Werner Electric Implements Multi-Channel Order Fulfillment
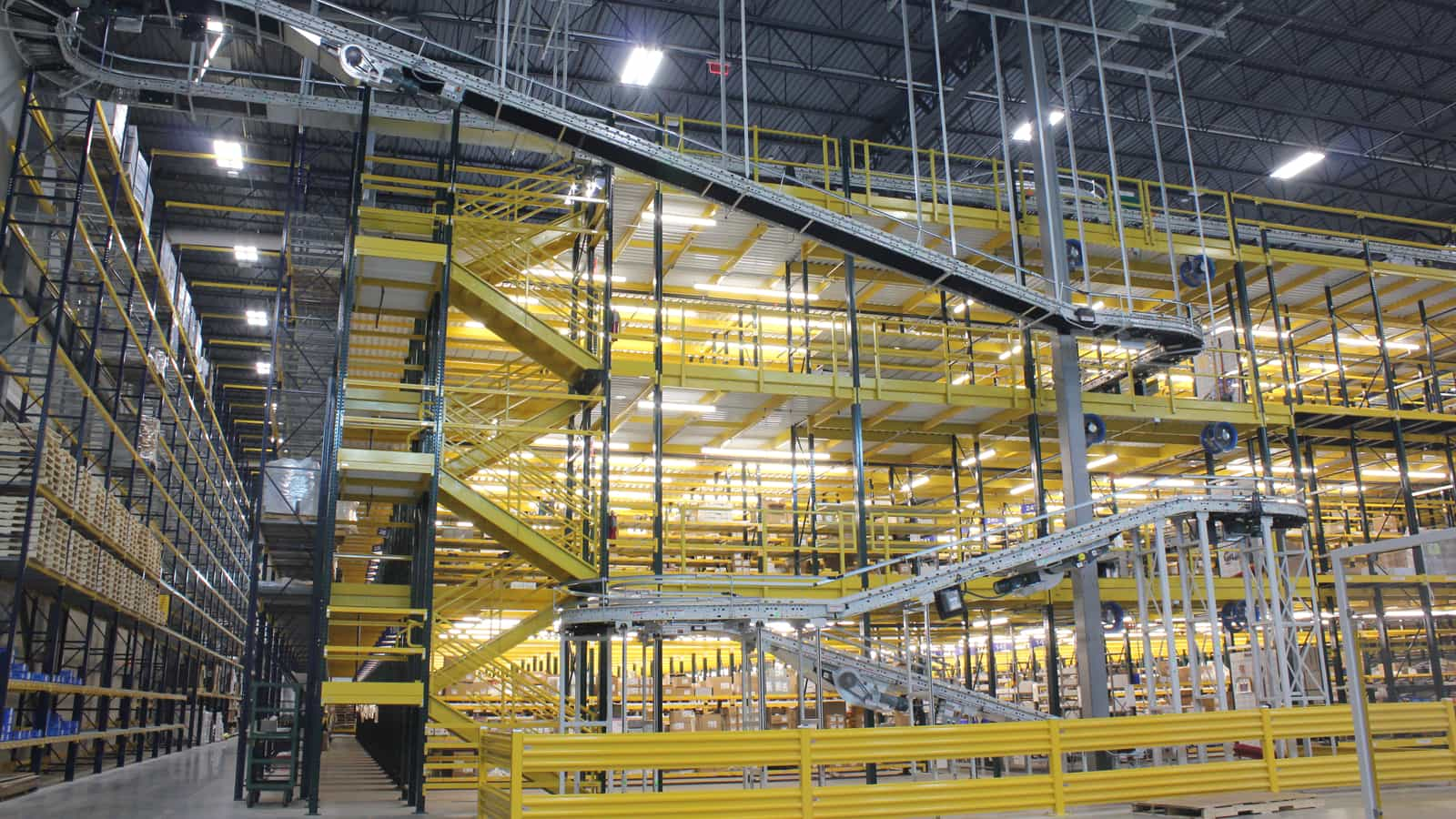
Werner Electric Supply is a wholesale distributor of electrical components, equipment, and parts serving the needs of electrical contractors and users of electrical equipment.
Werner Electric has a network of retail stores located in Wisconsin, Minnesota, North Dakota, and Michigan. Customers can also purchase products using the online store at wernerelectric.com.
The product categories offered include: industrial automation, safety products, pneumatics, motors, lighting, wire, cable, enclosures, datacom, and security.
The challenges
The requirements for increased order volume capacity drove the need for a new distribution center. Furthermore, the company needed the ability to process the increasing volume of e-commerce orders while replenishing their network of retail stores from the same distribution center. Werner Electric also needed a system configuration that could accommodate SKU growth; the company offers 25,000 stock keeping units and anticipates the need for more capacity in the future.
Our solution
Werner Electric implemented an automated, multichannel distribution center that can fill thousands of orders each day. In addition, the new DC is scalable and can accommodate surges in demand as well as future growth.
After customers place an order with Werner Electric, it is picked, packed, and shipped with speed and accuracy using modern technology and methods.
Inventory received from suppliers is scanned and placed into totes. The put-away process is optimized by a smart conveyor network that allows automatic transport to strategic locations in the warehouse.
The item velocity, size, and weight determine the appropriate location for storage. Inbound inventory is scanned during the re-stocking process to direct put-away and support accuracy.
The outbound order fulfillment process is an “order container to pick zone” system, also known as a zone route system. Warehouse Execution Software (WES) directs the order containers strategically through the piece picking module, packing, and shipping.
Orders download to the WES, which controls and directs the processes to pick pack and ship each item. Barcode labels are printed for each order and applied to shipping cartons. These labels act as license plates and are linked to orders.
Next, shipping cartons enter onto the conveyor network. The staff does not need to roam the warehouse looking for the items in each order. Instead, the cartons automatically convey to zones where there are items for the orders.
Scan validation at multiple points directs cartons to appropriate picking zones, ensuring accuracy and real-time tracking.
When a carton arrives in a picking zone, order fulfilment specialists receive picking instructions via hand-held RF devices. After making picks for that zone, the specialists move the carton back onto the smart conveyor. (Cartons only travel to zones where there are picks.)
Next, cartons travel to the packing area. Each carton is scanned and weighed “on-the-fly” to confirm order accuracy. Packing, document-insert, void fill, and seal occurs here.
At shipping, cartons are scanned prior to sorting. Steerable wheel sorters divert the cartons to the appropriate shipping door. The sort point depends on the address and the shipping method requested.
After cartons are automatically sorted, staff sorts to a pallet or container staged on the floor based on customer address or delivery route. If an order includes bulk items, it is selected, picked, and delivered to shipping.
The results
It’s a better way to pick, pack, and ship. Orders are assembled in less time, with precise accuracy, using real time software, and a smart conveyor system.
The order fulfilment system provides operational insight during every step of the process. Furthermore, the system supports high productivity and worker ergonomics & safety, all in a controlledaccess environment.
The order fulfilment system is scalable and can accommodate surges in demand as well as future growth.
Dematic Zone Route Pick at Werner Electric
System solution at a glance
- Convey & sort order fulfillment system
- Put-away 1st shift; picking 2nd shift
- Zone route for put-away & piece picking
- Packing workstations, in-line scale, shipping sorter
- Sort control (515 logical destinations)
- WES interface to WMS
- 4,000 – 4,500 lines/day (3,000 in pick module)
- 3.5 lines per order, 1,000 – 1,200 orders/day
- Reduced fulfillment cost per order t Compact footprint, capacity for growth
- Ship to 11 branches, 5 delivery routes/branch (20 – 35 stops/route)