Tasty Fresh Transforms Picking, Stocktake, and Supply Chain Operations with Dematic Voice Solution
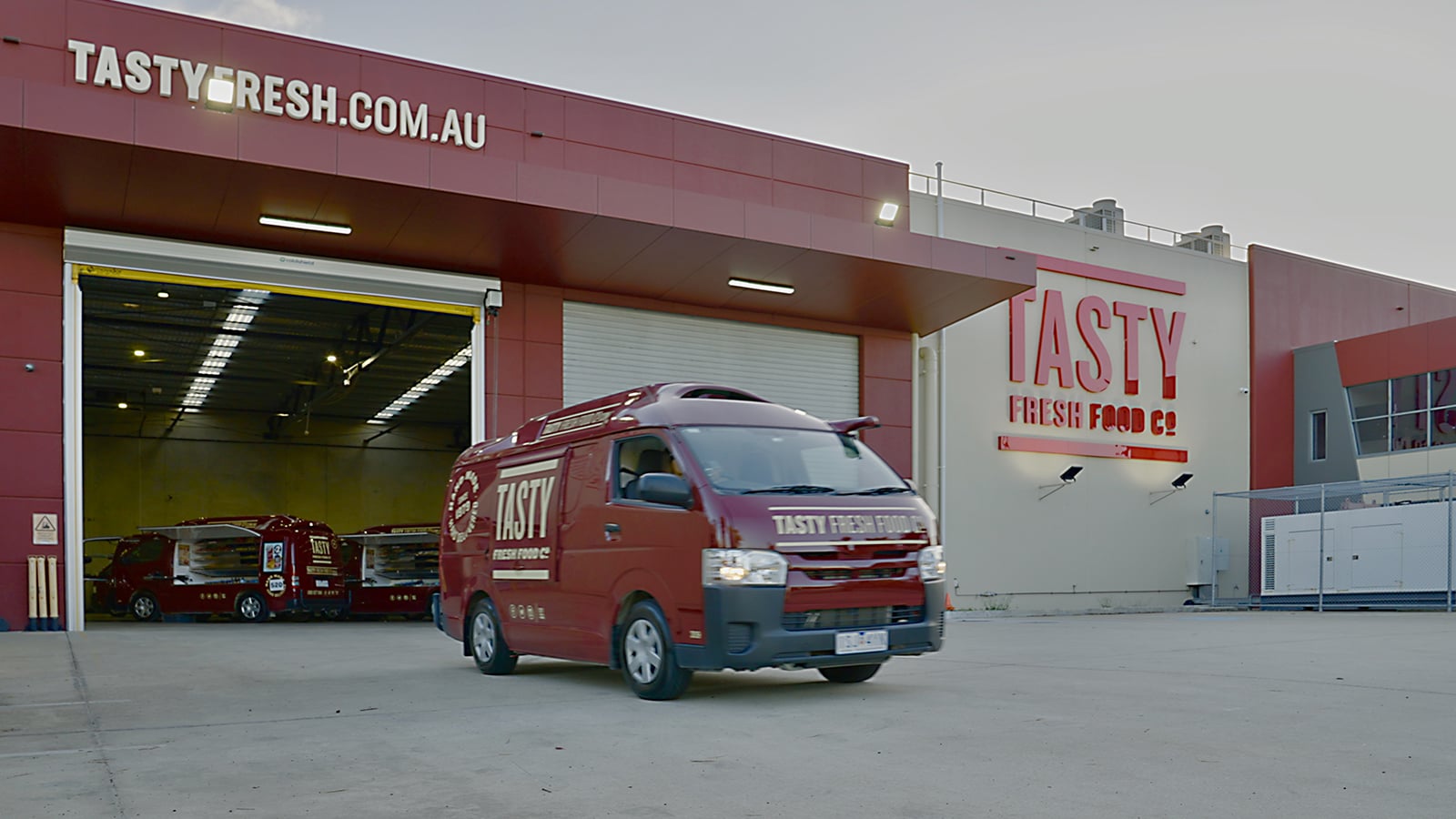
Tasty Fresh Foods Co is an Australian business success story – a company that originated from humble beginnings more than four decades ago. Today, Tasty Fresh delivers fresh and hot food, snacks, and drinks right to the door of workplaces daily in Melbourne, Perth, Sydney, Newcastle, and Queensland.
“Tasty Fresh is a national business that started back in 1979,” explains Colin Lear, Founding Director at Tasty Fresh Food Co. “We have six outlets across four states and service around 35,000 customers per day from around 153 vans. We produce around 60,000 units per day from our facilities and we handle around a 100,000 units per day.
Colin Lear, Founding Director at Tasty Fresh Food Co.“We provide service every business day of the year with over 500 employees around Australia who make that happen.”
Automating Tasty Fresh’s Supply Chain
“Today, many small and medium businesses still use manual methods to carry out the majority of tasks within the supply chain or use scanners and other technologies that are not centrally connected and extremely time consuming,” says Rob Deane, Southern Regional Sales Manager at Dematic Australia.
“As consumer expectations continue to rise, product delivery becomes increasingly demanding, and supply chains are under more pressure than ever before to pick and pack quicker and more accurately.”
Tasty Fresh approached Dematic to move from a manual way of tracing stock with paper and tablets to a more automated and centralised solution that would deliver much higher efficiency, productivity, and accuracy for its supply chain.
“Tasty Fresh’s stock-taking processes previously involved each individual Van Sales Manager doing a stocktake on each individual SKU on our vans,” explains Adam Van Bergen, National Operations Manager at Tasty Fresh Food Co. “With so many people counting so many SKUs, accurately managing stock was a real challenge.”
Rob Deane, Southern Regional Sales Manager at Dematic“As consumer expectations continue to rise, product delivery becomes increasingly demanding, and supply chains are under more pressure than ever before to pick and pack quicker and more accurately.”
Finding the Right Solution for Tasty Fresh
For Dematic, the first step in developing the right supply chain solution for Tasty Fresh was going onsite to learn about the business. It was crucial to get a clear understanding of current processes to achieve the key outcomes Tasty Fresh was seeking.
“We were instantly impressed that Dematic wanted to understand our operations and went through our facility multiple times,” adds Van Bergen. “Dematic understanding us, and not just telling us what we wanted to hear, was a big reason why we chose to partner with them.”
A key focus of the project was to provide data back to Tasty Fresh for inventory and reporting purposes. A real-time logistics voice-on-Android solution was selected as the best system to meet the needs of Tasty Fresh.
The system is a seamless, paperless, and hands-free, eyes-up solution. Operators are guided through a workflow using a mobile device and voice headset, with inputs from voice and scanning automatically sent back to Tasty Fresh’s central supply chain system. This includes data gathered through anything, from order-picking to replenishment and stocktake.
Voice technology can also scale to suit changing business requirements, while empowering management with greater control, flexibility, and visibility over the supply chain.
The strong collaboration between the project team members meant the voice project was delivered seamlessly on time and within budget.
“My favourite parts of this voice technology are the traceability, the ease of use, and the support we get,” says Van Bergen. “I definitely recommend it to any business considering it.”
How Voice Improves Operational Efficiency for Tasty Fresh
“The voice system was deployed at each Tasty Fresh depot,” says Deane. “The two primary voice workflows implemented were pick-to-trolley and van loading.”
The system tells Tasty Fresh team members which food or drink product SKUs and quantities to load onto each trolley. When completed, they proceed to van loading. Team members are then instructed, per van ID, which SKUs and associated quantities are to be replenished into each van in SKU sequence.
Product shorts, overfills, and audits are all tracked simultaneously, saving workers the time having to go back and forth doing these tasks separately. This helps Tasty Fresh to check expected stock from point-of-sale deductions versus physical van replenishment – all through the one voice technology process.
“The system tells us what to load in the vans and records how many are loaded,” says Aline, Brisbane Warehouse Manager at Tasty Fresh. “So the same time we are loading, we are also doing the stock take. It’s a great system that ensures our stock is right by matching our sales with the stock loaded in the vans.”
The Impact of Voice for Tasty Fresh
Some of the key benefits to Tasty Fresh feature management of inventory and providing traceability of that inventory.
Voice technology delivers up to a 35% productivity improvement from legacy systems, through allowing worker hands to always be free to pick products and complete all warehouse tasks.
“Voice has improved productivity across the business,” says Van Bergen. “Instead of having 157 people stocktaking, we now only have 20 to25.
“We're saving between five and ten minutes a day per van sales manager. That might not sound like a big deal, but five to ten minutes across 170 employees a day is quite a cost saving.”
Heightened worker productivity with voice guidance makes the employee roles more intuitive and focused, resulting in less errors and better worker satisfaction.
“It's great to have our hands-free, with no paper,” says Mirlla from the Brisbane Warehouse. “Instead, I'm able to use my hands to do the job quicker. It's also safer because I don't have to be holding the paper while handling the food and drink products.”
Voice technology offers management greater visibility, control, and flexibility over the supply chain operations.
“The voice technology makes my job a lot easier because I'm able to easily trace where the stock is and where it is going. Before, I would have to sift through hours of data just to find what I needed,” says Van Bergen.
With eyes always focused on the job, workers can quickly find, pick, and pack the right products, reducing errors by up to 50% and the time it takes to complete.
The voice solution is extremely easy for new workers to learn, particularly with the Android platform, which is familiar to most people.
“We're able to train new staff within half an hour,” adds Van Bergen. “And the feedback is that it’s great, that it’s easy to use, and any problems that arise are fixed within 24 hours.”
The voice solution is a simple bundle offering that includes hardware, headset, the application, and licencing for an easy purchase, deployment, and support guideline.
The voice solution improves supply chain efficiencies, productivity, and accuracy and provides additional benefit the end consumer.
“Every change we make in our business, it's always about how will this affect our customer? The move to voice is giving us a better opportunity to satisfy consumers by picking the correct product,” says Lear.
An additional benefit, Tasty Fresh has been able to re-deploy staff to more productive tasks.
Expanding Voice Usage Across New Business Areas
Because of the success of the voice solution rollout, Tasty Fresh is looking to roll out many more applications – from confectionary picking and production picking right through to its fleet of food vans.
“It's been a terrific partnership with Dematic. That's why we want to continue taking it to every area of our business so for everything that's handled and picked, voice and the Dematic system will take care of it,” says Lear.