Polaris pone en marcha el nuevo centro de distribución
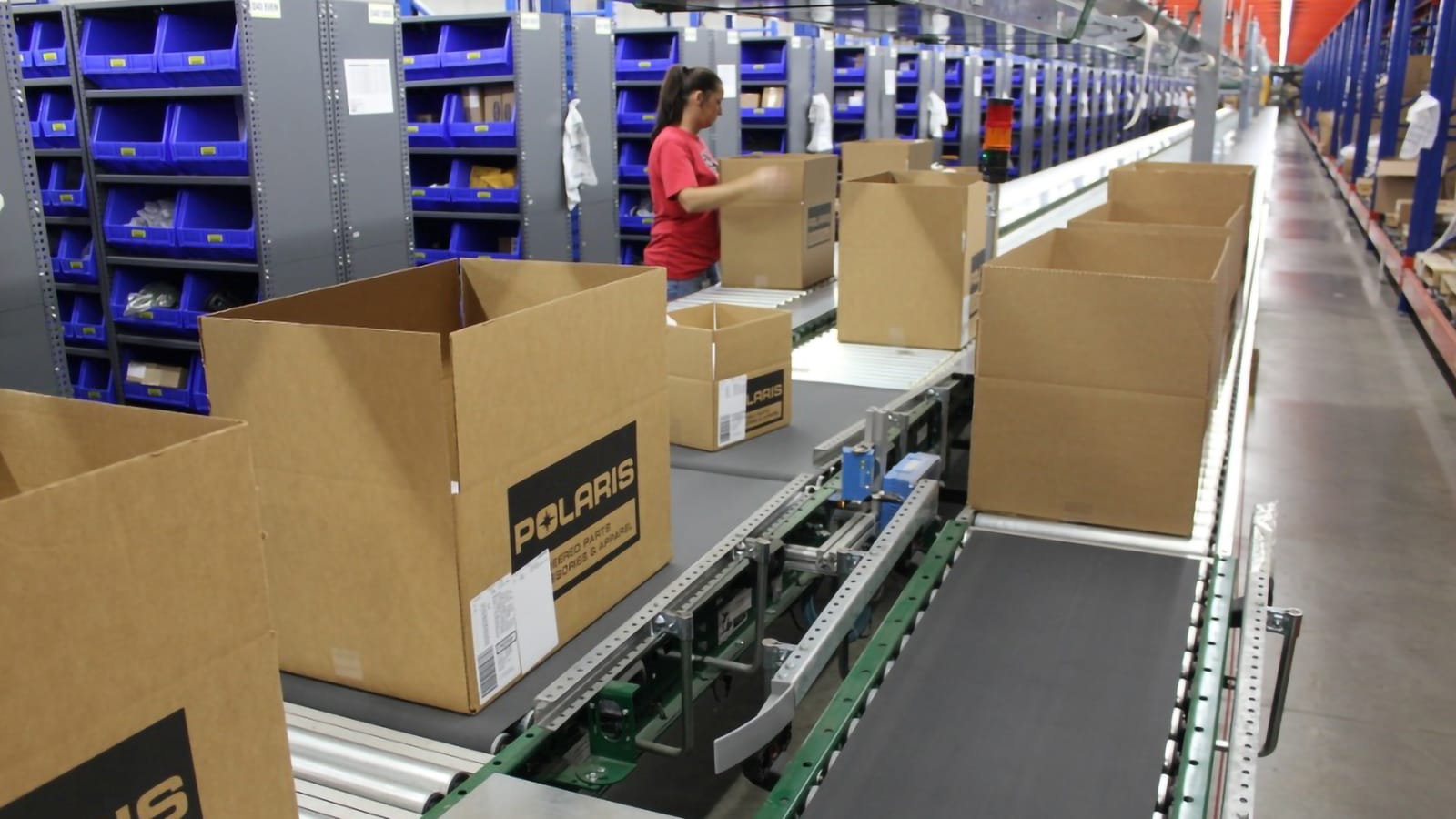
2 de agosto de 2022
Polaris Industries, fabricante de vehículos motorizados para carretera y todoterreno, motos de nieve y motocicletas, apoya a los entusiastas de las actividades al aire libre, a los conductores y a los trabajadores y ofrece vehículos y servicios innovadores y de alta calidad. Para suministrar piezas, prendas y accesorios a sus concesionarios, Polaris ha diseñado, construido y puesto en marcha un nuevo centro de distribución para dar asistencia a los concesionarios de la zona este de Norteamérica.
Introducción
Para dar respuesta a las grandes expectativas de sus concesionarios y garantizar que los pedidos se procesen con rapidez, precisión y eficacia, Polaris necesitaba una solución que pudiera optimizar el proceso de recogida, embalaje y envío. Según Paul Eickhoff, director de operaciones de Polaris, “La principal ventaja es nuestra cultura innovadora, la velocidad y flexibilidad operativas y la pasión por mejorar la cadena de suministro de distribución de piezas”.
Los desafíos
Con anterioridad, Polaris suministraba piezas, prendas y accesorios a sus concesionarios de la región este de Estados Unidos desde su centro de distribución en Vermillion, Dakota del Sur. Con el fin de optimizar el servicio y el tiempo de respuesta para estos concesionarios y respaldar el futuro crecimiento de la empresa, se necesitaba un nuevo centro de distribución. Desde el punto de vista de la eficiencia de la red, se determinó que Ohio era una ubicación geográfica ideal. Se adquirió un edificio existente y así nació un nuevo centro de distribución de Polaris.
La solución
El diseño del centro de distribución utiliza un plan estratégico de ubicación del inventario para optimizar el rendimiento operativo. Las piezas de Polaris que se recogen en cajas se centralizan en el módulo de recogida de cajas completas. Las piezas que se recogen como “piezas” se centralizan en el módulo de recogida de cajas divididas. Los artículos de menor movimiento, grandes y que no se pueden transportar se colocan juntos en palés en las estanterías. Además, las SKU se colocan en estas áreas según la velocidad.
El módulo de recogida de cajas divididas está diseñado según una metodología que acerca el contenedor de pedidos al trabajador. Este método se denomina sistema de rutas por zonas. Los trabajadores permanecen en una zona asignada; se gana en eficiencia ya que los trabajadores no recorren el almacén en busca de pedidos, sino que se centran en recoger una parte del inventario que se encuentra en una zona geográfica compacta.
El módulo de recogida de cajas divididas está configurado con 4 zonas. En cada zona, las SKU se colocan en estructuras deslizantes o en estantería. Las zonas se clasifican en función de atributos como la familia de piezas, la velocidad o la utilización de la acomodación de productos. El método operativo consiste en dirigir el contenedor de pedidos solo a las zonas de recogida.
Para respaldar el método de recogida del sistema de rutas por zonas, se proporciona una red de cintas transportadoras para controlar el flujo de cajas de pedidos hacia y desde las zonas. En cada zona hay un trabajador, pero se pueden agregar más trabajadores en los períodos de máxima afluencia. O bien, durante los períodos de menor volumen de pedidos, un trabajador podría recorrer varias zonas.
La disposición de la cinta transportadora incluye una columna de acumulación que recorre todo el módulo de recogida de cajas divididas con una salida y un apartadero para cada zona. Cada punto de salida consta de un escáner de códigos de barras y una transferencia en ángulo recto para desviar el contenedor de pedidos a la zona de recogida. Una vez finalizada la recogida, el operador empuja el contenedor de pedidos de nuevo a la columna de la cinta transportadora central. Si hay más recogidas, se desplaza a otras zonas; si no hay más recogidas, se desplaza directo al embalaje, en la columna de la cinta transportadora.
En el módulo de recogida de cajas divididas hay una estación de trabajo de inicio de pedidos que se encuentra antes de la columna de la cinta transportadora. Un trabajador aplica una etiqueta de código de barras único a cada caja, forma la caja y la introduce en la máquina incorporada que coloca la cinta. La caja avanza por la columna de la cinta transportadora hasta la zona donde se encuentra el inventario del pedido.
Los trabajadores que están en las zonas utilizan dispositivos portátiles de radiofrecuencia para recibir instrucciones sobre la recogida. Cuando un contenedor de pedidos llega a la zona de recogida, el trabajador escanea el código de barras del contenedor con el dispositivo de radiofrecuencia. A continuación, aparecen las instrucciones de recogida en la pantalla. En la zona de recogida, el trabajador escanea el código de barras de la SKU del producto para confirmar que sea la correcta. Los artículos se recogen y se colocan en el contenedor de pedidos. Una vez finalizada la recogida, el operador empuja el contenedor de pedidos de nuevo a la columna de la cinta transportadora central.
Cada contenedor de pedido de caja dividida se transporta al subsistema de embalaje y envío. En la estación de embalaje, se comprueba la exactitud del pedido, se pesa para calcular los costes de envío, se aplica una etiqueta de envío y se sella la caja. Las cajas de cartón terminadas con los pedidos de cajas divididas se transportan a la zona de envío, donde un clasificador desvía las cajas de forma automática hacia la puerta de envío adecuada para su carga fluida en los remolques de los camiones. Las cajas para envíos LTL se clasifican automáticamente hacia una estación de paletizado manual.
El módulo de recogida de cajas completas consta de palés con cajas colocados en una estructura de estanterías. Con las instrucciones que recibe desde un dispositivo portátil con radiofrecuencia, un operador se desplaza a la ubicación de un palé y recoge las cajas en la cinta transportadora que funciona en el centro del módulo de recogida de cajas completas. Se coloca una etiqueta preimpresa en cada caja. Las cajas del módulo de recogida de cajas completas se transportan a la expedición y se desvían de forma automática al remolque del camión correspondiente para la carga fluida o para el paletizado y envío LTL.
El software de los sistemas de control de almacenes gestiona el funcionamiento automático de toda la red de transporte y clasificación. Este software modular dirige el flujo de los contenedores de pedidos de cajas divididas hacia las zonas de recogida correspondientes. A partir de los datos de los escáneres de códigos de barras, el software activa los dispositivos de transferencia en ángulo recto para que las cajas se desvíen de forma automática a las zonas de recogida.
Asimismo, el software del WCS dirige el funcionamiento y el control del subsistema de la cinta transportadora del módulo de recogida de cajas completas, las estaciones de trabajo de embalaje y el subsistema de clasificación de envíos. Se dispone de información en tiempo real sobre la ubicación de las cajas en el sistema, las estadísticas de desvío/clasificación, los índices de lectura de códigos de barras y la recirculación de cajas. Un gráfico de la disposición del sistema muestra información en tiempo real sobre el estado y los atributos de rendimiento de cada subsistema: preparación, embalaje, combinación del embalaje, trash line y envío.
Los resultados
El diseño modular del sistema facilita la eficiencia operativa, la velocidad de procesamiento de pedidos y su precisión, a la vez que proporciona la flexibilidad necesaria para adaptarse a los cambios en las necesidades diarias. La capacidad de procesamiento de pedidos puede ampliarse si se aumenta la cantidad de trabajadores en los módulos de recogida de cajas divididas y cajas completas durante los períodos de máxima actividad. Cuando la actividad es baja, se pueden asignar menos operadores para atender el volumen de pedidos. Por otra parte, las estaciones de trabajo y los desvíos de las puertas de envío pueden ponerse o retirarse del servicio en función de la actividad diaria. La actividad actual es de alrededor de 500 a 700 pedidos al día (6 000 partidas), con unos 150 pedidos de reabastecimiento. La capacidad del sistema es de 25 000 partidas.
El personal de preparación de pedidos no tiene que circular por todo el almacén para localizar el inventario para la preparación. En su lugar, los diseños del sistema sitúan a los trabajadores en zonas de recogida donde el inventario está dispuesto en una configuración compacta de alta densidad. Esto permite que los trabajadores caminen menos y realicen más recogidas por hora. Asimismo, el sistema de rutas por zonas dirige los contenedores de pedidos solo a las zonas con recogida, lo que reduce el tiempo de procesamiento de los pedidos. El enfoque sistemático, combinado con la automatización del transporte y la clasificación, aporta disciplina, mejora del proceso y productividad laboral al proceso de recogida, embalaje y envío. También se ha diseñado el sistema para que se adapte al crecimiento; por ejemplo, los desviadores están preinstalados en el diseño de envío. En el futuro, cuando se requiera más capacidad, se conectará un transportador modular de línea descendente y se activará el software preconfigurado.