Automatización del último tramo en la producción
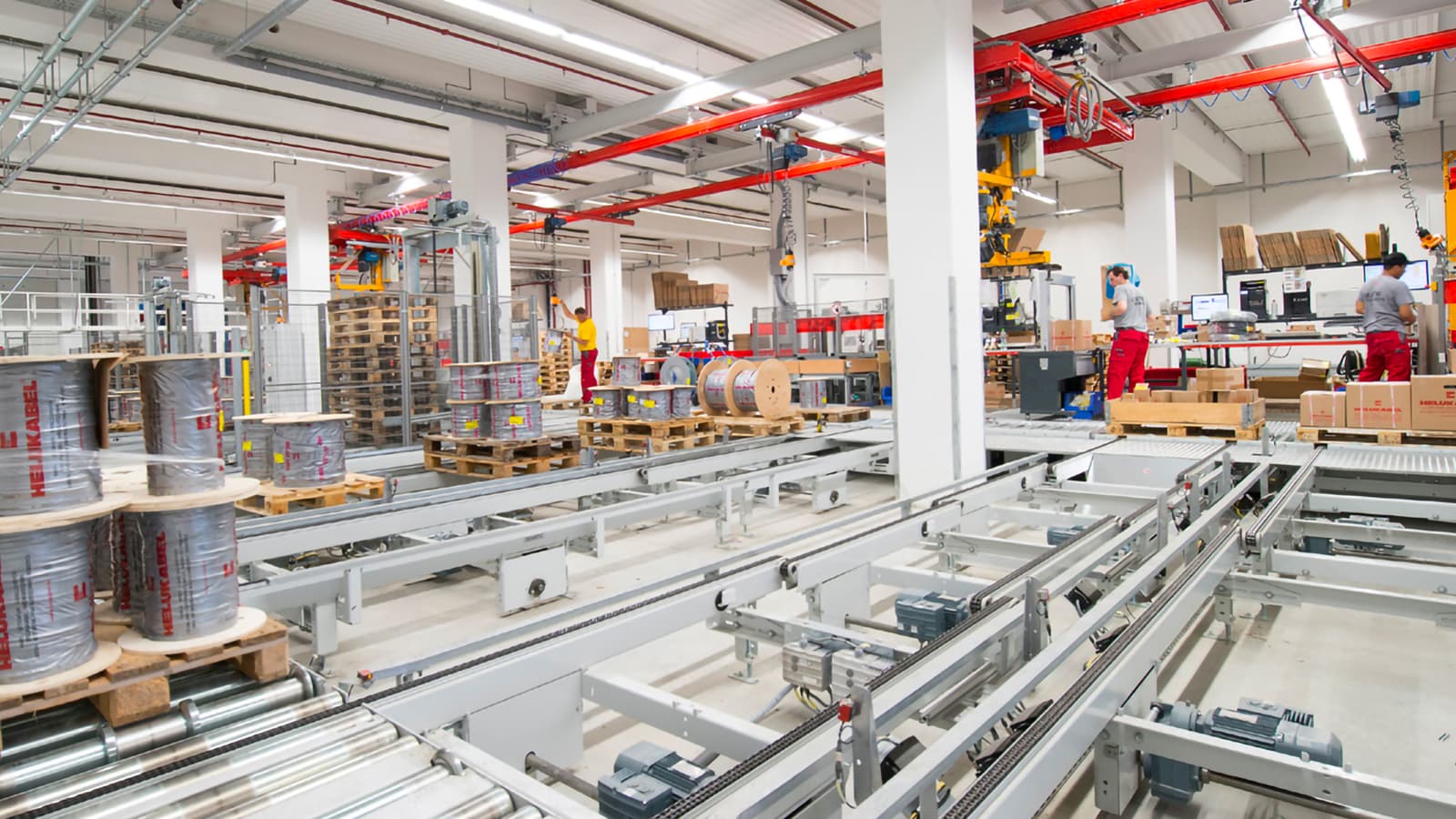
Sin dudas, la automatización no es nueva en la fabricación. La implementación de la línea de montaje por parte de Ford transformó la industria automotriz. Desde entonces, el ritmo de aceptación solo ha aumentado, con la automatización inicialmente participando en tareas simples y repetitivas y luego ampliándose a desafíos más complejos. Hoy en día, casi todos los centros de fabricación contienen una fascinante combinación de maquinaria automatizada que crea y envasa casi todo lo que usamos, tocamos o consumimos en nuestra vida cotidiana.
La mayor parte de la automatización en centros de producción se concentra en la fabricación y el envasado de los productos. Entre los ejemplos de tecnología de automatización se incluyen la robótica, que pinta, suelda, produce y ensambla productos, y la automatización dura, para rellenar, etiquetar y envasar bienes de consumo, como alimentos y bebidas.
Las tendencias recientes muestran que las empresas están acercando la fabricación a sus clientes, ya sea para controlar la calidad, mejorar el servicio de atención al cliente o reducir los costes de transporte. Algunas se están relocalizando (retorno del proceso de fabricación desde países extranjeros). Otras tendencias en consolidaciones, fusiones y adquisiciones están creando un cambio casi continuo en la forma en que los productos se distribuyen desde la fabricación hasta el consumidor. Mientras tanto, la demanda de mano de obra se ajusta a medida que la economía crece y la fuente de trabajadores disponibles se encoge.
La automatización es una respuesta obvia, pero la pregunta es: ¿dónde y cómo?
Dónde buscar el último tramo de automatización
A medida que las cadenas de suministro se vuelven más complejas, hay quienes se han vuelto hacia el «Internet de las cosas» para buscar soluciones. Como resultado, los procesos internos requerirían de más conectividad y del uso de dispositivos y procesos inteligentes para mejorar la eficiencia. Se hacen necesarios los flujos de trabajo sincronizados y la analítica predictiva, no solo para la producción, sino también para el mantenimiento. El flujo de información y los macrodatos son necesarios para sentar las bases de la automatización futura.
El software es el comienzo del último tramo de la automatización, pero ¿qué más se necesita para mejorar aún más una operación? ¿Qué áreas funcionales se deben considerar?
Material entrante
Se necesitan mucho esfuerzo y planificación para garantizar que las cadenas de suministro ascendentes estén en buen estado. No solo es necesario que proporcionen entregas a tiempo, sino también, en el mismo nivel de importancia, materiales de calidad. Las interrupciones en las cadenas de suministro entrantes pueden paralizar rápidamente una operación.
Incluso si su cadena de suministro entrante está en buenas condiciones, ¿ha pensado en cómo gestiona el material una vez que llega? Aquí hay algunas preguntas para considerar:
- ¿Mis materiales se gestionan apropiadamente una vez que llegan?
- ¿Cuento con un buen proceso para comprobar la calidad y precisión de los materiales y productos?
- ¿Tengo buen control de mi inventario físico de materia prima?
- ¿Estoy almacenando el material de manera eficiente y utilizando software para gestionar el espacio, los turnos y la mano de obra?
- ¿Cómo puedo automatizar la recepción y el almacenamiento de materia prima?
Gestión del flujo del material hacia la producción y a través de ella
Después de que el sector de entrantes del depósito esté en orden, la próxima área a tener en cuenta para mejorar es el movimiento del material hacia la producción. Las siguientes preguntas pueden determinar si el material está fluyendo de manera eficiente hacia la producción.
- ¿Mis trabajadores esperan que el material llegue a sus puestos de trabajo?
- ¿Los puestos de trabajo están recibiendo el material correcto?
- ¿Hay demasiado inventario en los puestos de trabajo?
- ¿El material que hay en el puesto de trabajo es el correcto para el programa de producción actual?
- ¿Puedo crear lotes de forma más efectiva utilizando la automatización?
El flujo de material debe ser preciso, puntual y, en muchos casos, dinámico. El material impreciso, el material erróneo, los espacios de trabajo abarrotados con demasiada cantidad del material correcto para el trabajo actual ralentizan la producción.
Trasladar el material del trabajo en proceso (WIP) de una estación de trabajo a otra también puede afectar la producción. Cuando las operaciones dentro de un centro de producción no están sincronizadas, el material puede fluir de forma irregular a lo largo del proceso. Una cantidad insuficiente de material ralentiza la producción, mientras que una cantidad excesiva de material del trabajo en proceso genera acumulación y atascos. Una mejor planificación y el almacenamiento intermedio del trabajo en proceso pueden perfeccionar el flujo de material.
Por último, el movimiento de productos terminados al final del proceso puede generar un embotellamiento en la operación. Algunas preguntas que hay que considerar son las siguientes:
- ¿Tengo suficiente espacio de muelle para manipular mis productos terminados?
- ¿Con qué rapidez puedo rotar un remolque en un muelle?
- ¿Tengo un circuito cerrado entre la fabricación y la distribución, ya sea un depósito/centro de distribución (CD) propiedad de la empresa o proveedores de servicios de logística contratados (3PL)?
- ¿Debería hacer un inventario de los productos terminados en el centro de fabricación? ¿En qué medida? ¿A qué ritmo?
La velocidad de la producción y el tamaño del producto terminado o trabajo en proceso influirán en su enfoque de automatización. Por ejemplo, producir cientos de dispositivos electrónicos pequeños por hora sin dudas implicará un conjunto de soluciones distintas a las necesarias para producir una docena de excavadoras de carga frontal por día.
Posibles soluciones para el último tramo de automatización
Retrocedamos a un tema anterior del software como base de una operación: las soluciones avanzadas de planificación de recursos empresariales (ERP), el sistema de ejecución de la fabricación (MES) y, en ocasiones, el sistema de gestión de depósitos (WMS) o el sistema de ejecución del depósito (WES) pueden ayudar a que las operaciones se ejecuten de forma más regular, no solo desde una perspectiva del flujo del material, sino también desde el punto de vista de la gestión de la mano de obra. Varias soluciones mecatrónicas pueden mejorar la operación y ayudar a resolver problemas de escasez de mano de obra. Hay que tener en cuenta que será necesario un análisis de datos preciso y exhaustivo para garantizar una comprensión plena del flujo de datos y el material de la operación en curso. Esto permite evaluar y aplicar la tecnología adecuada.
Gestión del flujo del material hacia la producción y a través de ella
Los avisos de recepción anticipados ayudan a planificar y almacenar el material entrante. La planificación del almacenamiento en un palé, un recipiente, una caja contenedora o un nivel de caja contenedora segmentada puede ahorrar espacio en su depósito si se implementa adecuadamente. La inspección del material entrante y el decantamiento del material en unidades de medida de un tamaño apropiado también ahorran espacio. Los artículos que tengan formas inusuales quizás deban almacenarse en estantes o muebles amurados especiales; sin embargo, los palés, los recipientes y las cajas contenedoras se pueden almacenar en sistemas automatizados de almacenamiento y recuperación. Estos sistemas pueden variar:
- Almacenamiento en pasillos de profundidad múltiple o de profundidad simple para palés
- Recipientes y cajas contenedoras en sistemas de lanzaderas para productos que se mueven a alta velocidad
- Sistemas de minicarga para productos que se mueven a velocidad media
- Cintas transportadoras o incluso estanterías para productos que se mueven a baja velocidad
Operaciones de preparación de lotes
Las operaciones de preparación de lotes por lo general utilizan varias listas de materiales para reunir partes específicas para los procesos de submontaje y montaje final. A veces, los lotes se envían como pedidos de partes de reemplazo y mantenimiento, pero además de la necesidad ocasional de algunas funciones de «valor agregado», la preparación de lotes no difiere mucho del procesamiento de pedidos en un centro de distribución. Por lo tanto, la automatización se puede aplicar utilizando estaciones de preparación por indicadores luminosos (Pick-to-Light), preparación por indicadores de voz (Pick-to-Voice) y mercancías a persona (Goods-to-Person), y el sistema de rutas por zona con el uso de cintas transportadoras y clasificación. La misma tecnología que se utiliza para almacenar artículos de unidades de mantenimiento de existencias (SKU) individuales también puede almacenar lotes terminados que se dirijan a producción o directamente al usuario final.
Material que fluye hacia la producción y a través de ella
La velocidad y el tamaño del material que fluye hacia la producción y a través de ella determinan la mejor tecnología de automatización para apoyar la preparación de lotes.
- Los vehículos de guiado automático (AGV) funcionan mejor para los palés y la manipulación de artículos más grandes. El flujo puede ser muy dinámico cuando a los AGV se les dan órdenes y tareas de trabajo según su ubicación y la ruta más eficiente de movimiento.
- Los remolcadores automatizados que acarrean un carro o un tren de carros son más eficientes para completar «viajes de rutina» cuando el movimiento es de un punto a otro en un entorno de producción.
- Los carros de guiado automático (AGC) pueden trasladar materiales para operaciones de Kanban y alinear las descargas laterales para artículos más pequeños, como cajas contenedoras y recipientes.
- El transporte aéreo y los monorrieles también pueden ser estrategias efectivas para el traslado del material. Sin embargo, estas soluciones no proveen la flexibilidad o escalabilidad que ofrecen las opciones más móviles.
- La tecnología Pick-to-Light puede mejorar la velocidad y precisión de la separación de partes o lotes en líneas laterales.
Almacenamiento intermedio del trabajo en proceso (WIP)
Los palés, las cubetas, las cajas contenedoras y las bandejas de material se pueden depositar en almacenamientos intermedios utilizando tecnología automatizada de almacenamiento y recuperación (AS/RS). Muchas operaciones utilizan sistemas de minicarga para sujetar el material y distribuirlo en partes iguales hacia las estaciones de trabajo y los distintos procesos. Esta tecnología se puede ubicar directamente entre dos operaciones o en un punto central para atender varias operaciones del trabajo en proceso.
Manipulación y almacenamiento de productos terminados
Hay varias soluciones disponibles para el final de las líneas de producción.
- Se pueden utilizar AGV, cintas transportadoras de palés y monorrieles para el transporte de palés de productos terminados. Cada tecnología ofrece ventajas según el ritmo, la longitud del transporte y la función. Los AGV son estupendos para recorridos largos y el apilado de palés en bloques, e incluso se pueden utilizar para la carga de remolques. Las cintas transportadoras son excelentes para recorridos más cortos, para la vinculación con otros procesos de automatización como los ASRS y la acumulación de palés en el muelle. Los monorrieles funcionan mejor para aplicaciones de mayor rapidez y recorridos largos de transporte.
- Un AS/RS para el inventario de productos terminados (ya sea adyacente a la fabricación o en un CD remoto) puede gestionar la recepción y el envío, y proveer una manipulación del producto precisa, segura y sin daños. La tecnología de AS/RS también puede apoyar el reabastecimiento de la separación manual o automatizada de recipientes. Otros beneficios incluyen un mejor uso del espacio y el ahorro energético.
- En los sistemas de circuito cerrado donde los remolques se trasladan de forma constante desde la fabricación hasta el CD, la carga y descarga automáticas del remolque pueden reducir la cantidad de muelles y mano de obra para otorgar apoyo a los muelles. En algunos casos, los remolques se pueden cargar o descargar tan solo en cinco minutos.
La automatización del último tramo puede requerir aplicaciones creativas de la tecnología existente o la personalización del equipo y el software. Sin embargo, si se implementa correctamente, la automatización puede mejorar mucho una operación de fabricación.