Neues Asahi Lager erreicht 250% Produktivitätssteigerung mit automatisiertem System
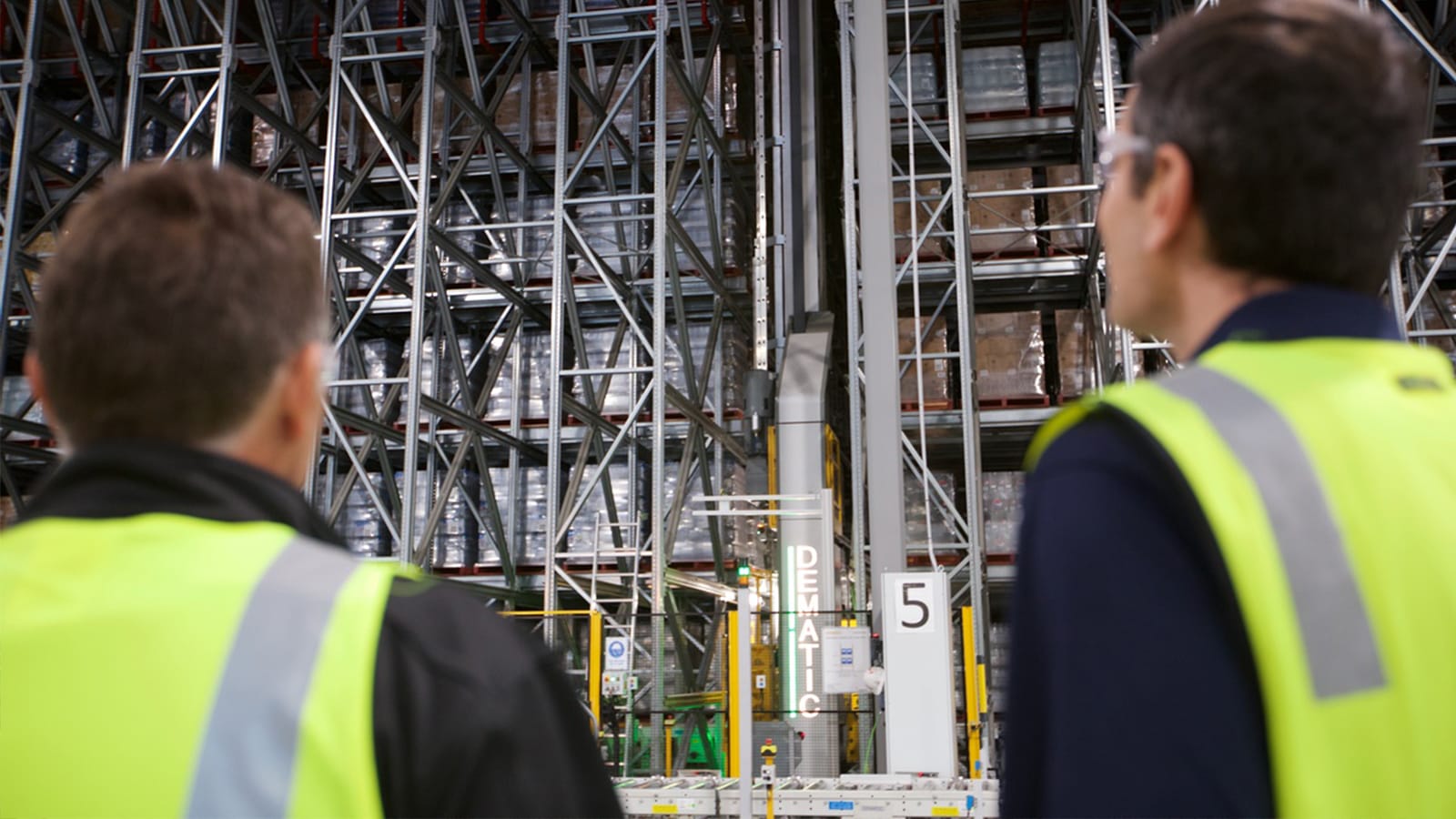
Asahi Beverages ist ein führender Getränkehersteller, der alkoholische und alkoholfreie Produkte in Australien und Neuseeland produziert und vertreibt. Mit einer reichen und abwechslungsreichen Geschichte vermarktet Asahi Qualitätsgetränke und verfügt über ein starkes Portfolio an etablierten Marken und innovativen, neu auf den Markt gebrachten Produkten.
Asahi Beverages gehört zur Asahi Group Holdings, einem der führenden Getränkeunternehmen Japans, und umfasst einige der erfolgreichsten Getränkeunternehmen Australiens und Neuseelands, wie Asahi Lifestyle Beverages (früher bekannt als Schweppes Australia), Asahi Premium Beverages, Independent Liquor und The Better Drinks Co.
Heute beschäftigt Asahi Beverages mehr als 2.100 Mitarbeiter in Australien und Neuseeland.
Umstieg von einem manuellen System
Asahi hat eine Reihe von Distributionszentren in ganz Australien. Früher arbeitete Asahi in Brisbane an mehreren Standorten und setzte manuelle Gabelstapler für die Blockstapelung ein, was mit vielen Nachteilen und Herausforderungen verbunden war.
Asahi hat vor kurzem seine Standorte in Brisbane zu einem Zentrallager zusammengefasst. Mit der Entwicklung des Zentrallagers in Heathwood beschloss Asahi, auf eine automatische Lagerlösung umzusteigen, da das Unternehmen zuvor ein sehr arbeitsintensives System im Einsatz hatte.
"Jeder Lkw, der ankam, musste mit einem Gabelstapler entladen werden, dann mussten wir den Papierkram manuell entgegennehmen, die Paletten manuell prüfen, die Paletten in den Lagerort bringen und dann all das in umgekehrter Reihenfolge tun, um sie zu kommissionieren", so Nathan Lucinsky, Heathwood DC Manager, Asahi.
Mit der Entscheidung, seine Standorte in einem einzigen Distributionszentrum zu konsolidieren und auf eine automatisierte Lösung umzusteigen, wollte Asahi eine Reihe von Vorteilen erzielen, darunter Kostensenkungen, Effizienz- und Produktivitätssteigerungen und die Möglichkeit, die Bedürfnisse seiner Kunden besser erfüllen zu können.
Automatisches Lagersystem
Ein Schlüsselfaktor im Entscheidungsprozess von Asahi bei der Suche nach einer automatischen Lagerlösung, die den Anforderungen des Heathwood DC entspricht, war die Zusammenarbeit mit einem Unternehmen, das den lokalen Markt kennt. Asahi entschied sich für Dematic, da das Unternehmen nachweislich in der Lage ist, ähnliche Projekte in Australien zu realisieren.
"Da es sich bei der neuen Automatisierungslösung um eine Erstimplementierung handelt, war es für Asahi von entscheidender Bedeutung, dass die Lösung richtig ist", so Dominic Figliano, Projektmanager bei Dematic. "Während der anfänglichen Design- und Konzeptentwicklungsphase zog Dematic eine Reihe von Niedrig- und Hochregallager-Alternativen in Betracht, aber nach der Bewertung der Lageranforderungen von Asahi wussten wir, dass die beste Lösung für sie das automatische Lagersystem (ASRS) mit sechsfach tiefer Satellitenlagerung war.
Das Hochregallager von Asahi Heathwood DC ist 13 Etagen hoch und 34 Lagerpätze tief. Das Regalbediengerät erstreckt sich auf sechs Palettenplätze in der Tiefe auf jeder Seite der sechs Krane, auf die mit Satellitenwagen zugegriffen wird. Insgesamt gibt es etwa 31.500 Palettenstellplätze.
"Das automatische Lager, das wir für Asahi gebaut haben, verwendet den neuesten und schnellsten Kran von Dematic, den 1200-1. Dies ist auch das höchste Satellitensystem, das wir in Australien gebaut haben", sagte Dominic.
Die Reise einer Palette beginnt an einem der beiden Produktionsstandorte von Asahi in Queensland. Das Produkt wird dann per LKW zum Heathwood DC transportiert. Wenn der Lkw vor Ort ankommt, fährt der Fahrer rückwärts auf die Schlittschuhrampe und löst dann die automatische Vorrichtung aus, um den Anhänger auszurichten und den Entladevorgang zu starten. Die Schlittschuhe fahren in den hinteren Teil des Anhängers, die Luftkissen lösen aus und heben die Paletten vom Boden des Anhängers.
An diesem Punkt fahren die Schlitten wieder auf die Rampe zurück, die Luftkissen entleeren sich, und Kettenförderer transportieren die Paletten dann auf unsere Hauptförderstrecke im Lager.
Die Paletten durchlaufen dann eine automatische Profilprüfung, bei der sie anhand der Spezifikationsanforderungen des Lagersystems validiert werden. Die Förderschleife liefert die Palette an die Abgabestation, wo das ASRS-System die Arbeit übernimmt.
Das Regalbediengerät hebt die Palette an und fährt sie an den zugewiesenen Einlagerungsort, dann übernimmt ein Supercap-Wagen die Palette und fährt sie in den Satelliten und lagert sie dort ein.
Das automatisiert Lager wird von der Dematic WCS-Software gesteuert. Im Auto-Kontrollraum und auch an den Arbeitsplätzen in der Anlage interagieren die Bediener mit dem WCS-GUI-System und sie haben auch den Vorteil eines SCADA-Systems, mit dem sie den Zustand des Systems in Echtzeit überwachen können.
Neben dem Hochregallager integrierte Dematic auch Fremdanlagen, darunter die Skate-Docks, eine Stretchwickelmaschine, automatische Etikettenapplikatoren und einen Palettenumrichter.
Die Einführung des Systems
Vor dem Bau des Zentrallagers in Heathwood war Dematic an der Auswahl eines neuen Standorts für das neue Zentrallager beteiligt, um sicherzustellen, dass der Standort den Lageranforderungen von Asahi sowie den Anforderungen des von Dematic entwickelten neuen Systems entspricht.
"Als wir mit der Installation des Lagers begannen, befand sich das Rechenzentrum von Asahi noch auf der grünen Wiese, was eine Reihe von Herausforderungen mit sich brachte", so Dominic. "Da das DC noch eine Baustelle war, gab es Bauarbeiter, Elektriker, Betonierer und andere Auftragnehmer und Arbeiter vor Ort, mit denen wir uns abstimmen und zusammenarbeiten mussten. So mussten wir uns beispielsweise eng mit der Installation der Sprinkleranlage abstimmen, um sicherzustellen, dass die Sprinkler in die Regale passen und den Anforderungen entsprechen."
Eine enge Koordinierung und Zeitplanung war ebenfalls von entscheidender Bedeutung, um die verschiedenen Geräte, die von den verschiedenen Arbeitern eingesetzt wurden, so zu koordinieren, dass die Projektfristen eingehalten werden konnten. Dematic hatte zwei Teams vor Ort, die bis zu zwei 80-Tonnen-Kräne, vier Ausleger- und zwei Scherenhebebühnen einsetzten.
"Wir hatten bis zu 50 Leute vor Ort und haben einen Teil der Installation in der Nacht durchgeführt, um den Zeitplan einzuhalten und das Projekt pünktlich abzuschließen.
Ein weiterer wichtiger Aspekt der Systemeinführung war die Schulung, die Dematic für das Asahi-Team nach Abschluss der Installation durchführte.
"Wir boten Asahi eine Superuser-Schulung an, bei der wir in kleinen Gruppen sowohl theoretische als auch praktische Schulungen zur Nutzung des neuen Systems durchführten. Diese Superuser konnten dann in Zukunft andere Mitarbeiter von Asahi schulen", so Dominic.
Da das Heathwood DC über Hochregallager verfügt, wurde ein zusätzlicher Schwerpunkt auf die Sicherheit bei Arbeiten in der Höhe gelegt.
Der Rollout des neuen Systems wurde im Mai 2019 erfolgreich abgeschlossen.
Vorteile des neuen Systems
Die herausragenden Vorteile des Dematic-Systems sind die hohe Lagerdichte und die geringere Stellfläche, die das Regalbediengerät einnimmt, wodurch Asahi seinen gesamten Betrieb an einem einzigen Standort konsolidieren kann. Dies führt zu Kosteneinsparungen durch geringere Mietkosten, weniger Komplexität bei der Kundenbetreuung, weniger Palettenumlagerungen, die zu Beschädigungen und Fehlern führen können, geringere Transportkosten und schnellere Umschlagzeiten der LKWs.
"Ein automatisiertes System wie dieses macht einen Großteil der manuellen Handhabung von Paletten überflüssig", so Dominic. "Das schafft nicht nur Effizienz und eine hohe Produktivitätssteigerung von 250 % für den Kunden, sondern erhöht auch die Sicherheit für die Mitarbeiter, da nicht so viele Gabelstapler benötigt werden."
In einem Distributionszentrum wie dem von Asahi in Heathwood stellt jede manuelle Berührung einer Palette einen Kostenfaktor für das Unternehmen dar und birgt das Risiko menschlicher Fehler.
Seitdem Asahi seine Lagerprozesse automatisiert hat und manuelle Prozesse nur noch dort einsetzt, wo es sinnvoll ist, werden die meisten Paletten nicht mehr von einem Menschen berührt, bis sie zum Kunden-DC gelangen.
"Wenn man bedenkt, wie viele Berührungen es in einem Lagerprozess gibt, ist jede Berührung ein Kostenfaktor für das Unternehmen", sagt David Rubie, Industry Manager F&B Manufacturing, Dematic. "Diesen Prozess zu automatisieren und manuelle Arbeit nur dann einzusetzen, wenn es sinnvoll ist, ist eine wirklich gute Möglichkeit, ein Logistikunternehmen zu führen."
"Als wir die Anlage für Asahi entwarfen und die erwartete Auslastung betrachteten, berechnete Dematic, dass wir eine Gesamtauslastung von etwa 89 % anstreben sollten", fügte David hinzu. "Wir freuen uns, dass Asahi dies mit einer Auslastung von 90 bis 92 % in der gesamten Anlage nun übertrifft."
Für die Zukunft gerüstet
Dematic hat Asahi kontinuierlich mit Servicetechnikern vor Ort unterstützt, um den Erfolg des automatisierten Lagers im Heathwood Distributionszentrum zu gewährleisten.
"Die ortsansässigen Dematic-Techniker waren entscheidend für den Erfolg und den reibungslosen Ablauf an unserem Standort", so Nathan. "Die Beziehung, die sie zu unseren Asahi-Schichtteams haben, ist fantastisch. Ihre Kommunikation und ihr Bemühen, unsere betrieblichen Zwänge zu verstehen, waren erstklassig."
Die Unterstützung durch Dematic während des gesamten Projekts hat Asahi geholfen, ihr eigenes Wissen über die Funktionsweise der Automatisierung, insbesondere von Lagern, zu erweitern. Dies hat es ihnen ermöglicht, das Beste aus ihrer neuen Lösung herauszuholen und sicherzustellen, dass das Heathwood DC weiterhin so effizient wie möglich läuft.
"Eines der Dinge, die mich an Systemen wie Regalbediengeräten begeistern, ist, dass es für unsere Mitarbeiter im Lager sicher ist", fügt Nathan hinzu. "Mit dem automatisierten System laufen unsere Lagerabläufe wie am Schnürchen, und es besteht keine Notwendigkeit mehr für so viele Arbeiter, die manuelle Tätigkeiten ausführen."
"Die Einführung des automatisierten Lagers hat uns für die Zukunft gerüstet. Und ich bin wirklich stolz auf das, was wir hier gemeinsam mit Dematic erreicht haben."