Benefits of Automated Mixed Case Palletizing
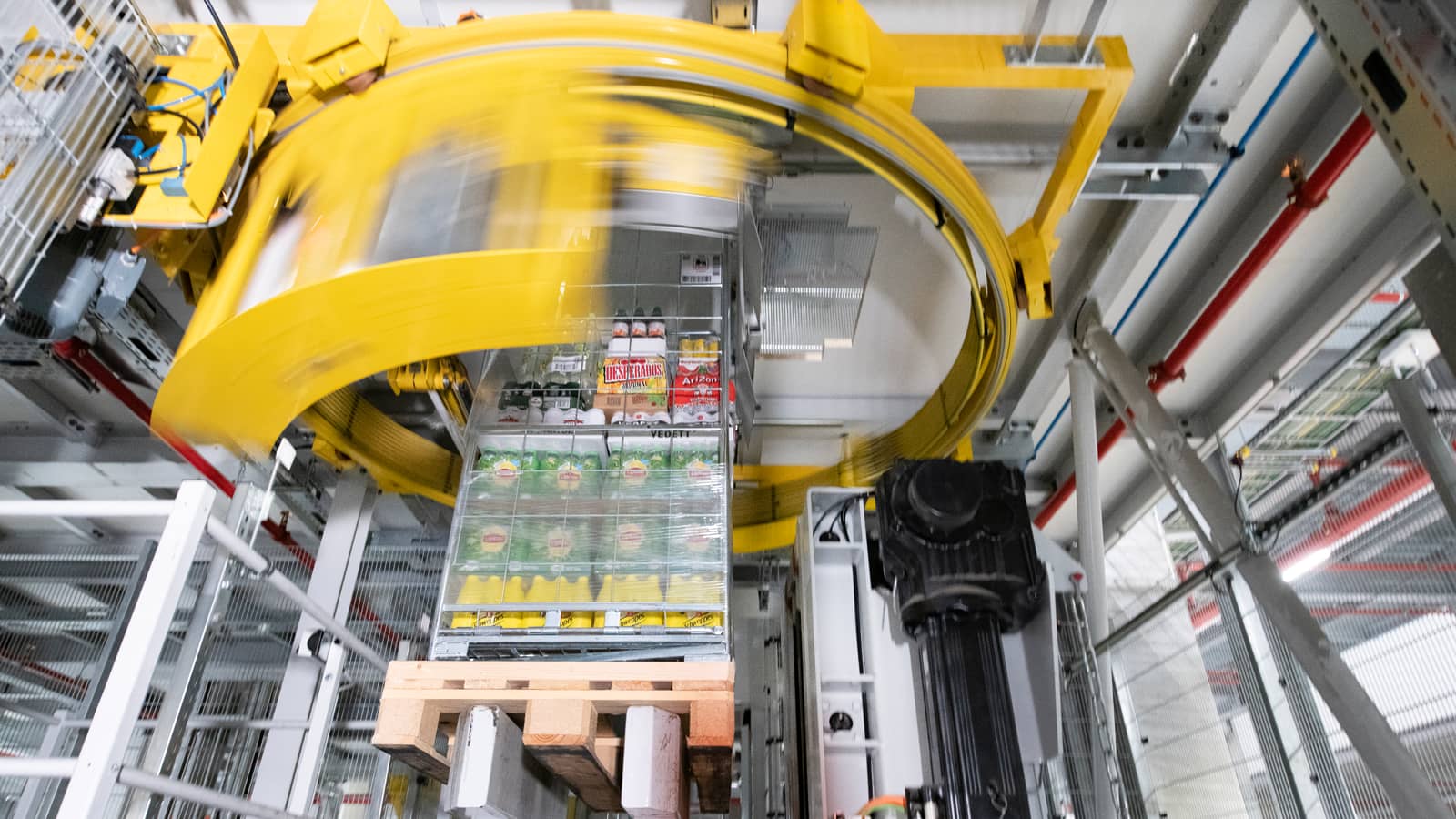
Nine reasons to use automation for mixed case palletizing
Faster, but safer. More SKUs, but less space. Lower costs, but higher volumes. Greater throughput, but fewer errors. Better efficiency, but more flexibility. Sound familiar? For retailers, wholesalers and manufacturers, these are the ongoing challenges of the modern marketplace.
It is not hard to understand where this comes from — there is a never ending pressure from consumers for greater variety, delivered faster, at a lower price. And as performance expectations of supply chains grow in an increasingly integrated global economy, the pressures will only grow as well.
Retailers, wholesalers and manufacturers need a strategy to keep up and keep ahead. This white paper presents the case for one such strategy: Mixed Case Palletizing, a methodology for creating mixed case pallets — automatically and effectively.
A mixed case palletizing system provides the flexibility for a wide variety of businesses to replenish inventories just-in-time and with exactly what is needed. Key markets for mixed case palletizing solutions include:
Let’s explore in detail some of the specific advantages of a mixed case palletizing system.
Dematic Mixed Case Palletizing
Business case for automation
There has always been a need to build and ship mixed case pallets. Whether a facility is handling dozens of SKUs or tens of thousands, the necessity to assemble and deliver pallets with multiple SKUs has always existed and, in fact, has grown. What has been missing is a way to do this systematically.
The business case for mixed case palletizing is about making “systematically” possible. Mixed case palletizing brings automation to the tasks necessary for creating pallets with multiple SKUs: case depalletizing, case buffering and then building mixed case pallets with maximum efficiency. Mixed case palletizing systems use mechanized automation and performance optimizing software to build pallets.
Here are specific benefits featured in an automated mixed case palletizing system:
Software directs pallet building according to how users want to receive the cases — for example, by family group or store planogram. Cases arrive at the palletizer in precise sequence and are automatically loaded accordingly. When the mixed case pallet arrives at its destination (like a grocery store) the cases can be unloaded according to the predetermined plan, thereby minimizing shelf-stocking time.
The control software manages and directs the entire process. It tracks the location of each case from incoming to staging to sequencing to pallet building. Potential for errors are greatly reduced.
Automation helps create a safer work environment. By eliminating the need for workers to lift and move heavy cases manually, ergonomics improve, which removes both intermittent and repetitive injuries. Cases transported and organized automatically within the system decrease the need for fork trucks, which are a source of potential injury.
The compact, high-density configuration of mixed case palletizing systems maximize floor space use. For example, storage and sequencing make the best use of vertical space. And palletizing brings cases to a specific space instead of moving the pallet to multiple areas. As a result, mixed case palletizing systems are ideal for upgrading existing facilities.
Mixed case palletizing systems handle cases in a controlled and automated environment, which minimizes the potential for damage as they move through the system.
Software generates volume-optimized, stable pallets based on the case attributes and business rules. Freight costs are reduced by maximizing the use of truck trailer space.
The system works seamlessly with a wide variety of transport bases, including roller containers and multiple sizes of pallets as required by users.
Mixed case palletizing systems are able to be installed completely or in stages to accommodate facility requirements and budget. Accordingly, they can expanded as market demands grow.
Mixed case palletizing systems use automated equipment to assemble mixed case pallets quickly. But they also optimize speed by how they handle individual SKUs. For example, fast moving cases are stored at forward positions in the buffer to assure efficient throughput.
Mixed case palletizing system design elements
The type of material handling equipment used in a mixed case palletizing system can vary. A system can be fully automated or have some manual components. There are numerous ways that components can be designed and software can be customized. But in the end, a mixed case palletizing system must have three basic functional sub-systems:
Pallets are transferred from the warehouse to an automated layer depalletizer. Layers of cases are placed on conveyor for descrambling and singulation, and then sent directly to the buffering module for sequencing. The cases are oriented for optimal storage space. Damaged cases are recognized and rejected.