Metcash Modernises Distribution with Dematic Automation at Truganina
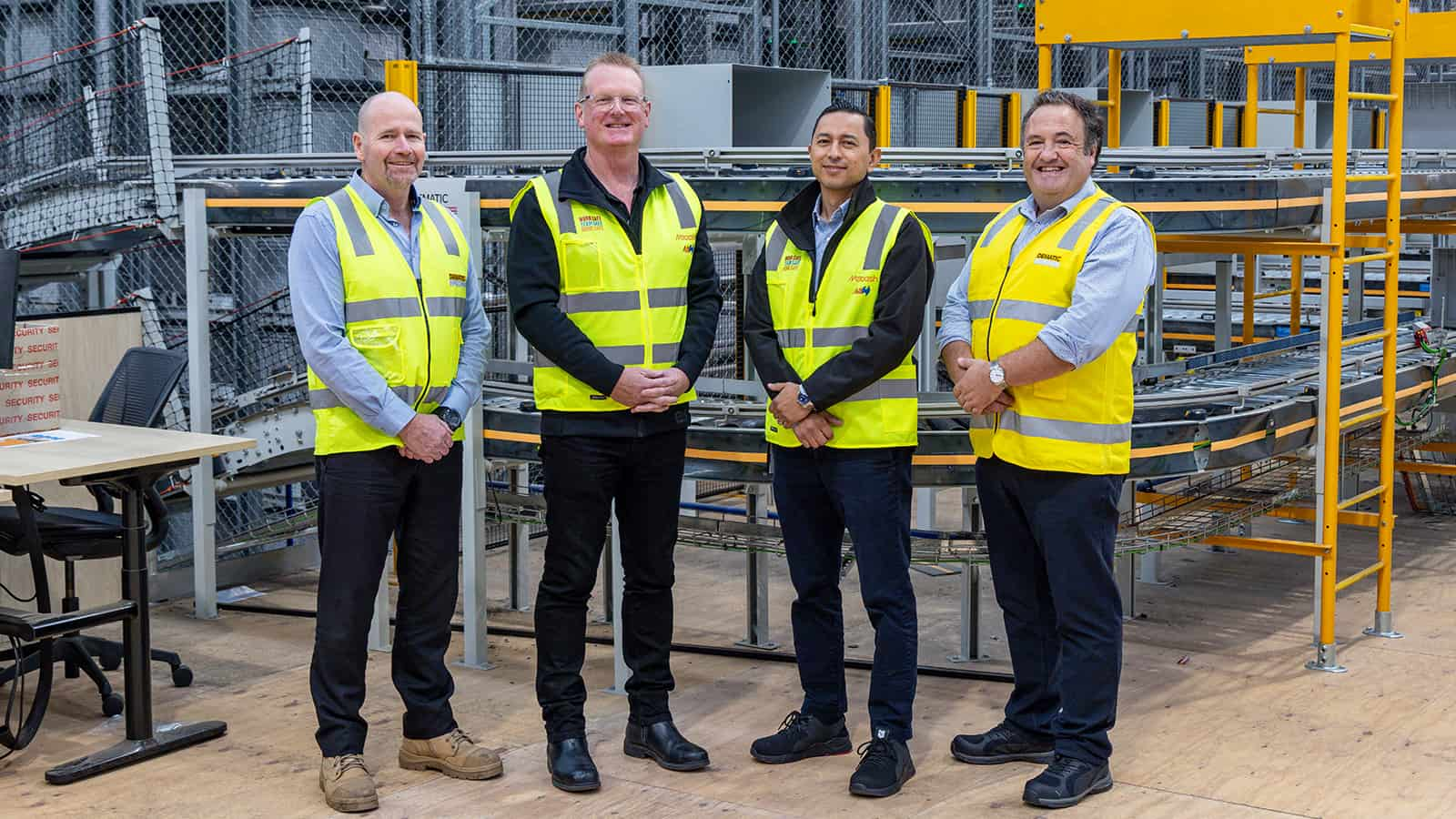
Looking to future-proof its Victorian supply chain operations, Metcash set out to consolidate its fragmented infrastructure into a single, modern distribution centre (DC) in Truganina. By partnering with Dematic, Metcash implemented a goods-to-person (GTP) automation solution powered by Multishuttle technology, designed to lift efficiency, reduce operational costs, and create a scalable foundation for growth.
The challenge
For many years, Metcash’s Victorian operations were spread across a multi-shed facility in Laverton, supporting its grocery, liquor, perishable, and convenience businesses. While functional, the site relied on a mini-load automation system installed nearly two decades ago. As the system aged, sourcing spare parts became a growing challenge, and operational efficiency began to suffer. The site’s fragmented layout also made it harder to streamline processes and keep pace with rising demand.
Recognising the limitations of their legacy setup, Metcash made the strategic decision to bring its operations together under one roof. The goal was to build a modern, integrated DC that could improve picking speed, simplify workflows, and provide the flexibility needed to support continued growth across multiple retail channels.
“The challenges of operating across multiple sites made it clear we needed a smarter, more integrated solution,” says Victor Cleves, Head of DC Automation and Design at Metcash. “Bringing everything under one roof was about creating a foundation that could support both current demands and future expansion.”
The solution
Dematic was selected to deliver a highly flexible, compact GTP automation solution tailored for Metcash’s new 115,000 square metre distribution centre. At the core of the system was a high-density Dematic Multishuttle, initially built with seven active pick stations and the ability to add an eighth as the business grows.
Dematic’s patented Inter-Aisle Transfer (iAT) technology provides high storage, retrieval, and picking flexibility, allowing bins to be dynamically shuffled, ensuring every pick station could access any stock keeping unit (SKU) in the system. This active flexibility was critical for enabling Metcash to ramp operations up or down as needed based on demand.
To support dispatch operations, Dematic installed Flex Shuttles in the sortation buffer, allowing Metcash to efficiently manage cartons of varying sizes and fulfil a wide range of customer order profiles. The Flex model uses advanced load handling technology, with flexible arms that adjust to different product sizes and gently grip items without needing trays. This flexibility was key to meeting Metcash’s diverse storage and picking needs, helping to maximise storage density and throughput within the site’s space constraints. It also ensured orders were processed in time to meet tight truck dispatch schedules and route commitments.
The system was also designed to handle liquor, a key requirement during the tender process. Dematic conducted successful live trials with wine bottles to validate the system’s ability to manage fragile and varied product formats, giving Metcash added confidence in the solution’s capabilities.
“Operator wellbeing was also a key focus for our business,” Cleves explains. “Dematic’s Gen3 pick stations, especially the adjustable platforms and powered lift-and-rotation tables, made a huge difference in ergonomics and safety. It’s been a real game changer for our team.”
Integration was another crucial factor in the project’s success. The Dematic system was engineered to interface simultaneously with two distinct warehouse management systems (WMS), one managing Metcash’s grocery operations and the other for its liquor division. With demonstrated expertise in multi-system environments, Dematic approached the integration with confidence. This capability was critical for Metcash. Overcoming these technical hurdles was key to guaranteeing Metcash could streamline operations within the new Truganina facility and lay the foundation for future scalability.
Executing a seamless transition
Metcash’s transition to Truganina was carried out in four stages, including a dedicated phase for the automation cutover. Operations at the Laverton site ceased completely on a Thursday. By the following Monday morning, the new Truganina facility was live, operational, and fulfilling orders.
“This was a high-pressure transition that required careful planning, strong operational discipline, and a lot of support,” says Cleves. “Dematic delivered months of structured training and hands-on commissioning, gradually bringing our team into the process. By the time go-live came around, our operators had already been running parts of the system themselves, so they were confident and ready.”
Dematic’s service team worked weekends and ran double shifts to prepare the site, ensuring every element of the system was tested and optimised. Three experienced technicians who had supported Laverton were transferred to Truganina, bringing invaluable knowledge.
Delivering on time was only possible through close collaboration between Dematic and Metcash, with both teams fully aligned and working in sync throughout the lead-up to go-live.
“They [Dematic] knew the Metcash team and the systems inside out. That familiarity helped immensely during go-live,” explains Terry Jamieson, Business Development Manager, Dematic.
Despite the enormous complexity of the transition, the new site began fulfilling orders from day one without disruption. The result was a seamless transformation of Metcash’s Victorian supply chain, executed with zero downtime to customers.
Customer service and support
Dematic’s strong local presence in Australia and New Zealand was instrumental not only in securing the Truganina project but also in ensuring its success during and after implementation. With more than 345 service professionals across the region, including engineers, technicians, spare parts specialists, and a dedicated modernisation unit, Dematic provided the kind of rapid, reliable support that Metcash required.
“Having a strong local service team was a huge advantage for us,” says Andrew North, Metcash Victorian State Logistics Manager at Metcash. “It meant we had immediate access to the support we needed, whether it was for technical advice, parts, or on-site assistance. That level of responsiveness gave us real confidence during the transition and set us up for long-term success.”
The transition was also strengthened by continuity in personnel. Several technicians who had long supported Metcash at the Laverton site were transferred to the new facility, ensuring valuable institutional knowledge wasn’t lost.
The results
Since implementation, Metcash has realised significant performance improvements. The higher pick rates have enabled the company to consolidate operations into a single-shift model, enhancing resource utilisation and driving greater cost-efficiency. The system’s built-in redundancy has mitigated the risks previously posed by the older crane-based mini-load setup, ensuring more reliable access to inventory.
Dematic also introduced a Lifecycle Cost Plan, providing Metcash with a clear forecast of expected capital expenditure and maintenance costs over five, ten, and fifteen years. This forward-looking approach allows Metcash to better plan and budget for future system upgrades, maintenance activities, and replacement parts, reducing the risk of unexpected costs and helping to protect the long-term performance of the automation investment.
“The new system has allowed us to significantly improve efficiency and better manage our labour requirements,” says North. “The visibility we now have around long-term maintenance and planning also means we can be more proactive with our servicing schedule and allows us to react quickly to retailer and market needs.”
Dematic’s relationship with Metcash continues through ongoing site support and modernisation projects.
“The solution we put forward at tender is exactly what we delivered, which confirmed we had a strong understanding of what was needed from day one,” concludes Jamieson. “We’ve worked hard to be the partner Metcash can depend on, from design through to daily support, we’ve built something together that’s not just functional, it’s future-proof.”
Victor Cleves, Head of DC Automation and Design, Metcash“Dematic’s pick stations, especially the adjustable platforms and powered lift-and-rotation tables, made a huge difference in ergonomics and safety. It’s been a real game changer for our team.”
About Metcash
Metcash is one of Australia’s leading wholesale distributors, supplying independent retail brands such as IGA, Foodland, Cellarbrations, Mitre 10, and more. With a strong national footprint and a focus on supporting local communities, Metcash plays a vital role in helping independent retailers stay competitive in a dynamic market.