Kitting-System verhilft Hersteller von medizinischen Geräten zur Expansion
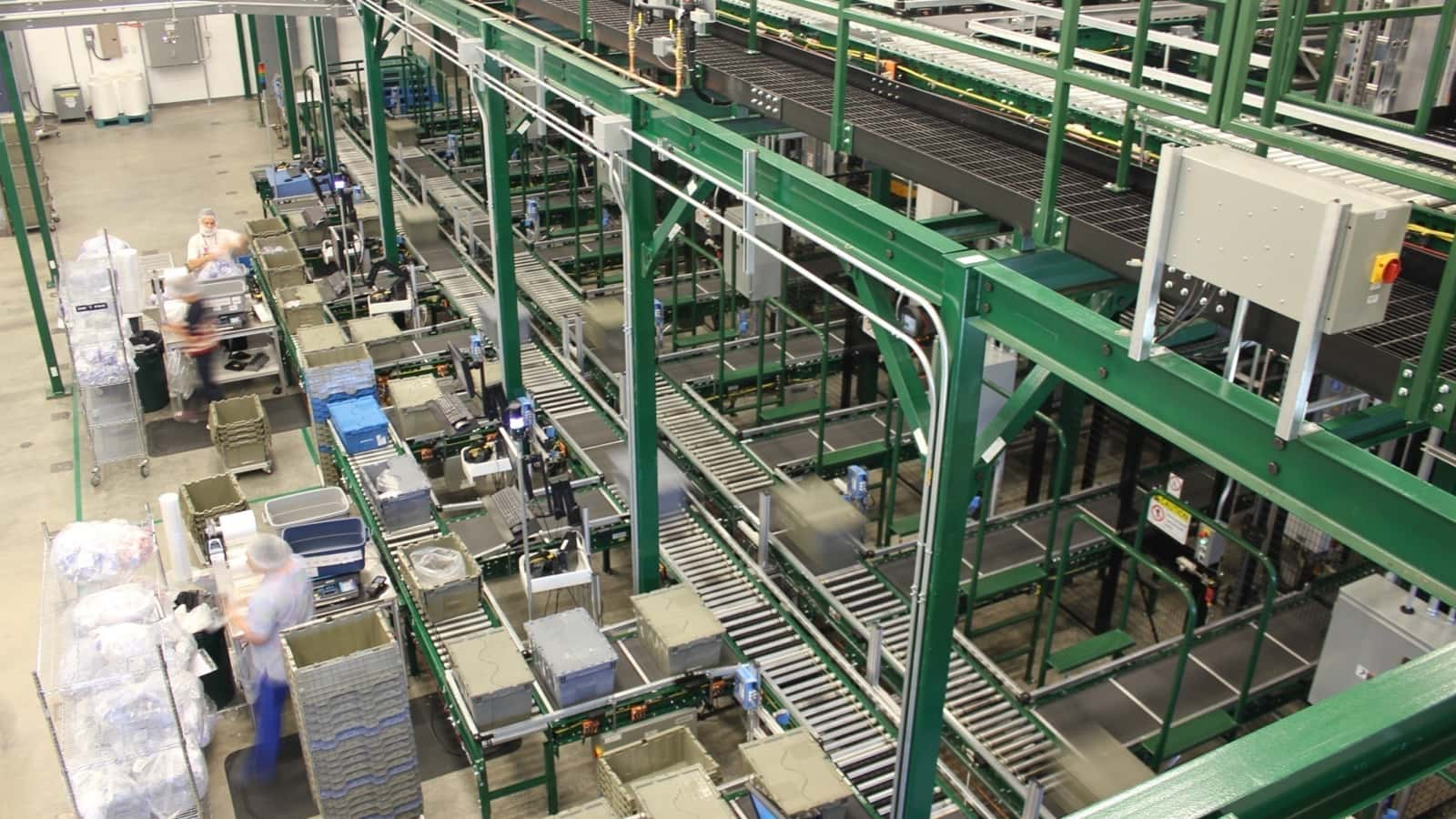
Merit Medical Systems, Inc., ist ein führender Hersteller von medizinischen Geräten, die in der Diagnostik und interventionellen Kardiologie und bei radiologischen Verfahren eingesetzt werden. Erfolgreiche Produkte und steigende Umsätze stellten das Unternehmen an seiner Fertigungsanlage in Utah vor Herausforderungen. Merit hat in Zusammenarbeit mit Dematic eine automatisierte Kitting-Lösung entwickelt, die den speziellen Anforderungen des Unternehmens gerecht wird.
Die Herausforderungen
Als Hersteller von Hightech-Geräten war Merit mit den Vorteilen der Automatisierung bereits wohlvertraut. In seiner Produktionsanlage in Utah werden hoch automatisierte Spritzgießmaschinen eingesetzt, um Komponenten für medizinische Geräte herzustellen.
Allerdings hat die durch die automatisierte Herstellung gesteigerte Effizienz später beim Montageprozess zu Schwierigkeiten geführt.
Die Montage war ineffizient. Das Zusammensuchen der Komponenten nahm viel Zeit in Anspruch, was Probleme bei der Bestandskontrolle zur Folge hatte.
Für Merit war klar, dass der Prozess verbessert werden musste. Zur Steigerung der Produktionsraten benötigte das Unternehmen Hilfe.
Unsere Lösung
Um der Produktivitätssteigerung und zukünftigem Wachstum Rechnung zu tragen, beschloss Merit, seine Anlage durch Errichtung eines neuen Bereichs für die Endmontage neben seinem bestehenden Produktionsgebäude zu erweitern.
Merit hat eine Kitting-Lösung implementiert, die durch ein Multishuttle®-Subsystem von Dematic unterstützt wird. Das Multishuttle maximiert die Flächennutzung und bietet einen kontrollierten Zugang zum Lagerbestand. Dematic hat gemeinsam mit Merit die Pufferprozesse und die Abläufe an den Arbeitsstationen optimiert.
Die Lösung beginnt, wenn hergestellte Produkte in Kunststoff-Lagerbehältern mit einem einbahnigen Hängeförderer vom Produktionsbereich in den Montagebereich transportiert werden.
Die Behälter werden in das Multishuttle-System eingespeist und in sieben Gängen in doppelter Tiefe gelagert. Das Multishuttle-System dient als Puffer für unfertige Produkte und wird von Dematic-Software gesteuert. Die verteilte Steuerungsarchitektur sorgt für einen stetigen Fluss.
Wenn Artikel für die Montage benötigt werden, zieht das Multishuttle Behälter aus dem Lager und platziert sie auf dem Förder-Loop. Der Förderer transportiert die Behälter zu einem rechtwinkligen Transfer und dann zur Arbeitsstation.
An den Arbeitsstationen führen Mitarbeiterinnen und Mitarbeiter das Goods-to-Person-Kitting durch. Mitarbeiterinnen und Mitarbeiter interagieren mit der Benutzeroberfläche der Dematic-Software, um Behälter mit Artikeln anzufordern, aus den Behältern entnommene Artikel zu bestätigen und die Behälter auf dem Förder-Loop zurückzusenden.
Die Kits werden dann auf Wagen in einen Bereich der Anlage gebracht, in dem andere Mitarbeiterinnen und Mitarbeiter die Kits zu Endprodukten montieren. Kommissionierer legen die Behälter mit den restlichen Komponenten zurück auf den Förder-Loop, woraufhin sie zurück zum Multishuttle transportiert werden.
Die Dematic-Software ist ein Warehouse Execution System (WES), das mit dem Warehouse Management System (WMS) von Merit interagiert. Das WMS sendet die Kit-Aufträge zum WES, das WES führt diese aus und bestätigt dem WMS die Fertigstellung
„Merit hat sich für das Dematic-Multishuttle entschieden, das die Flächennutzung maximiert und einen kontrollierten Zugang zum Lagerbestand bietet.“
Das Ergebnis
Mit der automatisierten Goods-to-Person-Kitting-Lösung von Dematic hat Merit seine Prozesse und seine Produktivität erheblich verbessert. Die Durchsatzkapazität wurde erhöht, die Bearbeitungszeit hingegen verringert:
- Verkürzung der für die Kitting-Zusammenstellung benötigte Zeit – von Stunden auf Minuten
- Verringerung des Arbeitsaufwands für den Kommissioniervorgang um 50 %
- Verbesserte Bestandskontrolle und Kitting-Genauigkeit
- Verbesserte Nutzung der Anlagenfläche mit geringer Stellfläche und hoher Lagerdichte
- Höhere Flexibilität mit der Möglichkeit zur Anpassung von Prozessen und Ergänzung von Kapazität für zukünftiges Wachstum
Wichtigste Fakten
Spritzgießbetrieb 24 Stunden/Tag
Produzierte Teile: 41.000/Stunde
Produzierte Behälter: bis zu 375/Stunde
Montierte fertige SKUs: 60/Tag