Polaris Shifts into Overdrive with New Distribution Center
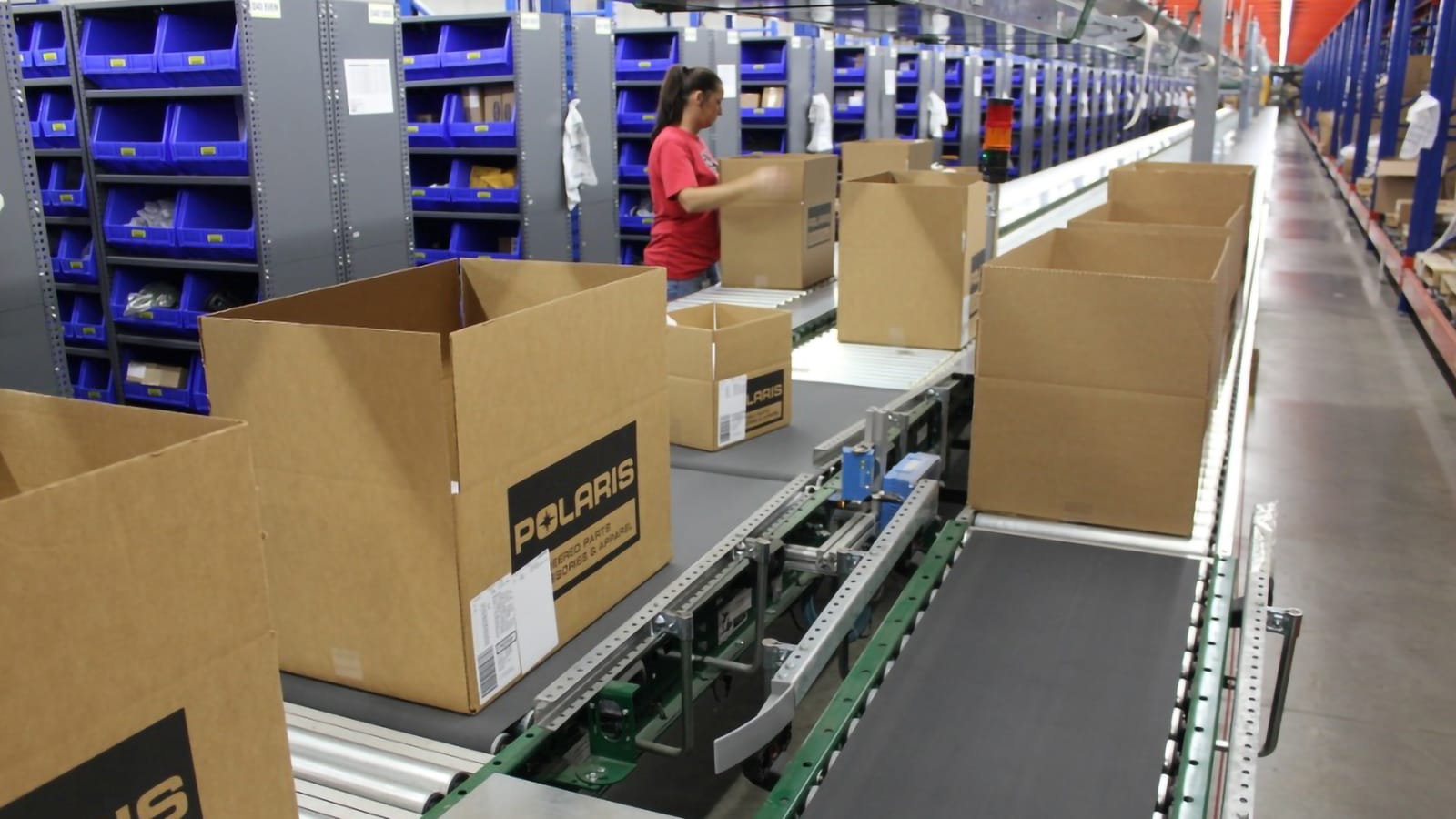
August 6, 2022
Polaris Industries, a manufacturer of motorized off-road and on-road vehicles, snowmobiles, and motorcycles, supports outdoor enthusiasts, riders and workers by delivering innovative, high quality vehicles, and services. To supply their dealers with parts, garments and accessories, Polaris has designed, built and implemented a new distribution center to service the dealers in the Eastern portion of North America.
Overview
To accommodate the high expectation of their dealers and assure that orders are processed with speed, accuracy and efficiency, Polaris needed a solution that could optimize the pick, pack and ship process. According to Paul Eickhoff, Director of Operations for Polaris, “Our winning advantage is our innovative culture, operational speed and flexibility, and passion to keep improving the parts distribution supply chain.”
Challenges
Previously, Polaris provided parts, garments and accessories to its dealers in the eastern region of the United States from their distribution center in Vermillion, South Dakota. To optimize service and response time for these dealers and support future company growth, a new distribution facility was required. From a network efficiency standpoint, Ohio was determined to be an ideal geographic location. An existing building was acquired and a new Polaris distribution center was born.
Solution
The distribution center design uses a strategic inventory location plan to optimize operational performance. Polaris parts that are picked in cases are centralized in the full case pick module. Parts that are picked as “pieces” are centralized into the split case pick module. Low velocity, large and non conveyable items are positioned together on pallets in racking. Furthermore, the SKUs are slotted within these areas by velocity.
The split case pick module is engineered around a methodology that brings the order container to the worker. This method is referred to as a Zone Route System. Workers remain in an assigned zone; efficiency is gained since workers do not roam the warehouse searching for picks, but instead are focused on picking a segment of the inventory located in a compact geography.
The split case pick module is configured with 4 zones. In each zone, SKUs are staged on flow rack or shelving. The zones are slotted based on attributes such as part family’s, velocity or cube utilization. The operational method is to route the order container only to the zones where there are picks.
To support the Zone Route System pick method, a conveyor network is provided to control the flow of order cartons into and out of the zones. One worker is stationed in each zone; however additional workers could be added during peak periods. Or, during periods of lower order volume, one worker could traverse multiple zones.
The conveyor layout features an accumulation conveyor spine that travels through the entire split case pick module with an exit and a siding for each zone. Each exit point consists of a bar code scanner and a right angle transfer to divert the order container into the pick zone. When the picks are completed, the operator pushes the order container carton back onto the central conveyor spine. If there are more picks, it moves to another zone(s); if no other picks, it travels directly to packing on the conveyor spine.
An order start workstation is located upstream of the conveyor spine in the split case pick module. A worker applies a unique bar code label to each carton, forms the carton and enters it onto the in-line tape applicator machine. The carton proceeds on the conveyor spine to the zone where inventory for the order is located.
Workers stationed in the zones use portable RF hand held devices to obtain picking instructions. When an order container arrives at the pick zone, the worker scans the bar code on the order container using the RF device. Next, pick instructions appear on the screen. At the pick location, the worker scans the SKU bar code on the product to confirm correct SKU. Items are picked and placed into the order container. The order container is manually pushed back onto the central conveyor spine.
Each split case order container is conveyed to the Pack & Ship sub-system. At the pack station, the order is checked for accuracy, weighed for shipping cost calculation, a shipping label is applied and the carton is sealed. These finished split case order cartons are conveyed to the shipping area where a sorter automatically diverts the cartons to the appropriate shipping door for fluid loading onto truck trailers. The cartons for LTL shipments are automatically sorted to a manual palletizing station.
The full case pick module consists of pallets with cases positioned on a rack structure. Using instructions from a portable RF hand held device, a worker travels to a pallet location and picks the case(s) onto the transportation conveyor that operates in the center of the full case pick module. A pre-printed label is attached to each case. Cases from the full case pick module are conveyed to shipping and automatically diverted to the appropriate truck trailer for fluid loading or to LTL palletizing and shipping.
The Warehouse Control Systems software manages the automated operation of the entire convey and sort network. This modular software directs the flow of the split case order containers into the appropriate pick zones. Using data from the bar code scanners, the software actives the right angle transfer devices allowing cartons to automatically divert into the pick zones.
The WCS software also directs the operation and control of the full case pick module conveyor sub-system, packing work stations, and shipping sorter sub-system. Real time information is available regarding carton location on the system, divert/sort statistics, bar code read rates, and carton re-circulation. A graphic of the system layout displays real time information about the status and performance attributes of each subsystem: picking, packing, packing merge, trash line, and shipping.
Results
The modular system design facilitates operational efficiency, order processing speed, and order accuracy while providing the flexibility to accommodate changes in daily requirements. Order processing capacity can be scaled up by increasing the number of workers in the split case and full case pick modules during peak periods. During periods of slow activity, fewer workers can be assigned to support the order volume. Furthermore, work stations and shipping door diverts can be placed into or taken out of service depending on daily activity. Current activity is approximately 500-700 orders per day (6,000 lines) with about 150 re-stocking orders. System capacity is 25,000 lines.
The picking staff is not required to circulate throughout the entire warehouse to locate inventory for picking. Instead, the system designs positions workers in pick zones where the inventory is arranged in a high density, compact configuration. This allows workers to walk less, and accomplish more picks per hour. In addition, the Zone Route System directs orders containers only to zones with picks, thereby reducing order processing time. The systemized approach, combined with convey and sort automation, brings discipline, process improvement and labor productivity to the pick, pack and ship process. In addition, the system is designed to accommodate growth; for example, diverters are pre-installed into the shipping layout. In the future, when additional capacity is required, modular down-line conveyor will be connected and the pre-configured software will be activated.