Adidas Scores Goals and Protects Brand with Automated Distribution Center
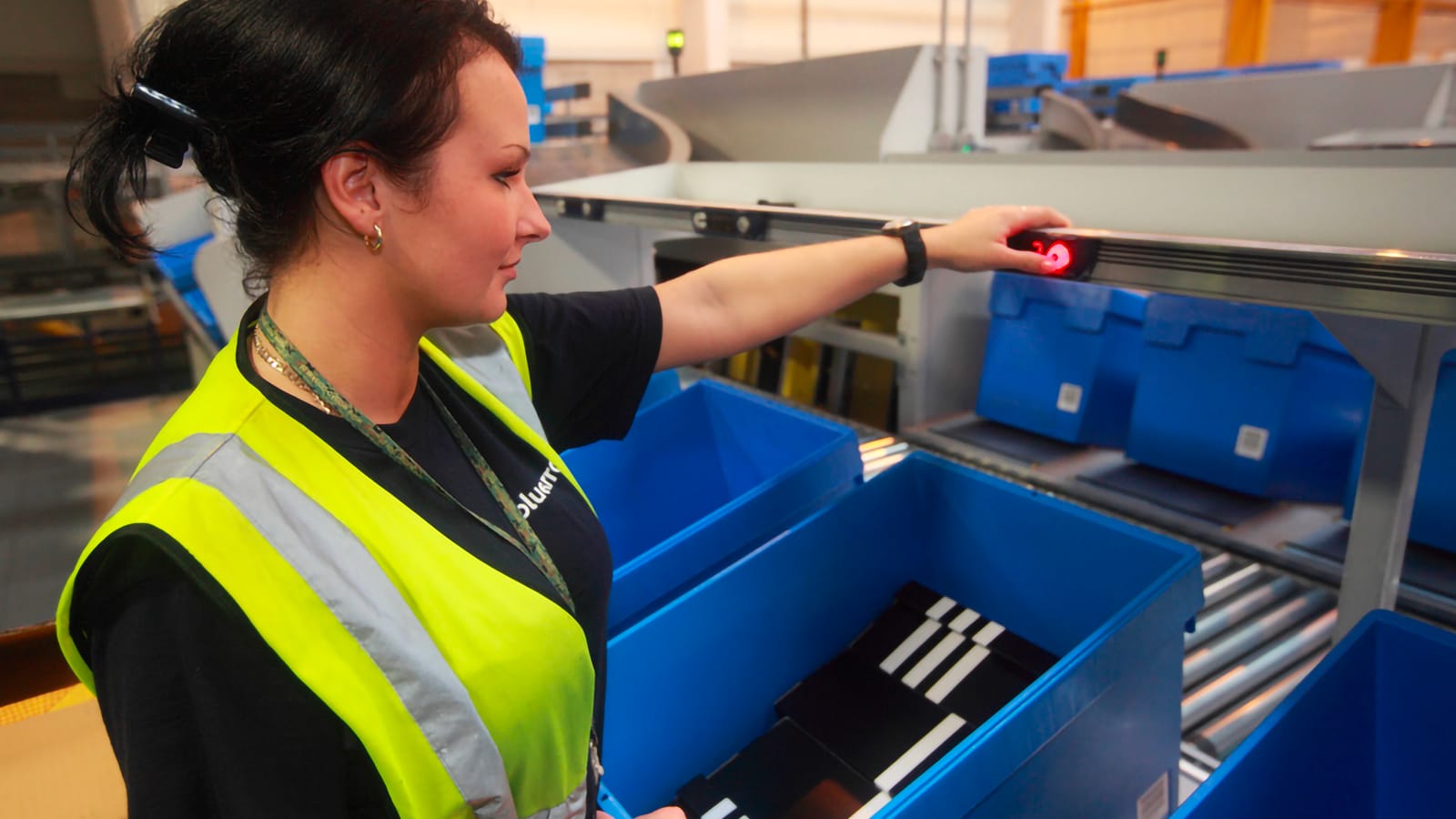
Global sportswear brand adidas faced major challenges in managing rapid growth while consolidating operations in Northern Europe. Working with Dematic and making a prudent investment in their order distribution turned out to be a winning game plan.
The challenge
Efficient and timely distribution of its state-of-the-art sports footwear, apparel and accessories is a critical issue for adidas, with its supply chain having been tested in recent years by the rapid expansion of the business.
In 2006, acquisition of the Reebok brand presented both a challenge and an opportunity to redefine and restructure its European Area North distribution operation, servicing retailers in the UK, Ireland and Benelux.
Analysis of a merged distribution network highlighted the efficiencies to be achieved by consolidating inventory from its five key brands: adidas, Reebok, TaylorMade, Rockport and Ashworth. Four existing conventional warehouses needed to be replaced with a single automated distribution facility in Trafford, Manchester.
New picking strategies for New Trafford
The purpose built 350,000 squarefoot (32,500 square-meter) DC in Manchester was kitted out within 18 months. Dematic worked with adidas to create a dynamic, space and cost-efficient warehouse.
The integrated design features large automated pallet and tote automated storage and retrieval systems (ASRS), together with a highly efficient goods-to-person (GTP) picking system.
Incorporating high rate put stations, they enable the operator to concurrently process up to 24 orders at a time. With pick rates averaging 500 units/hour, and the capacity to process up to 1500 units/hour, adidas can now pick more than 40,000 split case items a day.
Tim Adams, Global Business Solutions Warehousing, adidas Group“Automation allows us to handle a lot of volume in a relatively small amount of space, which keeps overheads down.”
Eliminating pick faces and replenishment
It soon became apparent that the system was easily capable of coping with not only the slow moving goods, but the vast majority of split case goods too, enabling adidas to reduce the area allocated to manual picking by two thirds. “With over 70,000 SKUs, the pick face for a manual operation would have been massive and, given the seasonal nature of our business, we would have been continually changing it — automation improves efficiency three fold,” says Tim Adams, Global Business Solutions Warehousing, adidas Group.
Space efficient storage
The bulk store is a 20,000 pallet location, fully automated high-bay operation equipped with five Dematic pallet cranes. Palletized loads leaving the high-bay are either destined for dispatch or move to one of four stations for carton picking operations.
The fully automated Dematic Miniload store has over 300,000 locations and is accessed by 12 cranes, each equipped with a double-deep load handling device designed to handle four different-sized loads simultaneously. The system can perform an impressive 800 dual cycles per hour.
Tim Adams, Global Business Solutions Warehousing, adidas Group“Automation helps with labor and resource utilization by smoothing out peaks and troughs in demand.”
Automated tote picking
Cases are directed to tote decanting stations and then on to the high rate put stations by Dematic’s DC Director warehouse control system.
Each of the four high rate put stations has 24 ‘put-to’ locations for customer orders, enabling up to 24 individual orders to be processed at a time. The Miniload and integrated conveyor system provide a smooth flow of items to the picking operator in the precise sequence to fulfil order requirements. As totes or cartons arrive at the picking stations, they are elevated into position ready for the operator.
High rate put station operation
A screen provides instructions with a ‘putto-light’ system on each order location identifying which of the 24 order totes to put the item(s).
Completed orders are pushed onto a take-away conveyor and transported to packing stations or, in the case of partially completed orders, are sent to an automated buffer awaiting completion of the order.
To ensure accuracy, every split case item is scanned before packing into a despatch carton at one of the DC’s 22 packing stations.
Directing warehouse control
Control of the automated facility is managed by Dematic iQ software, integrating with adidas’ Manhattan Associates WMS.
“Dematic iQ is a lot simpler to use than other systems I’ve seen,’ said Stuart Jones, Project Manager, Global Warehousing for adidas Group. “Dematic’s software team were most accommodating, easy to work with and very inventive at getting the most out of the system.”
Conclusion
The benefits that have accrued from this 20 million pound investment in automation is now shaping the way adidas is viewing its distribution strategy for Europe and wider markets.
Adidas has seen automation become far more flexible. A range of new possibilities have become available — from the picking of cartons to an individual pair of shoes — which has allowed for much greater accuracy.
DC Statsitics
- Facility Size: 350,000 square-feet
- Pallet Storage: 20,000 locations
- Miniload Storage: 300,000 locations
- Stock Keeping Units: 70,000+
- Packing Stations: 22