Polaris muda para Overdrive com novo centro de distribuição
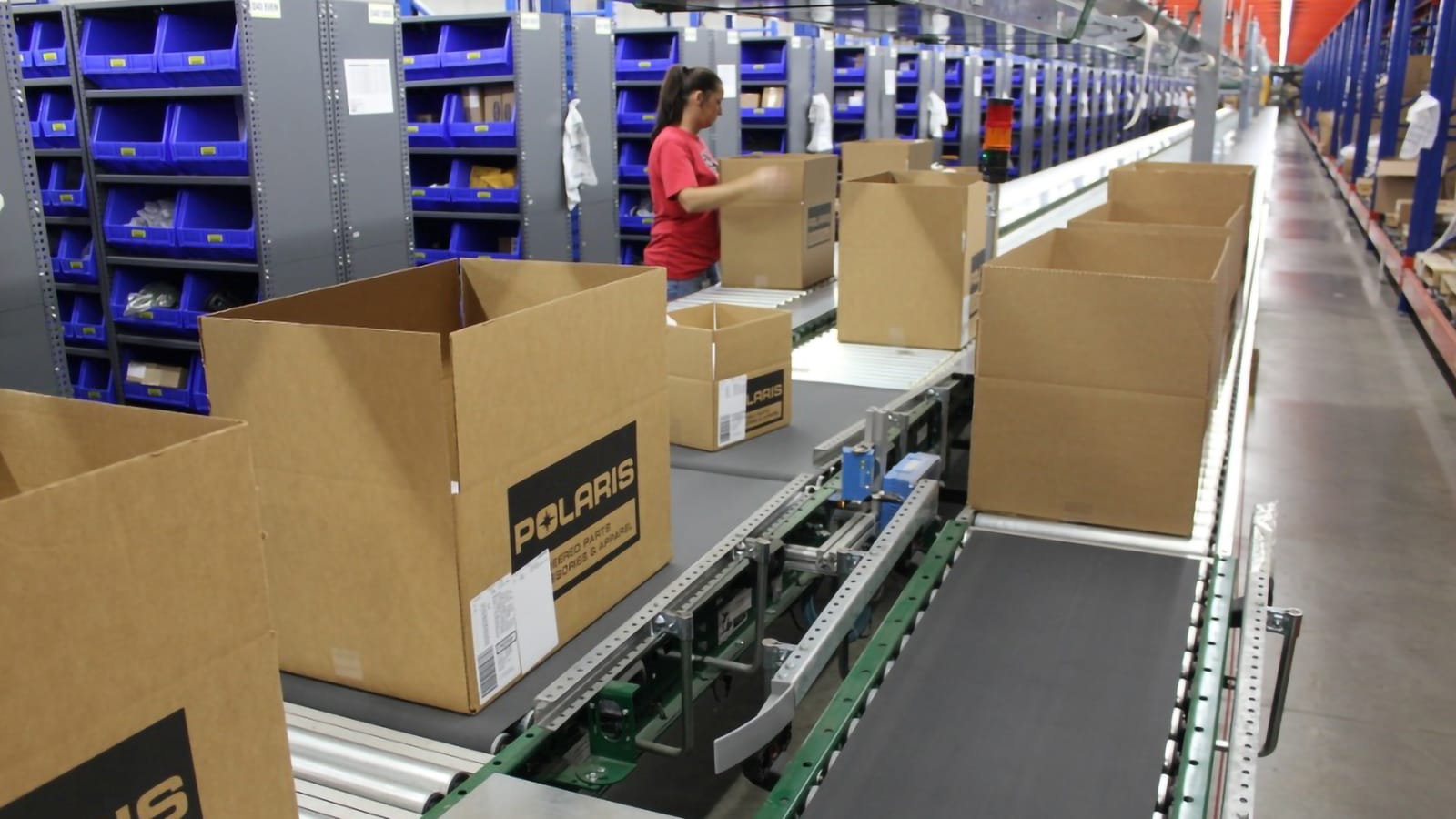
6 de agosto de 2022
A Polaris Industries, fabricante de veículos motorizados off-road e on-road, motos de neve e motocicletas, apoia entusiastas das atividades ao ar livre, motociclistas e trabalhadores, fornecendo veículos e serviços inovadores e de alta qualidade. Para abastecer seus revendedores com peças, roupas e acessórios, a Polaris projetou, construiu e implementou um novo centro de distribuição para atender os revendedores na parte leste da América do Norte.
Visão geral
Para acomodar a alta expectativa de seus revendedores e garantir que os pedidos sejam processados com rapidez, precisão e eficiência, a Polaris precisava de uma solução que pudesse otimizar o processo de separação, embalagem e envio. De acordo com Paul Eickhoff, Diretor de Operações da Polaris, “Nossa vantagem vencedora é nossa cultura inovadora, velocidade e flexibilidade operacional, além da paixão por continuar melhorando a cadeia de suprimentos de distribuição de peças”.
Desafios
Anteriormente, a Polaris fornecia peças, roupas e acessórios para seus revendedores na região leste dos Estados Unidos a partir de seu centro de distribuição em Vermillion, Dakota do Sul. Para otimizar o serviço e o tempo de resposta para esses revendedores e apoiar o crescimento futuro da empresa, foi necessária uma nova instalação de distribuição. Do ponto de vista da eficiência da rede, Ohio seria a localização geográfica ideal. Um edifício existente foi adquirido e um novo centro de distribuição Polaris nasceu.
Solução
O projeto do centro de distribuição usa um plano estratégico de localização de estoque para otimizar o desempenho operacional. As peças da Polaris separadas em caixas são centralizadas no módulo de separação de caixas cheias. As peças separadas como “partes” são centralizadas no módulo de separação de caixa dividida. Os itens de baixa velocidade, grandes e não transportáveis por esteira são posicionados juntos em paletes nas estantes. Além disso, as SKUs são inseridas nessas áreas por velocidade.
O módulo de separação de caixas divididas é projetado em torno de uma metodologia que leva o contêiner do pedido ao trabalhador. Este método é conhecido como Sistema de rotas de zonas. Os trabalhadores permanecem em uma zona designada. A eficiência é obtida porque os trabalhadores não percorrem o armazém fazendo a separação, mas, em vez disso, estão focados em separar um segmento do estoque localizado em uma área compacta.
O módulo de separação de caixa dividida é configurado com 4 zonas. Em cada zona, as SKUs são colocadas em rack de fluxo ou prateleiras. As zonas são divididas com base em atributos como família de peças, velocidade ou utilização do cubo. O método operacional é direcionar o contêiner de pedidos apenas para as zonas onde há separações.
Para dar suporte ao método de separação do Sistema de rotas de zonas, uma rede de transportadores é fornecida para controlar o fluxo de caixas de pedidos dentro e fora das zonas. Um trabalhador permanece em cada zona. No entanto, outros trabalhadores podem ser adicionados durante os períodos de pico. Ou, durante períodos de menor volume de pedidos, um trabalhador pode atravessar várias zonas.
O layout do transportador apresenta uma coluna do transportador de acumulação que percorre todo o módulo de separação de caixas divididas com uma saída e um desvio para cada zona. Cada ponto de saída consiste em um scanner de código de barras e uma transferência em ângulo reto para desviar o contêiner do pedido para a zona de separação. Quando as separações são concluídas, o operador empurra a caixa do contêiner do pedido de volta para a coluna central do transportador. Se houver mais separações, ele se move para outra(s) zona(s). Se não houver outras separações, ele vai diretamente para a embalagem na coluna do transportador.
Uma estação de trabalho de início de pedido fica a montante da coluna do transportador no módulo de separação de caixas divididas. Um trabalhador aplica uma etiqueta de código de barras exclusiva em cada caixa, forma a caixa e a insere na máquina aplicadora de fita em linha. A caixa segue na coluna do transportador até a zona onde o estoque do pedido está localizado.
Os trabalhadores estacionados nas zonas usam dispositivos portáteis de RF para obter instruções de separação. Quando um contêiner de pedido chega à zona de separação, o trabalhador digitaliza o código de barras no contêiner de pedido usando o dispositivo de RF. Em seguida, as instruções de separação aparecem na tela. No local de separação, o trabalhador digitaliza o código de barras da SKU no produto para confirmar a SKU correta. Os itens são separados e colocados no contêiner do pedido. O contêiner do pedido é empurrado manualmente de volta para a coluna central do transportador.
Cada contêiner de pedido de caixa dividida é transportado para o subsistema Pack & Ship. Na estação de embalagem, o pedido é verificado quanto à precisão, pesado para cálculo do custo de envio, uma etiqueta de envio é aplicada e a caixa é lacrada. Essas caixas de pedidos divididas acabadas são transportadas para a área de expedição, onde um classificador automaticamente as desvia para a porta de expedição apropriada para carregamento fluido nos caminhões. As caixas para remessas LTL são classificadas automaticamente para uma estação de paletização manual.
O módulo de separação de caixa cheia consiste em paletes com caixas posicionadas em uma estrutura de rack. Usando instruções de um dispositivo portátil de RF, um trabalhador se desloca para um local de palete e separa a(s) caixa(s) na esteira de transporte que opera no centro do módulo de separação de caixa cheia. Uma etiqueta pré-impressa é anexada a cada caixa. As caixas do módulo de separação de caixas cheias são transportadas para expedição e automaticamente desviadas para o caminhão apropriado para carregamento fluido ou para paletização e expedição LTL.
O software dos Sistemas de controle de armazém gerencia a operação automatizada de toda a rede de transporte e classificação. Este software modular direciona o fluxo dos contêineres de pedidos de caixas divididas para as zonas de separação apropriadas. Usando dados dos leitores de código de barras, o software ativa os dispositivos de transferência em ângulo reto, permitindo que as caixas sejam desviadas automaticamente para as zonas de separação.
O software do WCS também direciona a operação e o controle do subsistema transportador do módulo de separação de caixas cheias, das estações de trabalho de embalagem e do subsistema classificador de expedição. Informações em tempo real estão disponíveis sobre a localização da caixa no sistema, estatísticas de desvio/classificação, taxas de leitura de código de barras e recirculação da caixa. Um gráfico do layout do sistema exibe informações em tempo real sobre o status e os atributos de desempenho de cada subsistema: separação, embalagem, mesclagem de embalagem, linha de descarte e expedição.
Resultados
O design modular do sistema facilita a eficiência operacional, a velocidade de processamento de pedidos e a precisão do pedido, ao mesmo tempo em que oferece flexibilidade para acomodar mudanças nos requisitos diários. A capacidade de processamento de pedidos pode ser ampliada aumentando o número de trabalhadores nos módulos de separação de caixa dividida e caixa cheia durante os períodos de pico. Durante períodos de atividade lenta, menos trabalhadores podem ser designados para dar suporte ao volume de pedidos. Além disso, estações de trabalho e desvios da porta de expedição podem ser colocados ou retirados de serviço dependendo da atividade diária. A atividade atual é de aproximadamente 500-700 pedidos por dia (6.000 linhas) com cerca de 150 pedidos de reabastecimento. A capacidade do sistema é de 25.000 linhas.
A equipe de separação não é obrigada a circular por todo o armazém para localizar o estoque para separação. Em vez disso, os projetos do sistema posicionam os trabalhadores em zonas de separação onde o estoque é organizado em uma configuração compacta e de alta densidade. Isso permite que os trabalhadores andem menos e realizem mais separações por hora. Além disso, o Sistema de rotas de zonas direciona os contêineres de pedidos apenas para as zonas com separação, reduzindo assim o tempo de processamento dos pedidos. A abordagem sistematizada, combinada com a automação de transporte e classificação, traz disciplina, melhoria de processos e produtividade de mão de obra ao processo de separação, embalagem e envio. Além disso, o sistema foi projetado para acomodar o crescimento, por exemplo, os desviadores são pré-instalados no layout de expedição. No futuro, quando for necessária capacidade adicional, o transportador modular descendente será conectado e o software pré-configurado será ativado.