Goods-to-Person System E-Fulfillment Optimization
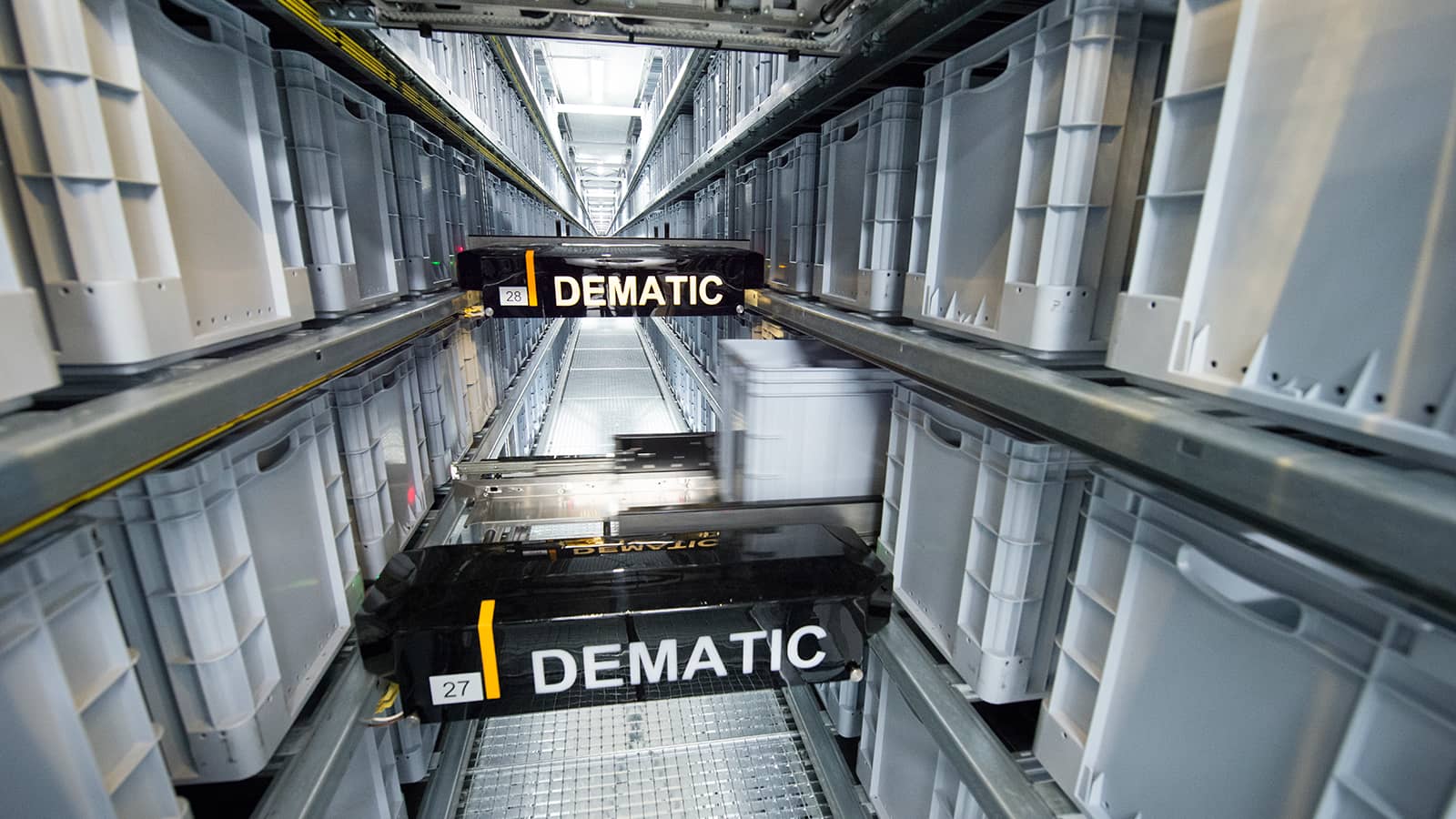
Magid, a manufacturer and distributor of personal protective equipment in Romeoville, Illinois, operates a distribution center that incorporates a goodsto-person piece picking method supported by a Dematic Multishuttle® inventory storage engine.
Magid is both a U.S.-based manufacturer and worldwide distributor of Personal Protective Equipment (PPE).
Their team of safety experts consults with industries across North America to answer questions, conduct onsite assessments, and tackle industrial challenges — from customizing PPE to creating inventory management and distribution programs.
For more than 70 years Magid has offered their own line of quality PPE — introducing 400 new products last year alone as well as over 700 leading brands of personal safety equipment for commercial and industrial applications.
Their tagline, “Safety at Work,” is more than just a slogan as they protect their own industrial workers each day and promise their customers:
The Products You Need, the Flexibility You Want, and the Experts You Trust.
The challenge
The company had outgrown their existing business headquarters/ offices and distribution center. The objective for the project was to consolidate the operation into one building at a new location and increase order processing capacity for current and future growth.
The intralogistics goal was to improve the customer experience using a new process and automation while reducing the cost and time to fill orders.
Our solution
Receiving Inventory
A key feature of the new distribution center is the goods-to-person (GTP) order fulfillment system featuring a Dematic Multishuttle. The system has a compact footprint, which allows more space for other warehouse functions and growth.
As a double-deep, two-aisle inventory storage buffer, Multishuttle, accommodates approximately 18,500 totes over 13 levels, with each level serviced by its own shuttle.
Inbound inventory is transported from the receiving area to the decanting workstations. Here, each stock keeping unit (SKU) is “checked-in” and unloaded from the received carton and placed into a storage tote.
There are two decanting workstations. Through the use of removable dividers, each tote can store one, two, four, or eight SKUs. When the decanting process is complete for each SKU, the inventory tote is conveyed to the Multishuttle storage sub-system.
Filling orders
The Multishuttle sub-system is the engine that supplies the inventory totes to the goods-to-person workstations. Inventory retrieved from the Multishuttle is delivered to the goods-to-person workstations as required for order assembly, ensuring very high productivity and order accuracy.
The workstation configuration presents a single inventory tote to operators with the order cartons so they do not waste time having to locate and identify stock. It also enables multiple orders requiring the same SKU to be fulfilled concurrently. There are three goods-to-person workstations:
- A single line workstation accommodates one donor inventory tote and one customer “pick to” order container.
- Two multi-line workstations accommodate one donor inventory tote and up to 20 customer order containers.
When a tote arrives at the workstation, a monitor displays an image of the SKU along with the quantity of items to be picked. Pick-to-light displays at each order location show the number of items required for each order, which virtually eliminates the potential for picking errors. In fact, the overall order accuracy rate for the entire distribution center is 99.9%.
Operators work in parallel at the goodsto-person workstations, unaffected by each other’s pace. The workstations can be opened and closed as required for a particular shift.
The system provides full redundancy as orders can be processed at any location, with all workstations operating independently.
Shipping preparation
After all of the required SKUs from the goods-to-person workstations have been picked, the integrated conveyor system transports customer order cartons to the shipping area.
The order cartons pass through an in-line packing system where they are void filled, sealed, and labeled for shipping. An in-line scale weighs each carton on-the-fly.
Conveyor then transports the orders to a sorting system that diverts cartons to the appropriate shipping door. At shipping, the order cartons are palletized or conveyed directly into a truck trailer.
The Magid distribution center processes approximately 1,300 orders during a typical day and ships about 2,600 cartons per day. About 98.5% of customer orders ship the same day.
Tracking & reporting
The Dematic iQ Warehouse Execution System (WES) software is responsible for managing and directing piece picking in the distribution center, replenishment, stock control, and location management within the Multishuttle system.
The software also controls the real-time flow of orders through the goods-to-person workstations and the flow of customer orders through the conveyor system to shipping.
The Dematic iQ WES software provides full track and trace capabilities for every customer order carton as well as visibility and insight into system performance.
It optimizes operational processes from planning to order fulfillment and shipping within one flexible, scalable and modular platform.
The results
The Dematic goods-to-person order fulfillment system is a modern and effective way to accomplish the complex task of piece picking.
The high density Multishuttle inventory storage sub-system has a compact footprint that uses less warehouse space for the growing number of SKUs.
The put-away process supports labor productivity, ergonomics, and inventory accuracy, and it reduces the time to replenish.
The inventory storage location management software supports FIFO strategies for the put-away process in the Multishuttle sub-system.
Inventory management is optimized with ongoing cycle counting and controlled access to the SKUs. Furthermore, the Dematic software plans and directs SKU movement to the goods-to-person workstations in a precise order to optimize order assembly.
Dedicated goods-to-person workstations for single line and multi-line orders maximize order picking productivity and efficiency. The goods-to-person workstations are designed to be so intuitive and easy-to-operate that they allow new warehouse staff to be productive on their first day on the job.
Future growth
The overall system is modular and expandable to accommodate operational changes and future growth. Additional Multishuttle sub-system aisles can be added to provide more inventory storage capacity.
By adding more storage locations and workstations in the future, the system can be significantly expanded as SKU growth occurs and order volume increases.