Automating the Last Mile in Manufacturing
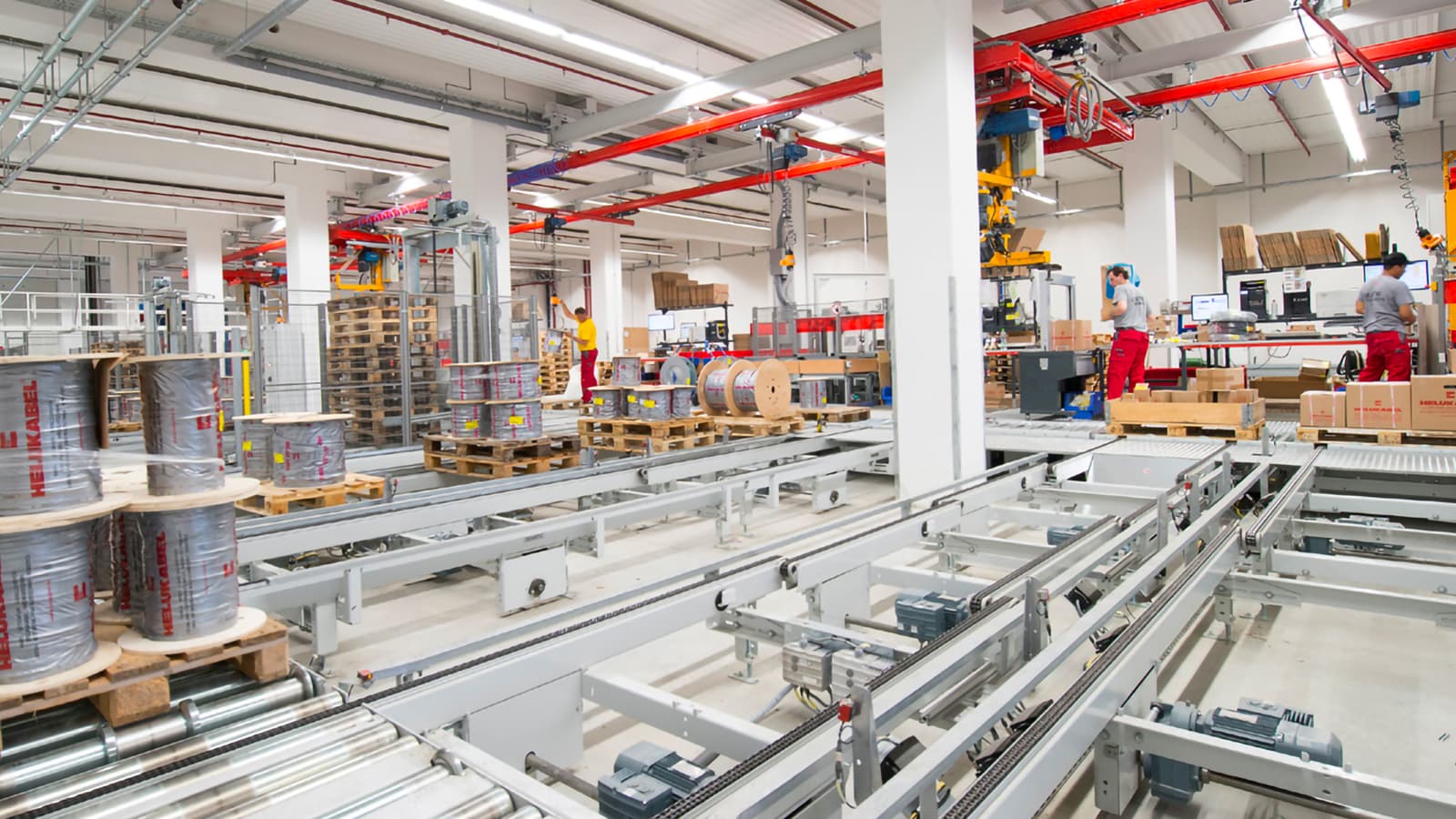
Automation is certainly no stranger to manufacturing. The adoption of the assembly line by Henry Ford transformed the automotive industry. Since then the pace of acceptance has only grown with automation initially taking on simple, repetitive tasks and expanding into more complex challenges. Today, nearly every manufacturing facility contains a fascinating mix of automated machinery that create and package almost everything that we use, touch or consume in our everyday lives.
Most automation in production facilities focus on the manufacturing and packaging of the products. Examples of automation technology include robotics that paint, weld, machine and assemble products, and hard automation to fill, label and package consumer goods such as food and beverages.
Recent trends show companies moving manufacturing closer to their customers, either to control quality, improve customer service or reduce transportation costs. Some are re-shoring (bringing back manufacturing from outside our borders). Other trends in consolidations, mergers and acquisitions are creating an almost constant change in how products are distributed from manufacturing to consumer. In the meantime, demand for labour tightens as the economy grows and the pool of available workers shrinks.
Automation is an obvious answer; the question is, where and how?
Where to look for the last mile of automation?
As supply chains become more complex, some have looked to the “Internet of Things” for solutions. It follows that internal processes would require more connectivity, using smart devices and processes to improve efficiency. Synchronised workflows and predictive analytics become necessary, not only for production planning but also for maintenance. Information flow and Big Data are necessary to create the foundation for future automation.
Software is the start to the last mile of automation, but what else is needed to further enhance an operation? What functional areas must be considered?
Inbound material
Great effort and planning are required to make sure upstream supply chains are healthy. They need to provide not only on-time deliveries, but just as importantly, quality materials. Disruptions to inbound supply chains can quickly grind an operation to a halt.
Even if your inbound supply chain is in good shape, have you thought about how you manage the material once it arrives? Here are some questions to consider:
- Are my materials being handled expediently upon arrival?
- Do I have a good process to check quality and accuracy of the materials and products?
- Do I have good control of my on-hand inventory of raw materials?
- Am I storing material efficiently, using software to manage space, turns and manpower?
- How could I automate raw material receiving and storage?
Managing the flow of material to and through production
After the inbound side of the warehouse is in order, the next area to consider for improvement is the movement of material to production. The following questions can determine whether material is flowing effectively to production.
- Are my workers waiting for material to arrive at their work cells?
- Are the work cells receiving the correct material?
- Is there too much inventory at the work cells?
- Is the material at the work cell correct for the current production schedule?
- Can I create kits more effectively using automation?
Material flow must be accurate, on–time and in many cases dynamic. Inaccurate material, wrong material, cluttered workspaces with too much of the right material for the current job will all slow production.
Moving work-in-process (WIP) material from work cell to work cell can also affect production. When operations within a production facility are not synchronised material can flow unevenly throughout the process. Insufficient material slows production while too much WIP material causes build-up and creates gridlock. Better planning and WIP buffers can improve material flow.
Finally, movement of finished goods at the end of the process can bottleneck an operation. Some questions to consider include:
- Do I have enough dock space to handle my finished goods?
- How quickly can I turn a trailer at a dock?
- Do I have a closed loop between manufacturing and distribution — either a company owned warehouse/DC or 3PL?
- Should I inventory finished goods at the manufacturing site? How much? At what rate?
Speed of production and size of the finished or WIP product will influence your approach to automation. For example, making hundreds of small electronic devices every hour will certainly involve a different set of solutions compared to producing a dozen front-end loaders per day
Potential Solutions for the Last Mile of Automation
Going back to an earlier theme of software as the foundation of the operation: An advanced ERP, MES and sometimes WMS/WES solutions can assist in making operations run smoother — not only from a material flow perspective but also from the labour management side. Several mechatronic solutions can improve the operation and help with the labour shortage issues. Keep in mind that an accurate, thorough data analysis will be required to ensure a complete understanding of the material and data flow of the current operation. This will allow you to assess and apply the proper technology.
Managing the flow of material to and through production
Advance receiving notices help plan for and store incoming material. Planning to store at a pallet, case, tote, or segmented tote level can save space in your warehouse if implemented correctly. Inspection of incoming material and decanting of material into properly sized units of measure also saves space. Unusually shaped items may need to be stored in special racking or fixtures; however, pallets, cases and totes can be stored in automated storage and retrieval systems. These systems can vary:
- Deep-lane or single-deep storage for pallets
- Cases and totes in shuttle systems for high-speed movers
- Mini-loads systems for medium movers
- Carousels or even shelving for slower movers
Kitting Operations
Kitting operations typically use various bills of materials to gather specific parts for sub or final assembly processes. Sometimes the kits ship as orders for maintenance replacement parts. But other than the occasional need for some “value added” functions, kitting is not much different from order fulfilment at a distribution centre. Consequently, automation can be applied using Pick-to-Light, Pick-to-Voice, Goods-to-Person stations and zone routing using conveyor and sortation. The same technology for storing single SKU items can also store finished kits going to production or directly to an end user.
Material flowing to and through production
The speed and size of the material flowing into and through production determines the best automation technology to support kitting:
- Automated Guided Vehicles (AGVs) work best for pallets and larger item handling. Flow can be very dynamic with AGVs given work orders and assignments based on their location and most efficient travel route.
- Automated Tuggers pulling a cart or train of carts are most effective completing “milk runs” when movement is from point to point in a production environment.
- Automated Guided Carts (AGCs) can move materials for Kanban operations and line side deliveries for smaller items like totes and cases.
- Overhead conveyance and monorails can also be effective strategies for material movement. However, these solutions do not provide the flexibility or scalability of the more mobile options.
- Pick-to-Light technology can enhance the speed and accuracy of line-side picking of parts or kits.
WIP Buffers
Pallets, tubs, totes and trays of material can be stored in buffers using automated storage and retrieval (AS/RS) technology. Many operations use mini-load systems to hold and evenly distribute material out to work cells and various processes. This technology can be located directly between two operations or centrally located to service multiple WIP operations.
Finished Goods Handling and Storage
Several solutions are available for end-of-production lines.
- AGVs, pallet conveyor and monorail may be used for transportation of finished goods pallets. Each technology offers advantages based on rate, length of transport and function. AGVs are great for long runs, block stacking of pallets and can even be used for trailer loading. Conveyors are great for shorter runs, tying into other automation such as ASRS and accumulation of pallets at the dock. Monorail works best for higher speed applications and long runs of transportation.
- An AS/RS for finished goods inventory — either adjacent to manufacturing or at a remote DC — can manage receiving and shipping as well as provide accurate, safe, damage-free handling of product. AS/RS technology can also support replenishment for manual or automated case picking. Additional benefits include better usage of space and energy savings.
- For closed loop systems where trailers are moving constantly from manufacturing to a DC, automated trailer loading and unloading can reduce the number of docks and labour to support the docks. In some instances, trailers can be loaded or unloaded in as little as five minutes.
Last mile automation may require creative applications of existing technology or some customisation of equipment and software. However, if implemented correctly, automation can greatly improve a manufacturing operation.