Pick Pack and Ship System Brings Smiles to Dental Professionals
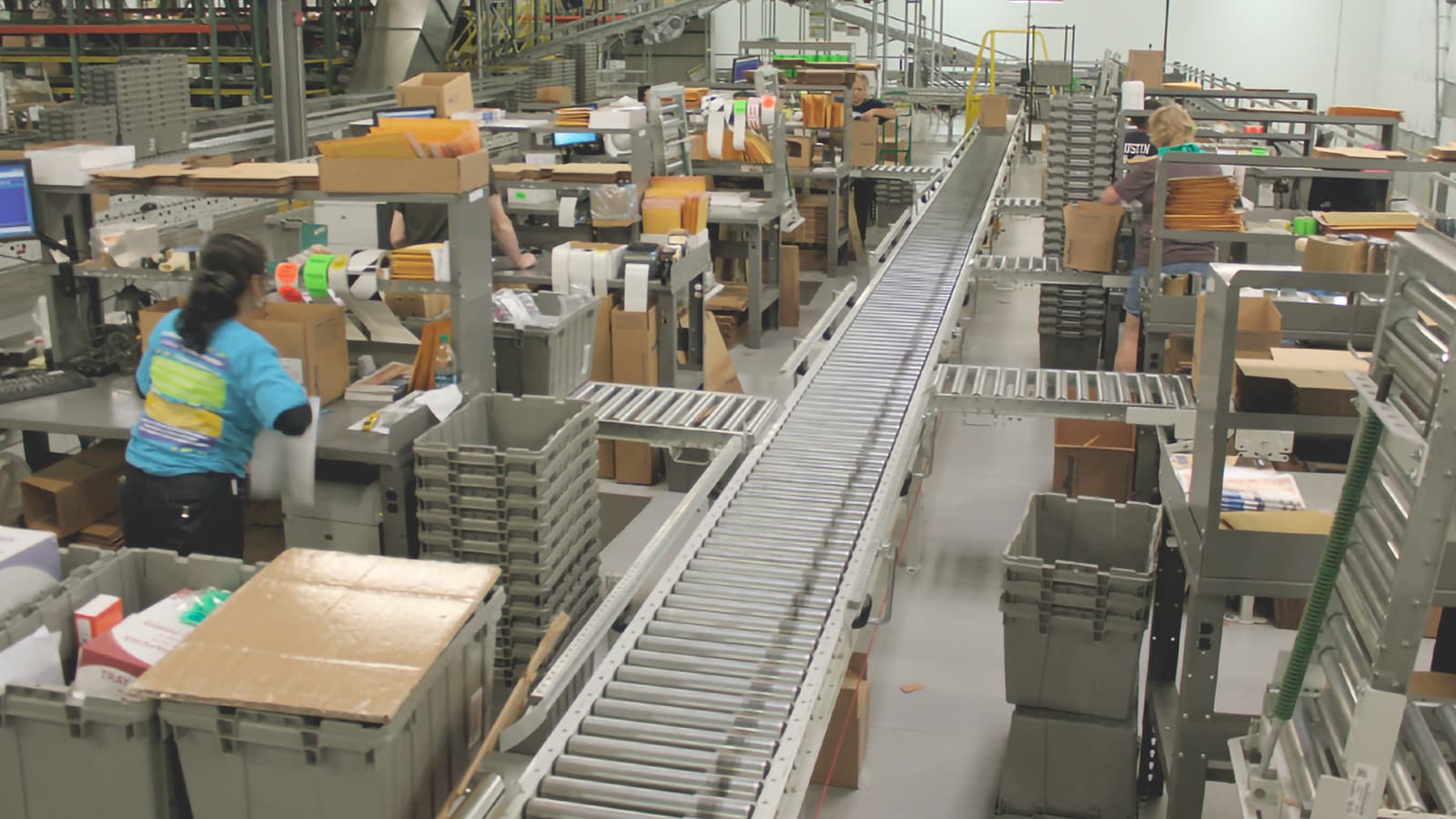
Benco Dental es un distribuidor de servicios integrales para suministros, equipos y mobiliario dentales. La empresa ofrece un conjunto completo de opciones de servicios, suministros y equipos, que incluyen el diseño de oficinas, la reparación de equipos y las soluciones tecnológicas.
Su centro de distribución de Flower Mound, Texas, utiliza un sistema de clasificación y de cintas transportadoras de Dematic para facilitar la preparación de piezas y cajas. Entre los componentes del sistema se encuentran la incorporación de pedidos, la red de cintas transportadoras de ruta por zonas, las estaciones de embalaje, la báscula en línea, el clasificador de envíos y la carga en remolques.
Los desafíos
Benco Dental cuenta con una estrategia de distribución que permite procesar los pedidos de forma rápida y precisa a más de 30 000 clientes en 50 estados. Mediante una red de cinco centros de distribución, Benco Dental ofrece su servicio a los consultorios dentales y a los centros educativos con envíos en un día a más del 80 % de la población de Estados Unidos.
Los centros de distribución regionales envían a los clientes de una región geográfica y se centran en la gestión de las SKU con velocidad lenta, media y alta. Cada año, se envían más de dos millones de paquetes mediante sistemas de preparación de pedidos que Dematic diseña e implementa.
En los últimos años, el centro de distribución de Grapevine, Texas, había quedado pequeño para Benco Dental. Necesitaba expandirse y hacer crecer su negocio sin agregar personal. Sin embargo, el tamaño y la estructura de este centro de distribución no podía adaptarse a los cambios. Benco Dental consultó a Dematic sobre la posibilidad de abrir una nueva instalación.
La solución
El almacén tiene la temperatura controlada para proteger el inventario y brindar comodidad a los trabajadores. El sistema está diseñado de tal manera que la preparación de piezas y cajas, así como el reabastecimiento, se realizan en un solo turno de trabajo y de forma simultánea. Para la preparación de piezas, el tamaño típico de los pedidos oscila entre cuatro y seis partidas de línea; la precisión de la preparación es superior al 99,95 %. En un día normal, este centro de distribución prepara, empaqueta y envía alrededor de 650 a 1 000 pedidos de clientes.
Se utiliza un método de preparación de pedidos a discreción en el que una caja contenedora de plástico de tamaño estándar (en las fotos, cajas contenedoras de color gris) es el contenedor que recoge todas las SKU necesarias para completar el pedido de un cliente. Durante el turno, los pedidos del sistema de gestión de almacenes (WMS) se descargan en el sistema de control de almacenes (WCS), que se ejecuta con el software de optimización del rendimiento de Dematic. El WCS gestiona el enrutamiento de cada caja contenedora de pedidos de clientes en todo el almacén, y que empieza por la estación de inicio de pedidos.
Al iniciar el pedido, se “enlaza” un código de barras en la caja contenedora con cada pedido del cliente. Tanto el código de barras de la caja contenedora como el del manifiesto de envío se escanean, uno tras otro. El WCS se encarga de controlar la caja contenedora en la red de cintas transportadoras de ruta de la zona. Cada caja contenedora solo se desplaza a las zonas en las que hay artículos para recoger, lo que reduce la distancia de desplazamiento, la congestión y el tiempo necesario para procesar cada pedido.
Además, los preparadores solo acceden al inventario en una zona reducida, lo que elimina la necesidad de recorrer todo el almacén. Esta configuración reduce el tiempo de desplazamiento de los preparadores a cada área de carga. Hay 12 áreas de preparación a las que se pueden dirigir las cajas contenedoras de pedidos. Un pedido típico solo tiene que recorrer 3 zonas.
El inventario que tiene menor movimiento se coloca más alejado de los preparadores, en las áreas de flujo y de estanterías. El inventario con mayor movimiento se almacena cerca de la red de cintas transportadoras.
Cuando todos los artículos del pedido de un cliente se seleccionan y se colocan en una caja contenedora, este se desplaza por la red de cintas transportadoras hasta las estaciones de embalaje. Una vez allí, un miembro del personal del almacén que trabaja en una de las 24 estaciones de empaquetado retira los artículos y realiza un control de calidad del 100 % mientras los empaqueta en un contenedor de cartón para el envío. El contenedor para el envío sale del módulo de la estación de empaquetado y se dirige a la zona de llenado de huecos y precintado de cajas.
A partir de aquí, todas las cajas se escanean y pasan por la báscula automática en línea para determinar el coste de envío y realizar los controles de calidad. Para finalizar, un clasificador desvía cada caja a una puerta de envío y luego se carga en los remolques de los camiones.
La red de cintas transportadoras de ruta por zonas también proporciona el método de logística inversa para llevar los artículos recibidos de vuelta al área de carga. Los artículos recibidos se escanean y se colocan en una caja contenedora especial de color verde. La caja contenedora verde solo se desplaza a las zonas en las que se encuentra la SKU. El operador de la zona coloca la SKU en la parte delantera del área de carga.
Los resultados
Como resultado de la utilización del sistema de logística de pedidos, se ha incrementado el rendimiento de los “pedidos perfectos” y también se concreta la eficacia operativa y una mejora general del proceso. Mediante el direccionamiento de cada pedido solo a las zonas de preparación, el tiempo de procesamiento de los pedidos se reduce de forma significativa.
El personal encargado de la preparación de pedidos permanece en una pequeña zona geográfica; esto reduce al mínimo el tiempo de desplazamiento a cada área de carga, lo que aumenta la productividad de los trabajadores. Los métodos de control de calidad integrados garantizan una precisión del 99,95 %. Los pedidos que se reciben antes de las 5:30 p. m. se envían el mismo día.
La automatización, como la báscula en línea, reduce las necesidades de mano de obra y el tiempo de procesamiento de los pedidos. El sistema de logística de pedidos está diseñado para una doble funcionalidad: la logística de pedidos y el procesamiento de devoluciones, ya que la red de cintas transportadoras de ruta por zonas envía los artículos devueltos al área de carga del almacén.