Success in an Omni-Channel World
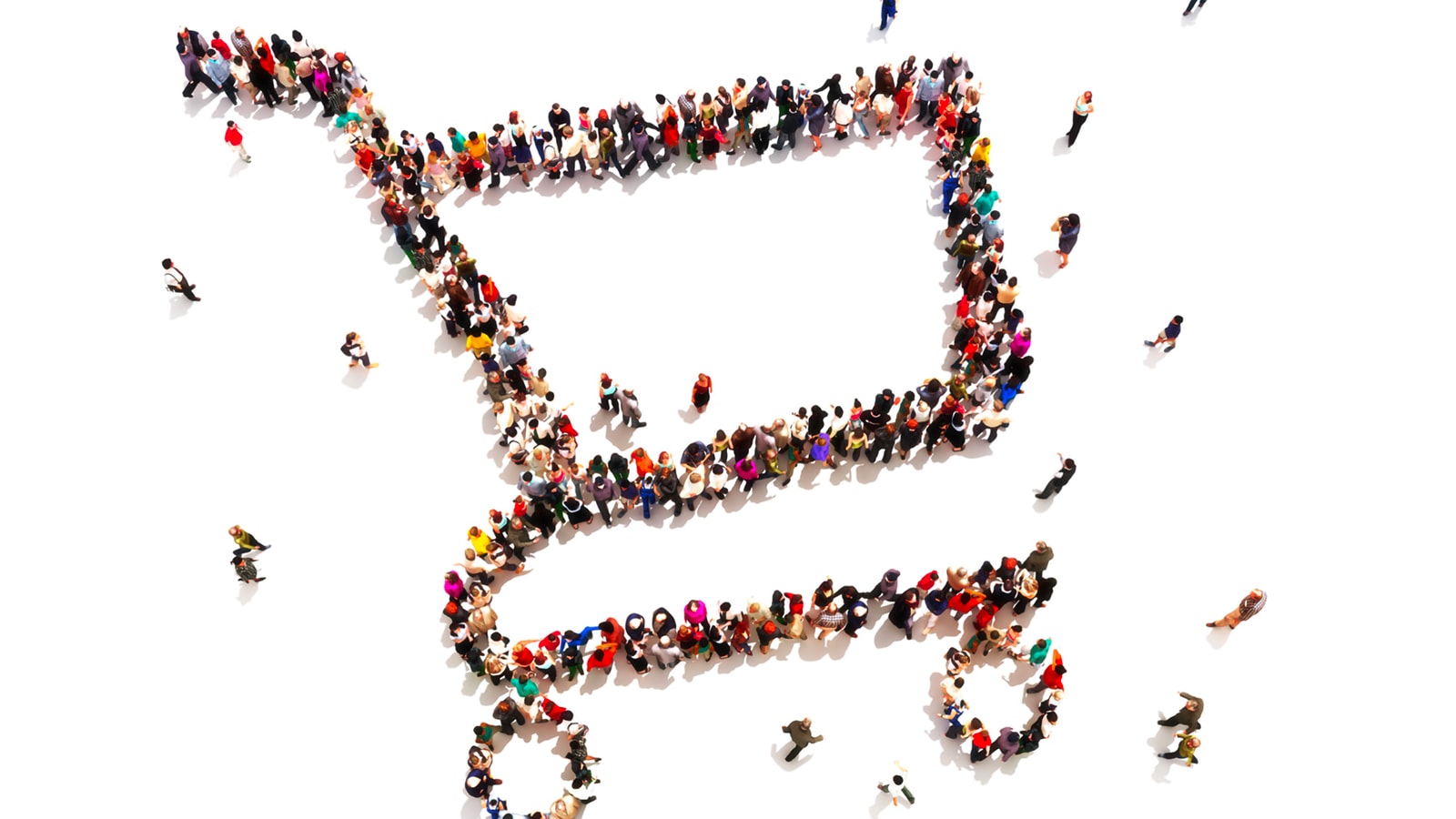
It is easy to define omni-channel business success by desired outcomes: happy, loyal customers resulting in increased sales and profits. What is considerably more difficult is describing how to get there and making it happen.
From the customer point of view, omni-channel means being the centre of the buying experience. No matter how customers interact with a particular brand — whether online, in a store or from a mobile device — they expect the experience to be seamless.
From the retailer point of view, omni-channel is much more complex. It means implementing a system that produces a consistently positive experience for shoppers and buyers. In practice this means providing multiple purchase and delivery options, managing channel expansion, optimising supply chains, automating order fulfilment and more.
Challenges of supporting omni-channel
Omni-channel is not a new concept. Retailers in many markets have recognised the wisdom of adapting to consumer buying habits to remain relevant and competitive. But even though a company is aware of the trend, it might not fully understand the barriers to developing a successful omni-channel initiative. Consider these challenges:
Omni-channel means delivering inventory in a way most convenient for the consumer, which is often not the most cost-effective way for the retailer. For example, instead of a shirt being shipped from a distribution centre (DC), the shirt is pulled from one store and shipped next-day to another. That can be much more expensive, but the consumer is happy.
If new methods are implemented to accommodate consumer demand (but without updating back-end processes and support structure), margins will inevitably be squeezed. Every attempt to be more responsive without well-defined supply chain solutions comes with an additional cost, and those costs add up quickly.
Omni-channel is often described as anytime/anywhere shopping. The net effect of responding to this is a greater variety of inventory to be distributed in more locations.
As next-day or same-day delivery have become the norm, consumers expect a rapid turnaround for all their orders. Shrinking cut-off times only increase the need for orders to be processed quickly. Competition is fierce. Retailers must ensure that inventory is available and controlled across their entire supply chain.
Consumers also expect their orders to be correct. Even a single wrong direct shipment can cause consumers never to order from a retailer again. And social media can compound that wrong shipment into multiple consumers. It is critical for order accuracy to be addressed in omni-channel supply chains.
Even with the best of intentions and planning, any retailer is potentially limited by their existing infrastructure and geography. Locations of DCs and stores factor heavily into meeting regional, national and global consumer demands, not to mention beating the competition.
To meet consumer expectations, retailers must know where inventory is in their supply chain and be confident the count is accurate.
Strategic intelligence from Dematic
To meet the anytime/anywhere shopping demands, retailers absolutely need full control of their inventory. The tenuous loyalty of a target demographic can rest on providing an accurate account of the stocking status of product they desire.
After a purchase decision, there are the complex calculations necessary to determine the most cost-effective method of delivering a specific item to store, home, office, or other location. This is well beyond capabilities of any manual or per location system. It requires strategic intelligence backed up by enterprise software applications and support hardware.
To retailers and wholesalers this means an enterprise resource planning (ERP) or distributed order management (DOM) system as the central processing brain for order fulfilment. Central processing with strategic intelligence enables retailers and wholesalers to measure not only inventory but also performance of stores.
Data from stores can be used to leverage existing information to plan orders, shipments and fulfilment activities. Real-time data, analytics and reports provide the information flow necessary for inventory visibility.
As an example, a consumer orders uses a mobile device to order a shirt for pick up at a local store. It is the ERP or DOM that knows that the particular SKU is not in stock at the local store, but available at a DC or two other stores and will determine the optimal way to deliver it.
Depend on Dematic to fill orders
The last (sometimes forgotten but certainly critical) step to a successful omni-channel order fulfilment system is actually fulfilling the orders. It sounds obvious, but it is no small consideration. Again, with a goal as aggressive as meeting every consumer’s shopping whim, modern automated solutions for order fulfilment are not an option — they are an essential component.
Automated order fulfilment solutions include the software and controls to receive, store, pick, put and ship products with absolute efficiency. It is the technology that brings the system to life and maintains the throughput.
In this example, after the ERP or DOM determines that the DC is the best source for filling this order, it is the automated order fulfilment that picks the shirt, packs it and ships it to the local store where the consumer picks it up.
Case study solution examples
The omni-channel challenge represents an opportunity to re-think how inventory is deployed to optimise labour productivity, order accuracy, inventory accuracy and processing speed. How a company configures its omni-channel order fulfilment operations depends on variations in business volume, geographic constraints and its logistics philosophy. Below are brief descriptions of the design approaches available:
- Owners of dedicated fulfilment centres believe that the activity profile and therefore the picking processes are fundamentally different for each channel. Industrial engineering analysis indicates that the order fulfilment system configuration and technology best suited for e-Commerce is different from the configuration for retail store replenishment. Simply stated, assembling orders that consists of one or two line items is a world apart from assembling orders that consist of hundreds of line items with multiple pallets of merchandise.
- Dedicated fulfilment centres are also more appropriate when the inventory is different from what is offered in the retail store version of the brand.
- Dedicated fulfilment centres can be designed to accommodate the peak periods of each channel more effectively. For example, on weekends e-Commerce must accommodate pooled order surges and a wider variation in average-to-peak ratios. Engineers need to consider order accuracy and order processing speeds in the system design — e-Commerce orders must be accurate and timely. On the other hand, if a retail store DC ships too much of a particular SKU, the store could accept the order and sell it without affecting customer goodwill.
- Fill orders for e-Commerce, small retail store and large retail store in a hybrid distribution centre. Share inventory and labour across channels.
- Flex labour between channels because each business peaks at different times. Apply labour to retail if it peaks prior to e-Commerce. Then apply same labour to e-Commerce when it peaks later in the cycle.
- Use reserve storage with separate active picking locations for e-Commerce and retail stores. Or use same active pick locations for both channels. An analysis of the activity profile reveals which strategy is best for each application.
- To gain efficiencies, some omni-channel retailers have merged multiple distribution centres and brands into one operation. This allows efficiencies of scale and volume to reduce the cost to pick, pack and ship each order. The single inventory storing location reduces the cost of carrying inventory, and there is less need for safety stock throughout the network. In addition, inventory coming from just one location simplifies decision making for the order management software.
- Consolidated operations are more appropriate for automation. Increased volume at a single location can make the business case for order fulfilment technology like sorting automation and label print/apply systems. With automation, the cost to assembly each order is reduced while processing speed, labour ergonomics and order accuracy increase.
- Low volume retailers must be both effective and efficient in supporting omni-channel. Many boutique retailers are implementing pick, pack and ship systems that are pre-engineered and modular. Paper-based picking with hunt and pick methods are clunky, slow and labour-intensive.
- Discrete or batch pick methods that use performance optimising software allow small volume operations to keep up with the highly automated large volume national/global brands, but with a much lower capital expenditure. Pre-engineered, modular solutions are scalable for weekend-pooled order surges as well as other peak periods. Furthermore, these solutions allow fast and easy expansion to accommodate volume growth.