Streamlined Small-Parts Warehousing with Dematic Multishuttle™
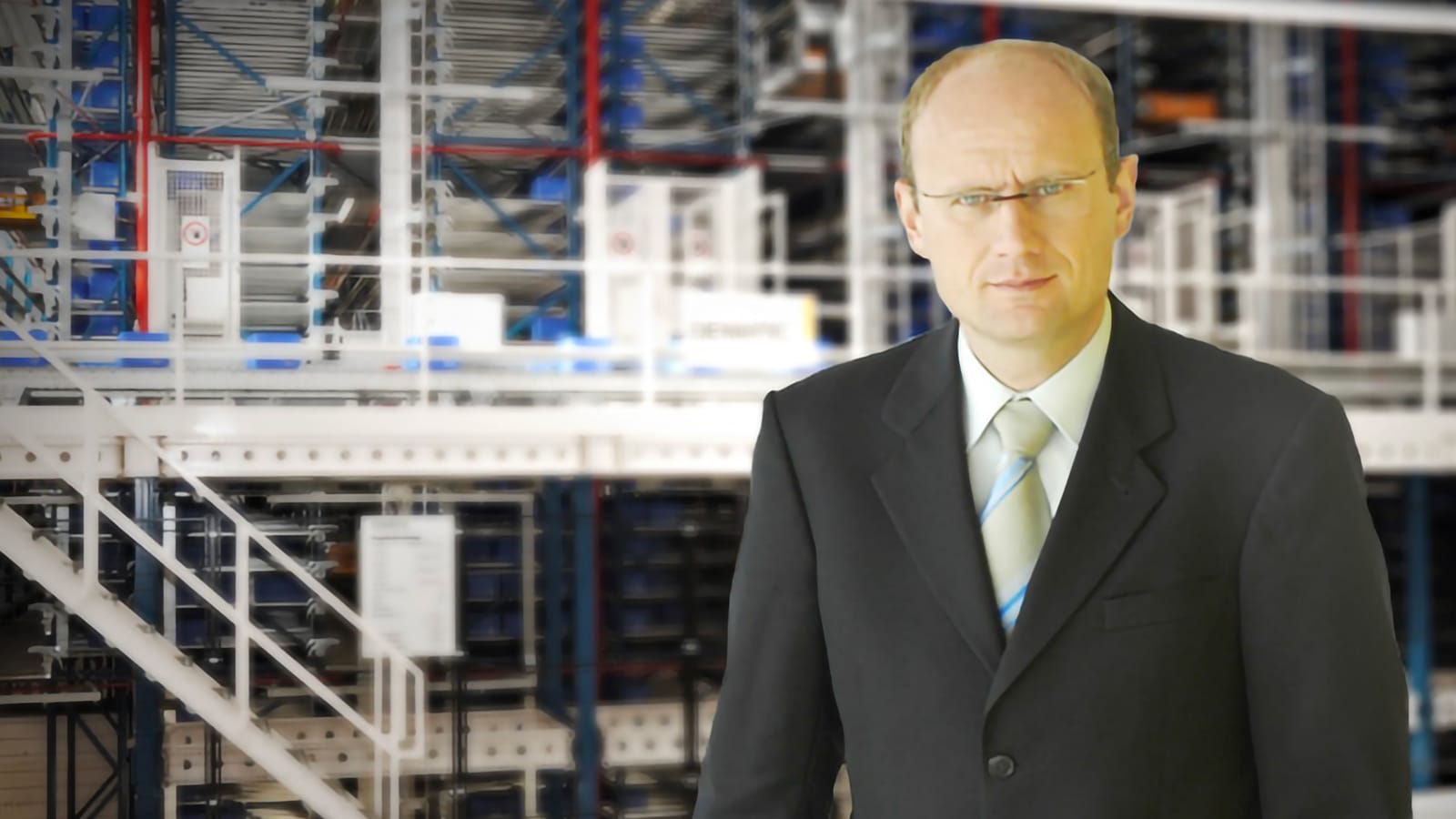
Ferdinand Gross, a major European supplier of fasteners and connectivity technologies, has installed a tailor-made and innovative storage and order fulfilment solution featuring the new Dematic Multishuttle. This solution has effectively increased storage capacity by 100 percent without an increase in footprint. Order throughput times have been reduced from as much as 3.5 hours to as little as 30 minutes, and as a result, the company was able to extend the incoming order cut-off time by three hours. In addition, labour hours have been reduced by 50 percent.
The challenge
For Ferdinand Gross, the primary objective of the design was to enhance the level of customer service through a cost-effective distribution concept and expansion of storage capacities. “Originally, Ferdinand Gross wanted to utilise unused space on their grounds for the DC expansion,” explained Dr Volker Jungbluth, with Dematic. “We showed them how they could build their new distribution centre within their existing building by modifying much of their system with Dematic Multishuttle.
The solution
Dematic retained the DC’s existing high-bay racking, and integrated it into the Dematic Multishuttle system, while repurposing it to handle roaming functions. Combined with the system’s captive functionality, the Ferdinand Gross DC became the world’s first system to operate Dematic Multishuttle with both roaming and captive modes in an integrated set-up.
The project was started in June, 2008. During the following eleven month the DC continued to operate at full functionality until Dematic Multishuttle went live in May, 2009.
Dematic Multishuttle
Dematic Multishuttle is a flexible Automated Storage and Retrieval Systems (AS/RS) solution for applications that require dynamic, high rate, product sequencing to support order assembly, goods to the person picking and pick face replenishment. The key attributes of Dematic’s Multishuttle include high-rate capacity, ability to accommodate load sequencing requirements and adaptability to existing building layouts.
Dr Volker Jungbluth - DematicFerdinand Gross decreased its warehouse labour utilisation by 50 percent once Dematic Multishuttle went live.
Order throughput times have been reduced from as much as 3.5 hours to as little as 30 minutes, and as a result, the company was able to extend the incoming order cut-off time by three hours.
Design
The key attributes of Dematic Multishuttle include high-rate capacity, the ability to accommodate load sequencing requirements and adaptability to existing building layouts.
The speed of the system is the result of integrating two tiers of picking shuttles – roaming and captive – within a single storage unit, and with identical shuttles in both areas.
The products are delivered to the picking stations in the precise sequence that they are needed for picking in accordance with the order. The system has a handling capacity of more than 1,000 picks per hour.
Ferdinand Gross’ Dematic Multishuttle storage and retrieval system comprises the racking, rail-guided shuttles, running rails and controls. In addition to guiding the shuttles, the rails also supply the carriages with electrical power. The load bearing elements ensure short cycle times for a large number of different bins, cartons or trays. Storage or retrieval orders are transmitted to the shuttles by WLAN (Wireless Local Area Network), to which the Dematic Multishuttle is linked via a sophisticated control system – Dematic’s DC Director warehouse management and control system, which provides real-time management of the system, ensuring seamless integration of all the subsystems and technologies.
The results
Faster order processing, reduced shipping costs
The new Dematic Multishuttle system has delivered a significant reduction in order throughput times, from as long as 3.5 hours previously to as little as 30 to 60 minutes with Dematic Multishuttle. This has allowed the daily order cut-off time to be moved back three hours, from 12:00 noon to 3:00 pm. For the company’s customers, and particularly those with just-in-time manufacturing requirements, this means greater flexibility in ordering.
It also facilitates reduced shipping costs. At a delivery deadline established by the customer, all pending orders in the system are bundled into a single shipment. The resultant later order dispatch allows better bundling of individual orders, reducing the number of separate packages to be shipped.
Additionally, before the switch to Dematic Multishuttle, customer’s shipping containers had a fixed label, showing article number, article description, product count and the customer’s name. Once the customer emptied the container, Ferdinand Gross would pick it up and return it to the DC, ready to be refilled and shipped out again. With the new system, customer containers can now be relabelled for filling with any product rather than waiting for the original empty container to return to trigger a new order.
Customer benefits
- Improvement in order fulfilment times, extending order acceptance deadlines
- Sequencing to customer specification
- Ergonomic workstations for improved operator performance and safety
- Modular concept, allowing for future expansion at any time
- Increased storage capacity by 100 percent without an increase in footprint
- Labour hours reduced by 50 percent
- Order throughput times reduced from as much as 3.5 hours to as little as 30 minutes