Five Benefits of Automation to Maintain Food Integrity
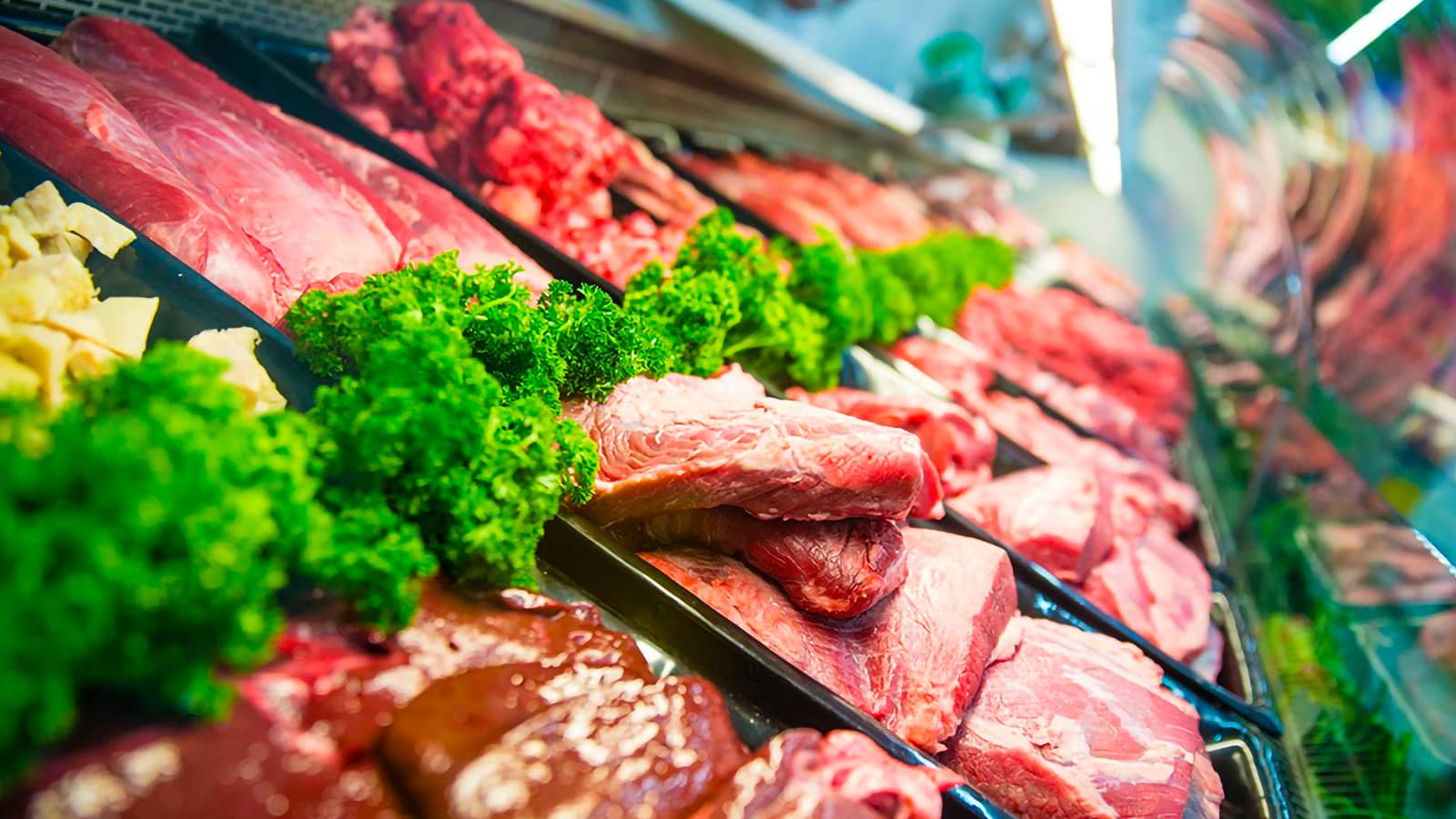
As the world experiences unprecedented fluctuation in our business climate, supply chain has inarguably been one of the sectors most impacted. Concentrating on food and beverage, the industry is experiencing fundamental change. Now with overflowing demand and obstacles at every turn in the flow of distribution, businesses are put to the ultimate test. To combat these challenges and to adapt to today’s market, an increasing number of businesses are now turning toward technology to innovate and future-proof their operations.
The addition of automation to existing warehouse designs opens the door to a world of possibilities. Automation solutions in the supply chain optimize fulfillment speeds, increase productivity, improve worker safety, and more. Many solutions are configurable and scalable, allowing businesses to maintain competitiveness in local and global markets.
Benefit #1: Operate in a smaller footprint
Automation in the warehouse allows for denser storage and easy retrieval. Because an automated warehouse features a high bay configuration, businesses are able to utilize a smaller building size than a traditional warehouse. Typically, an automated operation requires 25% less space and will also experience higher levels of throughput.
Benefit #2: Energy savings
Especially in cold storage, energy operating costs are reduced by the high-density configuration of an automated warehouse. With denser storage in the refrigeration space, floorspace and ceiling height are maximized, allowing for less overall space needed in the cooler. Energy costs for cooling are higher than heating and most loss is from the roof. An Automated Storage and Retrieval System (ASRS) has a smaller roof surface than traditional racking and can create energy savings of 35-50%.
Benefit #3: Minimized exposure to harsh environment
With automation, workers are not required to work in the freezer. Instead, order fulfillment and load consolidation occur on the shipping/receiving dock in ambient temperatures. Elimination of labor in the harsh freezer environment means improved worker ergonomics, improved labor productivity, and the end of worker recruitment issues related to filling staff positions that require work in a freezer.
Benefit #4: Reduced damage
Since the automated warehouse does not require manually operated forklift trucks, damage to racks, product, freezer doors, and the facility are eliminated. On average, a traditional cold storage warehouse may need to replace a freezer door once per month due to fork truck damage.
Benefit #5: Improved inventory and order accuracy
Automated material handling equipment combined with software eliminates lost inventory in the warehouse. Manual put-away becomes automated with data driven inventory management.
This data driven approach provides F&B operations with improved order accuracy by ensuring inventory locations are correct and first-in-first-out (FIFO) inventory rotation is followed. The cost of an inaccurate order for a food distributor is significant. Food quality and freshness, expiration dates, and delivery times all influence order accuracy. If an inaccurate order is delivered to a customer, a costly, expedited delivery is often required. Traditional warehouses can experience several picking errors per day. Automated systems may experience a picking error once per month.
The Dematic difference
With Dematic intelligent automated solutions, producers, and distributors improve efficiency, increase throughput, and reduce the need for manual handling, greatly improving worker safety and operational productivity. Our portfolio provides:
- Automated material handling that integrates high-density pallet storage systems
- Order picking systems for retail stores, e-Commerce, home delivery, and store pick up
- Reverse route truck loading order fulfillment
- Mixed case palletizing
- Flexibility to accommodate variations in order volume and order profiles
- Temperature controlled environments — coolers, freezers
- Traceability controls and software to comply with product tracking regulations
- Standardized configurations for specific categories such as produce, dry goods, soft drinks, and spirits
Furthermore, we tailor our solutions to your business needs by using standardized systems and industry-leading insight and expertise. You can feel comfortable knowing that Dematic offers this support throughout the lifecycle of your system. From design to maintenance, you get the training, assistance, and confidence with a partner just as invested in your success as you are.
Related insights