Navigating a Complex Landscape: Survey of Top Supply Chain Challenges for 2024
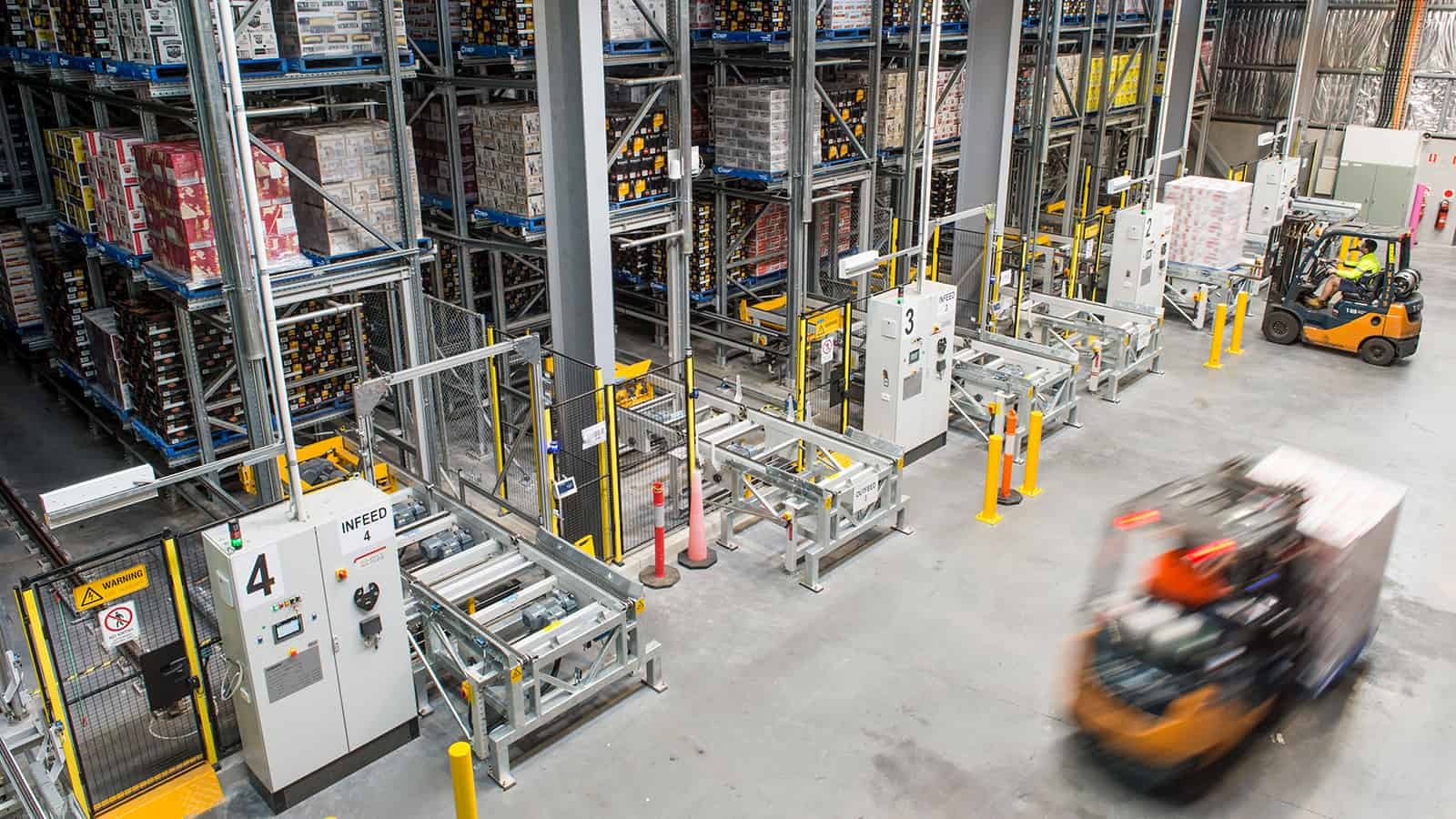
Across countries in Southeast Asia, food and beverage and grocery companies find themselves faced with a shared dilemma: land shortages amidst rapid urbanisation, coupled with the ongoing volatility of energy costs.
However, within these challenges lie opportunities for innovation, capacity and efficiency enhancements, and the cultivation of sustainable practices. This dynamic environment calls for strategic responses and fresh approaches to not only address current challenges but also to be prepared for future uncertainties.
Population density: operational challenges in a crowded landscape
High population density in many areas of the Southeast Asia region has significantly impacted food and beverage and grocery supply chains, with an average population density of 151 inhabitants per square kilometres across the ASEAN region. This has steadily been on the increase over many years.
High population density, particularly in urban areas, has led to high land demand, creating land scarcity and high real-estate costs.
The high population densities in some parts of Southeast Asia have caused a rethink in how suppliers manage their logistics and distribution networks to service increasing demands of their customers, including making it more common for businesses to share multi-level fulfilment facilities.
Innovative solutions to high urban density
High-density population centres and limited land has led to smaller footprint urban stores, so grocery retailers can stay closer to their customers and better service their needs of convenience in our major cities.
These smaller stores, with more distributed networks, require strategically located food and beverage distribution facilities and the need of getting the most out of the limited land available. For food and beverage manufacturers, the need to be close to customers as well as manufacturing facilities (and ideally co-locating and integrating warehouses with existing manufacturing sites to streamline operations, eliminate production bottlenecks and reduce transportation costs), means that manufacturers are looking to maximise capacity and throughput in the smallest land footprint.
When considering their logistics footprint, food and beverage suppliers must implement optimised solutions that not only enhance economies of scale but also maintain agility in response to fluctuating market demands, without sacrificing performance. It's imperative they leverage their existing land footprints to achieve increased storage capacity, heightened throughput, improved facility velocity and greater overall value, ensuring every square inch contributes to operational efficiency and effectiveness in production, warehousing and distribution.
Automation enabling optimised space utilisation
One leading solution used for these logistics requirements is Automated Storage and Retrieval Systems (AS/RS), which offer a way to significantly enhance storage efficiency within the limited available space. Combined with the capability of automatically loading and unloading trucks, this solution provides a high-density, high capacity, fast, accurate and cost-efficient storage and delivery solution.
Because automated warehouses do not require space for forklift trucks, they take up less cubic space for the same amount of storage — typically 25% to 35% more storage density over traditional warehouses, and with heights typically 30-35 m (and up to 45 m) they can deliver 200% or higher increased storage in the same land footprint. As AS/RS are fully automated solutions they also reduce reliance on labour during a time of low worker availability. With an AS/RS solution, stock cannot be lost or forgotten, as the system provides complete and real-time visibility of overall inventory.
PepsiCo Thailand AS/RS
PepsiCo, a global leader in convenient foods and beverages, recently partnered with Dematic to integrate automation as a central feature of its expanded production and logistics facility in Rojana, Thailand.
To support PepsiCo’s growth and address space constraints and labour challenges, Dematic worked closely with PepsiCo to develop an automation solution to address their storage, throughput capacity, and productivity needs in their logistics operations. The solution centres around an AS/RS with a direct link to both the production and order fulfilment areas.
The AS/RS stores pallets within five aisles of double-deep, high-bay racking with a total of 16,520 pallet locations. A network of pallet conveyors and Rail-Guided Vehicles (RGVs) receives pallets automatically at the end of the production lines and transports them for storage, then directs them from storage to despatch docks or to automatically replenished pick locations for full-case order picking. The solution includes Dematic Warehouse Control System (WCS) software to manage all the automation, the material flow, and the inventory as well as to provide real-time tracking and visibility of all transactions.
Colin Matthews, Supply Chain Senior Director – IndoChina Foods, PepsiCo, says, “Previously we had a very manual solution that took a lot of time for people to go around and understand exactly what products we had in the warehouse. In contrast, the Dematic solution is very intuitive. It enables our team to look across the whole of the AS/RS and understand exactly where we have the stock, and they can intuitively and quickly make any adjustments they need to. The AS/RS has more than doubled our capacity and the automation takes us away from the very manual operation we had before. This allows us to supply goods to customers with greater efficiency, leaving them very satisfied.”
The solution is designed with the future in mind and can be expanded to accommodate additional growth and adapted to changing business requirements.
Bikaji India AS/RS
Bikaji, one of India’s leading FMCG food brands, offers over 100 packaged snack products, including more than 10 varieties of their signature Bhujia. At their Bikaner, Rajasthan production facility, high SKU proliferation, unpredictable demand, and varying product popularity led to inventory control problems, dispatch inaccuracies, and delayed order fulfilment. Additionally, the slow movement of goods within the facility caused production and dispatch volume issues, resulting in operational difficulties and revenue losses.
Armstrong Dematic, Dematic’s strategic partner in India, identified storage and retrieval as the primary issue to be overcome. The facility had unused storage space on the ground level, but transportation challenges prevented its utilisation. Through its end-to-end consultative approach, Armstrong Dematic designed a solution utilising an ultra-high density pallet shuttle AS/RS system, capable of housing up to 2,064 pallets in multiple-deep, high-density storage.
In the system, a pallet shuttle carries a smaller pallet cart in the storage aisle with the pallet. When it reaches the correct storage bay, the child cart leaves the parent shuttle to store the pallet into the multi-deep storage lane, before driving back to the shuttle ready for the next storage or retrieval task.
The solution provided numerous benefits for Bikaji: better space utilisation and increased storage capacity enabling more flexible handling of SKU proliferation, labour and time savings in storage, with reduced order fulfilment times. With the WMS integrated seamlessly into the ERP software it improves operations management and provides highly accurate inventory tracking. The result was multi-fold turnover in the same space, faster inventory processing, higher customer service levels driving higher customer satisfaction, and wider geographic reach.
Volatile Energy Markets
Another pressing challenge for supply chain operations across industries is the rise in energy costs, and many parts of the Southeast Region are affected by this.
For instance, Singapore is reliant on imported natural gas for approximately 95% of its electricity supply. This means any global energy impacts will have a flow on effect to Singapore’s electricity prices. This has created volatility in the wholesale electricity market over recent years due to disruptions from geopolitical tensions, inflation, high local demand, and spikes in global fuel prices.
Meanwhile, the Philippines has one of the highest electricity prices in Southeast Asia, second only to Singapore.
Predictions for ongoing future rises in energy prices, coupled with the high energy consumption characteristic of these sectors, have highlighted the urgent need for more energy-efficient warehousing solutions.
This is particularly pertinent for cold chain logistics where energy efficiencies are lost due to footprint and ineffective use of the available cube.
Moving Towards Energy Efficiency
AS/RS high bay warehouses in cold chain logistics environments represent a significant advancement towards improving energy efficiency. By maximising storage density and minimising overall cubic volume, these facilities can reduce energy consumption by more than 50% compared to traditional, larger footprint lower-height warehouses. Energy efficiency is achieved through maximising storage density in the cube, minimising open spaces, minimising floor and ceiling area (which typically has the highest heat loss), reduced, faster doorway opening and deploying a lights out operation, with smart automation that can optimise energy consumption through on/off operation and electrical energy regeneration capability.
Harnessing Innovation and Efficiency
Looking ahead, food and beverage manufacturing and grocery industries across Southeast Asia need to be prepared for ongoing changes and challenges. The challenges of land shortages and rising energy costs require a strategic approach that balances immediate needs with long-term adaptability.
By optimising the logistics footprint and embracing sustainable operations with automation, companies will not only be addressing today’s challenges, but also positioning themselves for the future with higher operational resilience and agility, improved customer service levels and increased competitive advantage.