Automatyzacja ostatniej prostej w produkcji
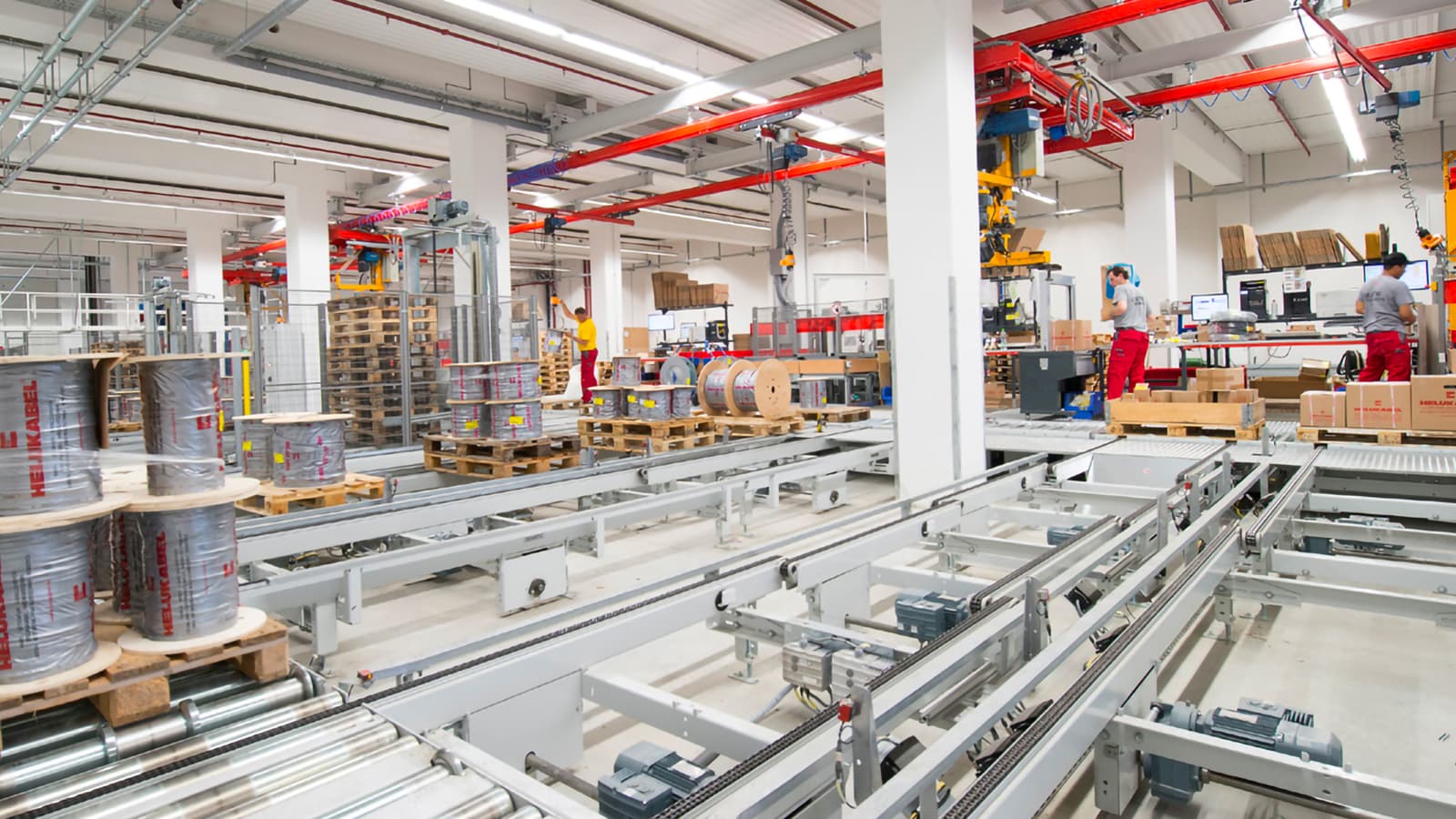
Automatyzacja z pewnością nie jest obca branży produkcyjnej. Wprowadzenie linii montażowej przez Henry'ego Forda zmieniło oblicze przemysłu motoryzacyjnego. Od tego czasu tempo wdrażania wzrastało — początkowo automatyzacja obejmowała proste, powtarzalne zadania, a następnie coraz bardziej złożone wyzwania. Obecnie w niemal każdym zakładzie produkcyjnym znajduje się fascynująca gama zautomatyzowanych maszyn, które tworzą i pakują niemal wszystko, czego używamy, dotykamy lub konsumujemy w naszym codziennym życiu.
Większość procesów automatyzacji w zakładach produkcyjnych koncentruje się na wytwarzaniu i pakowaniu produktów. Przykłady technologii automatyzacji obejmują robotykę, która maluje, spawa, obrabia i montuje produkty, oraz automatykę twardą do napełniania, etykietowania i pakowania towarów konsumpcyjnych, takich jak żywność i napoje.
Najnowsze trendy pokazują, że firmy przenoszą produkcję bliżej swoich klientów, aby kontrolować jakość, poprawić obsługę klienta lub zmniejszyć koszty transportu. Niektóre wykorzystują reshoring (cofnięcie biznesu z powrotem do kraju, w którym go rozpoczęto). Inne trendy związane z konsolidacją, fuzjami i przejęciami powodują niemal ciągłe zmiany w sposobie dystrybucji produktów od producenta do konsumenta. W międzyczasie popyt na pracę zmniejsza się wraz ze wzrostem gospodarczym i kurczeniem się puli dostępnych pracowników.
Automatyzacja jest oczywistym rozwiązaniem; pytanie brzmi: gdzie i jak?
Gdzie szukać automatyzacji ostatniej prostej?
W miarę jak łańcuchy dostaw stają się coraz bardziej złożone, niektórzy szukają rozwiązań w „Internecie rzeczy”. Wynika z tego, że procesy wewnętrzne będą wymagały większej łączności, z wykorzystaniem inteligentnych urządzeń i procesów w celu poprawy efektywności. Zsynchronizowane przepływy pracy i analityka predykcyjna stają się niezbędne nie tylko w planowaniu produkcji, ale także w konserwacji. Przepływ informacji i Big Data (duże ilości danych) są niezbędne do stworzenia podstaw przyszłej automatyzacji.
Oprogramowanie to początek ostatniej prostej automatyzacji, ale czego jeszcze potrzeba, aby dodatkowo usprawnić działanie? Jakie obszary funkcjonalne należy wziąć pod uwagę?
Materiał przychodzący
Zapewnienie dobrej kondycji łańcuchów dostaw w górę wymaga ogromnego wysiłku i planowania. Muszą zapewniać nie tylko terminowe dostawy, ale – co równie ważne – materiały wysokiej jakości. Zakłócenia w łańcuchach dostaw towarów przychodzących mogą szybko doprowadzić do wstrzymania działalności.
Nawet jeśli Twój łańcuch dostaw jest w dobrej kondycji, czy myślisz o tym, jak zarządzać materiałami po ich dotarciu na miejsce? Oto kilka pytań, nad którymi warto się zastanowić:
- Czy moje materiały są sprawnie obsługiwane po dotarciu na miejsce?
- Czy dysponuję odpowiednim procesem sprawdzania jakości i dokładności materiałów i produktów?
- Czy dobrze kontroluję stan zapasów surowców w magazynie?
- Czy wydajnie przechowuję materiały, wykorzystując oprogramowanie do zarządzania przestrzenią, obrotami i siłą roboczą?
- Jak można zautomatyzować przyjmowanie i przechowywanie surowców?
Zarządzanie przepływem materiałów do i przez produkcję
Po uporządkowaniu strony przychodzącej magazynu kolejnym obszarem, który należy uwzględnić w celu usprawnienia, jest przepływ materiałów do produkcji. Poniższe pytania pozwalają określić, czy materiał jest efektywnie przekazywany do produkcji.
- Czy pracownicy czekają, aż materiały dotrą do ich stanowisk pracy?
- Czy do gniazd produkcyjnych trafia właściwy materiał?
- Czy w gniazdach produkcyjnych znajduje się zbyt dużo zapasów?
- Czy materiał w gniazdach produkcyjnych jest prawidłowy dla bieżącego harmonogramu produkcji?
- Czy mogę tworzyć zestawy bardziej efektywnie, korzystając z automatyzacji?
Przepływ materiałów musi być dokładny, terminowy, a w wielu przypadkach dynamiczny. Nieprecyzyjne materiały, niewłaściwe materiały, zagracone miejsca pracy ze zbyt dużą ilością materiałów właściwych dla danego zadania — wszystkie te czynniki spowalniają produkcję.
Przemieszczanie materiałów w toku (work-in-process, WIP) z gniazda produkcyjnego do komórki roboczej może również wpływać na produkcję. Gdy operacje w zakładzie produkcyjnym nie są zsynchronizowane, materiał może przepływać nierównomiernie przez cały proces. Niewystarczająca ilość materiału spowalnia produkcję, natomiast zbyt duża ilość materiału WIP powoduje nagromadzenie, tworząc zatory. Lepsze planowanie i bufory WIP mogą poprawić przepływ materiałów.
Przemieszczanie wyrobów gotowych na końcu procesu może również doprowadzić do jego zatoru. Do pytań, które warto rozważyć, należą:
- Czy mam wystarczająco dużo miejsca w doku, aby obsłużyć moje wyroby gotowe?
- Jak szybko można obsłużyć przyczepę w doku?
- Czy mam zamknięty obieg między produkcją a dystrybucją — magazyn firmy/DC (centrum dystrybucji) lub 3PL (logistyka firm trzecich)?
- Czy należy inwentaryzować wyroby gotowe w zakładzie produkcyjnym? Ile? W jakim tempie?
Szybkość produkcji i wielkość produktu końcowego lub WIP mają wpływ na podejście do automatyzacji. Na przykład, produkcja setek małych urządzeń elektronicznych w ciągu godziny z pewnością będzie wymagała innego zestawu rozwiązań niż produkcja tuzina ładowarek czołowych dziennie
Potencjalne rozwiązania dla automatyzacji ostatniej prostej
Wracając do wcześniejszego wątku dotyczącego oprogramowania jako podstawy działalności: zaawansowane rozwiązania ERP, MES, a czasem WMS/WES mogą pomóc w usprawnieniu operacji — nie tylko z punktu widzenia przepływu materiałów, ale także zarządzania pracą. Kilka rozwiązań mechatronicznych może usprawnić działanie i pomóc w rozwiązaniu problemów związanych z brakiem siły roboczej. Należy pamiętać, że aby zapewnić pełne zrozumienie przepływu materiałów i danych w bieżącej działalności, konieczna jest dokładna i szczegółowa analiza danych. Pozwala na ocenę i zastosowanie odpowiedniej technologii.
Zarządzanie przepływem materiałów do i przez produkcję
Wcześniejsze zawiadomienia o odbiorze pomagają w planowaniu i przechowywaniu przychodzących materiałów. Prawidłowe planowanie składowania na poziomie palet, skrzyń, pojemników lub segmentów pojemników pozwala zaoszczędzić miejsce w magazynie. Kontrola przychodzących materiałów i rozdzielanie ich na jednostki miary o odpowiedniej wielkości również pozwala zmniejszyć zajmowaną przestrzeń. Elementy o nietypowych kształtach mogą wymagać składowania na specjalnych regałach lub w specjalnych stojakach; jednak palety, skrzynie i pojemniki mogą być przechowywane w zautomatyzowanych systemach magazynowania i pobierania. Systemy mogą być różne:
- Składowanie głębokie lub system pojedynczego składowania głębokiego palet
- Skrzynie i pojemniki w systemach transportu wahadłowego dla przewoźników szybkobieżnych
- Systemy typu mini-load dla średnich przewoźników
- Regały karuzelowe lub nawet półki dla wolniejszych przewoźników
Kompletowanie zestawów
W operacjach kompletowania zazwyczaj wykorzystuje się różne zestawienia materiałów w celu zgromadzenia określonych części do procesów montażu podrzędnego lub końcowego. Czasami zestawy są dostarczane jako zamówienia na części zamienne do konserwacji. Jednak poza sporadycznym zapotrzebowaniem na funkcje „wartości dodanej”, kompletowanie nie różni się zbytnio od realizacji zamówień w centrum dystrybucji. W związku z tym, można zastosować automatyzację, wykorzystując stacje Pick-to-Light, Pick-to-Voice, Goods-to-Person oraz wyznaczanie stref za pomocą przenośników i sortowania. Ta sama technologia przechowywania pojedynczych jednostek magazynowych może również służyć do przechowywania gotowych zestawów przeznaczonych do produkcji lub bezpośrednio do użytkownika końcowego.
Przepływ materiałów do i przez produkcję
Szybkość i wielkość materiału wpływającego do produkcji i przechodzącego przez nią decyduje o wyborze najlepszej technologii automatyzacji wspomagającej kompletowanie:
- Automatycznie sterowane pojazdy (AGV) najlepiej sprawdzają się w przypadku palet i przenoszenia większych elementów. Przepływ może być bardzo dynamiczny, a pojazdy AGV otrzymują zlecenia i zadania w oparciu o swoją lokalizację i najbardziej efektywną trasę przejazdu.
- Zautomatyzowane wózki holownicze ciągnące wózek lub zestaw wózków są najbardziej efektywne przy wykonywaniu kursów z wieloma miejscami rozładunku, gdy przemieszczanie odbywa się z punktu do punktu w środowisku produkcyjnym.
- Automatycznie sterowane wózki (AGC) mogą transportować materiały w ramach systemu Kanban i dostaw do linii produkcyjnych w przypadku mniejszych elementów, takich jak pojemniki i skrzynki.
- Efektywnymi strategiami przemieszczania materiałów mogą być również przenośniki podwieszane i kolejki jednoszynowe. Jednak te rozwiązania nie zapewniają takiej elastyczności i skalowalności jak bardziej mobilne opcje.
- Technologia systemu Pick-to-Light może zwiększyć szybkość i dokładność kompletacji części lub zestawów przy linii produkcyjnej.
Bufory WIP (produkcja w toku)
Palety, tuby, pojemniki i tace z materiałem mogą być przechowywane w buforach przy użyciu technologii automatycznego magazynowania i pobierania (AS/RS). Wiele operacji wykorzystuje systemy typu mini-load do przechowywania i równomiernego rozprowadzania materiałów do gniazd produkcyjnych i różnych procesów. Technologia ta może być umieszczona bezpośrednio między dwoma operacjami lub centralnie, aby obsługiwać wiele operacji WIP.
Obsługa i przechowywanie wyrobów gotowych
Dla końcowych odcinków linii produkcyjnych dostępnych jest kilka rozwiązań.
- Do transportu palet z wyrobami gotowymi można wykorzystać pojazdy AGV (samojezdne), przenośniki paletowe i kolejki jednoszynowe. Każda technologia oferuje korzyści wynikające z szybkości, długości transportu i funkcji. Pojazdy AGV doskonale sprawdzają się przy długich trasach, blokowym układaniu palet w stosy, a nawet mogą być wykorzystywane do załadunku przyczep. Przenośniki doskonale sprawdzają się w przypadku krótszych odcinków, łącząc się z innymi systemami automatyzacji, takimi jak ASRS i gromadzenie palet w doku. Kolejki jednoszynowe najlepiej sprawdzają się w przypadku zastosowań wymagających większych prędkości i długich serii transportowych.
- System AS/RS dla zapasów wyrobów gotowych – w sąsiedztwie produkcji lub w odległym centrum dystrybucji – może zarządzać odbiorem i wysyłką, a także zapewniać dokładną, bezpieczną i wolną od uszkodzeń obsługę produktów. Technologia AS/RS może również wspomagać uzupełnianie zapasów w przypadku ręcznego lub automatycznego pakowania. Dodatkowe korzyści to lepsze wykorzystanie przestrzeni i oszczędność energii.
- W systemach zamkniętej pętli, w których naczepy stale przemieszczają się z produkcji do centrum dystrybucji, zautomatyzowany załadunek i rozładunek naczep może zmniejszyć liczbę doków i ograniczyć liczbę pracowników potrzebnych do ich obsługi. W niektórych przypadkach załadunek i rozładunek naczep mogą trwać zaledwie pięć minut.
Automatyzacja ostatniej prostej może wymagać kreatywnego zastosowania istniejącej technologii lub dostosowania sprzętu i oprogramowania. Jeśli jednak automatyzacja zostanie wdrożona prawidłowo, może znacznie usprawnić działalność produkcyjną.