Automatisierung in der Fertigung – die 10 wichtigsten Trends
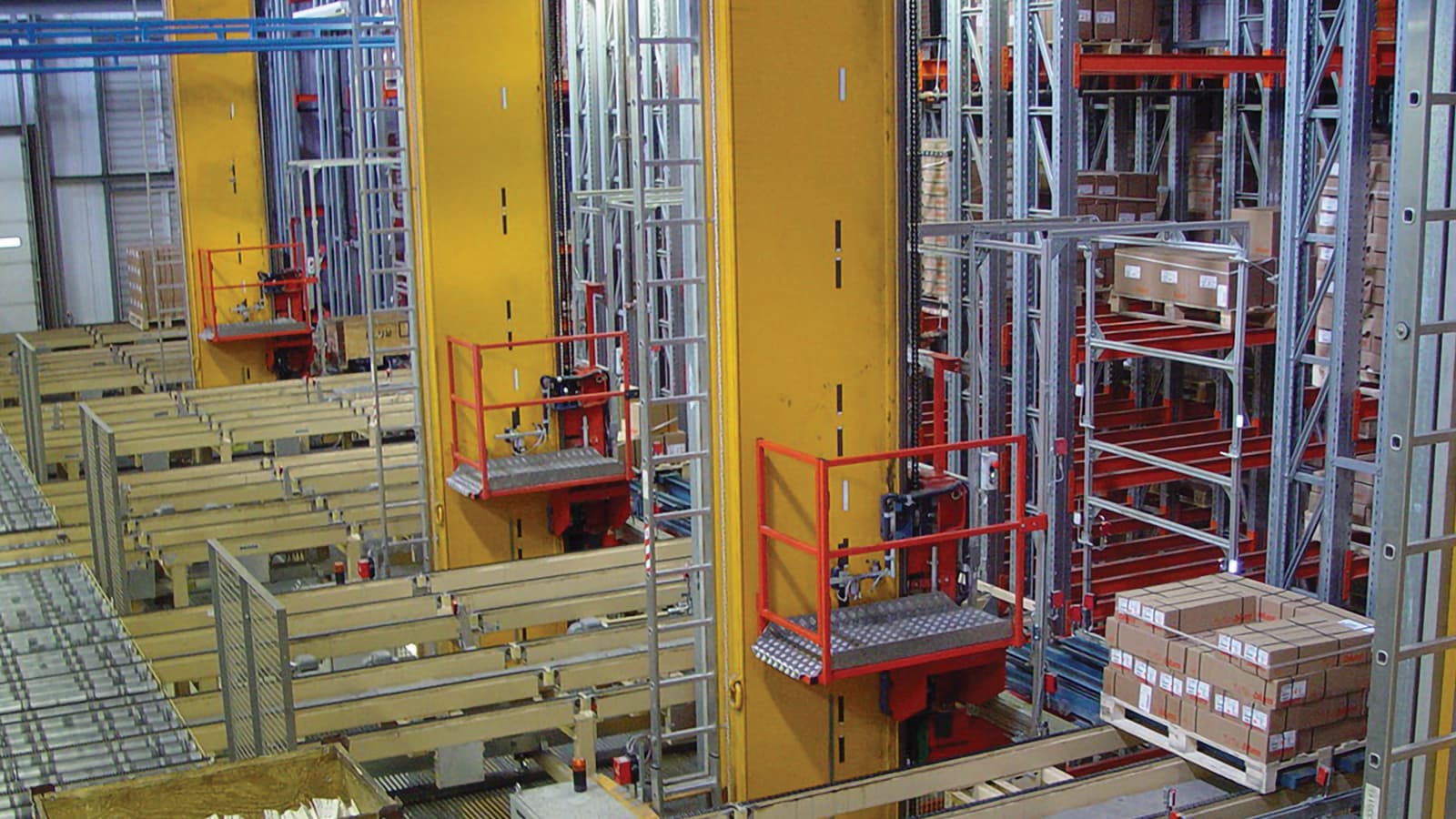
Was bringt die Hersteller von Gebrauchsgütern dazu, die Lagerhaltung zu automatisieren? Um wettbewerbsfähig zu bleiben, müssen Hersteller ihre Produktivität steigern und die Kosteneffizienz verbessern. Tendenziell wird der Schwerpunkt auf den Montageprozess gelegt, und andere kritische Elemente, die sich auf die Gesamtkosten der Herstellung auswirken, werden übersehen. Die Verwaltung des Wareneingangs, der unfertigen Erzeugnisse (Work in Progress, WIP) und der ausgehenden Fertigprodukte ist zu einer Schlüsselkomponente geworden, da die Trends auf dem Fertigungsmarkt die Anforderungen an diese Funktion erhöht haben. In diesem Whitepaper werden 10 Faktoren aufgezeigt, von der schlanken Produktion bis hin zu steigenden Kraftstoffkosten, die den verstärkten Einsatz von automatisierten Systemen erforderlich machen.
1. Schlanke Produktion
Der Prozess der schlanken Fertigung ist seit Jahrzehnten bekannt und unterstützt die Umstellung vom „Push“-Betrieb auf „Build to order“-Betrieb. Bei diesen Pull-Systemen steigt der Bedarf an Echtzeittransparenz und -kontrolle des innerbetrieblichen Bestands, einschließlich des eingehenden Materials, des WIP-Materials und der ausgehenden Fertigwaren.
2. Outsourcing
Da sich die Hersteller zunehmend auf ihre wichtigsten Marktunterscheidungsmerkmale und die Prozesse mit der höchsten Wertschöpfung konzentrieren, werden weniger kritische Bereiche ausgelagert. Für viele Hersteller hat dieser Trend die Zahl der Zulieferer deutlich erhöht, die eine höhere Raffinesse in den Prozessen der Annahme, Einlagerung und Kommissionierung vor der Produktion benötigen.
3. Off-shoring
Ähnlich wie beim Outsourcing nutzen die Kunden die Vorteile von Niedriglohnländern für die Bereitstellung verschiedener Komponenten. Die Kehrseite dieser Geschäftsmethode sind erheblich längere Vorlaufzeiten bei ausländischen Lieferanten und größere Bestellmengen, die erforderlich sind, um die Produktion ohne Unterbrechung aufrechtzuerhalten. Die Platzverfügbarkeit wird schnell zu einem Hauptproblem für die Produktionsstätte. Das veranlasst die Hersteller gegebenenfalls dazu, Kosten für externe Lager in Kauf zu nehmen, die zur Dosierung der Materialien für das Werk verwendet werden. Die Verbesserung von Lagerdichte und Raumnutzung kann die Lösung sein, um andere kostspielige Alternativen zu vermeiden.
4. Kürzere Produktlebenszyklen
Kürzere Produktlebenszyklen erfordern eine hohe Flexibilität auf der Baustelle und eine schnellere Markteinführung von neuen Produkten. Die Produkttransparenz in Bezug auf die Lagerautomatisierung sorgt dafür, dass die Verwaltung und Lieferung von Materialien an die Produktion ein einheitlicher Prozess ist. Durch die Reduzierung oder Eliminierung der menschlichen Komponente kann der Materialfluss mit den Produktionsanforderungen Schritt halten, sodass sich die Hersteller auf die Einführung neuer Produkte, Montageprozesse und Qualität konzentrieren können. Containerisierung ist der Schlüssel für höchste Flexibilität und Transparenz im Materialflussprozess.
5. Massenanfertigung
Die Verbraucher verlangen nach Produkten, die auf ihre eigenen Vorlieben zugeschnitten sind, was die Hersteller dazu veranlasst, eine Vielzahl von Konfigurationen, Farben und Komponentenoptionen anzubieten (SKU-Proliferation). Dieser Trend führt zu Platzproblemen in der Produktion. Häufig wird dann Inventar in den Gängen gelagert oder es entstehen behelfsmäßige Überkopfkonstruktionen für die Lagerung am Fließband. Das Ergebnis sind Staus und Produktivitätsverluste. Eine sequenzierte Lieferung von Komponenten und Lagerlösungen am Verwendungsort, die die vertikale Höhe ausnutzen, können diese Probleme lösen und die Produktivität steigern.
6. Globaler Wettbewerb
Der globale Wettbewerb ist die größte Bedrohung für Produktionsunternehmen im ganzen Land. Mehr denn je sind die Unternehmen gezwungen, nach Lösungen zu suchen, die die Gesamtkosten der Produktion senken. Geringere Arbeitskosten, bessere Raumausnutzung, weniger Lagerbestand, höherer Durchsatz und verbesserte Versandgenauigkeit sind nur einige der Elemente, die sich positiv auswirken, wenn die richtige Lagerlösung gewählt wird.
7. Pull-Prinzip in der Lieferkette
Da alle Glieder der Verbraucherversorgungskette versuchen, ihre Kosten zu senken und ihre Wettbewerbsfähigkeit zu steigern, werden die Bestände in der Versorgungskette weiter nach oben zum Hersteller verschoben. Unabhängig davon, ob der Versand direkt oder an eine zentrale Vertriebseinrichtung erfolgt, müssen die Hersteller kleinere, häufigere Lieferungen in einem engeren Zeitfenster versenden. Der Fertigwarenprozess einschließlich Lagerung, Kommissionierung, Auftragsvorbereitung und Versand wird in Frage gestellt.
8. Rückverfolgung
Die Anforderungen an die Produktverfolgung steigen mit den Industrienormen und -vorschriften weiter an. Effektive Lagerlösungen in Verbindung mit der richtigen Tracking-Infrastruktur sind die Schlüsselelemente der Datenerfassung.
9. Grüne Initiativen
Die Hersteller beteiligen sich an grünen Initiativen und überprüfen ihren derzeitigen Kohlenstoff-Fußabdruck auf Verbesserungen. Effizientere Gerätetechnologien und Steuerungsmethoden in der Automatisierung können die Gesamtgleichung verbessern.
10. Steigende Treibstoffkosten
Steigende Treibstoffkosten wirken sich auf die gesamte Lieferkette einschließlich der Hersteller aus. Die richtige Lagerlösung in Verbindung mit Warehouse Control Software (WCS) optimiert die Auftragskonsolidierung und verbessert die Dichte der Anhängerbeladung.
Fazit
Jeder in diesem Papier erwähnte Trend hat entsprechende Auswirkungen, mit denen die meisten Hersteller heute konfrontiert sind. Es bestand immer die Tendenz, sich auf den Montage-/Produktionsprozess zu konzentrieren und andere kritische Elemente zu übersehen, die die Gesamtkosten der Herstellung senken können.
Automatisierte Lösungen für den Materialtransport und die Lagerung von eingehenden Materialien, Produktionsmaterial und Fertigwarenbeständen senken die Gesamtkosten der Produktion, indem sie den Arbeitsaufwand und die Lagerbestände reduzieren und gleichzeitig die Genauigkeit, den Durchsatz und die Raumnutzung verbessern. Darüber hinaus werden die Hersteller ihren Kundenservice durch eine verbesserte Lieferleistung und Qualität verbessern.
Es geht darum, Ihren Materialfluss zu organisieren und zu verfolgen, vom Eingang und der Einlagerung der Rohstoffe bis zur Kommissionierung und dem Versand der Fertigwaren. Es ist jedoch zu beachten, dass verschiedene Technologien und Lösungen zu unterschiedlichen Ergebnissen führen können. Die endgültige Lösung sollte sorgfältig mit den strategischen Geschäftsplanzielen des Herstellers abgestimmt werden.