Das Kommissionier-, Pack- und Versandsystem von Benco Dental
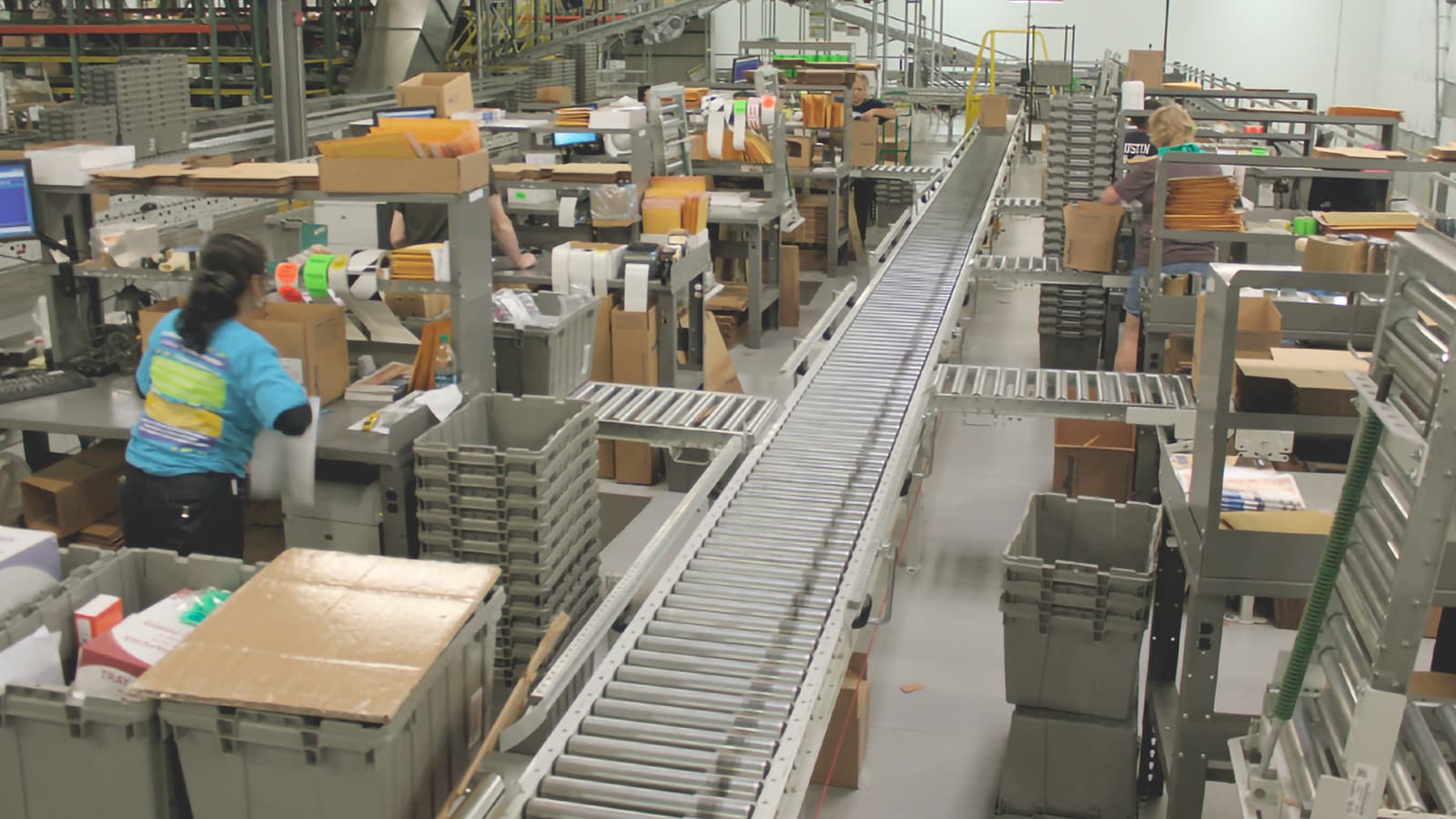
Benco Dental ist ein Full-Service-Händler für zahnmedizinisches Zubehör, Ausrüstung und Möbel. Das Unternehmen bietet ein umfassendes Angebot an Service-, Liefer- und Ausstattungsoptionen, einschließlich Bürodesign, Reparatur von Ausrüstung und Technologielösungen.
In seinem Distributionszentrum in Flower Mound, Texas, kommt ein Förder- und Sortiersystem von Dematic zum Einsatz, um die Kommissionierung von Einzelteilen und Kartons zu erleichtern. Zu den Komponenten des Systems gehören eine Auftragszuführung, ein Netz von Zonenförderern, Packstationen, eine Inline-Waage, ein Versandsortierer und eine Anhängerbeladung.
Die Herausforderungen
Benco Dental verfügt über eine Vertriebsstrategie, die eine reaktionsschnelle und hochpräzise Auftragsabwicklung für über 30.000 Kunden in 50 US-Bundesstaaten ermöglicht. Mit Hilfe eines Netzwerks von fünf Distributionszentren beliefert Benco Dental Zahnarztpraxen und Bildungseinrichtungen und bietet über 80 % der Bevölkerung der Vereinigten Staaten eine Zustellung am selben Tag an.
Die regionalen Distributionszentren beliefern Kunden in einer bestimmten geografischen Region und konzentrieren sich auf das Handling von SKUs mit langsamer, mittlerer und hoher Geschwindigkeit. Mehr als zwei Millionen Pakete werden pro Jahr mit den von Dematic entwickelten und implementierten Auftragsabwicklungssystemen versandt.
In den letzten Jahren wurde das DC von Benco Dental in Grapevine, Texas zu klein. Das Unternehmen musste sein Geschäft skalieren und ausbauen, ohne die Zahl der Mitarbeitenden zu erhöhen. Die Größe und Struktur des DC konnte die Änderungen jedoch nicht verkraften. Benco Dental konsultierte Dematic bezüglich einer neuen Anlage.
Die Lösung
Das Lager ist klimatisiert, um das Inventar zu schützen und den Komfort der Mitarbeitenden zu gewährleisten. Das System ist so konzipiert, dass die Kommissionierung von Einzelteilen und Kartons sowie die Auffüllung gleichzeitig in einer Arbeitsschicht durchgeführt wird. Bei der Stückkommissionierung liegt die typische Auftragsgröße zwischen vier und sechs Artikeln; die Kommissioniergenauigkeit beträgt über 99,95 %. An einem typischen Tag werden in diesem DC etwa 650 bis 1.000 Kundenaufträge kommissioniert, verpackt und versandt.
Es wird eine diskrete Kommissioniermethode verwendet, bei der ein Kunststoffbehälter in Standardgröße (graue Behälter auf den Fotos) als Behälter für alle SKUs dient, die für einen Kundenauftrag erforderlich sind. Während der gesamten Schicht werden die Aufträge vom Warehouse Management System (WMS) auf das Warehouse Control System (WCS) heruntergeladen, das mit der leistungsoptimierenden Software von Dematic arbeitet. Das WCS steuert den Weg jedes Kundenauftragsbehälters durch das gesamte Lager, beginnend mit der Startstation des Auftrags.
Beim Auftragsstart wird ein Barcode auf dem Behälter mit jedem Kundenauftrag verknüpft. Sowohl der Barcode des Behälters als auch der Barcode des Versandmanifests werden nacheinander gescannt. Das WCS übernimmt die Steuerung des Behälters auf dem Netz der Zonenförderer. Jeder Behälter fährt nur Zonen an, in denen Artikel zu kommissionieren sind, wodurch die Transportwege, die Staus und die Zeit, die für die Bearbeitung jedes Auftrags benötigt wird, minimiert werden.
Außerdem greifen die Kommissionierenden in nur einem kleinen Bereich auf den Bestand zu, so dass sie nicht das gesamte Lager durchqueren müssen. Diese Konfiguration reduziert die Fahrtzeit der Kommissionierenden zu jeder Kommissionierstelle. Es gibt 12 Kommissionierzonen, in die Auftragsbehälter geleitet werden können. Ein typischer Auftrag muss möglicherweise nur 3 Zonen ansteuern.
Langsam drehende Waren werden am weitesten von den Kommissionierenden entfernt in den Fließ- und Regalbereichen gelagert. Schneller drehende Waren werden in der Nähe des Fördersystems gelagert.
Sobald alle Artikel für einen Kundenauftrag ausgewählt und in einen Behälter gelegt wurden, wird dieser über das Fördersystem zu den Packstationen transportiert. Dort nimmt ein Mitglied des Lagerpersonals, das an einer der 24 Packstationen arbeitet, die Artikel heraus und führt eine 100%ige Qualitätskontrolle durch, während er oder sie die Artikel in einen Versandkarton verpackt. Der Versandbehälter verlässt das Modul der Packstation und fährt zur Füllmaterial- und Kartonverschließzone.
Von hier aus werden alle Kartons gescannt und über die automatische Inline-Waage befördert, um die Versandkosten zu ermitteln und Qualitätsprüfungen durchzuführen. Schließlich leitet eine Sortieranlage jeden Karton zu einer Versandtür und dann zum Verladen in LKW-Anhänger.
Das Netz von Zonenförderern bietet auch die Möglichkeit der Rückwärtslogistik, um eingegangene Artikel zurück zur Kommissionierstelle zu bringen. Die eingegangenen Artikel werden gescannt und in einen speziellen grünen Behälter gelegt. Der grüne Behälter fährt nur in die Zonen, in denen sich die SKU befindet. Das Bedienpersonal in der Zone legt die SKU vorne in die Kommissionierstelle.
Das Ergebnis
Durch den Einsatz des technischen Auftragsabwicklungssystems konnte die Qualität der Auftragsabwicklung gesteigert werden, während gleichzeitig die betriebliche Effizienz und der Gesamtprozess verbessert wurden. Da jeder Auftrag nur an Zonen geleitet wird, wo eine Kommissionierung erfolgt, verringert sich die Bearbeitungszeit für die Aufträge erheblich.
Das Kommissionierungspersonal bleibt in einem kleinen geografischen Bereich; dies minimiert die Fahrtzeit zu den einzelnen Kommissionierstellen und erhöht so die Produktivität der Mitarbeitenden. Integrierte QC-Verfahren gewährleisten eine Genauigkeit von 99,95 %. Aufträge, die um 17:30 Uhr eingehen, werden am selben Tag versandt.
Automatisierung wie die Inline-Waage reduziert den Arbeitsaufwand und die Zeit für die Auftragsabwicklung. Das Auftragsabwicklungssystem ist für eine Doppelfunktionalität ausgelegt: Kommissionierung und Retourenbearbeitung, da die Zonenförderer die zurückgegebenen Artikel zurück an die Kommissionierstelle im Lager befördern.