Automatizzare l'ultimo miglio nella produzione
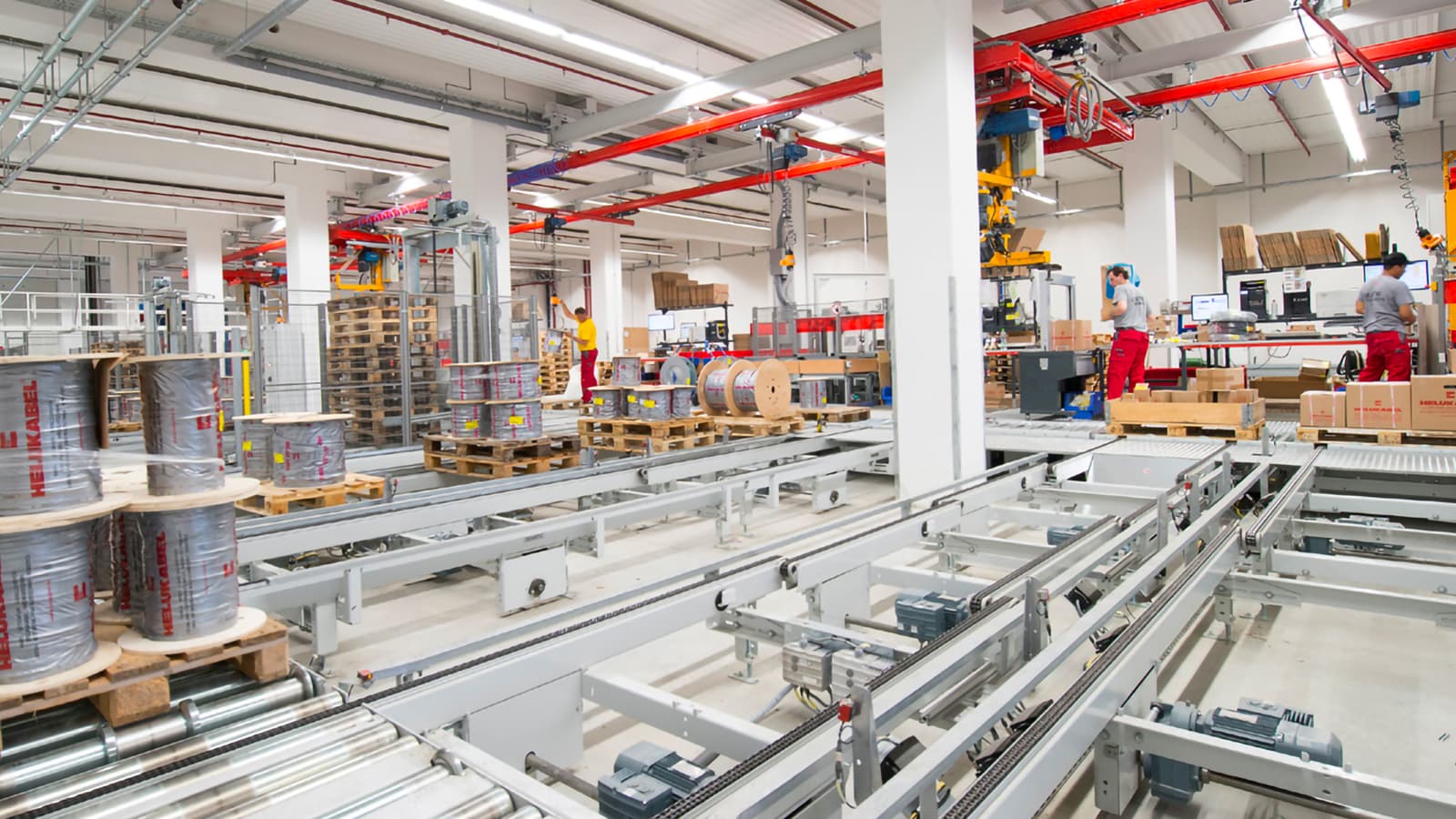
L'automazione non è certo estranea al settore manifatturiero. L'adozione della catena di montaggio da parte di Henry Ford ha trasformato l'industria automobilistica. Da allora il ritmo di accettazione è cresciuto e l'automazione si è inizialmente occupata di compiti semplici e ripetitivi, per poi espandersi verso sfide più complesse. Oggi, quasi tutti gli impianti di produzione contengono un'affascinante combinazione di macchinari automatizzati che creano e confezionano quasi tutto ciò che usiamo, tocchiamo o consumiamo nella nostra vita quotidiana.
La maggior parte dell'automazione negli impianti di produzione si concentra sulla produzione e sul confezionamento dei prodotti. Esempi di tecnologie di automazione sono la robotica che vernicia, salda, lavora e assembla i prodotti, e l'automazione rigida per riempire, etichettare e confezionare beni di consumo come alimenti e bevande.
Le tendenze recenti mostrano che le aziende stanno spostando la produzione più vicino ai loro clienti, per controllare la qualità, migliorare il servizio clienti o ridurre i costi di trasporto. Alcuni stanno effettuando il reshoring (riportare la produzione dentro i nostri confini). Altre tendenze di consolidamento, fusione e acquisizione stanno creando un cambiamento quasi costante nel modo in cui i prodotti vengono distribuiti del produttore al consumatore. Nel frattempo, la domanda di manodopera si fa più intensa, perché l'economia cresce e il bacino di lavoratori disponibili si riduce.
L'automazione è una risposta ovvia, ma la domanda è: dove e come?
Dove cercare l'ultimo miglio dell'automazione?
Con la crescente complessità delle catene di fornitura, alcuni hanno cercato soluzioni nel cosiddetto "Internet of Things" (IoT - Internet delle Cose). Ne consegue che i processi interni richiederanno una maggiore connettività, utilizzando dispositivi e processi intelligenti per migliorare l'efficienza. I flussi di lavoro sincronizzati e l'analisi predittiva diventano necessari non solo per la pianificazione della produzione, ma anche per la manutenzione. Il flusso di informazioni e i Big Data sono necessari per creare le basi dell'automazione futura.
Il software è il punto di partenza dell'ultimo miglio dell'automazione, ma cos'altro è necessario per migliorare ulteriormente un'operazione? Quali sono le aree funzionali da considerare?
Materiali in entrata
Per assicurarsi che le catene di fornitura a monte siano sane sono necessari grandi sforzi e lavori di pianificazione. Esse devono garantire non solo consegne puntuali, ma soprattutto materiali di qualità. Le interruzioni delle catene di fornitura in entrata possono rapidamente mettere in crisi un'attività.
Anche se la tua catena di fornitura in entrata è in buone condizioni, hai pensato a come gestire il materiale una volta arrivato? Ecco alcuni esempi da considerare:
- I miei materiali vengono gestiti tempestivamente al loro arrivo?
- Ho un buon processo per controllare la qualità e la precisione dei materiali e dei prodotti?
- Ho un buon controllo delle scorte disponibili di materie prime?
- Sto stoccando il materiale in modo efficiente, utilizzando un software per gestire lo spazio, i turni e la manodopera?
- Come posso automatizzare il ricevimento e lo stoccaggio delle materie prime?
Gestire il flusso di materiali da e verso la produzione
Dopo aver messo in ordine il lato in entrata del magazzino, l'area successiva da migliorare è la movimentazione dei materiali verso la produzione. Le seguenti domande possono determinare se è presente un flusso efficace dei materiali verso la produzione.
- I miei lavoratori aspettano che i materiali arrivino nelle loro celle di lavoro?
- Le celle di lavoro ricevono i materiali corretti?
- Ci sono troppe scorte nelle celle di lavoro?
- I materiali presenti nelle celle di lavoro sono corretti per il programma di produzione corrente?
- È possibile creare kit in modo più efficace utilizzando l'automazione?
Il flusso di materiali deve essere preciso, puntuale e in molti casi dinamico. I materiali imprecisi, i materiali sbagliati o gli spazi di lavoro ingombri con troppi materiali giusti adatti all'attività in corso possono rallentare la produzione.
Anche lo spostamento di materiali in lavorazione (WIP) da una cella di lavoro all'altra può influire sulla produzione. Quando le operazioni all'interno di un impianto di produzione non sono sincronizzate, i materiali possono fluire in modo non uniforme lungo il processo. L'insufficienza di materiale rallenta la produzione, mentre l'eccesso di materiale WIP causa un accumulo di materiale e crea una situazione di stallo. Una migliore pianificazione e dei buffer WIP possono migliorare il flusso dei materiali.
Infine, la movimentazione dei prodotti finiti alla fine del processo può creare un imbuto operativo. Ecco alcuni domande da porsi:
- Ho abbastanza spazio in piattaforma per gestire i miei prodotti finiti?
- Quanto velocemente posso girare un rimorchio in piattaforma?
- Esiste un circuito chiuso tra la produzione e la distribuzione - un magazzino/DC di proprietà dell'azienda o un 3PL?
- Devo mettere in inventario i prodotti finiti nel sito di produzione? Quanti? A che ritmo?
La velocità di produzione e le dimensioni del prodotto finito o in corso di lavorazione influenzeranno l'approccio all'automazione. Ad esempio, la produzione di centinaia di piccoli dispositivi elettronici ogni ora comporterà sicuramente una serie di soluzioni diverse rispetto alla produzione di una dozzina di caricatori front-end al giorno.
Potenziali soluzioni per l'ultimo miglio dell'automazione
Tornando al tema precedente del software come fondamento delle operazioni: un ERP avanzato, soluzioni MES e talvolta WMS/WES possono contribuire a rendere più fluide le operazioni, non solo dal punto di vista del flusso dei materiali ma anche della gestione della manodopera. Diverse soluzioni meccatroniche possono migliorare il funzionamento e aiutare a risolvere i problemi di carenza di manodopera. Ricorda che sarà necessaria un'analisi accurata e approfondita dei dati per garantire una comprensione completa del flusso di materiali e dati dell'operazione corrente. Questo ti permetterà di valutare e applicare la tecnologia adeguata.
Gestire il flusso di materiali da e verso la produzione
Gli avvisi di ricevimento anticipato aiutano a pianificare e stoccare il materiale in arrivo. Se si pianifica lo stoccaggio a livello di pallet, casse, cassette o cassette segmentate, si può risparmiare spazio in magazzino se si implementa correttamente. Anche l'ispezione dei materiali in entrata e il travaso dei materiali in unità di misura adeguatamente dimensionate consentono di risparmiare spazio. Gli articoli di forma insolita possono dover essere stoccati in scaffalature o attrezzature speciali; tuttavia, pallet, casse e cassette possono essere stoccati in sistemi di stoccaggio e raccolta automatizzati. Questi sistemi possono variare:
- Stoccaggio a corsia profonda o a profondità singola per pallet
- Casse e contenitori in sistemi di navette per articoli ad alta movimentazione
- Sistemi di minicarico per articoli con richiesta media
- Supporti girevoli o anche scaffali per gli articoli meno richiesti
Operazioni di kitting
Le operazioni di kitting utilizzano solitamente varie distinte base per raccogliere pezzi specifici per i processi di assemblaggio secondario o finale. A volte i kit vengono spediti come ordini di pezzi di ricambio per la manutenzione. Ma a parte la necessità occasionale di alcune funzioni "a valore aggiunto", il kitting non è molto diverso dalla gestione degli ordini in un centro di distribuzione. Di conseguenza, l'automazione può essere applicata utilizzando le stazioni Pick-to-Light, Pick-to-Voice, Goods-to-Person e l'instradamento a zone tramite trasportatori e smistamento. La stessa tecnologia per lo stoccaggio di singoli articoli SKU può anche archiviare kit finiti destinati alla produzione o direttamente all'utente finale.
Flusso dei materiali da e verso la produzione
La velocità e le dimensioni dei materiali che fluiscono verso e attraverso la fase di produzione determinano la migliore tecnologia di automazione per supportare il kitting:
- I veicoli a guida automatica (AGV) sono ideali per la movimentazione di pallet e articoli di grandi dimensioni. Il flusso può essere molto dinamico con gli AGV, in quanto ricevono ordini di lavoro e incarichi in base alla loro posizione e al percorso di viaggio più efficiente.
- I rimorchiatori automatici che trainano un carrello o un treno di carrelli sono più efficaci nel completare i percorsi programmati ("milk run") quando il movimento è da un punto all'altro di un ambiente di produzione.
- I carrelli a guida automatica (AGC) possono spostare i materiali per le operazioni Kanban e le consegne in linea per gli articoli più piccoli, come cassette e casse.
- Anche i trasportatori aerei e le monorotaie possono essere strategie efficaci per la movimentazione dei materiali. Tuttavia, queste soluzioni non garantiscono la flessibilità o la scalabilità delle opzioni più mobili.
- La tecnologia Pick-to-Light può migliorare la velocità e la precisione del prelievo in linea di pezzi o kit.
Buffer WIP
Pallet, casse, contenitori e vassoi di materiale possono essere stoccati nei buffer utilizzando la tecnologia di stoccaggio e raccolta automatici (AS/RS). Molte operazioni si servono di sistemi di minicarico per contenere e distribuire uniformemente il materiale alle celle di lavoro e ai vari processi. Questa tecnologia può essere collocata direttamente tra due operazioni o in posizione centrale per servire più operazioni WIP.
Movimentazione e stoccaggio dei prodotti finiti
Sono disponibili diverse soluzioni per le linee di fine produzione.
- Per il trasporto di pallet di prodotti finiti possono essere utilizzati AGV, trasportatori di pallet e monorotaie. Ogni tecnologia offre vantaggi in base alla velocità, alla durata del trasporto e alla funzione. Gli AGV sono ottimi per le lunghe percorrenze, per l'impilamento in blocco dei pallet e possono essere utilizzati anche per il carico dei rimorchi. I trasportatori sono ottimi per le corse più brevi e si collegano ad altre automazioni come l'ASRS e l'accumulo di pallet in piattaforma. La monorotaia funziona meglio per le applicazioni a velocità elevata e per le lunghe tratte di trasporto.
- Un AS/RS per l'inventario dei prodotti finiti, adiacente alla produzione o in un centro di distribuzione remoto, può gestire la ricezione e la spedizione e fornire una gestione precisa, sicura e senza danni dei prodotti. La tecnologia AS/RS può anche supportare il rifornimento per la raccolta manuale o automatico delle casse. Tra gli ulteriori vantaggi ci sono un migliore utilizzo dello spazio e il risparmio energetico.
- Per i sistemi a ciclo chiuso in cui i rimorchi si spostano costantemente dalla produzione a un centro di distribuzione, il carico e lo scarico automatizzato dei rimorchi può ridurre il numero di piattaforme e la manodopera per sostenerle. In alcuni casi, i rimorchi possono essere caricati o scaricati in soli cinque minuti.
L'automazione dell'ultimo miglio può richiedere applicazioni creative della tecnologia esistente o una certa personalizzazione di apparecchiature e software. Tuttavia, se implementata correttamente, l'automazione può migliorare notevolmente le operazioni di produzione.