Pick Pack and Ship System Brings Smiles to Dental Professionals
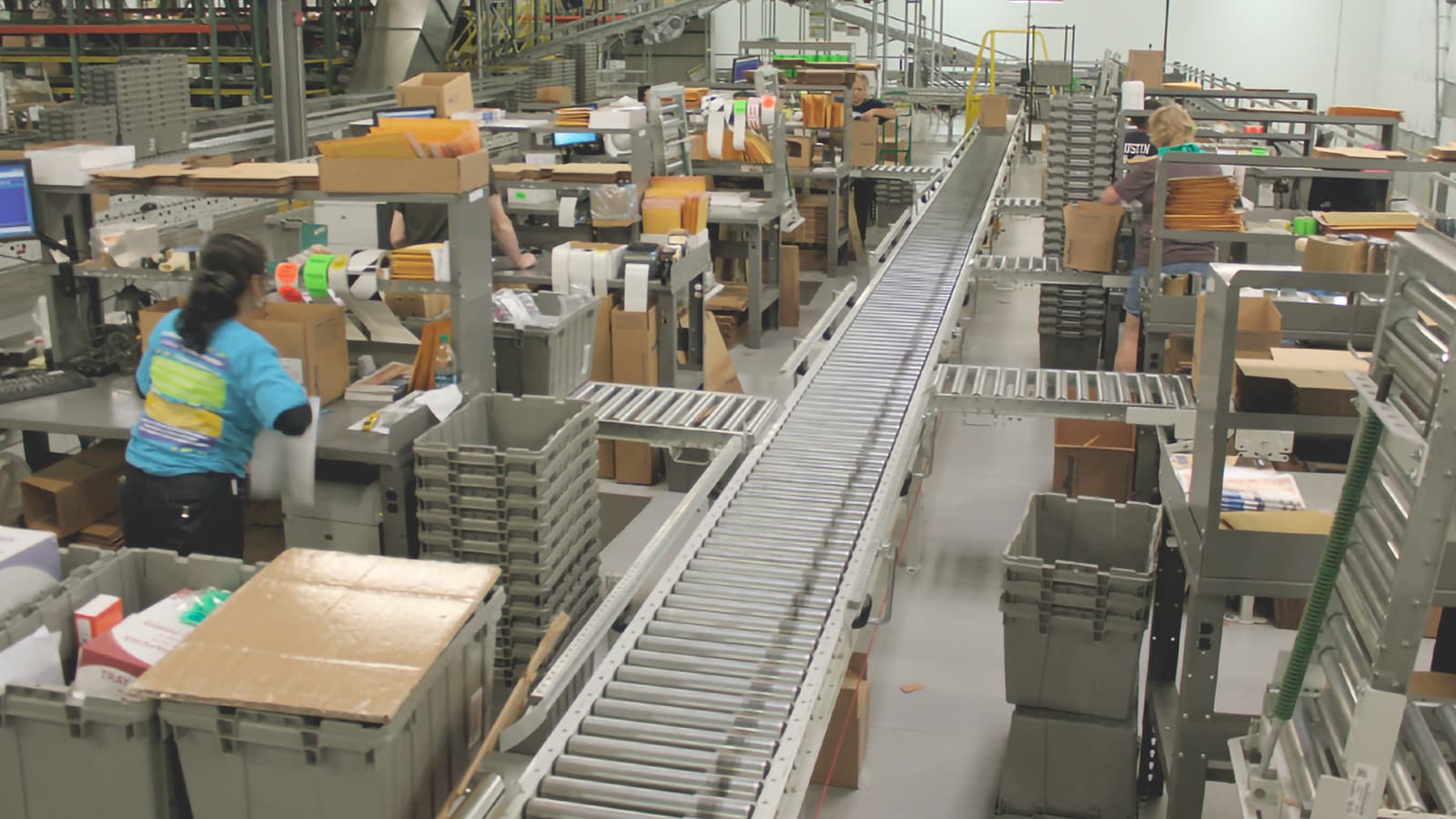
A Benco Dental é uma distribuidora completa de suprimentos, equipamentos e móveis odontológicos. A empresa oferece um conjunto abrangente de opções de serviços, suprimentos e equipamentos, incluindo design de escritório, reparo de equipamentos e soluções de tecnologia.
Seu centro de distribuição em Flower Mound, no Texas, usa um sistema de transporte e classificação da Dematic para facilitar a seleção de peças e caixas. Os componentes do sistema incluem indução de pedidos, rede de transportadores de rota de zona, estações de embalagem, balança de pesagem em linha, classificador de remessas e carregamento de caminhões.
Os desafios
A Benco Dental tem uma estratégia de distribuição que oferece suporte ao processamento de pedidos responsivo e altamente preciso para mais de 30.000 clientes em 50 estados. Usando uma rede de cinco centros de distribuição, a Benco Dental atende a consultórios odontológicos e instituições educacionais, fornecendo envio de um dia para mais de 80% da população dos Estados Unidos.
Os DCs regionais enviam pedidos para clientes de uma região geográfica e se concentram no manuseio de SKUs com velocidade lenta, média e alta. Mais de dois milhões de remessas são enviadas por ano, usando sistemas de atendimento de pedidos projetados e implementados pela Dematic.
Nos últimos anos, a Benco Dental superou seu DC de Grapevine, Texas. Precisava escalonar e expandir seus negócios sem aumentar o número de funcionários. Entretanto, o tamanho e a estrutura deste DC não puderam acomodar as mudanças. A Benco Dental consultou a Dematic a respeito de uma nova instalação.
A solução
O armazém tem temperatura controlada para proteger o estoque e proporcionar conforto ao trabalhador. O sistema é projetado para que a seleção de peças e de caixas, bem como a reposição, sejam realizados simultaneamente em um turno de operação. Para a operação de separação de peças, o tamanho comum do pedido varia de quatro a seis itens de linha; a precisão de separação é superior a 99,95%. Em um dia típico, este DC coletará, embalará e enviará aproximadamente de 650 a 1.000 pedidos de clientes.
Um método de separação de pedidos discreto é usado quando uma caixa de plástico de tamanho padrão (as caixas de cor cinza das fotos) é o recipiente que reunirá todas as SKUs necessárias para compor um pedido do cliente. Durante todo o turno, os pedidos do Sistema de gerenciamento de armazém (WMS) são baixados para o Sistema de controle de armazém (WCS), que é executado por meio do software de otimização de desempenho da Dematic. O WCS gerencia o encaminhamento de cada caixa de pedido do cliente em todo o armazém, começando com a estação de início do pedido.
No início do pedido, um código de barras na caixa é associado com cada pedido do cliente. Tanto o código de barras da caixa quanto o código de barras do manifesto de carga são digitalizados, um após o outro. O WCS assume e controla a caixa na rede de transportadores de rota de zona. Cada caixa se desloca apenas para as zonas com itens a serem retirados, minimizando a distância do percurso, o congestionamento e o tempo necessário para processar cada pedido.
Além disso, os seletores só acessam o estoque em uma pequena área, eliminando a necessidade de percorrer todo o armazém. Essa configuração reduz o tempo de deslocamento do seletor para cada face de seleção. Existem 12 zonas de separação onde as caixas de pedidos podem ser encaminhadas. Um pedido típico pode precisar deslocar apenas para três zonas.
O estoque de movimento lento é colocado mais longe dos seletores nas áreas de fluxo e prateleira. O estoque de movimentação mais rápida é estocado próximo à rede de transportadores.
Uma vez que todos os itens de um pedido do cliente são selecionados e colocados em uma caixa, ela percorre a rede de transportadores até as estações de embalagem. Lá, um funcionário do armazém que trabalha em uma das 24 estações de embalagem remove os itens e fornece uma verificação de 100% de CQ enquanto embala os itens em uma caixa de remessa de papelão. A caixa de remessa sai do módulo da estação de embalagem e percorre até zona de preenchimento de vazios e vedação da caixa.
A partir daqui, todas as caixas são digitalizadas e transportadas pela balança automática em linha para determinar o custo de envio e realizar verificações de qualidade. Finalmente, um classificador desvia cada caixa para uma porta de expedição e, em seguida, carrega em carretas de caminhão.
A rede de transportadores de rota de zona também fornece o método de logística reversa para trazer os itens recebidos de volta ao local de seleção. Os itens recebidos são digitalizados e colocados em uma caixa especial de cor verde. A caixa verde percorre apenas as zonas onde a SKU está localizada. O operador na zona coloca a SKU na frente do local de seleção.
Os resultados
Com o uso do sistema de atendimento de pedidos projetado, o desempenho do “pedido perfeito” aumentou ao mesmo tempo em que alcançou eficiência operacional e melhoria geral do processo. Ao encaminhar cada pedido apenas para as zonas com separação, o tempo de processamento do pedido é reduzido significativamente.
A equipe de separação de pedidos permanece em uma pequena zona geográfica; isso minimiza o tempo de deslocamento para cada lado de separação, aumentando assim a produtividade do trabalhador. Os métodos integrados de CQ garantem 99,95% de precisão. Pedidos aprovados até as 17h30 são enviados no mesmo dia.
A automação, como a balança em linha, reduz os requisitos de mão de obra e o tempo de processamento de pedidos. O sistema de atendimento de pedidos é projetado para dupla funcionalidade: separação de pedidos e processamento de devoluções, uma vez que a rede de transportadores de rota da zona entrega os itens devolvidos de volta ao local de seleção no armazém.