10 najważniejszych trendów napędzających automatyzację w produkcji
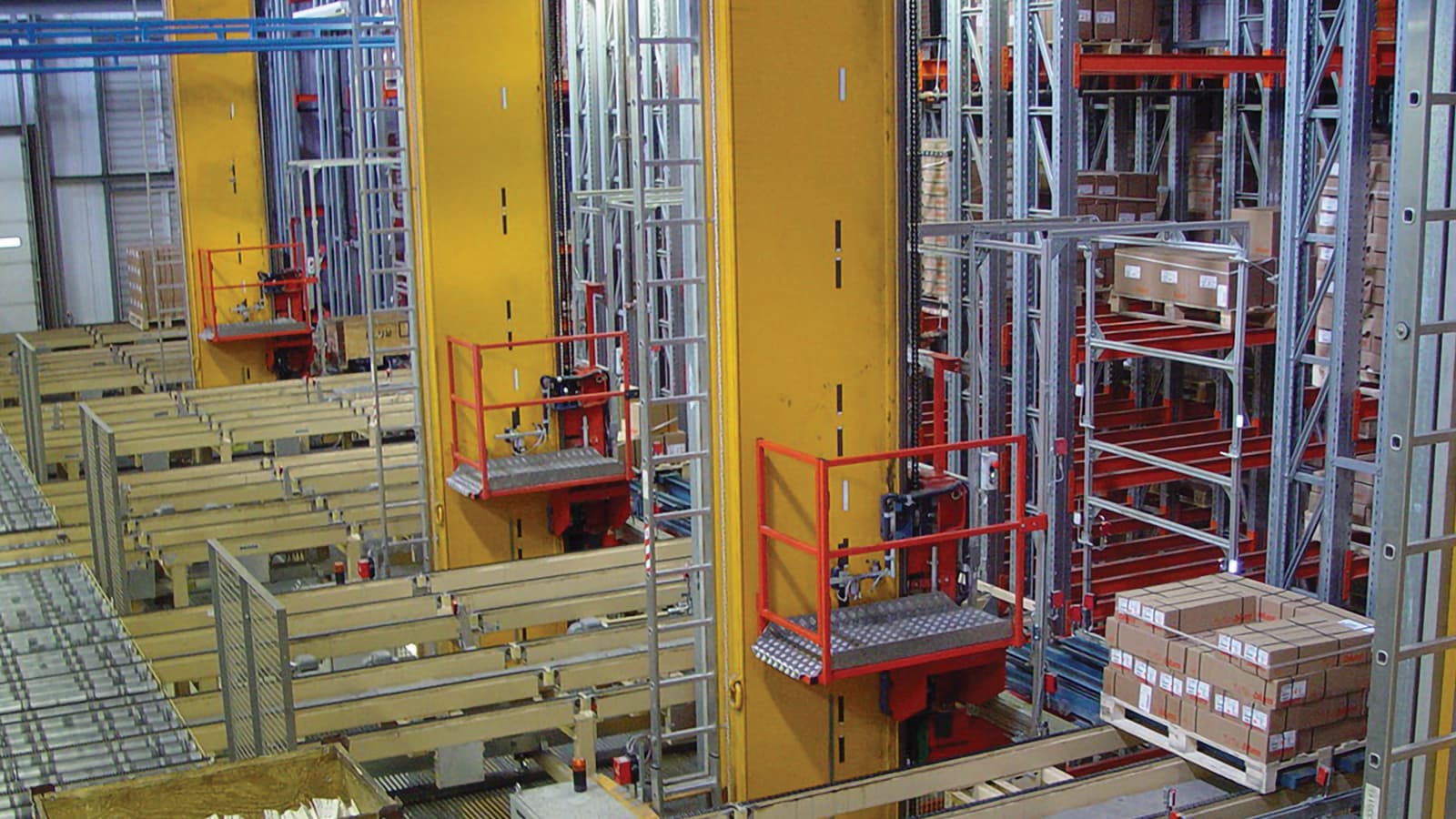
Co skłania producentów dóbr trwałych do automatyzacji funkcji magazynowania? Aby zachować konkurencyjność, producenci wymagają zwiększonej wydajności i lepszej efektywności kosztowej. Tendencją jest koncentrowanie się głównie na procesie montażu i pomijanie innych krytycznych elementów systemu door to door, które mają wpływ na całkowity koszt produkcji. Funkcja zarządzania produkcją przychodzącą, produkcją w toku (WIP) i wychodzącą produkcją gotową stała się kluczowym elementem, ponieważ trendy na rynku produkcyjnym zwiększyły na nie zapotrzebowanie. W niniejszym opracowaniu przedstawiono 10 czynników, począwszy od lean manufacturing, a skończywszy na rosnących kosztach paliwa, które powodują konieczność szerszego stosowania systemów zautomatyzowanych.
1. Lean manufacturing (odchudzona produkcja)
Proces odchudzonej produkcji jest realizowany od dziesięcioleci i wspiera transformację od operacji typu „push” do operacji typu „build to order” (składany na zamówienie). Systemy typu „pull” zwiększają zapotrzebowanie na widoczność i kontrolę w czasie rzeczywistym zapasów w zakładzie, w tym materiałów przychodzących, materiałów WIP oraz wychodzących wyrobów gotowych.
2. Outsourcing
W miarę jak producenci koncentrują się na kluczowych czynnikach różnicujących rynek i procesach o najwyższej wartości dodanej, mniej istotne elementy zlecają firmom zewnętrznym. Trend ten znacznie zwiększył liczbę dostawców dla wielu producentów wymagających bardziej zaawansowanych procesów odbioru, odkładania na miejsce i kompletacji przed rozpoczęciem produkcji.
3. Zamówienia zagraniczne
Podobnie jak w przypadku outsourcingu, klienci wykorzystują kraje o niskich kosztach do zaopatrywania się w różne komponenty. Wadą tej metody biznesowej jest znacznie wydłużony czas realizacji zamówień od zagranicznych dostawców oraz większe rozmiary zamówień, które są wymagane do utrzymania produkcji bez przerw. Dostępność przestrzeni szybko staje się kluczowym problemem dla zakładu produkcyjnego, co czasami zmusza producentów do ponoszenia kosztów magazynów poza własnym zakładem, wykorzystywanych do dozowania materiałów do zakładu. Poprawa gęstości składowania i wykorzystania przestrzeni może być rozwiązaniem pozwalającym wyeliminować inne kosztowne alternatywy.
4. Krótsze cykle życia produktu
Krótsze cykle życia produktów wymagają dużej elastyczności w miejscu pracy i szybszego wprowadzania nowych produktów na rynek. Przejrzystość produktu w odniesieniu do automatyzacji magazynowania sprawia, że zarządzanie i dostarczanie materiałów do produkcji stanowi spójny proces. Dzięki ograniczeniu lub wyeliminowaniu czynnika ludzkiego, przepływ materiałów nadąża za wymaganiami produkcyjnymi, co pozwala producentom skupić się na wprowadzaniu nowych produktów, procesach montażowych i jakości. Wspólna konteneryzacja jest kluczem do uzyskania najwyższej elastyczności i przejrzystości w procesie przepływu materiałów.
5. Masowa personalizacja
Konsumenci żądają produktów dostosowanych do ich własnych preferencji, co zmusza producentów do tworzenia wielu konfiguracji, kolorów i opcji komponentów (mnożenie jednostek magazynowych). Ten trend ujawnia problemy związane z ograniczeniem przestrzeni na hali produkcyjnej, co często prowadzi do konieczności umieszczania zapasów w korytarzach lub stosowania prowizorycznych konstrukcji podwieszanych do magazynowania przy linii produkcyjnej. Ogólnym skutkiem jest zatłoczenie i spadek wydajności. Sekwencyjne dostawy komponentów i rozwiązania magazynowe w miejscu użytkowania, które wykorzystują pionową wysokość, mogą rozwiązać te problemy i poprawić poziom wydajności.
6. Globalna konkurencja
Globalna konkurencja stanowi zagrożenie numer jeden dla firm produkcyjnych w całym kraju. Obecnie, bardziej niż kiedykolwiek, firmy są zmuszone do poszukiwania rozwiązań, które pozwolą obniżyć całkowite koszty produkcji. Niższe koszty pracy, lepsze wykorzystanie przestrzeni, mniejsza ilość zapasów w magazynie, większa przepustowość i lepsza dokładność wysyłek to tylko niektóre z elementów, które przyniosą pozytywne efekty po wybraniu odpowiedniego rozwiązania magazynowego.
7. Planowanie łańcucha dostaw
Ponieważ wszystkie elementy łańcucha dostaw dla konsumentów dążą do obniżenia kosztów i zwiększenia konkurencyjności, zapasy są przesuwane dalej w górę łańcucha dostaw, do producenta. Niezależnie od tego, czy wysyłka odbywa się bezpośrednio, czy do centralnego obiektu dystrybucyjnego, producenci muszą realizować mniejsze, częstsze dostawy w krótszym czasie. Proces produkcji wyrobów gotowych, obejmujący magazynowanie, kompletację, przygotowywanie zamówień i wysyłkę, staje się wyzwaniem.
8. Identyfikacja i monitorowanie produktów
Wymagania dotyczące śledzenia produktów stale rosną wraz z normami i przepisami branżowymi. Efektywne rozwiązania magazynowe w połączeniu z odpowiednią infrastrukturą śledzenia stanowią kluczowe elementy pozyskiwania danych.
9. Zielone inicjatywy
Producenci angażują się w inicjatywy ekologiczne, analizując swój obecny ślad węglowy w celu jego poprawy. Bardziej wydajne technologie sprzętowe i metody kontroli stosowane w automatyzacji mogą poprawić ogólne wyniki.
10. Rosnące koszty paliwa
Rosnące koszty paliwa mają wpływ na cały łańcuch dostaw, w tym na producenta. Właściwe rozwiązanie magazynowe wraz z systemem sterowania magazynem (WCS) zoptymalizuje konsolidację zamówień i poprawi gęstość załadunku naczep.
Wnioski
Każda z tendencji wymienionych w niniejszym dokumencie ma określone implikacje, z którymi boryka się obecnie większość producentów. Zawsze istniała tendencja do skupiania się na procesie montażu/produkcji i pomijania innych krytycznych elementów, które mogą obniżyć całkowity koszt produkcji.
Zautomatyzowane rozwiązania w zakresie obsługi materiałów i magazynowania, stosowane w przypadku materiałów przychodzących, podawania materiałów do produkcji oraz funkcji inwentaryzacji wyrobów gotowych, pozwalają obniżyć całkowity koszt produkcji dzięki zmniejszeniu nakładów pracy i zapasów przy jednoczesnej poprawie dokładności, przepustowości i wykorzystania przestrzeni. Ponadto producenci będą mogli poprawić poziom obsługi klienta dzięki zwiększeniu wydajności i jakości dostaw.
Chodzi o to, aby zorganizować i śledzić przepływ materiałów od momentu przyjęcia i odłożenia surowców do kompletacji i wysyłki wyrobów gotowych. Należy jednak pamiętać, że różne technologie i rozwiązania mogą prowadzić do różnych rezultatów. Ostateczne rozwiązanie powinno być starannie dopasowane do celów strategicznego planu biznesowego producenta.