaus können Arbeitsstationen und Versandtor-Ausschleuser je nach Aktivität in oder außer Betrieb genommen werden. Die aktuelle Aktivität entspricht etwa 500-700 Aufträgen pro Tag (6.000 Artikel) mit etwa 150 Wiederbeschaffungsaufträgen. Die Systemkapazität beträgt 25.000 Artikel.
Die Kommissionierer müssen nicht das gesamte Lager ablaufen, um die zu kommissionierenden Waren zusammenzusuchen. Stattdessen sieht das System die Positionierung von Mitarbeiterinnen und Mitarbeitern in Kommissionierzonen vor, wo die Waren in einer dichten, kompakten Konfiguration zusammengestellt werden. So müssen die Kommissionierer weniger laufen und schaffen mehr Kommissionierungen pro Stunde. Darüber hinaus leitet das Zone-Routing-System Auftragsbehälter nur in Zonen mit Kommissionierungen, wodurch die Auftragsverarbeitungszeit verkürzt wird. Durch den systematischen Ansatz in Verbindung mit der Förder- und Sortierautomatisierung werden der Kommissionier-, Verpackungs- und Versandprozess rationalisiert, optimiert und produktiver gestaltet. Außerdem ist das System auf Wachstum ausgelegt, indem zum Beispiel Ausschleuser im Versandlayout vorinstalliert sind. Wenn in Zukunft zusätzliche Kapazität benötigt wird, wird der modulare nachgelagerte Förderer angeschlossen und die vorkonfigurierte Software aktiviert.