Smart Intralogistics Serve Wide Variety and High Volume
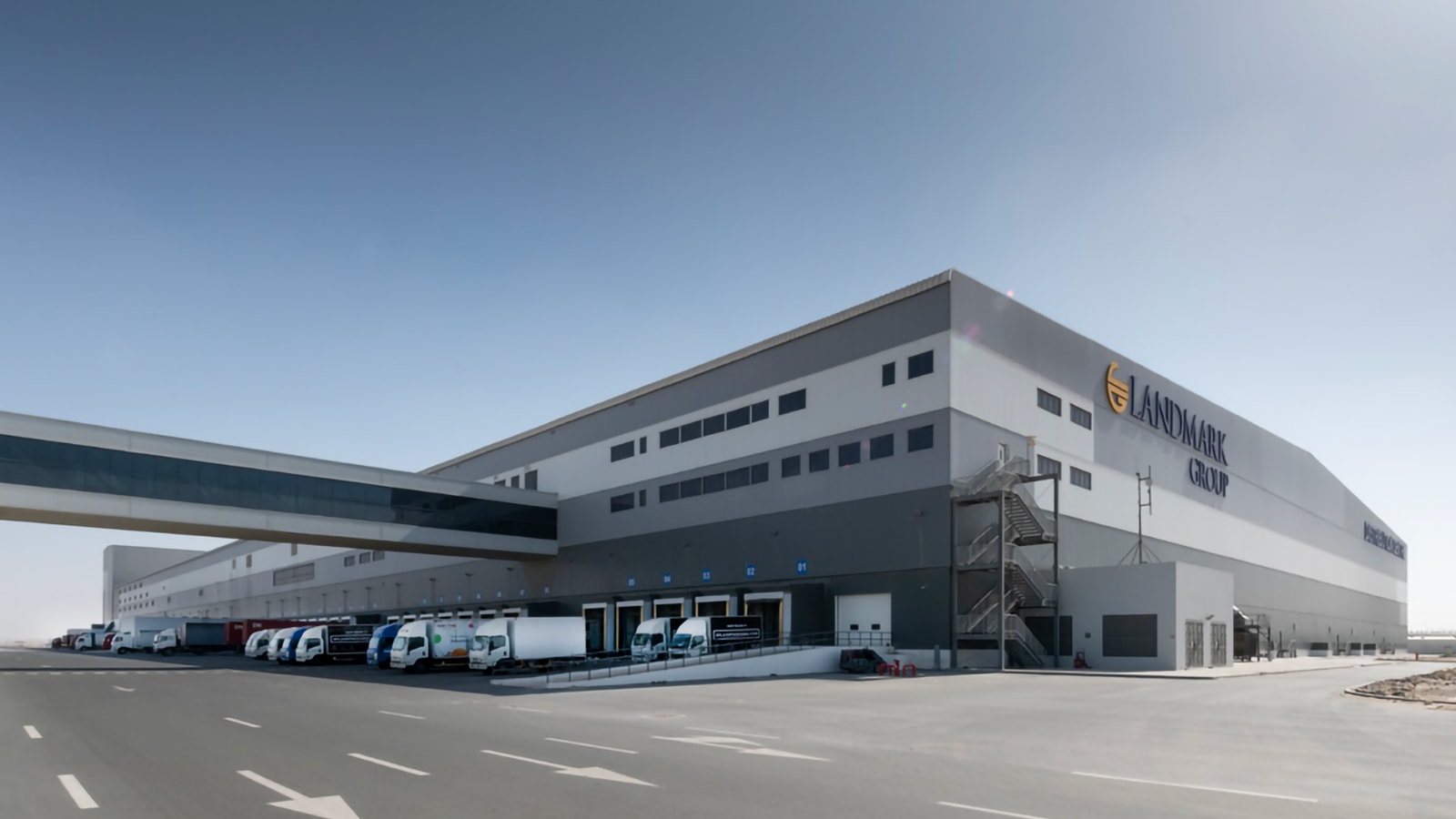
This new distribution center is located in Dubai, UAE, and spans across a plot size of 265,000 square metres. It has a capacity to store and handle up to 2.2 million cartons and 2 million textiles on hangers. Dematic provided the extensive automation technology for this highly modern storage facility, including a pallet highbay warehouse, two Dematic Multishuttle systems, and a garment-on-hanger sorting system. Dematic software controls the systems smoothly and efficiently and provides operation data in real time.
From an initial shop selling baby items in Bahrain in 1973 to a retail empire: In less than 50 years, the Landmark Group has become one of the largest non-food retail groups in the Middle East and India, with a growing presence across South East Asia. The Group has an extensive network of 2,200 plus stores in 21 countries, with a total sales area of over 30 million sqft. Now, with its premier new fully automated distribution center, the company has consolidated the logistics operations of its 5 existing distribution sites.
Even from far away, the Landmark Group’s new distribution center is an imposing sight and symbolic of the entire company history. From a single business in Bahrain, the company has grown to become one of the largest retail chains in the world, while remaining family-owned. As it grew, the Landmark Group began retailing clothing, shoes, accessories, furniture, decorative items, cosmetics, toys, and small goods from its own home-grown brands in the Middle East, as well as from its network of global franchise brands. The new distribution center — is located in the Jebel Ali Free Zone (JAFZA) and close to one of the largest container ports in the world – DP World Jebel Ali Port — centrally consolidates the inventory and supplying regional warehouses in other GCC countries, stores, and end consumers directly.
About the customer
Landmark Group started in 1950 as a children’s clothing store in Bahrain. Since then, the familyowned business has grown to become one of the largest retailers in the Middle East, India and Southeast Asia. The group of companies has an extensive network of 2,200 stores in 21 countries with a total selling space of over 2.7 million square metres.
Customer benefits
- Five distribution sites bundled into one
- Solution from a single source including software and service
- Very high degree of automation allows high throughput rates
- Handling of a very wide range of products
- Faster and more accurate order fulfillment and more satisfied customers
Ashish Sood - Chief Supply Chain Officer, Landmark GroupBased on their deep knowledge and experience in this area, Dematic became the preferred and most suitable partner for us.
- 43 m high pallet high-bay warehouse in silo design with 4 stacker cranes and 36,000 storage spaces
- 10 automatic and 3 manual docks process 74,000 cartons per day
- Dematic Multishuttle as carton buffer with 22 aisles, 33 levels, 580,000 locations and 726 Flex Shuttles
- Dematic Multishuttle as daily buffer with 24 levels, 370,000 storage positions and 528 Static Shuttles
- 60 workstations for the infeed of hanging garments with a throughput of 250,000 pieces / day
- 47 workstations for value added services
- Nearly 150 additional workstations, including 44 goods-to-person picking stations, 27 repacking stations and various control stations
- 11 km of conveyor technology
43 metre tall pallet warehouse in the UAE
By processing more than 75,000 TEU’s annually, the Landmark Group is one of the largest importers of non-food products in the Middle East. As a result, the company places a high value on intralogistics that can handle both a wide variety and high volume. Ashish Sood, Chief Supply Chain Officer of the Group explains the motivations for the gigantic DC project: “With this investment, we wanted to drive both technological progress as well as take on a pioneering position in the region in terms of logistics efficiencies and omnichannel fulfillment.”
As part of the selection process, the Landmark Project Team visited numerous reference projects in Europe to define the exact parameters of the project. “Based on the Dematic team’s deep knowledge and experience in this area, they became the preferred and most suitable partner for us,” says Ashish Sood.
Ashish Sood - Chief Supply Chain Officer, Landmark GroupWith this investment, we wanted to drive both technological progress as well as take on a pioneering position in the region in terms of logistics efficiencies and omni-channel fulfillment.
Dematic delivered a fully integrated solution. What first draws the eye is the 43 metre tall pallet warehouse with up to 36,000 storage places. Moreover, Dematic equipped the high-bay racking with a fire-protection system with an oxygen-reduced atmosphere to store even delicate and highly flammable goods. The climate-regulated pallet high-bay warehouse is the largest in the UAE to date. The support structure of the building including building shell is made up of the shelving system itself. This rack clad silo system guarantees a cost effective and sealed environment within the DC.
Largest Dematic multishuttle of all time
Goods reach the distribution center in boxes in sea freight containers. The DC has capacity to process over 74,000 boxes per day on 10 automatic and 3 manual docks. These boxes are subjected to a laser-controlled contour check and measured precisely up to 1 millimetre. In this way, the system prevents boxes that cannot be gripped optimally from getting into the Multishuttle system.
Items to be processed within days are deposited onto the Multishuttle. Items that are not required in the near term are placed on pallets and stored double-deep in the high-bay warehouse by the 41-metre-high SR-U1500/1 stacker cranes with two telescopic forks.
Individual items are housed in boxes or containers in two Dematic Multishuttle systems with 22 aisles each. On 33 levels, 726 Dematic Shuttles buffer, sort, and sequence items to be used in the next few days in the first system with 580,000 storage places. The daily requirement of a good 370,000 items is retrieved with the help of 528 Dematic Shuttle Static units in the adjacent Dematic Multishuttle on 24 levels. In this way, up to 15,000 totes per hour can be transported to the picking stations. By using a total of 94 lifts as well as shuttles controlled via power rails with very high acceleration and speed performance, one shuttle can operate between 700 and 800 storage spaces.
Dematic‘s patented Inter-Aisle Transfer system maximizes use of space when transferring across aisles as well as storing double-deep. The system is not only the largest that Dematic has installed, it is also the fastest. The Landmark Group is setting new standards with this system, as Ashish Sood reflects: “With the mega distribution center, we have set a logistics benchmark for the entire Middle East.”
Garment on hangar sorting system for 2 million clothing items
The warehouse for textiles on hangers also offers impressive capacities: There is room for up to 2 million clothing items storage in the Dematic Garment-on-Hanger sorting system. Three 20 metre long ironing units with steam generators ensure that items come out of the system ironed for shipment. Items are stored in a software-controlled process so that retailers receive them in an order that most efficiently resupplies their stores and with throughputs of up to 250,000 pieces per day. Sixty workstations feed incoming textiles into the system as carton goods.
An 11 kilometre Dematic conveyor system for containers and pallets and a Dematic sorter connects the systems. “It marks a new era of speed and productivity for our supply chain” summarizes Ashish. Furthermore, 47 workstations for valueadded services including e-commerce are planned for direct customer delivery. The system takes into account individual business or customer requests as well as other volumetric VAS requirements either during goods receipt or when the order is fulfilled.
An additional 150 workstations specified for the respective application complete the overall structure. Of these, 44 are goods-to-person picking stations for order fulfillment, 28 are refilling stations, and the rest are various quality and inspection stations.
The software is critical for smooth, optimal flow of materials at high throughput rates. The Landmark Group has committed itself, as well as its home-grown brands to deliver to stores and end customers within a certain period of time. This is ensured by Dematic software, which combines a warehouse management system (WMS) for stock management, with a warehouse control system (WCS) and a material flow controller (MFC) and dynamically repositions all items throughout the facility.
System availability and future plans
According to Ashish Sood, choosing a hybrid servicing facility with combination of on-site & 24/7 remote service plan has worked well for their business. By following its guiding principle of “Always look ahead and build today to achieve tomorrow, the Landmark Group has set a course that will continue to improve its services and expand its capabilities.”
360-degree panoramas
Take a look at the 360-degree panoramas at Landmark to capture the full scale diversity of the Dematic installation.