Modernisation of the Bell logistics centre in Zell, Switzerland
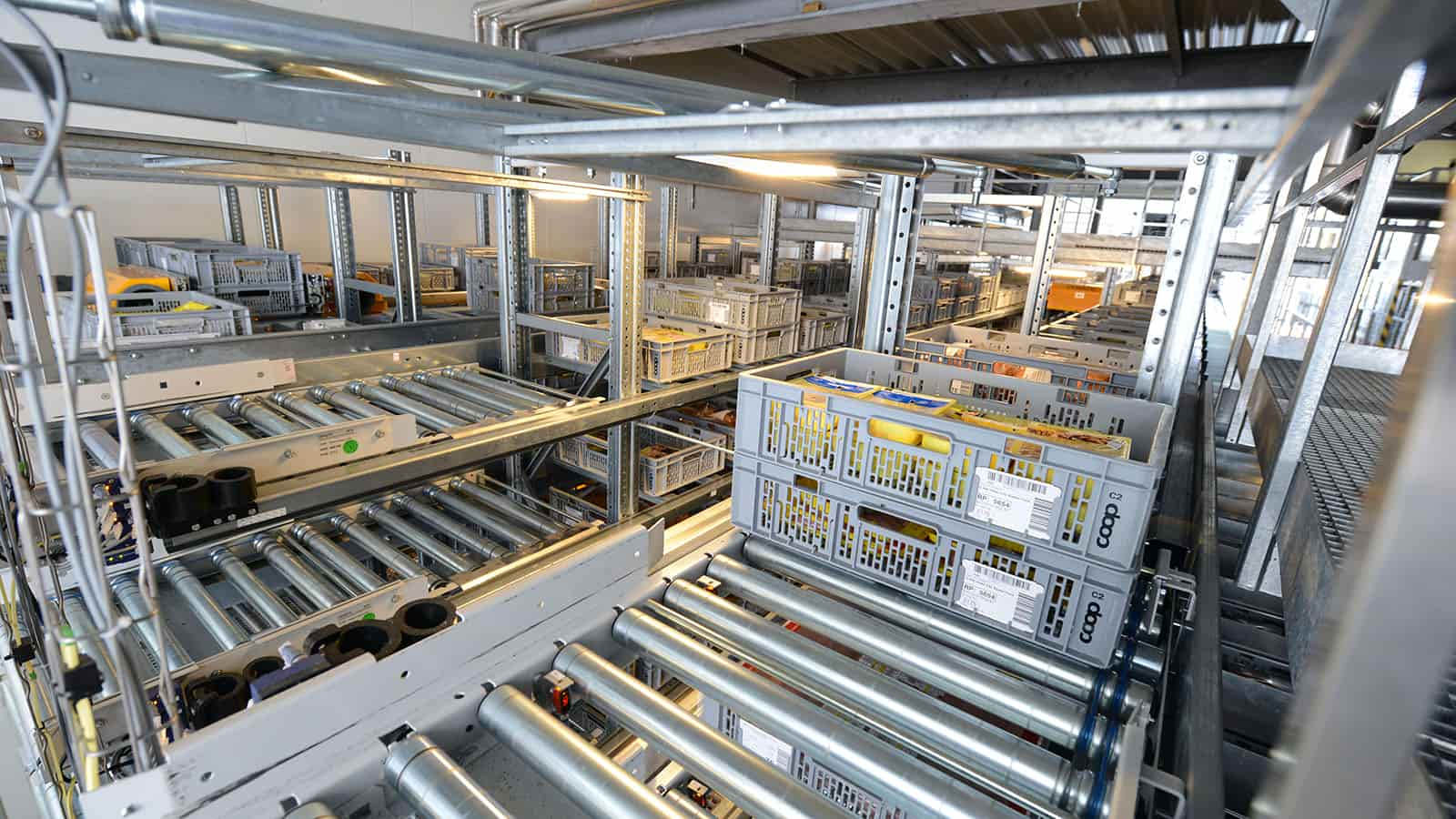
The installation of a Multishuttle warehouse as an outgoing goods buffer and the replacement of the existing warehouse software during operation has effectively increased the throughput of the logistics centre. This enables Bell to load and deliver more roll containers to retailers in a sequenced manner.
The challenge
The logistics centre for raw materials and finished goods with an operating temperature of 0 to +2 °C, next to the production area and equipped with highly automated conveying, storage and order-picking technology, reached its capacity limits already. Bell therefore decided to work with a logistics planner to develop solutions for optimising and expanding the logistics facility within the existing building.
Deviating from the developed concept, Bell finally decided on the solution provided by Dematic, which envisaged the innovative Multishuttle technology for the storage, order consolidation and sequencing of all picked and single SKU containers.
At the site in Zell, which has existed since 1950, mainly poultry is slaughtered, cut up and processed. Production planning is largely based on forecasts, as 80% of incoming orders must be delivered on the same day.
From the cutting plant, the meat containers are first transported via a conveyor system to the raw materials warehouse. When requested by the production department, the containers are automatically transported to the packing department via a conveyor system. There, the fresh meat is packaged for the retail trade according to the order and placed in C2 containers according to article.
These containers weighing up to 30 kg with the finished goods are then stored in stacks of two in a finished goods warehouse consisting of several blocks. From here, the shelf trucks equipped with four forks also load the channels for Pick-by-Light picking directly adjacent to the front of the warehouse from the warehouse aisle.
Up to this point, the existing transport, storage and picking processes will remain operational, but will be supported by a new warehouse management system (WMS) and a new material flow control system based on the Dematic Software. Dematic has redesigned the material flow for the subsequent intermediate storage of the finished picked totes and complete packs, which are directly retrieved from the finished goods warehouse via a conveyor system.
Thomas Graf, Head of Operations at Bell Schweiz AG, Poultry Business Unit“Our goal was, of course, to complete the commissioning without any noticeable impact on our customers. We have achieved this”.
The solution
As Bell’s existing logistics facility was a system with highly complex functionalities and a large number of dependencies and influencing factors, the required strategies and material flows were to be confirmed by means of a comprehensive simulation model before the start of the implementation. The software solution developed on the basis of these results and the specific requirements was then subjected by Dematic together with Bell to an extensive factory acceptance test.
During this test, all coordinated business processes as well as special cases and malfunctions were intensively tested in a laboratory environment. A standstill in production or outgoing goods was to be avoided by all means. In order not to take any risks, all tests had to be run through and function properly before commissioning.
Implementation
To make the tests as realistic as possible, Dematic’s IT specialists created an emulation that simulates and graphically displays the control level and mechatronics. From the point of view of the software application, the emulation behaves in the same way as the real control system on the plant later. The emulation also makes it possible to run at higher speeds than in the real plant in order to stress the hardware a little.
This test phase has been used intensively in order not to risk production losses and to keep commissioning times short. Testing and commissioning the software during operation was the biggest challenge. Dematic only had very limited time slots available at night or on weekends. But the effort was worth it because the commissioning went smoothly.
In a first stage, Dematic replaced the IT system for the raw materials warehouse and introduced an interface between the host and the Dematic Software. In addition, an interface to the old warehouse control system also had to be programmed, as the finished goods warehouse was still running under the old control system. The work for this was very complex, as there was no open documentation.
In the next step, the technicians installed the four Multishuttle storage blocks, including the conveyor connection to the existing order picking system. In this phase Bell initially processed all productive orders using the existing finished goods warehouse and the existing roller container loading system. The Multishuttle system was exclusively commissioned with test orders during this time.
In the third stage, the remaining parts of the warehouse management and material flow control systems were replaced – before the Multishuttle sorting buffer was finally put into live operation.
Technical data
- Dematic Multishuttle system with 4 aisles, 9 levels and 36 shuttles
- 3,600 container storage positions, storage in stacks of two is possible, with a stacking factor of 1.5, the Multishuttle warehouse can accommodate 5,400 containers
- Top speed of 6 m/s and throughput of 3,000 containers per hour
- Simulation and emulation of the control level and mechatronics
- Interface to the old warehouse control system
The process
Today, the finished picked totes arrive at the new outgoing goods buffer via the existing lower or the new upper retrieval section, either singly or in stacks of two. The Multishuttle warehouse of the type Captive with one shuttle per level and aisle is divided into two lower and two upper blocks with nine levels each for single-deep storage of the totes.
The simulation beforehand showed how large the required system performance of the Multishuttle must be in order to achieve the required throughput. The spatial conditions then determined how large and how deep the modules could be built. With a stacking factor of 1.5, the Multishuttle warehouse can accommodate 5,400 containers and, with 36 shuttles travelling at a top speed of 2 m/s, achieves a throughput of 3,000 containers per hour.
When feeding the finished picked totes into the goods issue buffer, care is taken to ensure that all totes planned for the same shipping roll container are also stored in the same Multishuttle block. For this purpose, the system is equipped with four storage and four retrieval lifts, whereby each lift can simultaneously accommodate two transport units. As soon as all the containers for a roller container have been stored, they can be retrieved in the desired sequence according to shipping priority and branch-specific and then fed to the roller container loading system. For this purpose, each storage block is equipped with a supply conveyor with one workstation assigned.
Thomas Graf, Head of Operations at Bell Schweiz AG, Poultry Business Unit“Dematic had the best solution for our circumstances – also with regard to space utilisation – and performance requirements and also made the most competent impression when it came to software replacement during operation”.
The results
Bell Schweiz AG has achieved the performance targets specified in the offer and has been able to increase throughput significantly since the commissioning. In addition, the technical stability and availability of the existing plant was improved. This is because the retrofit and the reduction of movements in the finished goods warehouse have greatly reduced the technical load on the entire system. This has a positive effect on the maintenance of the system and the racking vehicles, which now manage with longer maintenance intervals.
About Bell Group
The Bell Group is one of the leading meat processors in Europe and is known to consumers through brands such as Bell, Abraham, Zimbo, Môssieur Polette, Hoppe, as well as various private labels and trade brands.
Bell produces traditional specialities of high quality in 27 production plants in seven countries, including smoked ham, salami, cooked sausages and portioned and marinated fresh meat for grilling. Customers include retailers, wholesalers, the catering trade and the food industry.
At the Zell site Bell processes poultry into packaged fresh meat and convenience products for the retail trade - primarily for the sales outlets of the parent company Coop.