Enterprise Asset Management Seamless Integration
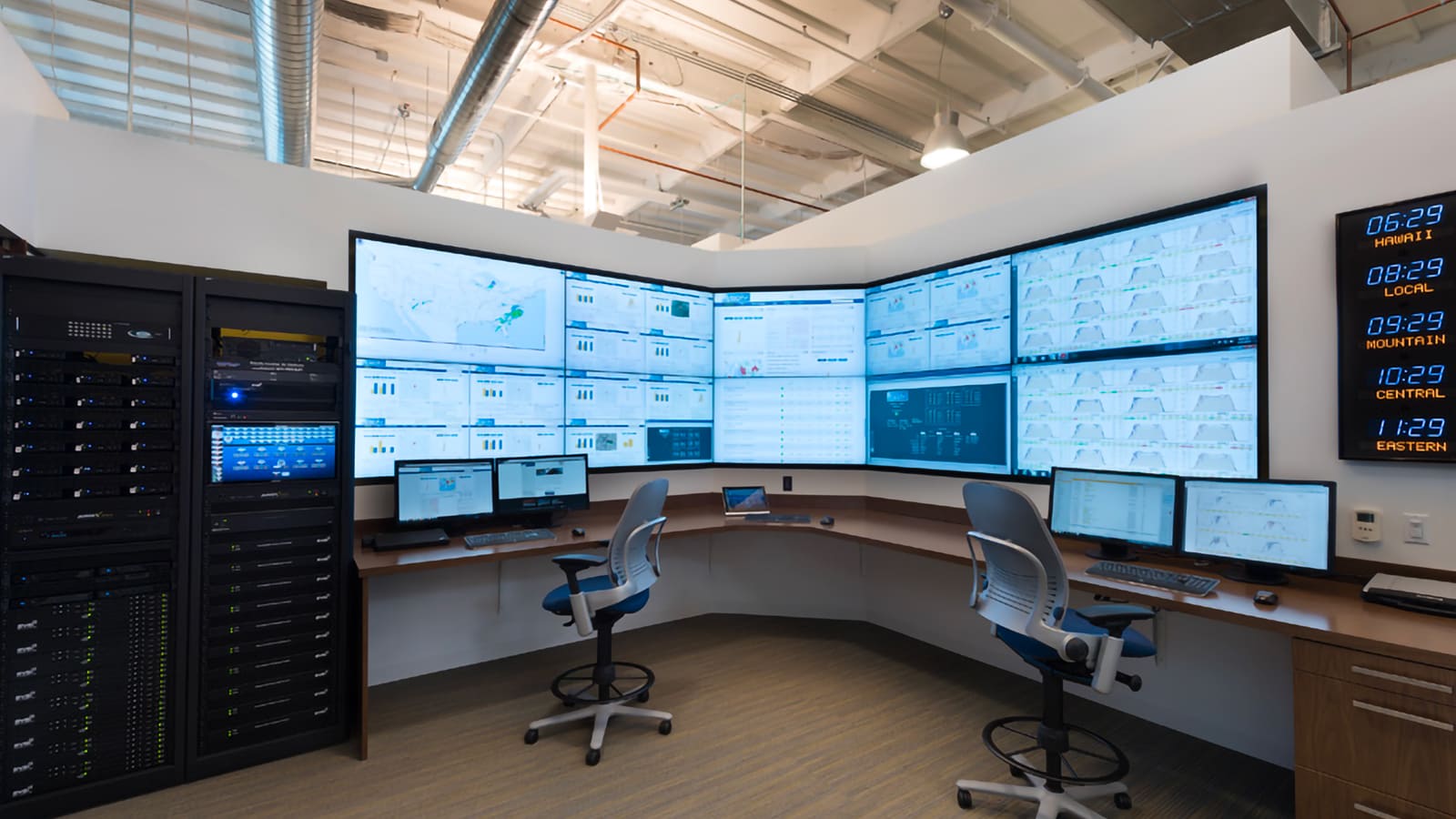
Considering the size and complexity of a power generating plant, it’s easy to understand the value of an Enterprise Asset Management (EAM) system. Whether coal, nuclear, or natural gas powered, they are all enormous facilities filled with many critically important components — and an EAM is key to managing and maintaining the assets. But what about solar power?
As it turns out, EAM also fits well with solar power generation, and SOLV provides a perfect example.
The challenge
SOLV, a division of Swinerton Renewable Energy (based in San Diego, California), is an operations and maintenance (O&M) provider that offers turnkey utility-scale solar power solutions to their customers.
Their expertise in installing and maintaining utility-scale solar has led to a practical knowledge of the importance of proper maintenance.
Utility-scale solar power stations — sometimes called solar parks or solar farms — are large-scale photovoltaic (PV) systems designed to generate electricity from solar energy. They can have millions of solar panels distributed over hundreds of acres and handle enormous electrical voltages.
As SOLV grew in developing and maintaining solar parks, it faced the challenges of a quickly evolving industry. New technologies and shifting trends made it critical for them to stay on top of system maintenance. Collecting and understanding metrics were vital to being an innovative leader.
At first, the company was able to hold their own. But soon, they began to seek a more complete solution.
Adam Snyder, Product Manager at SOLV, explains, “We had started with a simple service ticket platform. It was helpful to track tickets, but difficult to collaborate across a large portfolio. As our organization and portfolio grew, it became apparent a more adaptable and powerful system would be required. A searchable, traceable and scalable platform was what we needed. One that could grow with us, yet easily allow working traditional processes to continue to function.”
The answer was to implement an EAM, which seemed straightforward enough, but in reality presented its own series of challenges.
Snyder continues, “The EAM had to be flexible enough to adapt to our needs, but not cumbersome to use. We evaluated our data and reporting requirements — both immediate and long term — then looked for a system that would best meet those requirements.”
Our solution
SOLV needed something powerful, adaptable, but immediately usable. Dematic Software EAM was the right fit.
After reviewing other offerings and contacting references, the value of Dematic Software proved to be unmatched. Dematic Software provided the level of detailed equipment tracking, reporting and work order management needed to manage current and future facilities.
Adam Snyder, Product Manager at SOLV“The flexibility of Dematic Software is vital to our long-term success.”
Bonus: Seamless integration
In addition, the flexibility and ease of integration with other systems have made Dematic Software even more valuable. Through integration, SOLV generates work orders automatically based on certain types of asset events. When a monitoring system detects an asset failure, it sends a data set that Dematic Software uses to create a new work order. (Technicians no longer need to create work orders manually.) Furthermore, as part of the process, Dematic Software automatically notifies customers and field technicians so the work can be scheduled.
Snyder describes the larger benefit. “As our industry grows, we not only need to become more efficient in what we do, but become smarter in how we do it. A quality EAM with the right integration saves our organization time and allows maximum responsiveness to our customers. Solar is growing quickly, with a lot of change still to come. The flexibility of Dematic Software is vital to our long-term success.”
The results
With Dematic Software, SOLV can manage the maintenance of solar power stations over multiple locations. Customers are informed immediately, consistently and with thorough information. Notifications are sent when work orders are opened, closed or modified, keeping all parties up-to-date with maintenance operations.
Problem reports, resolution documents and field technician notes are easily referenced. Issues can be tracked down to asset level. Detailed searches and lookups provide quick reference to historical issues.
The tracking features of Dematic Software allow SOLV to compare device failures across all of their operations and observe trends not only for specific assets, but also for the time and location of where that work occurs.
“We could perform similar reports in the past,” says Snyder, “but with much manual effort. These reports are now at our fingertips.”
In addition, customers can submit service requests directly for issues that they feel need attention. The SOLV team is notified immediately and can quickly turns these requests into work orders. Customers receive instant email notifications with access to all progress and notes.
Customized reports provide many benefits, including:
- Time saved by automating data entry and collection
- Concise history of work completed, such as across a certain site or for a specific asset
- Consistent access to facility metrics for customers