New HQ Delivers Improved Supply Chain Performance for Blackmores
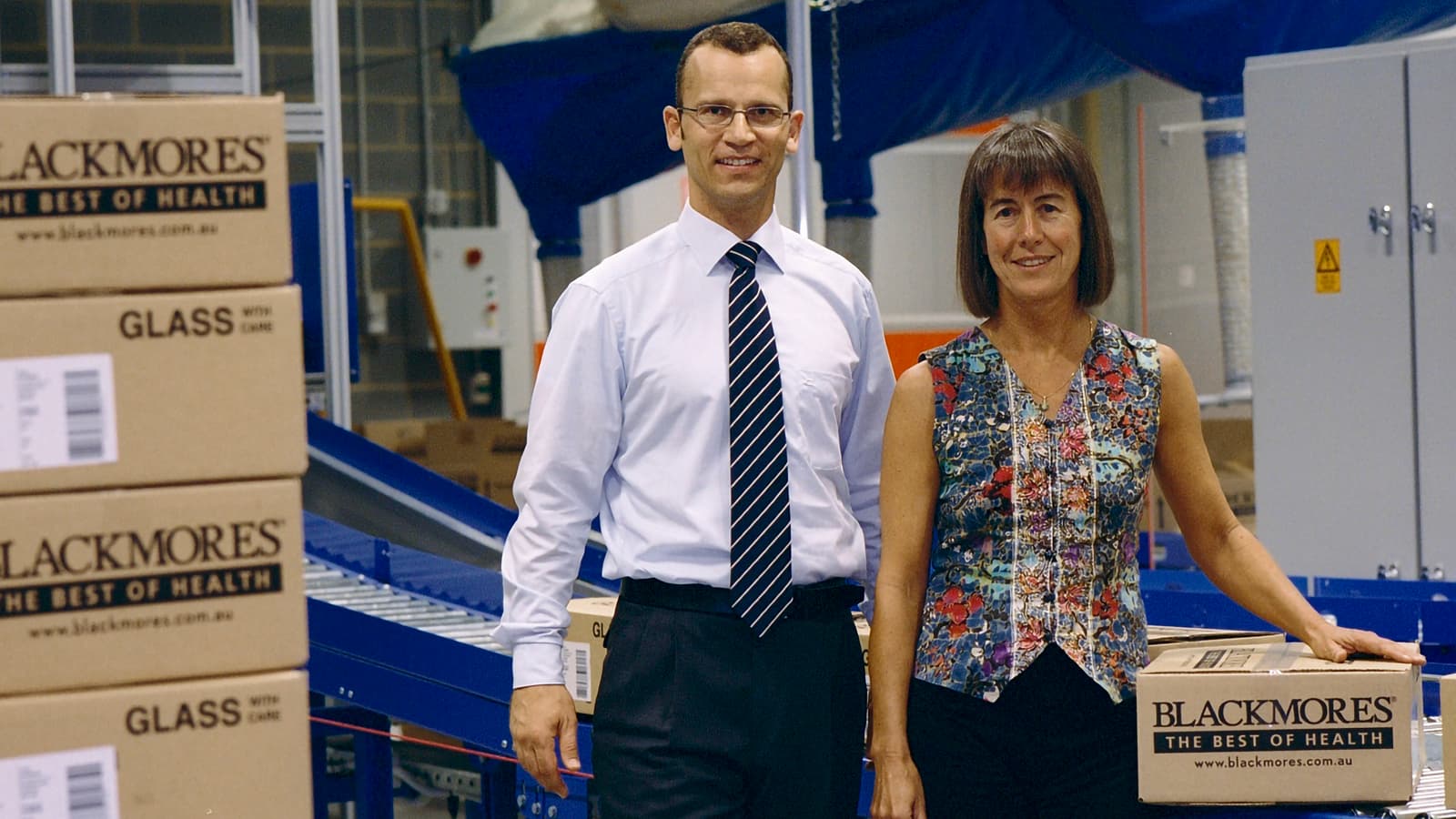
Over the past 70 years, Blackmores has become Australia’s leading natural health supplements supplier and one of the country’s most trusted brands. The company supports a customer base of more than 5000 health food stores, pharmacies, supermarkets and health practitioners throughout the country. It has also established strong export markets in the Australasian and SE Asian regions. Fundamental to this growth has been its commitment to good manufacturing practice and supply chain innovation. Dematic was a natural choice of partner to understand this commitment and, working together, have realized new efficiencies in the business and supply chain savings of $1 million per year.
The challenges
The Blackmores Campus involved the company bringing its operations under one roof for the first time in over 15 years. Strong growth had made it necessary for Blackmores to split its manufacturing and distribution operations across a number of separate facilities and it was time to consolidate and enhance their operations. And, whilst bringing new efficiencies and cost savings to the business, Blackmores new Campus needed to embody the values and principles that drive the company’s ethos and culture.
Our solution
Dematic designed the new distribution center (DC) as a flowthrough facility. Raw materials feed through to production, and finished goods back through to storage and distribution. Materials handling is optimized at all stages and the DC has been equipped with the latest generation of order picking technologies including smart conveyors, Voice Picking, RF and Pick-to-Light systems.
Blackmores also rationalized their distribution IT systems with Dematic’s new PickDirector software. And in a world-first, Dematic has integrated Blackmores put-away and replenishment functions within PickDirector, which seamlessly interfaces with Blackmores’ host computer system.
Dematic’s DC systems incorporate a lot of flexibility to ensure efficient materials handling, storage and order fulfillment, even if Blackmores’ distribution requirements were to change over time. Dematic believed this was necessary because the company’s SKU (stock keeping unit) profile has changed considerably in recent years as a result of market growth and maturity.
Liz Burrows, Director of Operations, Blackmores“Bringing our operations back under the one roof will not only provide direct supply chain savings in excess of $1 million per annum, it will also enable us to significantly streamline our supply chain and enhance productivity across the board.”
Storage
“Bringing our operations back under the one roof will not only provide direct supply chain savings in excess of $1 million per annum, it will also enable us to significantly streamline our supply chain and enhance productivity across the board.”
Split-case picking
All split-case products are picked from a Pick Module comprising two aisles of carton live storage (CLS) and a small area of static shelving. A central conveyor comprising gravity conveyors on either side of a powered take-away conveyor, transports orders through the Pick Module, while an automated carton erector delivers empty cartons direct to the pick face via an overhead conveyor.
All split-case product locations within the Pick Module are equipped with RapidPick3 Pick-to-Light (PTL) alphanumeric displays, enabling fast and accurate paperless picking. The clip-on PTL displays are easy to reposition, making it a simple task to alter the configuration to accommodate changing layouts and product dimensions.
Pre-cubing software determines the size and number of cartons that will be required for an order, with PickDirector generating the required number of barcoded shipping labels.
When a carton is full or the order completed, it is pushed onto the central powered take-away conveyor, which transports the carton to a void fill and packing station via a check-weighing station.
With increasing numbers of customers preferring to receive electronic invoices (50%+), only those orders requiring a printed invoice are diverted to an invoice station. The sealed cartons are then conveyed to the sorter where they are automatically diverted down one of four shipping lanes, and consolidated for distribution.
Lee Richards, Chief Technology Officer, Blackmores“With PickDirector providing the interface for all of our DC technologies, we were able to decommission a number of servers, systems and interfaces which has allowed us to simplify the DC’s IT systems architecture, enhancing operational reliability and reducing our IT systems management requirements.”
Full-case picking
Fast moving, full case SKUs are picked from a combination of Pallet Live Storage (PLS) and selective racking within the full case Pick Module. A combination of RF and Voice Picking may be used for picking full case SKUs which are labeled and placed directly onto a central powered take-away conveyor.
Other full case products are picked to pallet directly from their bulk storage locations, again using a combination of RF and Voice Picking.
Full pallets for larger customer and export orders are also picked from their bulk storage location by RF or Voice Picking and transported to dispatch by forklift.
Stephen Vile, Supply Chain Manager, Blackmores“The performance of the Voice picking system in the full case Pick Module has been exceptional; we are now able to pick full cases twice as quickly as before, and with only half the people!”
Dematic’s integrated logistics solution gives Blackmores a set of tools with which it can handle, store, pick and dispatch goods faster and more accurately now, and for many years to come.
Customer benefits
- Increased productivity
- Faster order turnaround
- Increased order fulfillment accuracy
- Improved OH&S
- Higher order fill rate
- Automated order tracking and sortation for distribution
- Improved palletizing and dispatch procedures for larger orders