Dematic delivers AutoStore™ system to manufacturer for building communication, Siedle
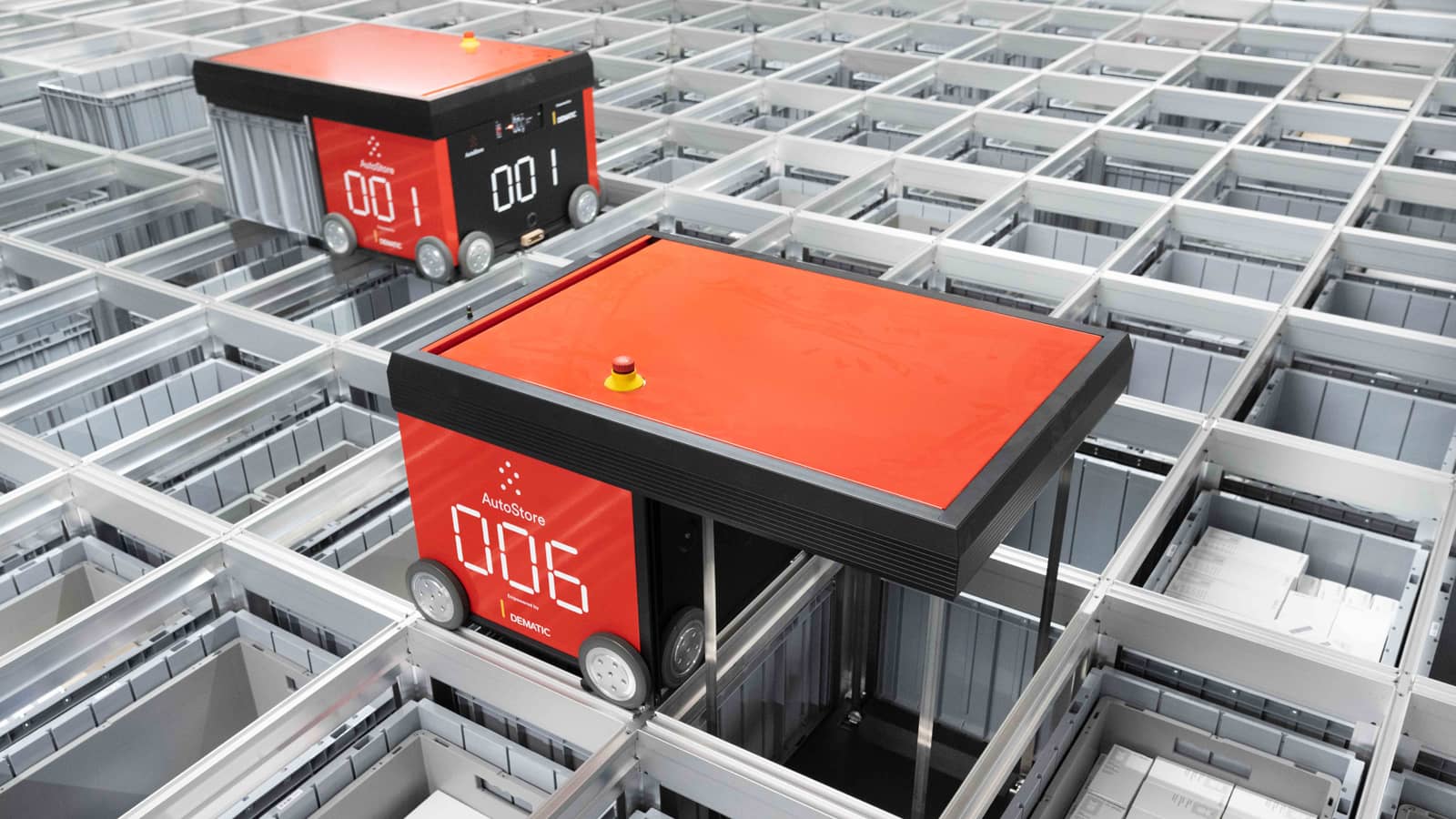
A connection to the future
From video intercoms at the entrance to mobile door opening with a mobile phone to completely networked communication systems: developments in building technology are increasingly moving in the direction of smart homes. According to current forecasts, the number of living areas with such systems in Germany will increase to around 17 million by 2025. One of Europe‘s leading manufacturers of building communication technology is S. Siedle & Söhne Telefon- und Telegrafenwerke OHG.
Christoph Weber, Managing Director Technology at Siedle“We were focused on optimizing our internal processes, which we also achieved with the project. We therefore thank Dematic for a very good cooperation.”
About the customer
S. Siedle & Söhne Telefon- und Telegrafenwerke OHG is one of the leading manufacturers of building communication technology in Germany and Europe. The company is based in Furtwangen in the Black Forest. The company has grown from a pioneer in the field of door intercom systems to an innovative leader in building communication whose systems are used all over the world — in small and large residential buildings, in companies, clinics, concert halls and museums.
The challenge
In order to make the development and production site in Furtwangen in the Black Forest fit for the future, the company commissioned the intralogistics specialist Dematic to automate the warehouse and order picking. Dematic installed an AutoStore system to replace the previous automated small parts system, a miniload. With the compact eaches picking system, Siedle is streamlining and accelerating processes in logistics and production. In addition, the existing material flow computer in the pallet warehouse was replaced and the Dematic module SubSuite was used to control all automatic system components of the pallet warehouse in SAP. As a result, the system will comply with the company’s “lean production” approach in future and the IT landscape at Siedle has been significantly simplified.
Over the past decades, Siedle has developed from a pioneer in door intercom systems to an innovation leader in building communication. The technology of the seventh generation of the family-run company is used worldwide in homes, companies, clinics, concert halls and museums. As a result, Siedle achieved consolidated sales of 88 million euros in 2018 and employs 550 people. Despite its constant growth, the company has remained true to its roots and has been producing at the same location for 270 years: in Furtwangen in the Black Forest.
“Our aim is to keep as many processing steps as possible in-house. We still achieve more than 80% of the added value in-house,” explains Christoph Weber, Managing Director Technology at Siedle. This is an important prerequisite for continuous quality assurance, short transport routes and rapid availability.
Siedle therefore regularly invests in the production site in order to make manufacturing in Furtwangen future-proof in the long term. In order for the manufacturer of building communication to be able to meet the increasing demands of customers and the reliability and performance of the warehouse, modernization of the processes and technologies had become urgently necessary. “Our miniload system was more than 25 years old and was also reaching spatial capacity limits,” explains Weber. “Further growth and an accompanying increase in the number of accesses could no longer be achieved efficiently and reliably, so we needed a new solution — ideally without major structural changes and with moderate investments.”
Technical data
- Floor space of the AutoStore facility: 480 square meters
- 12,500 totes
- 7 robots
- 3 order picking ports
- SAP connection with Dematic SubSuite
Space-saving system
Siedle has been using storage and retrieval units and conveyor technology from Dematic for several years. Due to the given requirements, Dematic suggested the installation of an AutoStore system. One of the greatest advantages of the compact unit load picking system is the compressed storage option. Due to the compact design, Siedle would also not have to expand its logistics center. Rather, AutoStore adapts to the spatial conditions on site.
At Siedle’s request, this recommendation was checked again by io-consultants GmbH & Co. KG and also confirmed. The technical consulting and planning company then drew up the tender documents, in the process of which the Dematic proved itself. “In the end, the proposal proved to be spot on. Besides the performance and the space-saving design, we were particularly convinced by the possibility of being able to adapt the system to future business developments without much effort,” Weber recalls.
In the run-up to the installation, io-consultants assisted with a comprehensive modernization concept and with support during the realization phase. Thanks to precise planning, Siedle put the system into operation in just a few months.
Uniform IT landscape
At Siedle, the system automates both storage and order picking of products and components, which are either delivered directly to customers or processed further in the company’s own production facilities. The articles are stored in a storage block consisting of 12,500 containers. The facility takes up a mere 480 square meters. Seven robots travel on the surface, automatically accessing any container when the goods it contains are requested. They then transport them independently to the workstations where the items are picked and distributed for further processing in production or delivered to the customer. “With the installation of the AutoStore system, we are significantly streamlining and accelerating the processes in logistics and production,” Weber sums up.
In addition, the high reliability is convincing: if a robot fails, another one takes over its job in the shortest possible time. And last but not least, the new AutoStore system is also optimally scalable: “If necessary, it can be expanded at any time, for example with additional robots and ports,” says Weber.
The AutoStore system is controlled and operated automatically via the SAP WM warehouse management software. To map all functions, the Dematic SubSuite module was added. The solution is a template developed by Dematic for controlling the material flow and control center activities, which is fully integrated into SAP WM. All relevant data from the miniload and pallet warehouse automatically flow together in one system and ensure smooth operations.
“In this way, we are standardizing our IT landscape. This is a decisive advantage for ongoing operations and the associated data evaluation,” says Weber. The software also takes care of sequencing the order picking. For this purpose, it groups individual articles, assigns them a picking location and initiates the automatic transport of the totes to the workstations.
The control of the processes is integrated directly into Siedle’s SAP system, eliminating the need for interfaces to external systems. “The SAP system is always in charge. This integration gives us complete transparency in one and the same platform,” says the Managing Director.
Equipped for the future
By investing in the AutoStore system, Siedle has made its production site in Furtwangen economically and technically future-proof for the coming years. “In the process, the cooperation was characterized by fair dealings, clear communication and targeted implementation,” summarizes Weber.
And the AutoStore system is also equipped for further company growth. Dematic already took precautions during the installation to put three more order picking ports into operation at short notice, if necessary. In addition, ten more robots are to be added in the next expansion stage by 2025 while the system is in operation. “We were focused on optimizing our internal processes, which we have achieved with the project. We therefore thank Dematic for a very good cooperation,” he says.
Customer benefits
- AutoStore systems can be implemented in existing facilities
- More storage space in a smaller area
- 98% less system disruptions
- 20% increase in picking efficiency
- Improved picking dialogues
- 30% reduction in error rate
- Increased flexibility through scalable performance and modular design
- Unified IT landscape