Conveyor Systems Maintenance
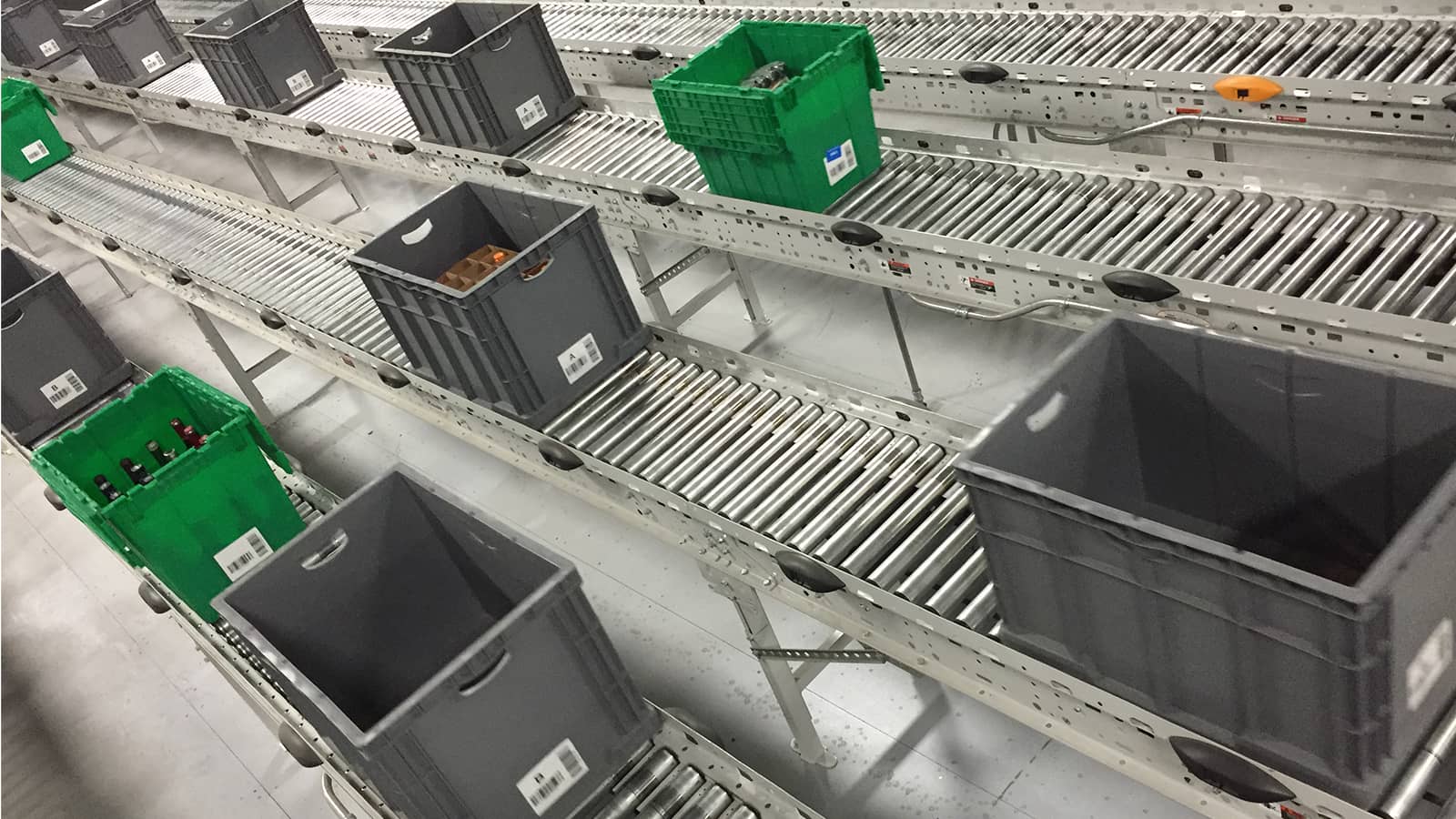
Supporting your operating plan
Whether the conveyor system you implement is a small “point” solution or a fully integrated receiving-to-shipping solution, Dematic supports your operating plan for the long term. To make conveyor maintenance effective, Dematic offers multiple services and products such as Asset Management software, SiteView technical support app, online and on-site conveyor maintenance training courses, resident maintenance program and the Dematic University mobile training unit.
Asset management software
Dematic Asset Management software delivers a streamlined solution for effectively managing and scheduling maintenance activities and resources. It also includes spare part inventory management and automatic parts re-ordering. By automating maintenance processes, conveyor system users can increase productivity, reduce labor requirements, and reduce operating costs by allowing technicians to focus on completing the work on the floor rather than managing it in a complicated work order system. Key attributes include:
- Automatic scheduling of preventive maintenance activities
- Dispatch work orders to technicians, add time and parts used, print invoices and close with less down time
- Automatic routing of work to specific individuals based on work order types or technician skillset
- Email notifications for different stages of the work order cycle
- Work order cost summary including labor time and replacement parts used
- Analytics and reporting to provide visibility and insight to maintenance operations
SiteView
If you are experiencing an issue with your conveyor system, you need to get it back online fast. With Dematic SiteView app, you can. Dematic SiteView is an app that lets you stream live video and audio from your mobile device. An experienced Dematic technician sees what you see and hears you describe the issue. You get 24/7 remote support from technicians and engineers who are specially trained to support automated material handling systems.
Maintenance training videos and eLearning
Dematic conveyor maintenance training includes mechanical and controls instruction for the staff that maintains and operates Dematic conveyor systems. It consists of technical classes about specific maintenance procedures and practices as well as explanations, definitions and “how to” instructions. Most of classes are designed for the maintenance staff that require the specialized knowledge and skills necessary to ensure high system uptime, operational effectiveness, and cost efficiency. The key attributes of conveyor system maintenance training program include:
- Maximize system uptime & minimize time to repair.
- Improve overall operational effectiveness while reducing cost to maintain.
- Increase skills, expertise & competency of maintenance staff.
- Introduce new diagnostics & repair techniques.
- Accommodate need for new employee training.
- Minimize reactive breakdown repair by implementing preventive strategies.
- Obtain understanding of asset management software to streamline maintenance
eLearning
Online remote
Comprehensive course catalog of eLearning classes for maintenance staff that prefer to go at their own pace, time and location. Also used prior to and after taking an instructor-led class.
Open Enrollment
Training center
Instructor-led classroom and hands-on instruction in the Dematic Training Center. Offered as open enrollment with participants from multiple customers. Classes scheduled throughout the year.
Private
Onsite user's facility
Instructor-led training at your facility. It consists of classroom training and at-the-equipment-instruction in your operation. Dematic Mobile Training Unit can be brought to your site.
Custom
Special configuration
Customized and advanced training classes configured for your specific requirements and location preference.
Mobile training unit
The Dematic Mobile Training Unit is a technical training center on wheels. It consists of a long-haul truck/trailer that transports modules of convey and sort technology to customer sites to facilitate maintenance training.
The Mobile Training Unit is configured to support mechanical and controls training for maintenance and operations staff.
The training service occurs at the customer site, typically a warehouse or distribution center. This training center on wheels could be staged at other locations, such as corporate offices, regional offices or a hotel.
The conveyor modules are portable and designed to be moved into the user’s facility so training can take place in the customer’s environment. Each conveyor module is mounted on wheels for easy and fast transport in/out of the truck trailer.
Resident maintenance
If the plan is to concentrate your resources on operations, Resident Maintenance may be an option for consideration.
Dematic Resident Maintenance program provides daily on-site service support for conveyor systems and other material handling automation. The goal of Resident Maintenance is to proactively identify and repair potential component and system failures, reduce the risk of downtime, lower system operating costs, and assure improved overall system performance. On site Dematic technicians inspect, test, lubricate, repair, adjust and replace components as required. Worn or malfunctioning components are replaced. Emergency repairs are done quickly and efficiently by the Dematic Resident Maintenance staff.
Resident Maintenance Responsibilities:
- Preventive & routine maintenance
- Spare parts management
- Emergency repairs
- Monitoring & reporting
- Operational support
Ensure conveyor system operational excellence
Ongoing conveyor system maintenance support means maximum uptime and high system performance levels. When the system is operating at full capacity during peak periods, it will operate reliably with predictable results.