พื้นที่เล็กแต่ความจุมหาศาล
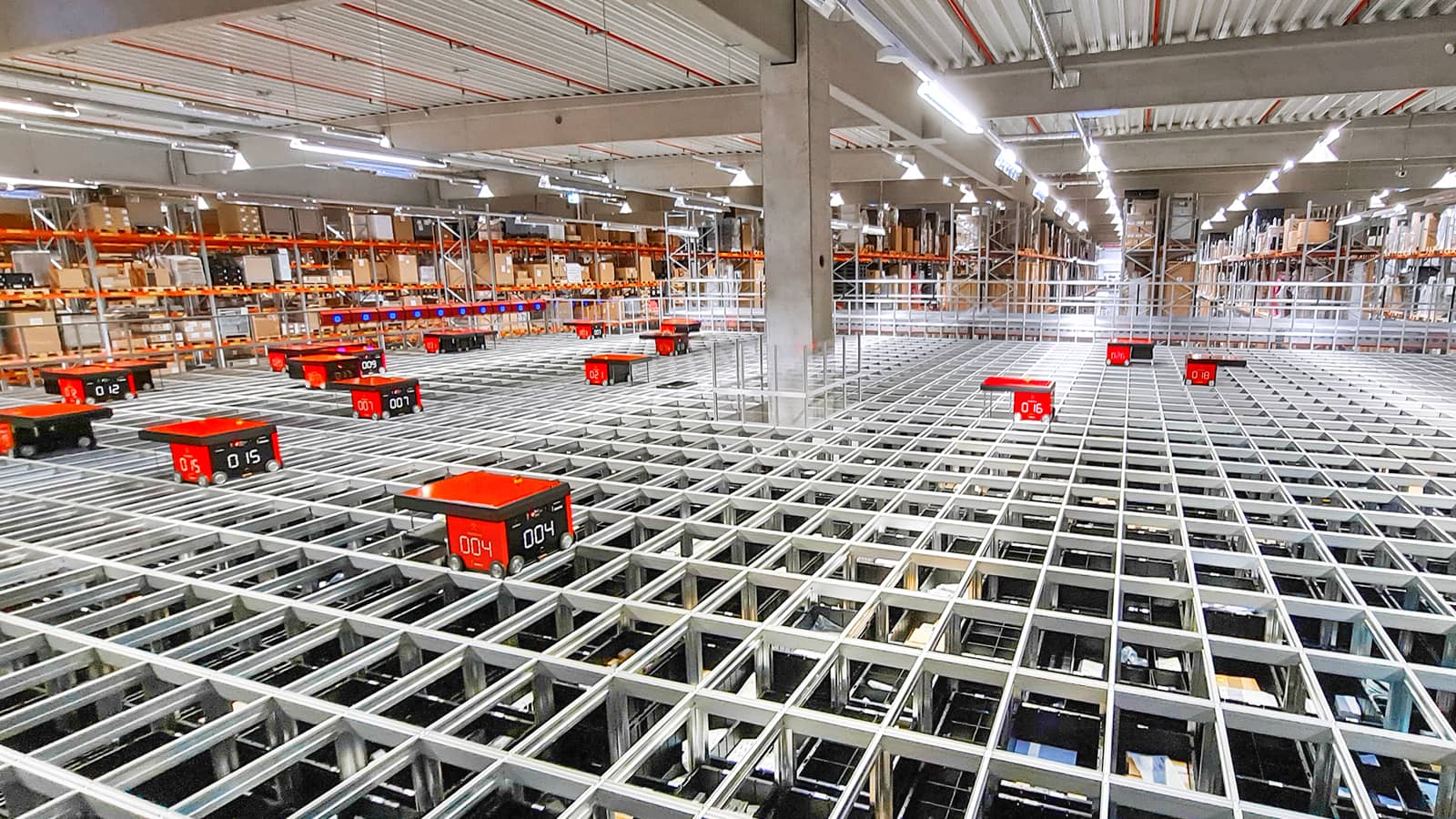
โรงงานของ Siemens WKC ในเมืองเคมนิทซ์ประเทศเยอรมนี คือผู้นำด้านงานติดตั้งตู้สวิตช์เกียร์สำหรับเครื่องมือและเครื่องจักรในการผลิตของยุโรป ณ สถานที่แห่งนี้เป็นแหล่งผลิตอุปกรณ์ไฟฟ้าเทคโนโลยีชั้นสูงรวมถึงการประกอบอุปกรณ์ต่างๆสำหรับเครื่องควบคุมเครื่องจักรและโรงงานการผลิตต่างๆทั่วโลก ซึ่งรวมถึงโครงการต่างๆในอุตสาหกรรมโลจิสติกส์และยานยนต์อีกด้วย ก่อนหน้านี้ระบบจัดเก็บชิ้นส่วนขนาดเล็กเป็นแบบชั้นวางที่ใช้คนในการค้นหาซึ่งทำได้ถึงขีดจำกัดสูงสุดแล้ว ดังนั้น Siemens WKC จึงมองหาโซลูชันที่มีประสิทธิภาพมากขึ้นเพื่อตอบสนองความต้องการที่สูงขึ้น
ความท้าทาย
บริษัทได้ตัดสินใจครั้งสำคัญโดยการเปลี่ยนไปใช้โซลูชันการหยิบสินค้าชิ้นเล็กเหล่านั้นด้วยระบบ ‘สินค้าถึงบุคคล’ ด้วยระบบ AutoStore™ ในการนี้ Still Intralogistics Consulting บริษัทที่เป็นพันธมิตรที่ยาวนาน ได้พัฒนาแนวคิดด้านโลจิสติกส์ใหม่ โดยการใช้ระบบคลังสินค้าขนาดเล็กอัตโนมัติที่จัดการด้วยระบบ AutoStore จนกระทั่ง Siemens ได้มอบหมายให้ Dematic ผู้เชี่ยวชาญด้านโลจิสติกส์ในโรงงาน เป็นผู้จัดการระบบคัดเลือกชิ้นส่วนขนาดเล็กที่เชื่อมต่อโดยตรงกับระบบสายพานลำเลียงทั้งหมด
ตู้สวิตช์เกียร์กว่า 46,000 ชุดรวมไปถึงอุปกรณ์อิเล็กทรอนิกส์ภายในที่เป็นส่วนประกอบ ได้ถูกผลิตขึ้นที่ Siemens WKC แห่งนี้เพื่อป้อนเข้าสู่ตลาดโลกทุกปี ในช่วงหลายปีที่ผ่านมา ปริมาณงานและชิ้นส่วนในคลังเก็บวัสดุเพิ่มขึ้นมาอย่างมาก ทำให้จำเป็นต้องจัดระเบียบการจัดการคลังเก็บวัสดุใหม่ทั้งหมด “ตอนนั้นเรายังทำงานกับคลังวัสดุแบบ manual อยู่เลย” กล่าวโดย Mr. Carsten Sambo หัวหน้าฝ่ายโลจิสติกส์ขาเข้าของ Siemens WKC แต่บัดนี้คลังวัสดุที่ใช้คนแบบเดิมไม่สามารถทำได้ตามข้อกำหนดของความต้องการในปัจจุบันได้อีกต่อไป
เกี่ยวกับ Siemens
โรงงานวิศวกรรมระบบของ Siemens WKC ในเมืองเคมนิทซ์มีประวัติอันยาวนานในการสร้างตู้ควบคุมสำหรับเครื่องมือกล ตลอดจนอุตสาหกรรมที่หลากหลายในด้านวิศวกรรมเครื่องกลและโรงงานทั่วไป ซึ่งรวมถึงโครงการในภาคการขนส่งโลจิสติกส์และยานยนต์อีกด้วย ขอบเขตของการให้บริการครบครันตั้งแต่วิศวกรรมการออกแบบการใช้งาน การขนส่งวัสดุ และการประกอบวัสดุอุปกรณ์ไฟฟ้าที่รวมไปถึงการทดสอบคุณภาพและการทดสอบระบบก่อนการใช้งาน ซึ่งลูกค้ามาจากที่ต่างๆทั่วโลก โดยขอบเขตการให้บริการจะเฉพาะเจาะจงตามที่ตกลงกับลูกค้าแต่ละรายที่แตกต่างกัน Siemens WKC ได้รับการยอมรับในการสร้างตู้ควบคุมที่ทนต่อสภาพภูมิอากาศได้เป็นอย่างดี โดยมีห้องปฏิบัติการการทดสอบโหลดภาระต่างๆเป็นของตนเอง Siemens WKC ยังได้รับการรับรองการผลิตตู้ควบคุมจาก UL Panel Shop อีกด้วย
Mr. Carsten Sambo หัวหน้าฝ่ายโลจิสติกส์ขาเข้าของ Siemens WKC“ด้วยคลังวัสดุแบบใหม่ เราพร้อมแล้วสำหรับอนาคต” กล่าวโดย
ระบบอัตโนมัติของแวร์เฮ้าส์ในสายการผลิตทำงานด้วย AutoStore
Siemens จึงเริ่มค้นหาโซลูชันใหม่ “เป้าหมายของเราคือทำให้การวางแผนและการผลิตมีประสิทธิภาพมากที่สุด ในขณะเดียวกันเวลาการทำงานต้องลดลงและต้นทุนการผลิตก็ต้องลดตามด้วย” กล่าวโดย Mr. Sambo ระบบจัดเก็บวัสดุใหม่รวมถึงเทคโนโลยีสายพานลำเลียงจำเป็นต้องได้รับการติดตั้งบนพื้นในชั้นเดียวกันของอาคารที่มีอยู่เดิม และต้องสามารถดำเนินการติดตั้งได้ในขณะที่สายการผลิตยังคงสามารถดำเนินการได้อย่างต่อเนื่องไม่มีหยุด
Still Intralogistics Consulting พันธมิตรที่ยาวนาน ได้เริ่มวางแผนเบื้องต้นเกี่ยวกับแนวคิดด้านโลจิสติกส์ โดยการทำให้คลังวัสดุขนาดเล็กเป็นระบบอัตโนมัติด้วยระบบ AutoStore เพื่อเป็นการปรับปรุงการจัดส่งชิ้นส่วนอุปกรณ์ขนาดเล็กในสายการผลิต “เรามีประสบการณ์ที่ดีกับระบบการจัดเก็บวัสดุด้วยระบบ AutoStore ที่โรงงานของเราใน Bad Neustadt (EWN)” Mr. Sambo อธิบายต่อ ระบบนี้รองรับสต็อกของวัสดุได้มากกว่าระบบ manual เดิมถึงสี่เท่า หลังจากเริ่มช่วงต้นของโครงการไม่นาน Siemens WKC ได้รับการพิสูจน์ด้วยการปรับปรุงประสิทธิภาพจากการจัดส่งวัสดุได้ 75 รายการต่อชั่วโมง (เทียบกับอัตรา 30 รายการในก่อนหน้านี้) ด้วยความก้าวล้ำของระบบนี้ทำให้เป็นไปได้ว่าประสิทธิภาพของระบบอาจจะเพิ่มขึ้นได้อีกอย่างน้อย 15 เปอร์เซ็นต์
Dematic (บริษัทในเครือของ STILL ในกลุ่ม KION) ในฐานะพันธมิตรการจัดจำหน่ายระดับโลกของระบบ AutoStore ที่มีความรู้และประสบการณ์ความเชี่ยวชาญที่กว้างขวาง ได้รับความไว้วางใจจากทาง Siemens ให้เป็นผู้รวมระบบ System Integrator ระหว่างระบบ AutoStore เชื่อมต่อกับเทคโนโลยีสายพานลำเลียงของ Dematic เพื่อให้เป็นระบบอัตโนมัติรวมศูนย์ที่สามารถปรับการไหลของวัสดุสอดคล้องกับการผลิตได้อย่างเหมาะสม ข้อได้เปรียบที่สำคัญของโซลูชันนี้คือความต้องการในการใช้พื้นที่น้อยมาก ซึ่ง Siemens สามารถใช้พื้นที่ที่เหลือไปกับการจัดเก็บวัสดุที่มีขนาดใหญ่ เช่น เคสของตู้สวิตช์เกียร์ต่างๆ ขณะที่ทาง STILL ก็จัดหาระบบชั้นวางวัสดุได้กว่า 12,000 จุด และประสานพื้นที่ขนาด 2,100 ตารางเมตรนี้ขึ้นเป็นแพลตฟอร์มระบบโลจิสติกส์ภายในที่สมบูรณ์แบบ
ข้อมูลทางเทคนิค
- จุดคัดแยกวัสดุ 8 แห่ง
- พื้นที่จัดเก็บของระบบ AutoStore® ขนาด 760 ตารางเมตร
- กระบะเก็บวัสดุอุปกรณ์จำนวน 45,000 ใบ
- หุ่นยนต์จำนวน 34 ตัว
- จุดรับวัสดุ 5 แห่ง
- ตำแหน่งของจุดเก็บวัสดุ 7,000 ตำแหน่งต่อวัน
ความจุเพิ่มขึ้นอย่างทวีคูณ
ระบบสายพานลำเลียงที่ดำเนินการโดย Dematic มีสองชั้นด้วยกัน ในพื้นที่รับสินค้าขาเข้า พัสดุที่เข้ามาจะถูกสแกนและขนถ่ายไปยังชั้นบนโดยลิฟต์ขนของ จากนั้นพัสดุจะถูกสุ่มกระจายโดยอัตโนมัติไปยังหน่วยคัดแยกแปดจุด ขณะที่ชั้นล่าง กระบะเปล่าใส่อุปกรณ์ของ AutoStore จะเคลื่อนที่ขึ้นเพื่อรับวัสดุจากหน่วยคัดแยกวัสดุด้านบน จากนั้นเจ้าหน้าที่จะนำวัสดุที่ได้รับการคัดแยกใส่ลงในกระบะเหล่านั้นเพื่อที่จะส่งไปยังจุดเก็บวัสดุคงคลังขนาดเล็กอัตโนมัติต่อไป กระบะแต่ละใบที่บรรจุวัสดุคงคลังเหล่านั้นจะได้รับการตรวจสอบน้ำหนักเพื่อให้แน่ใจว่าไม่เกินน้ำหนักสูงสุดที่ 30 กิโลกรัม เซลล์หุ่นยนต์เคลื่อนย้ายอัตโนมัติจะรับเอากระบะแต่ละใบเข้าสู่ระบบ AutoStore ซึ่งหุ่นยนต์เคลื่อนที่จะนำกระบะสินค้าคงคลังไปจัดเก็บในพื้นที่ที่เตรียมไว้กว่า 760 ตารางเมตร สถานที่แห่งนี้สามารถรองรับกระบะวัสดุคงคลังได้มากกว่า 45,000 ใบ ซึ่งแบ่งออกได้เป็นช่องต่างๆตามชนิดของวัสดุคงคลังที่มีอยู่มากมายหลายชนิด
เมื่อมีการเบิกชิ้นส่วนมาจากฝ่ายผลิต การจัดหาวัสดุชิ้นส่วนต่างๆที่เป็นกระบวนการโลจิสติกส์ภายในก็เริ่มต้นขึ้นเพื่อเตรียมวัสดุให้ได้ตามข้อกำหนดและเพียงพอสำหรับการผลิต คำสั่งเบิกวัสดุอุปกรณ์ต่างๆจะถูกจัดการด้วยหุ่นยนต์เคลื่อนที่ 34 ตัวที่เดินทางอยู่บนระบบรางด้านบนของระบบ AutoStore หุ่นยนต์เหล่านี้จะทำหน้าที่เลือกกล่องจากตำแหน่งการจัดเก็บเพื่อนำไปส่งที่จุดรับวัสดุ ซึ่งเจ้าหน้าที่สามารถดำเนินกิจกรรมการบรรจุรวบรวมได้โดยไม่มีการหยุดชะงัก แต่ก่อนหน้านี้เจ้าหน้าที่ต้องเดินทางไกลเพื่อเลือกวัสดุแต่ละชิ้นด้วยตัวเอง แต่มาตอนนี้ด้วยจำนวนเจ้าหน้าที่ที่เท่ากัน ทาง Siemens สามารถจัดการกับคำสั่งได้มากขึ้นในเวลาที่น้อยลงมาก “ระบบนี้มีประสิทธิภาพสูงและลดข้อผิดพลาดให้น้อยลงมากในกระบวนการคัดเลือกวัสดุที่หลากหลาย” Mr. Carsten Sambo กล่าว
พร้อมแล้วสำหรับอนาคต
ระบบ AutoStore สามารถจัดเก็บสต็อควัสดุคงคลังได้มากกว่าเดิมถึงสี่เท่าในพื้นที่เดียวกันเมื่อเทียบกับระบบเดิม “โครงสร้างการจัดเก็บวัสดุเป็นแบบลูกบาศก์ที่มีโครงข่ายอะลูมิเนียมรองรับตัวเอง การจัดเก็บแบบนี้จะทำให้สามารถวางกระบะวัสดุซ้อนทับกันและวางอยู่ชิดติดกันได้ นอกจากนี้ มันถูกจัดการในลักษณะการกระจายศูนย์ —จะกล่าวได้คือหากหุ่นยนต์ตัวใดตัวหนึ่งเสีย ระบบโดยรวมจะยังสามารถทำงานต่อไปได้” กล่าวโดย Mr. Sambo “เรามีความต้องการเบิกวัสดุอุปกรณ์มากกว่า 7,000 ตำแหน่งในแต่ละวัน ดังนั้นเพื่อให้สามารถนำวัสดุอุปกรณ์ไปใช้ได้เลยในการผลิตในตอนเช้า เราจึงต้องตั้งโปรแกรมฟังก์ชั่นการคาดการณ์สำหรับการกำจัดสต็อกล่วงหน้า หรือไม่ก็ทำการจัดเตรียมวัสดุในเวลากะกลางคืน” ในช่วงกลางคืนคำสั่งเบิกวัสดุของวันถัดไปจะถูกประมวลและตรวจสอบ วัสดุที่ต้องใช้จะถูกถ่ายโอนจากระดับชั้นที่ต่ำสุดของระบบ AutoStore ไปยังชั้นบนสุดของกริดที่เตรียมไว้ "ทั้งนี้เพื่อให้มั่นใจได้ว่าวัสดุอุปกรณ์ที่ต้องการจะได้รับการเข้าถึงได้เร็วที่สุดเมื่อเริ่มกะการทำงานถัดไปได้ทันที"
แนวคิดการจัดการคลังวัสดุชิ้นส่วนขนาดเล็กได้รับการพัฒนาโดยความร่วมมืออย่างใกล้ชิดระหว่าง Siemens, Dematic และ STILL ในท้ายที่สุด Mr. Sambo ได้สรุปไว้ว่า “ตอนนี้เราพร้อมแล้วสำหรับอนาคต โดยในช่วงที่ทำการวางแผนเราคำนึงถึงความสามารถในการขยายตัวให้เพิ่มขึ้นต่อไปได้ เราสามารถเพิ่มความจุในการจัดเก็บและการคัดเลือกวัสดุรวมทั้งทำให้การจัดการคลังวัสดุอุปกรณ์ทั้งหมดมีประสิทธิภาพมากยิ่งขึ้น” มีอีกหนึ่งเรื่องที่ได้รับการชมเชยโดยผู้จัดการโครงการของ Siemens ที่ว่า การจ่ายงานเพื่อป้อนกิจกรรมในการผลิตยังดำเนินต่อไปได้ตามปกติขณะที่ทำการติดตั้งระบบใหม่นี้เข้าไป ทำให้การทำงานโดยรวมของบริษัทฯไม่มีการหยุดชะงัก
ผลประโยชน์ที่ลูกค้าได้รับ
- ความจุในการจัดเก็บมากกว่าเดิมถึง 4 เท่าในพื้นที่เดียวกัน
- ไม่มีพื้นที่ทางเดินสูญเสียในระบบการจัดเก็บ
- ระบบมีความผิดพลาดต่ำมาก
- มีการกระจายงานของระบบหุ่นยนต์ช่วยลดเวลาสูญเสียจากหุ่นยนต์ที่เสียหาย
- การออกแบบเป็นโมดูลาร์ทำให้ขยายพื้นที่การจัดเก็บเพิ่มเติมได้ง่าย
- ฟังก์ชั่นการคาดการณ์และการจัดเตรียมในช่วงกะกลางคืนช่วยทำให้เข้าถึงวัสดุที่ต้องการได้เร็วขึ้น