Solution spécialisée pour la préparation automatique des commandes de fruits et légumes frais
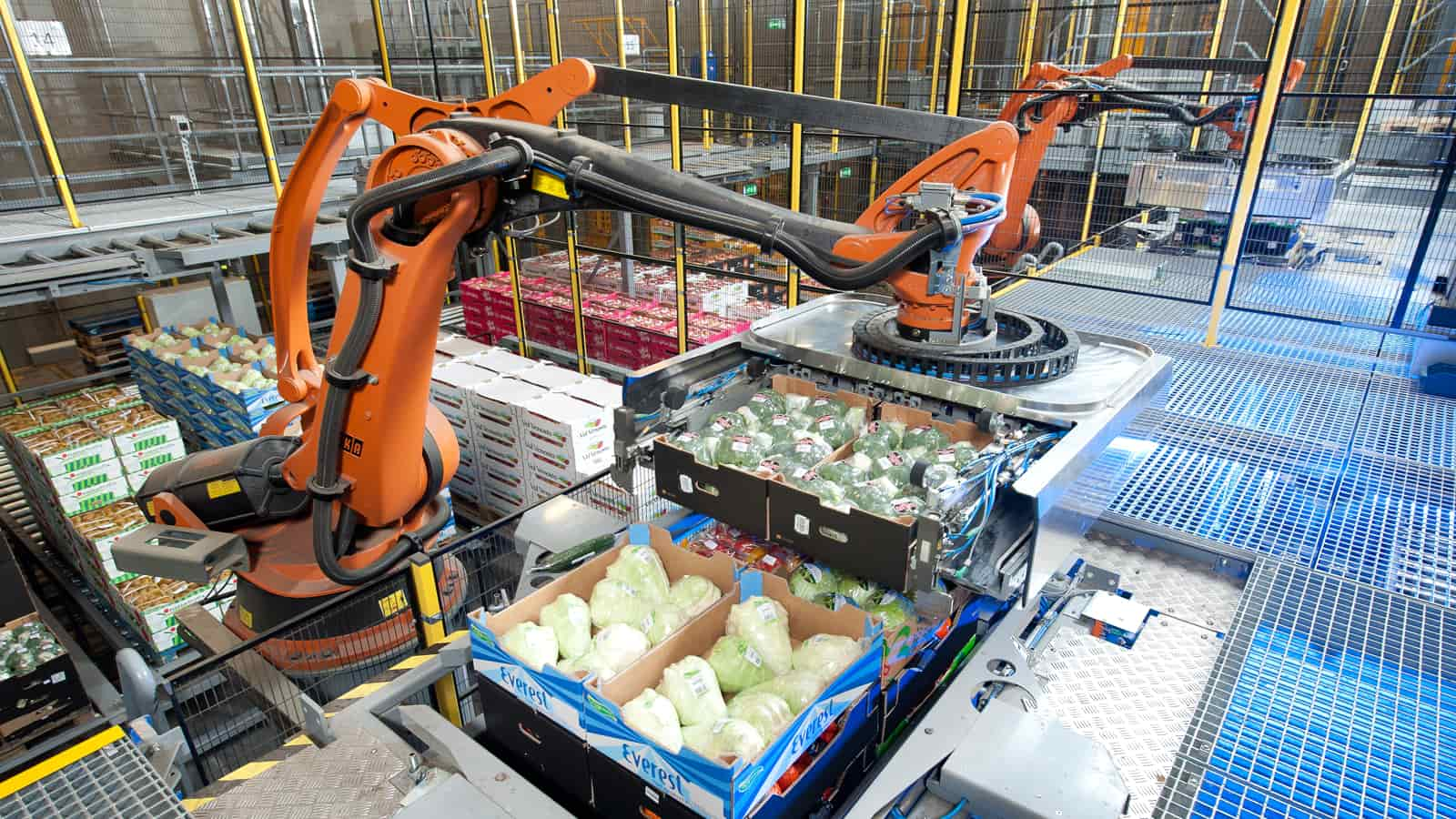
Netto – Køge, Danemark - Pour la chaîne de supermarchés danoise Netto, Dematic a intégré une conception de système unique utilisant des composants de technologie logistique entièrement nouveaux et des robots haute performance pour la palettisation automatique, en magasin, des caisses et cartons de fruits et légumes : Une manutention à une touche qui protège les marchandises, génère une productivité élevée et permet un amortissement rapide. La conception innovante crée une solution spécialisée pour la manutention automatique des produits frais.
Structure de la commande
Pour le centre de distribution central de Netto, Dematic a mis en œuvre une solution innovante pour la préparation de commandes et la palettisation automatiques de fruits et légumes à Køge, au Danemark, à une trentaine de kilomètres au sud de Copenhague. Plus de 70 % des palettes de commande sont désormais préparées et emballées de manière entièrement automatique grâce à cette nouvelle solution dans l'entrepôt central de manutention des produits frais de la chaîne de supermarchés danoise.
Dematic, en tant qu'entrepreneur général, a équipé le nouvel entrepôt Netto d'innovations technologiques (basées sur les dernières technologies robotiques et de nouveaux composants de flux de matériaux) et d'un contrôle intégré et intelligent du flux de matériaux.
Portée du service et de la fourniture :
- Intégration de robots palettiseurs à haute performance avec des systèmes de préhension spéciaux pour la préparation et l'emballage entièrement automatiques des palettes
- Systèmes de convoyage
- Zone de préparation manuelle par commande vocale
- Logiciel Dematic iQ
- Contrat de service pour les résidents
Les défis
Depuis la mise en place des centres de distribution en 2003, Netto était à la recherche d'une solution qui, avec un minimum de manutention de marchandises, permettait des niveaux élevés de rendement et d'automatisation.
Dans le secteur des produits frais du commerce alimentaire, une chaîne d'approvisionnement efficace et un traitement unique sont les principaux objectifs. Les exigences de l'autorité danoise chargée de l'environnement de travail concernant le levage quotidien ont initié le processus de ce projet. Ce concept représente des défis particuliers pour l'intralogistique. En effet, l'automatisation des processus (une méthode éprouvée de manutention des caisses/cartons) n'était pas envisageable compte tenu de la nature délicate des marchandises.
Cibles
- Performance et rendement plus élevés
- Manipulation automatique de produits frais
- Des processus de manutention rapides et optimisés
- Délai d'exécution rapide
- Respect des règles de sécurité locales
Données techniques
- 15 cellules de palettisation robotisées
- Manipulation de cartons, caisses et boîtes
- Préparation de 75 groupes de produits en même temps
- Jusqu'à 28 emballages différents par palette
- Préparations robotisées/jour : environ 75 UGS
- Préparations manuelles/jour : environ 50 UGS
- Temps de traitement des commandes : moins de 30 minutes
La solution
Le centre de manutention des produits frais de Netto est l'un des centres logistiques à la fine pointe de la technologie au Danemark. Dans le même temps, le Danemark dispose de l'une des réglementations les plus strictes en matière de sécurité au travail. Elle réglemente, entre autres, le poids total qu'un employé peut soulever par poste et la hauteur à laquelle il peut accéder aux marchandises. Les tables élévatrices à ciseaux utilisées pour lever et abaisser les palettes sont donc une caractéristique typique des centres logistiques danois. Dans le cas des fruits et légumes en particulier, cela signifie qu'il est difficile de changer quoi que ce soit. Les marchandises délicates doivent être emballées manuellement.
La nouvelle solution intégrée de Dematic est cependant différente. Dematic a initialement conçu les flux de marchandises pour trois types d'unités de manutention :
- Boîtes à bananes
- Fruits et légumes dans des caisses en plastique ouvertes
- Boîtes en carton avec base 600 x 400 mm
- Tous sont livrés sur des palettes chargées jusqu'à 2,30 mètres de haut chaque jour dans le centre de distribution de produits frais de Køge. Des portes de chargement spécifiques sont attribuées aux fournisseurs en collaboration entre le système de gestion d'entrepôt (WMS) utilisé à Netto et le système de contrôle d'entrepôt (WCS) installé par Dematic comme interface. Après la mise à quai, les palettes de marchandises entrantes sont transférées sur un convoyeur à rouleaux ou pour être affectées à la zone de préparation manuelle par commande vocale.
Mise en œuvre
Le système de convoyage distribue les palettes de marchandises entrantes sur une ligne de convoyage. Il commence par quatre points de convoyeur d'alimentation qui conduisent les palettes vers l'une des cellules robotisées. Les couloirs du convoyeur sont à la fois des voies d'alimentation et de retour, et chaque couloir ne transporte que des palettes d'un seul produit. Les robots de granulation/dépalettisation fonctionnent dans la cellule robotisée. Lorsque les palettes de marchandises sont introduites dans un côté de la cellule, les robots prennent une ou deux des unités de manutention, selon les paramètres du système informatique. Ainsi, dans une opération, c'est une couche de quart ou de demi-palette que le robot prend et met sur des palettes de commande.
Dans ce processus, le Dematic WCS spécifie les restrictions pour la formation des palettes, telles que la pondération et l'utilisation optimale du volume. Un système séparé de circulation des palettes vides a été installé pour les palettes vides requises. Ce pool est constitué en grande partie des palettes vides de marchandises entrantes positionnées ou retirées par les robots sur le système de circulation. Les pinces sont équipées à cet effet d'un dispositif intégré de levage de palettes.
Quinze de ces cellules robotisées sont installées à Køge, ce qui signifie que 75 groupes de produits peuvent être préparés en même temps. Grâce à la capacité tampon de chaque voie, il n'était pas nécessaire de prévoir des voies de circulation ou de débordement pour le séquençage de l'alimentation. Cela signifie que les commandes peuvent être préparées par lots dans les cellules robotisées positionnées les unes après les autres. Le porte-palettes circule en séquence vers les cellules robotisées requises.
Les palettes sont toujours emballées sur la base d'un maximum de 28 emballages différents – dans le pire des cas, cela signifie quatre arrêts entre la palette vide et la palette d'expédition complétée vers les cellules robotisées. Grâce à la nouvelle technologie unique des têtes de préhension, il est possible de manipuler les trois unités de manutention de base sur les 15 cellules robotisées, la redondance étant assurée par le placement de dispositifs de déplacement rapide sur un plus grand nombre de cellules robotisées.
Le WCS contrôle les livraisons de marchandises entrantes et la palettisation en magasin sur les 15 cellules robotisées et donne un itinéraire optimisé sur la ligne de convoyage.
Les palettes de magasin préparées automatiquement dans les cellules robotisées sont finalement retirées automatiquement dans les systèmes de guidage d'empilage des palettes par l'intermédiaire de l'une des deux voies à rouleaux entraînés reliées en plusieurs points dans le sens de la manutention des marchandises sortantes. Dans ce processus, la ligne de convoyage à double voie est utilisée à la fois pour le chargement et le déchargement des cellules robotisées. Les palettes de marchandises entrantes vidées sont saisies par les bras du robot et transférées vers la ligne de convoyage des palettes vides pour une utilisation continue.
Le dernier point fort de la conception innovante du système est le système de manutention des marchandises sortantes. Il est situé au deuxième niveau. Ici, les palettes de magasin préparées sont amenées dans leurs guides d'empilage de palettes sur les pistes à rouleaux. Dans une position exacte et prédéfinie sous le système de manutention des marchandises sortantes, l'élévateur pousse les palettes de magasin par le dessous hors des guides d'empilage des palettes et sur le deuxième niveau. Tout cela se fait sous un seul et même emballage.
Dans la mesure où la palette est soulevée et poussée hors du guide d'empilage des palettes, le processus d'enveloppement de la palette avec du film étirable commence automatiquement, de haut en bas. La palette entièrement emballée et sécurisée pour le transport est ensuite dirigée vers la zone des marchandises sortantes.
Innovation
Deux autres caractéristiques spéciales sont importantes dans cette conception exceptionnelle du système :
- La pince combi nouvellement développée sur les robots
- Un système de guidage pour l'empilage et le transport des palettes spécialement conçu à cet effet
L'équipement de préhension est une innovation. Tout d'abord, elle traite les palettes vides. Ensuite, avec ses équipements pneumatiques et mécaniques, il est conçu spécifiquement pour la manipulation des trois unités de manutention clés pour les livraisons délicates de fruits et légumes : Selon les besoins, les pinces innovantes peuvent saisir les cartons et les caisses par le haut, par le bas ou par pression latérale. Il s'agit d'une conception de système unique à ce jour. La deuxième innovation clé est le système de guidage pour l'empilage des palettes, développé spécialement pour ce concept. Il est utilisé à la fois pour soutenir la formation de palettes stables et pour le flux interne automatique de marchandises en tant que conteneur de transport. Le système de guidage de l'empilement des palettes maintient les palettes de commande pendant la préparation, se déplaçant sur une ligne de convoyeur séparée à double voie installée sous la zone de palettisation. Il est positionné à un endroit précis de la cellule robotisée par rapport aux voies d'entrée des marchandises. Ici, un système de levage maintient et abaisse successivement les palettes lors de leur chargement par les pinces du robot, à la même hauteur pour chaque niveau, jusqu'à ce que les palettes de commande soient entièrement préparées.
Les résultats
Depuis la mise en service du système à Køge, 2 700 palettes de commande contenant des fruits et légumes sont assemblées pour être livrées chaque jour à environ 275 magasins. La solution intégrée innovante de Dematic réduit le temps de traitement des fruits et légumes de sorte que la commande puisse être prête en moins de 30 minutes.
Un autre maximum d'environ 50 UGS est traité par le personnel dans la zone de préparation manuelle des commandes, complété par des palettes de commandes ou le traitement des commandes est finalisé par l'alimentation en paquets individuels. Pour la zone de préparation manuelle, Dematic a fourni une solution vocale fournissant toute la structure de communication et connectée au WMS, et (en plus du matériel informatique tel que les serveurs d'application et de base de données) fournissant l'équipement pour la manutention des opérateurs avec des casques, des scanners, des terminaux de données radio et des PC.
Le logiciel est un autre facteur de réussite de la solution. Les processus opérationnels complexes ne peuvent être optimisés de cette manière que grâce à la gamme d'algorithmes utilisés par le logiciel.
Le système Dematic IT ne se contente pas d'assurer une mise à disposition optimale avec un minimum d'effort pour la préparation de commandes en magasin ou des réglages mémorisés pour un assemblage sûr et stable des palettes. Le logiciel gère aussi automatiquement des palettes vides, calcule en temps réel les priorités de traitement des commandes et plus encore, assure un équilibrage optimal de la charge entre la préparation automatique et la préparation manuelle par profil de commande ou encore fournit aux stations d'étiquetage des brancards les informations nécessaires à l'impression des étiquettes.
Les composants éprouvés de la technologie de convoyage nécessitant peu d'entretien, les dernières technologies pour les processus automatisés et un système informatique puissant conçu pour répondre à toutes les exigences, ainsi qu'un contrat de service résident de deux ans, font que le système Netto est prêt pour l'avenir.
En plus de la rapidité et de l'optimisation des processus de manutention, la conception du système de Dematic a permis à Netto de disposer d'un espace libre supplémentaire pour la préparation des expéditions et laisse également la possibilité d'augmenter encore le nombre de marchandises entrantes et le rendement. Avec le système maintenant installé à Køge, Dematic a mis en œuvre un concept global complet pour la préparation de commandes automatisée en magasin de gammes compilées de fruits et légumes, qui est le seul système de ce type au monde.
Avantages pour le client
- Des palettes de commande contenant des fruits et légumes sont automatiquement assemblées pour être livrées chaque jour aux magasins
- Environ 75 UGS sont traités chaque jour dans les cellules robotisées
- Environ 50 UGS sont manipulées chaque jour par le personnel dans la zone de préparation manuelle des commandes
- Solution intégrée pour la formation automatique et prioritaire de palettes
- Utilisation optimale de la pondération et du volume grâce aux spécifications Dematic WCS pour la formation des palettes
- Temps de traitement des commandes : moins de 30 minutes
- La conception du système de Dematic a permis à Netto de disposer d'un espace libre supplémentaire pour la préparation des expéditions et laisse également la possibilité d'augmenter encore le nombre de marchandises entrantes et le rendement
- Conception, fourniture de composants, innovations et informatique à partir d'une source unique
- Contrat de service de deux ans pour les résidents
- Conception ergonomique conforme aux réglementations danoises en matière de sécurité