Polaris passe à la vitesse supérieure avec un nouveau centre de distribution
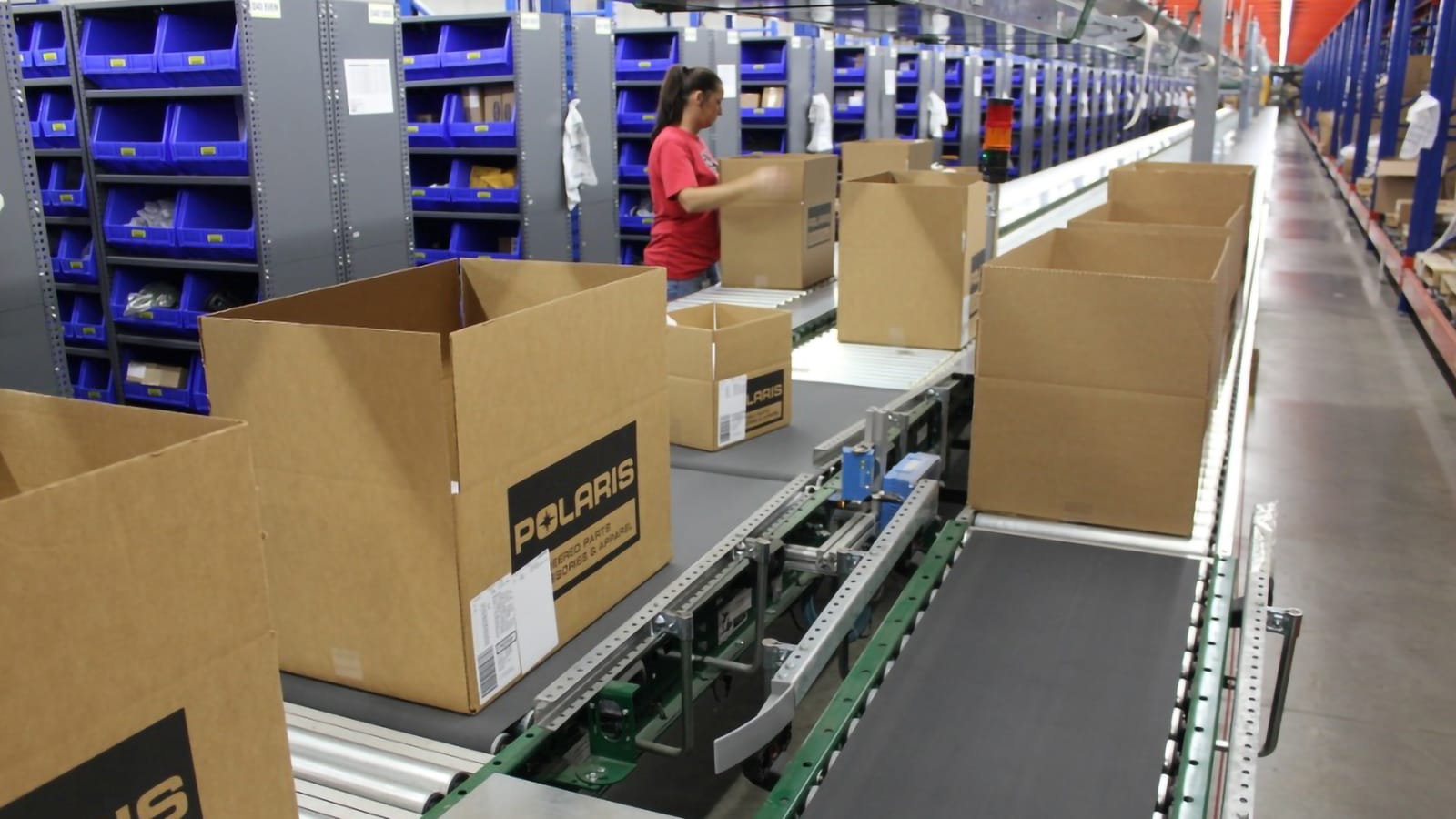
6 août 2022
Polaris Industries, fabricant de véhicules motorisés tout-terrain et routiers, de motoneiges et de motocyclettes, soutient les amateurs de plein air, les motocyclistes et les travailleurs en leur fournissant des véhicules et des services innovants et de haute qualité. Pour approvisionner ses concessionnaires en pièces, vêtements et accessoires, Polaris a conçu, construit et mis en place un nouveau centre de distribution pour desservir les concessionnaires de la partie Est de l’Amérique du Nord.
Vue d’ensemble
Pour répondre aux attentes élevées de ses concessionnaires et veiller à ce que les commandes soient traitées avec diligence, précision et efficacité, Polaris avait besoin d’une solution capable d’optimiser le processus de préparation, d’emballage et d’expédition. Selon Paul Eickhoff, Directeur des opérations chez Polaris, « notre avantage comparatif est notre culture de l’innovation, la rapidité et la flexibilité de nos opérations, et notre passion pour continuer à améliorer la chaîne d’approvisionnement de la distribution des pièces. »
Les défis
Auparavant, Polaris fournissait des pièces, des vêtements et des accessoires à ses concessionnaires de la région Est des États-Unis à partir de son centre de distribution de Vermillion, dans le Dakota du Sud. Pour optimiser le service et le temps de réponse pour ces concessionnaires et pour soutenir la croissance future de l’entreprise, une nouvelle installation de distribution était nécessaire. Du point de vue de l’efficacité du réseau, il a été déterminé que l’Ohio était un emplacement géographique idéal. Un bâtiment existant a été acquis et un nouveau centre de distribution Polaris a vu le jour.
Les solutions
La conception du centre de distribution s’appuie sur un plan stratégique de localisation des stocks pour optimiser les performances opérationnelles. Les pièces Polaris qui sont prélevées dans des caisses sont centralisées dans le module de prélèvement de caisses complètes. Les pièces qui sont prélevées en tant que « éléments » sont centralisées dans le module de prélèvement de caisses fractionnées. Les articles à faible vitesse, volumineux et non transportables sont placés ensemble sur des palettes dans des rayonnages. En outre, les UGS sont placées dans ces zones en fonction de leur vitesse.
Le module de préparation de commandes pour caisses fractionnées est conçu suivant une méthodologie qui amène le conteneur de la commande vers le travailleur. Cette méthode est appelée « système d’itinéraire par zone ». Les travailleurs restent dans la zone qui leur a été assignée ; l’efficacité est accrue puisque les travailleurs ne parcourent pas l’entrepôt à la recherche de prélèvements, mais se concentrent sur le prélèvement d’un segment des stocks situés dans une zone géographique compacte.
Le module de prélèvement de caisses fractionnées est configuré avec 4 zones. Dans chaque zone, les unités de gestion des stocks sont disposées sur des racks de stockage ou des étagères. Les zones sont classées en fonction d’attributs tels que la famille de pièces, la vitesse ou l’utilisation des cubes. La méthode opérationnelle consiste à acheminer le conteneur de commande uniquement vers les zones où il y a des prélèvements.
Pour prendre en charge la méthode de prélèvement du système d’acheminement par zone, un réseau de convoyeurs est prévu pour contrôler le flux des cartons de commande tant à l’intérieur qu'en dehors des zones. Un travailleur est posté dans chaque zone, mais des travailleurs supplémentaires pourraient être ajoutés pendant les périodes de pointe. Ou, pendant les périodes de faible volume de commandes, un seul travailleur pourrait parcourir plusieurs zones.
La disposition du convoyeur comprend un convoyeur d’accumulation qui parcoure l’ensemble du module de préparation de commandes pour caisses fractionnées, avec une sortie et une voie de garage pour chaque zone. Chaque point de sortie est comprend un lecteur de codes-barres et un transfert à angle droit pour dévier le conteneur de commande vers la zone de prélèvement. Lorsque les prélèvements sont terminés, l’opérateur repousse le carton contenant la commande sur la colonne centrale du convoyeur. S’il y a d’autres prélèvements, il passe à une ou plusieurs autres zones ; s’il n’y a pas d’autres prélèvements, il passe directement à l’emballage sur la colonne du convoyeur.
Un poste de travail pour le démarrage des commandes est situé en amont de la colonne du convoyeur dans le module de préparation de commandes pour caisses fractionnées. Un travailleur appose une étiquette à code-barres unique sur chaque carton, forme le carton et l’introduit dans la machine d’apposition de ruban en ligne. Le carton avance sur la colonne du convoyeur jusqu’à la zone où se trouve le stock pour la commande.
Les travailleurs stationnés dans les zones utilisent des appareils portables RF pour obtenir des instructions de prélèvement. Lorsqu’un conteneur de commande arrive dans la zone de prélèvement, le travailleur scanne le code à barres du conteneur de commande à l’aide du dispositif RF. Ensuite, des instructions de prélèvement apparaissent à l’écran. Au point de prélèvement, le travailleur scanne le code-barres UGS sur le produit pour confirmer que c’est la bonne UGS. Les articles sont prélevés et placés dans le conteneur de la commande. Le conteneur de la commande est repoussé manuellement sur la colonne centrale du convoyeur.
Chaque conteneur de commande de caisses fractionnées est acheminé vers le sous-système Pack & Ship. Au poste d’emballage, l’exactitude de la commande est vérifiée, la commande est pesée pour le calcul des frais d’expédition, une étiquette d’expédition est apposée et le carton est scellé. Ces cartons finis sont acheminés vers la zone d’expédition où une trieuse dirige automatiquement les cartons vers la porte d’expédition appropriée pour un chargement fluide sur les remorques des camions. Les cartons des expéditions LTL sont automatiquement triés vers un poste de palettisation manuelle.
Le module complet de préparation des commandes est constitué de palettes contenant des caisses placées sur une structure de rayonnage. En utilisant les instructions d’un appareil portable RF, un travailleur se rend à l’emplacement d’une palette et prélève la ou les caisses sur le convoyeur de transport qui fonctionne au centre du module de prélèvement de caisses complètes. Une étiquette pré-imprimée est apposée sur chaque caisse. Les caisses provenant du module de prélèvement de caisses complètes sont acheminées vers l’expédition et sont automatiquement dirigées vers la remorque du camion approprié pour un chargement fluide ou pour une palettisation et une expédition en LTL.
Le logiciel du Système de contrôle des entrepôts gère le fonctionnement automatisé de l’ensemble du réseau de convoyage et de tri. Ce logiciel modulaire dirige le flux des conteneurs de la commande de caisses fractionnées vers les zones de prélèvement appropriées. Grâce aux données fournies par les lecteurs de codes à barres, le logiciel active les dispositifs de transfert à angle droit, ce qui permet aux cartons de se diriger automatiquement vers les zones de prélèvement.
Le logiciel WCS commande aussi le fonctionnement et le contrôle du sous-système de convoyeur du module de prélèvement des caisses, des postes de travail d’emballage et du sous-système de trieuse d’expédition. Des informations en temps réel sont disponibles concernant l’emplacement des cartons sur le système, les statistiques de déviation/tri, les taux de lecture des codes à barres et la recirculation des cartons. Un graphique de l’agencement du système affiche des informations en temps réel sur l’état et les attributs de performance de chaque sous-système : le prélèvement, l’emballage, la fusion d’emballages, la ligne de déchets et l’expédition.
Les résultats
La conception modulaire du système facilite l’efficacité opérationnelle, la vitesse de traitement des commandes et la précision des commandes, tout en offrant la flexibilité nécessaire pour s’adapter aux exigences quotidiennes en perpétuel changement. Il est possible d’accroître la capacité de traitement des commandes en augmentant le nombre de travailleurs dans les modules de préparation de commandes pour caisses fractionnées et pour caisses complètes pendant les périodes de pointe. Pendant les périodes de faible activité, moins de travailleurs peuvent être affectés pour soutenir le volume de commandes. En outre, les postes de travail et les déviateurs de portes d’expédition peuvent être mis en service ou hors service en fonction de l’activité quotidienne. L’activité actuelle est d’environ 500 à 700 commandes par jour (6 000 lignes) avec environ 150 commandes de réapprovisionnement. La capacité du système est de 25 000 lignes.
Le personnel chargé du prélèvement n’a pas besoin de circuler dans tout l’entrepôt pour localiser les stocks à prélever. Au contraire, le système est conçu pour positionner les travailleurs dans des zones de prélèvement où les stocks sont disposés selon une configuration compacte et à haute densité. Cela permet aux travailleurs de marcher moins et d’effectuer plus de prélèvements par heure. En outre, le système d’acheminement par zone dirige les conteneurs de commande uniquement vers les zones où se trouvent des prélèvements, ce qui réduit le temps de traitement des commandes. L’approche systématisée, combinée à l’automatisation du convoyage et du tri, confère discipline, amélioration des processus et productivité à la main-d’œuvre et au processus de prélèvement, d’emballage et d’expédition. En outre, le système est conçu pour s’adapter à la croissance ; par exemple, des déviateurs sont préinstallés dans le plan d’expédition. À l’avenir, lorsque des capacités supplémentaires seront nécessaires, un convoyeur modulaire en aval sera connecté et le logiciel préconfiguré sera activé.