Mayor capacidad en menor superficie
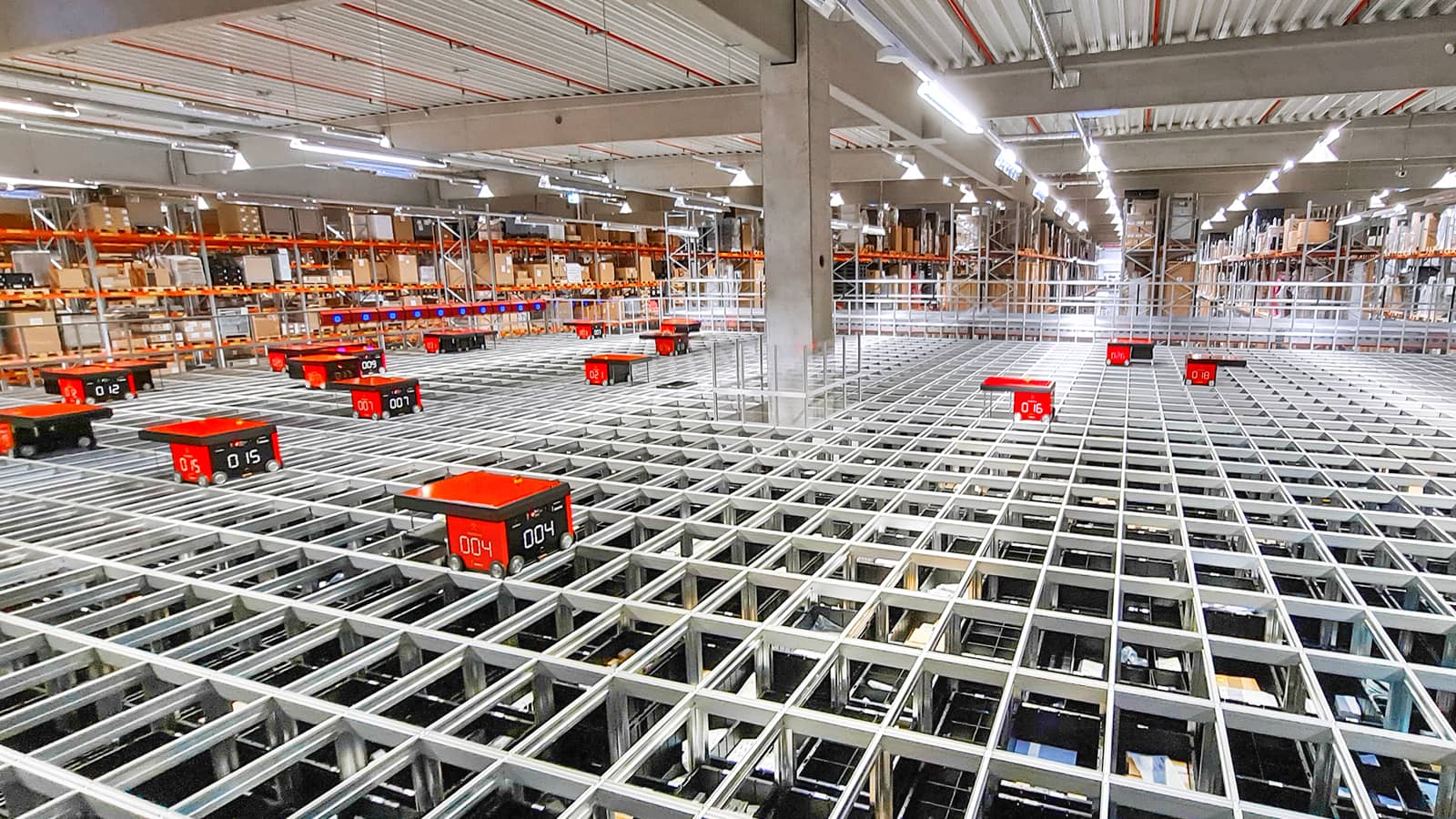
Desarrollo, ingeniería, producción, pruebas y puesta en servicio previa: la planta de Siemens para tecnología combinada de Chemnitz (Alemania) (Siemens WKC) es líder en Europa en la construcción de equipos de conmutación para máquinas herramienta y máquinas de producción. Aquí, la corporación tecnológica fabrica equipos eléctricos avanzados, así como conjuntos y dispositivos para fabricantes de máquinas e instalaciones de todo el mundo. Esto incluye también proyectos en los sectores de la logística y la automoción. Su anterior sistema manual de almacenamiento en estanterías para piezas pequeñas había alcanzado sus límites de capacidad, por lo que Siemens WKC buscaba una solución más eficiente.
El desafío
La empresa decidió cambiar a un sistema de picking de piezas pequeñas "mercancía a persona" con un sistema AutoStore™.
Still Intralogistics Consulting, socio desde hace muchos años, desarrolló el nuevo concepto logístico, que incluía la automatización del almacén de piezas pequeñas con un sistema AutoStore. Siemens encargó al especialista en intralogística Dematic el sistema compacto de picking de piezas pequeñas y la conexión directa al sistema de transporte.
En Siemens WKC se fabrican anualmente unos 46.000 conmutadores y componentes electrónicos a medida para el mercado mundial. A lo largo de los años, el volumen y el rendimiento del almacén han aumentado considerablemente. Esto hizo necesario reorganizar toda la gestión del almacén: "Hasta entonces, seguíamos trabajando con un almacén manual de estanterías modulares", informa Carsten Sambo, responsable de logística de entrada de Siemens WKC. Sin embargo, el antiguo almacén manual ya no cumplía los requisitos actuales.
Sobre el consumidor
La planta de ingeniería de sistemas de Siemens (WKC) en Chemnitz tiene una larga tradición en la construcción de armarios de control para máquinas herramienta, así como una amplia gama de industrias en ingeniería mecánica general y de plantas. Esto incluye también proyectos en los sectores de la logística y la automoción.
La gama de servicios abarca todo el espectro, desde la ingeniería de aplicaciones, la logística de materiales y el montaje de equipos eléctricos hasta las pruebas y la puesta en servicio previa. Las entregas se realizan a clientes de todo el mundo. El alcance específico de los servicios es determinado individualmente por cada cliente en función de cada pedido. WKC es también un centro de competencia reconocido para la climatización de armarios de control. Dispone de su propio laboratorio de pruebas con posibilidades asociadas para realizar pruebas de carga. WKC es además un taller de paneles certificado por UL.
Carsten Sambo, Head of Inbound Logistics, Siemens WKC"Con el nuevo almacén, estamos bien preparados para el futuro..."
Automatización del almacén de producción con AutoStore
Siemens inició la búsqueda de una nueva solución: "Nuestro objetivo era que la planificación y la producción fueran lo más eficientes posible. Al mismo tiempo, había que reducir el plazo de entrega y, por supuesto, los costes", explica Sambo. Los nuevos sistemas de almacenamiento, incluida la tecnología de transporte, debían instalarse en el mismo espacio del edificio existente y durante las operaciones en curso.
Still Intralogistics Consulting, socio desde hace muchos años, se encargó de la planificación inicial del concepto logístico. Esto incluía la automatización del almacén de piezas pequeñas con un sistema AutoStore para mejorar el suministro de piezas pequeñas a la producción. "Ya teníamos muy buena experiencia con un sistema de almacenamiento AutoStore en una planta de Siemens en Bad Neustadt (EWN)", explica Sambo. Tiene capacidad para hasta cuatro veces más existencias que el anterior sistema manual. Tras una breve fase de introducción, el WKC de Siemens también consiguió mejorar el rendimiento de picking con 75 posiciones de recuperación por hora (antes sólo 30 posiciones de recuperación por hora). Con la ayuda del sistema, este rendimiento aumentará al menos otro 15%.
Como socio de distribución mundial de AutoStore, se recurrió a Dematic por su amplia experiencia y conocimientos. Siemens encargó a Dematic (una empresa hermana de STILL en el Grupo KION) como integrador de sistemas la implementación del sistema AutoStore y su conexión mediante la tecnología de transportadores de Dematic para la automatización que optimiza el flujo de material para el suministro de la producción. Una gran ventaja de esta solución de picking de carga unitaria es que requiere muy poco espacio. Siemens puede utilizar el espacio ganado para almacenar material de mayor tamaño, como armarios para aparamenta. STILL suministró un sistema de estanterías para unas 12.000 ubicaciones de almacenamiento y 2.100 metros cuadrados de espacio de plataforma como parte del concepto logístico global.
Datos técnicos
- 8 estaciones de transferencia
- Huella de AutoStore: 760 metros cuadrados
- 45.000 contenedores
- 34 robots
- 5 puertos de picking
- 7.000 posiciones de picking diferentes al día
Aumento significativo de la capacidad
El sistema de transporte implantado por Dematic consta de dos niveles. En la zona de recepción de mercancías, los paquetes entrantes se escanean primero y se transportan al nivel superior mediante un ascensor. Allí, la mercancía se distribuye automática y aleatoriamente a las ocho estaciones de transferencia. Los contenedores vacíos de AutoStore del nivel inferior se dirigen a las estaciones de trabajo. Los contenedores se cargan con existencias y se transportan al almacén automático de piezas pequeñas. Una báscula comprueba el peso de los contenedores para garantizar que no superan el peso máximo permitido de 30 kilogramos. Las células de transferencia entregan automáticamente los contenedores al sistema AutoStore, donde los robots móviles pueden recoger el inventario y almacenarlo. El compacto sistema AutoStore ocupa una superficie de sólo 760 metros cuadrados. Contiene un total de más de 45.000 contenedores, que se dividen en distintos compartimentos y pueden albergar así varios productos diferentes.
Cuando llega un pedido de producción, se inicia el proceso de picking: el suministro de mercancías a la logística interna, que prepara los materiales según los requisitos de producción y los pone a disposición de ésta. El inventario de los pedidos lo recogen los 34 robots móviles que se desplazan sobre el sistema AutoStore. Recogen las cajas de la parrilla y las llevan al puerto, donde los empleados pueden realizar sus actividades de picking sin interrupción. Antes, tenían que recorrer largas distancias para recoger los artículos individuales. Con el mismo número de empleados, Siemens puede ahora gestionar más pedidos en menos tiempo.
"El sistema es muy eficiente y con un número significativamente menor de errores en el proceso de picking", afirma Carsten Sambo.
Equipado para el futuro
El sistema AutoStore puede almacenar hasta cuatro veces más existencias en el mismo espacio que los sistemas de almacenamiento convencionales. "El sistema de almacenamiento por cubos es una rejilla de aluminio autoportante cuya estructura modular permite apilar contenedores muy juntos y unos encima de otros. Además, está organizado de forma descentralizada: si un robot se estropea, el sistema sigue funcionando", explica Sambo, y añade: "Diariamente tenemos más de 7.000 puestos de picking diferentes. Para poder acceder rápidamente a la mercancía necesaria por la mañana, hemos programado una función de previsión de salidas de stock o de transferencia del turno de noche". Durante la noche, se comprueba la demanda para el día siguiente. Los materiales determinados se transfieren de los niveles inferiores del sistema AutoStore a la zona superior de la parrilla. "Así se garantiza que se pueda acceder rápidamente a los contenedores necesarios con el inicio del turno de mañana".
El concepto de almacén de piezas pequeñas se desarrolló en estrecha colaboración entre Siemens, Dematic y STILL. Al final, Sambo lo resume así: "Ahora estamos bien preparados para el futuro, ya que la escalabilidad ya se tuvo en cuenta durante la fase de planificación. Hemos podido aumentar las capacidades de almacenamiento y preparación de pedidos, así como hacer más eficiente toda la gestión del almacén." El hecho de que el suministro de producción se mantuviera sin interrupciones durante la instalación fue un punto culminante personal para el jefe de proyecto de Siemens.
Beneficios para el consumidor
- Cuatro veces más existencias en la misma superficie
- Se acabaron los recorridos a pie improductivos
- Menor tasa de errores
- La organización descentralizada de los robots minimiza el tiempo de inactividad
- El diseño modular permite una fácil ampliación
- La función de previsión y reasignación del turno de noche permite un acceso más rápido a las mercancías necesarias