Convey & Sort System Optimizes Multi-Channel Distribution
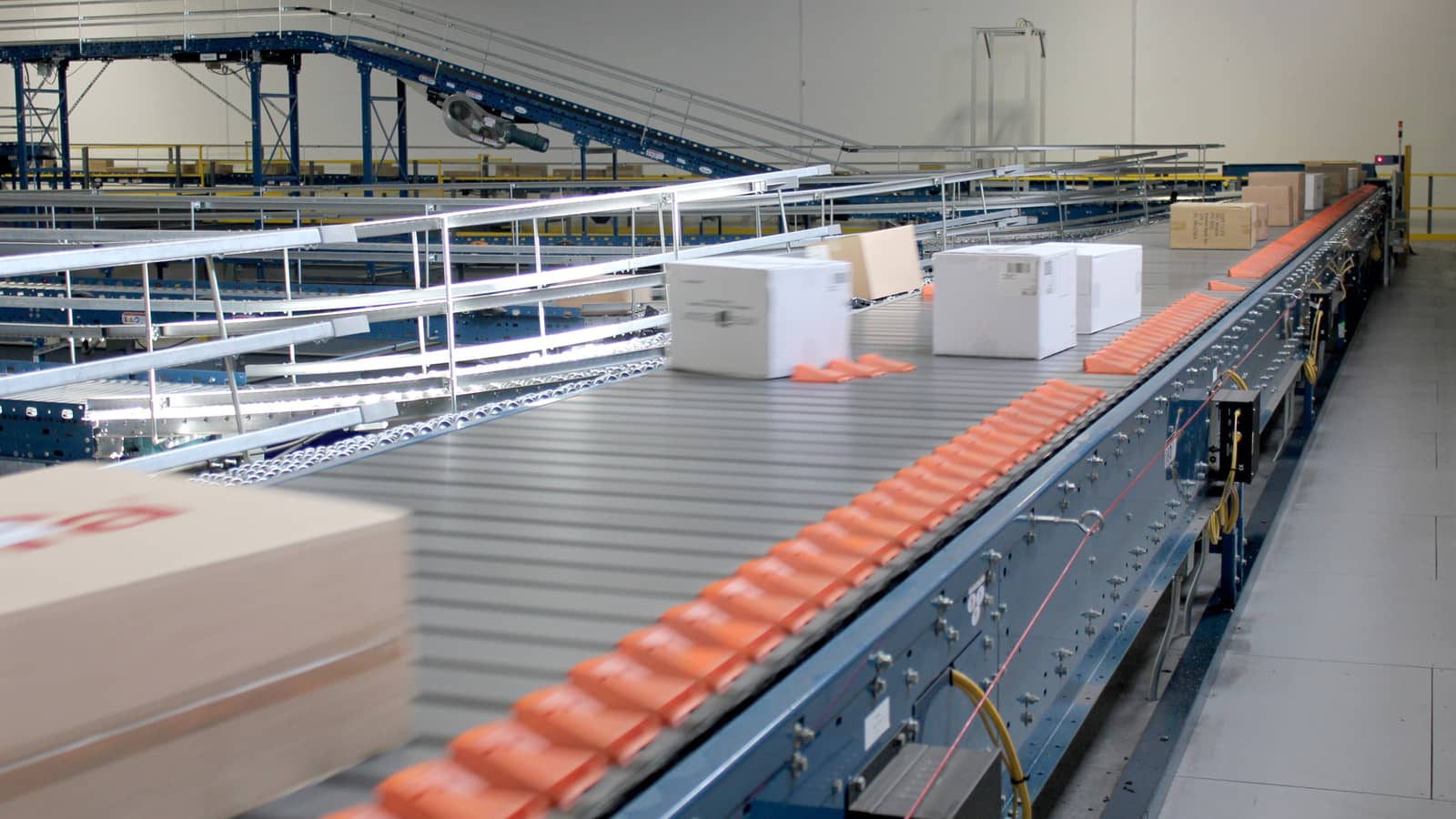
The Container Store is the nation’s leading retailer of storage and organization products and the only one solely devoted to the category. The Container Store has more than 11,000 multi-functional and innovative products for solving the smallest to most intimidating organizational challenges. Products are organized in 16 signature lifestyle sections such as closet, kitchen, office, travel, gift packaging, and laundry to help organize time-and-spacestarved customers.
The challenge
The requirement for increased distribution capacity and the ability to accommodate a wide variety of order profiles drove the design for a high performance order fulfillment system.
A more efficient way to pick, pack, and ship in less time was needed. Furthermore, The Container Store required a distribution center design that utilized the same inventory and operational staff for multiple sales channels.
The solution
The Container Store Coppell, Texas facility is comprised of an “order container to pick zone” system, also known as a zone route system. Warehouse Execution Software (WES) directs the order containers strategically through the piece picking module, to packing workstations, and to the truck trailers in shipping.
The packing sub-system consists of workstations to pack e-commerce (customer direct) orders, including a case sealer, automatic label print/ apply, and in-line weigh scale. At the shipping doors, a sliding shoe sorter directs cartons to the appropriate truck trailer to be delivered to the retail stores.
Inventory is received from merchandise vendors, processed, and placed into storage. The item velocity, size, and weight determine the appropriate location for storage. Pick location re-stocking is directed using RF devices.
When an order is received, it is downloaded to the Warehouse Management System (WMS), which controls and directs the pick, pack, and ship processes.
A bar code label on the tote acts as a license plate and is linked to the order. The order tote enters onto the conveyor network. There’s no need to roam the distribution center looking for the items for an order. Instead, the order tote is automatically conveyed to zones in the pick modules.
Totes are scanned for validation at multiple points. This assures that each tote is directed to the appropriate zone and allows real time tracking.
When an order tote arrives in a picking zone, the items for an order are placed inside. Voice picking technology directs employees to a location and tells them the quantity of items to pick.
Then the tote is moved back onto the conveyor network. Order totes only travel to zones where there are picks. The different tote colors differentiate order sizes and sales channels.
Next, the order totes travel to the packing area. Here, the items are removed, audited, and packed into a shipping carton. Documents are inserted along with packing materials. From there, the cartons pass through a case sealer.
The shipping carton for each order is scanned and weighed automatically “on-the-fly” to confirm order accuracy and determine parcel shipping costs. A label is printed and automatically applied to each carton.
The order fulfillment system supports retail stores, e-commerce (customer direct), and business-tobusiness wholesale channels, all within one integrated layout.
The cartons are then conveyed to a shipping door and loaded onto a truck trailer for shipping. If an order includes bulk items, it is selected, picked, and delivered to the appropriate dock door for shipping.
For retail store replenishment and business-to-business channels, employees pick cases of merchandise and place them onto the conveyor system in the full case pick module.
Other merchandise not stored in the pick modules is picked onto a pallet and then inducted into the conveyor system.
Smaller, less than case quantities required for the retail store and businessto-business channels are picked from the zone route, piece pick module. The cases of merchandise flow to the store replenishment sorter in the shipping area.
A scanner reads the bar code on each case or tote. The sliding shoe sorter diverts the cartons and totes to the appropriate shipping door.
The results
The order fulfillment system supports retail stores, e-commerce (customer direct), and business-to-business wholesale channels, all within one integrated layout. Numerous benefits were created by using the same inventory and the same distribution center employees to accommodate all channels to market.
This process improvement — along with material handling automation and software — have increased efficiency, order accuracy, and employee productivity while reducing order processing time. In addition, the fulfilment system is scalable and can accommodate surges in demand as well as future growth.