More Capacity in Less Space
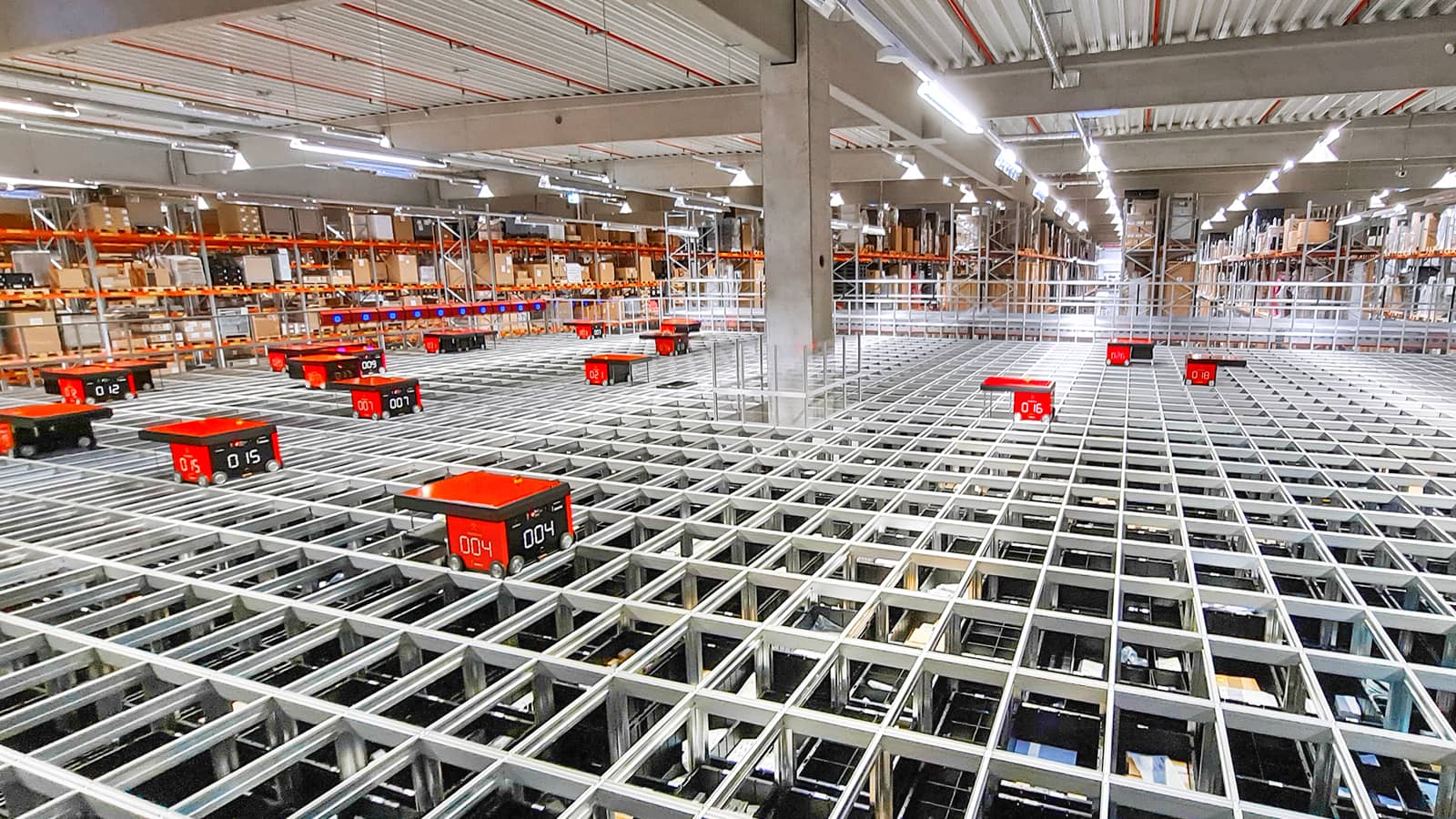
Development, engineering, production, testing, and pre-commissioning — the Siemens plant for Combination Technology in Chemnitz, Germany (Siemens WKC) is a leader in switchgear construction for machine tools and production machines in Europe. Here, the technology corporation manufactures advanced electrical equipment as well as assemblies and devices for machine and plant manufacturers worldwide. This also includes projects in the logistics and automotive industries. Its previous manual shelf storage system for small parts had reached its capacity limits, so Siemens WKC was looking for a more efficient solution.
The challenge
The company decided to switch to a goods-to-person small item picking system featuring an AutoStore™ system. Long-time partner, Still Intralogistics Consulting, developed the new logistics concept, which included the automation of the small parts warehouse with an AutoStore system. Siemens commissioned intralogistics specialist Dematic with the compact small parts picking system and the direct connection to the conveyor system.
Around 46,000 switchgears and customised electronic components for the global market are manufactured annually at Siemens WKC. Over the years, the volume and throughput in the warehouse have increased significantly. This made it necessary to reorganise the entire warehouse management: “Until then, we were still working with a manual modular rack warehouse,” reports Carsten Sambo, Head of Inbound Logistics, Siemens WKC. However, the former manual warehouse was no longer meeting current requirements.
About the customer
The Siemens Systems Engineering Plant (WKC) in Chemnitz has a long tradition in control cabinet construction for machine tools as well as a wide range of industries in general mechanical and plant engineering. This also includes projects in the logistics and automotive sectors. The range of services includes the complete spectrum from application engineering, material logistics and assembly of electrical equipment to testing and pre-commissioning. Deliveries are made to customers worldwide. The specific scope of services is determined individually by the respective customer on an order-by-order basis. WKC is also a recognized competence centre for the climatization of control cabinets. It has his own test laboratory with associated possibilities for performing load test. WKC is in addition a certified UL panel shop.
Carsten Sambo, Head of Inbound Logistics, Siemens WKC“With the new warehouse, we are well prepared for the future...”
Automation of the production warehouse with AutoStore
Siemens initiated the search for a new solution: “Our goal was to make planning and production as efficient as possible. At the same time, the lead time was to be reduced and, of course, the costs were to be lowered,” explains Sambo. The new storage systems, including the conveyor technology, needed to be installed on the same floor space in the existing building and during ongoing operations.
Long-time partner, Still Intralogistics Consulting, took on the initial planning of the logistics concept. This included automating the small parts warehouse with an AutoStore system to improve the supply of small parts to production. “We already had very good experience with an AutoStore storage system at a Siemens plant in Bad Neustadt (EWN),” explains Sambo. It accommodates up to four times more stock than the previous manual system. After only a short introductory phase, the Siemens WKC also achieved improved picking performance with 75 retrieval positions per hour (previously only 30 retrieval positions per hour). With the help of the system, this performance will increase by at least another 15 per cent.
As a global distribution partner for AutoStore, Dematic was brought in for its extensive experience and expertise. Siemens commissioned Dematic (a sister company of STILL in the KION Group) as a system integrator to implement the AutoStore system and connect it using Dematic conveyor technology for automation that optimizes the material flow for production supply. A major advantage of this unit load picking solution is that it requires very little space. Siemens can use the space gained for storing larger material items, such as enclosures for switchgear. STILL supplied a racking system for around 12,000 storage locations and 2,100 square metres of platform space as part of the overall logistics concept.
Technical data
- 8 Transfer Stations
- AutoStore® foot print: 760 suqare metres
- 45,000 bins
- 34 robots
- 5 picking ports
- 7,000 different picking positions daily
Capacities significantly increased
The conveyor system implemented by Dematic has two levels. In the goods receiving area, incoming parcels are first scanned and transported to the upper level via a lift. There, the goods are automatically and randomly distributed to the eight transfer stations. Empty AutoStore totes from the lower level go to the workstations. The totes are loaded with inventory and conveyed to the automatic small parts store. A scale checks the weight of the totes to ensure that they do not exceed the permissible maximum weight of 30 kilograms. Transfer cells automatically deliver the totes into the AutoStore system where the mobile robots can then take the inventory and store it. The compact AutoStore system itself occupies an area of only 760 square metres. It contains a total of more than 45,000 bins, which are divided into different compartments and can thus hold several different products.
With a request comes from production, the picking process starts — the provision of goods to the internal logistics, which prepares the materials according to production requirements and makes them available for production. The inventory for the orders are collected by the 34 mobile robots that travel on top of the AutoStore system. They pick the boxes from the grid and bring them to the port, where employees can carry out their picking activities without interruption. Previously, they had to travel long distances to pick the individual items. With the same number of employees, Siemens can now handle more orders in less time. “The system is highly efficient and with significantly fewer errors in the picking process,” says Carsten Sambo.
Equipped for the future
The AutoStore system can store up to four times more stock in the same footprint than conventional storage systems. “The cube-storage system is a self-supporting aluminium grid whose modular structure allows containers to be stacked closely next to and on top of each other. Furthermore, it is organised in a decentralised manner — if a robot is out of service, the system continues to run,” explains Sambo, adding, “We have daily call-offs of more than 7,000 different picking positions. To be able to access the required goods quickly in the morning, we have programmed a forecast function for stock removal or night shift transfer.”
Overnight, the demand for the next day is checked. The determined materials are transferred from the lowest levels of the AutoStore system to the upper area of the grid. “This ensures that the required containers can be accessed quickly with the start of the early shift.”
The small parts warehouse concept was developed with close collaboration among Siemens, Dematic, and STILL. In the end, Sambo sums it up, “We are now well prepared for the future, with scalability already taken into account during the planning stage. We’ve been able to increase the storage and picking capacities as well as make the entire warehouse management more efficient.” The fact that the production supply was maintained without interruptions during installation was a personal highlight for the Siemens project manager.
Customer benefits
- Four times more stock in the same floor space
- No more unproductive walking routes
- Lower error rate
- Decentralised organisation of robots minimises downtime
- Modular design allows for easy expandability
- Forecasting function and night shift reallocation allows faster access to the required goods