Adidas marque des buts et protège sa marque grâce à un centre de distribution automatisé
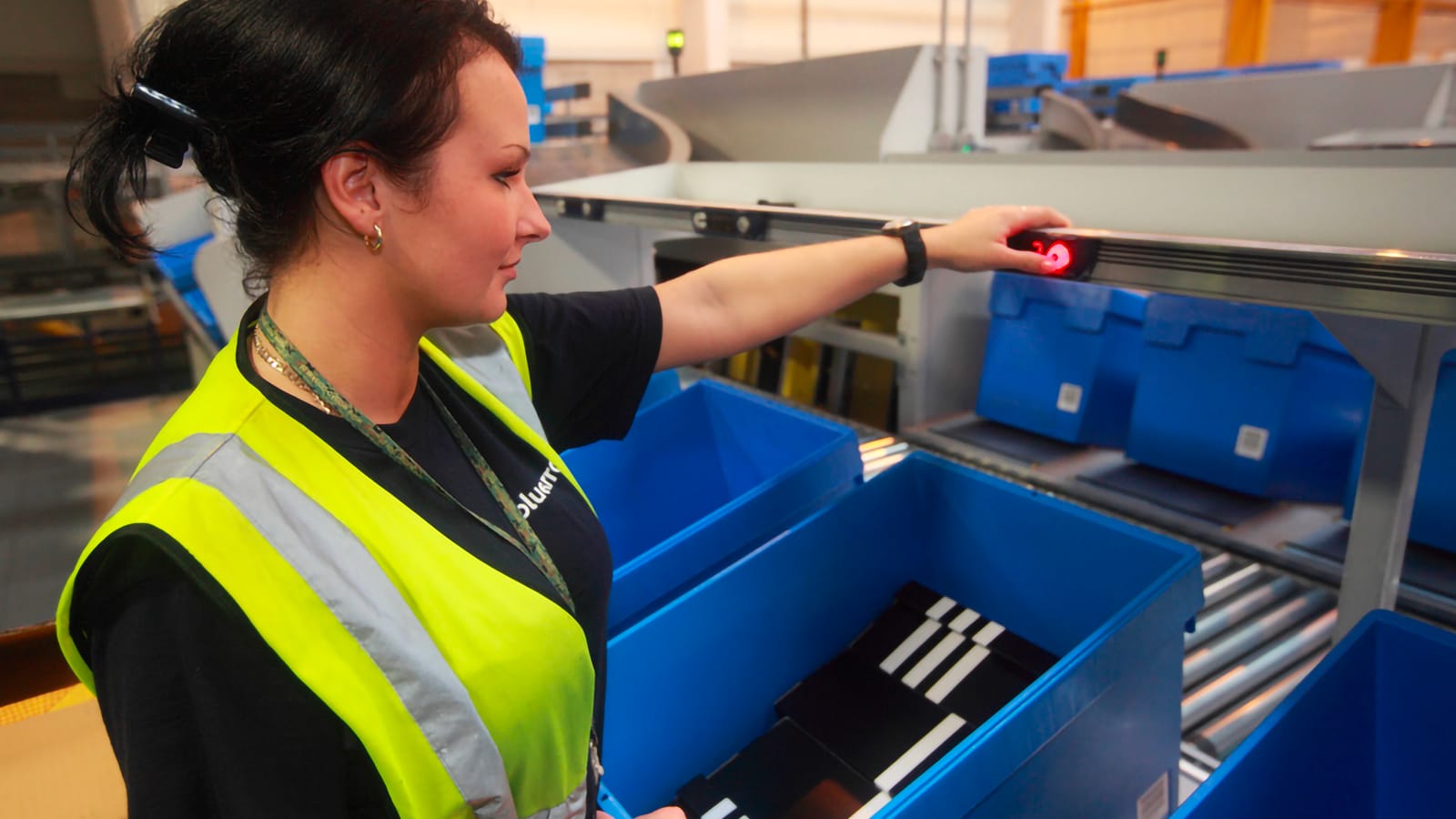
La marque mondiale de vêtements de sport adidas s’est heurté à des défis majeurs pour gérer une croissance rapide tout en consolidant ses opérations en Europe du Nord. Grâce à sa collaboration avec Dematic et à un investissement prudent dans la distribution des commandes, son pari s’est avéré gagnant.
Le défi
La distribution efficace et en temps voulu de ses chaussures, vêtements et accessoires de sport de pointe est une question primordiale pour adidas, dont la chaîne d’approvisionnement a été mise à rude épreuve ces dernières années par l’expansion rapide de l’entreprise.
En 2006, l’acquisition de la marque Reebok a été un véritable défi, mais aussi l’occasion de redéfinir et de restructurer ses activités de distribution dans la zone Europe du Nord, au service des détaillants du Royaume-Uni, de l’Irlande et du Benelux.
L’analyse de la fusion du réseau de distribution a mis en évidence les gains d’efficacité à réaliser en consolidant les stocks de ses cinq marques clés : adidas, Reebok, TaylorMade, Rockport et Ashworth. Quatre entrepôts conventionnels existants devaient être remplacés par une seule installation de distribution automatisée à Trafford, Manchester.
De nouvelles stratégies de prélèvement pour New Trafford
Le centre de distribution de Manchester, construit sur mesure et d’une superficie de 32 500 m², a été équipé en 18 mois. Dematic a collaboré avec adidas pour créer un entrepôt dynamique, spacieux et rentable.
La conception intégrée comprend de grands systèmes automatisés de stockage et de récupération de palettes et de sacs, ainsi qu’un système de préparation de commandes de type « goods-to-person » (GTP) très efficace.
Grâce à des stations de dépose à haute cadence, ils permettent à l’opérateur de traiter simultanément jusqu’à 24 commandes. Avec des taux de préparation de 500 unités/heure en moyenne, et la capacité de traiter jusqu’à 1 500 unités/heure, adidas peut désormais préparer plus de 40 000 articles en caisses séparées par jour.
Tim Adams, Global Business Solutions Warehousing, Adidas Group« L’automatisation nous permet de traiter un volume important dans un espace relativement réduit, ce qui permet de maintenir les frais généraux à un niveau bas. »
Élimination du prélèvement en façade faces de préparation et du réapprovisionnement
Il s’est rapidement avéré que le système était capable de gérer non seulement les marchandises à faible rotation, mais aussi la grande majorité des marchandises en caisses séparées, ce qui a permis à adidas de réduire de deux tiers la surface allouée à la préparation manuelle des commandes. « Avec plus de 70 000 UGS, la face de préparation d’une opération manuelle aurait été énorme et, étant donné la nature saisonnière de notre activité, nous l’aurions continuellement modifiée – l’automatisation permet de tripler l’efficacité », explique Tim Adams, Global Business Solutions Warehousing, adidas Group.
Rangement efficace de l’espace
Le magasin de vrac est un entrepôt de 20 000 palettes, entièrement automatisé et équipé de cinq transpalettes Dematic. Les charges palettisées qui quittent le grand hall sont soit destinées à l’expédition, soit dirigées vers l’une des quatre stations en vue des opérations de préparation des cartons.
Le magasin entièrement automatisé Dematic Miniload compte plus de 300 000 emplacements et est accessible par 12 grues, chacune équipée d’un dispositif de manutention de charges à double profondeur conçu pour manipuler simultanément quatre charges de tailles différentes. Le système peut effectuer un nombre impressionnant de 800 cycles doubles par heure.
Tim Adams, Global Business Solutions Warehousing, Adidas Group« L’automatisation contribue à l’utilisation de la main-d’œuvre et des ressources en atténuant les pics et les creux de la demande. »
Préparation automatisée de sacs
Le système de contrôle d’entrepôt Dematic DC Director dirige les caisses vers les stations de décantation des conteneurs, puis vers les stations de dépose à haute cadence.
Chacune des quatre stations de dépose à haute cadence dispose de 24 emplacements de dépose pour les commandes des clients, permettant ainsi de traiter jusqu’à 24 commandes individuelles à la fois. Le Miniload et le système de convoyage intégré fournissent un flux régulier d’articles à l’opérateur de préparation de commandes, dans l’ordre précis pour répondre aux exigences de la commande. Lorsque les bacs ou les cartons arrivent aux stations de préparation, ils sont élevés et mis en position, à la disposition de l’opérateur.
Fonctionnement de la station de dépose à haute cadence
Un écran fournit des instructions avec un système « Pick-To-Light » sur chaque emplacement de commande, indiquant parmi les 24 sacs de commande celui qui doit être placé.
Les commandes terminées sont poussées sur un convoyeur d’enlèvement et transportées vers les stations d’emballage ou, dans le cas de commandes partiellement terminées, sont envoyées vers un tampon automatisé en attendant que la commande soit terminée.
Pour garantir l’exactitude des données, chaque article en caisse séparée est scanné avant d’être emballé dans un carton d’expédition à l’un des 22 postes d’emballage du centre.
Gestion du contrôle de l’entrepôt
Le contrôle de l’installation automatisée est géré par le logiciel Dematic iQ, qui s’intègre au WMS Manhattan Associates d’adidas.
« Dematic iQ est beaucoup plus simple à utiliser que les autres systèmes que j’ai vus », a déclaré Stuart Jones, chef de projet, Global Warehousing pour adidas Group. « L’équipe logicielle de Dematic a été très flexible, facile à travailler et très ingénieuse pour tirer le meilleur du système. »
Conclusion
Les avantages qui ont découlé de cet investissement de 20 millions de livres dans l’automatisation conditionnent désormais la manière dont adidas envisage sa stratégie de distribution pour l’Europe et les marchés plus larges.
Adidas considère que l’automatisation est devenue beaucoup plus flexible. Une série de nouvelles améliorations sont disponibles – de la préparation de cartons à une paire de chaussures individuelle – ce qui a permis une précision beaucoup plus grande.
Statsitiques du centre de distribution
- Taille de l’installation : 32 500 m²
- Stockage de palettes : 20 000 emplacements
- Stockage Miniload : 300 000 emplacements
- Unité de gestion des stocks : plus de 70 000
- Postes d’emballage : 22